华中数控助力打造中国版“工业4.0”智能车间
2016-7-26 来源:武汉华中数控股份有限公司 作者:
一、背景
随着“工业4.0”的热潮从德国涌向全球,中国经济经过30年两位数的高速发展,也到了发展的十字路口,需要转型升级、提高制造业整体水平。2015年5月,国务院发布中国制造强国战略的第一个十年行动纲领《中国制造2025》,标志着中国“工业4.0”时代开启。“中国制造2025”的主攻方向是智能制造,重点推进“智能化、数字化、网络化”制造,是信息化、工业化深度融合的主攻方向,是传统产业进行转型升级的主要技术手段。
2015年,华中数控股份有限公司(以下简称:华中数控)携手东莞劲胜精密构建集国产高端数控机床、国产机器人、自动化设备、国产系统软件于一体的3C产品智能工厂,实现了工业4.0纵向集成,形成智能制造工厂在3C行业的示范,实现高速高精国产钻攻数控设备、数控系统与机器人的协同工作,在业内率先实现装夹环节采用机器人代替人工操作,节省70%以上的人力;建立基于物联网技术的制造现场“智能感知”系统,改造升级现有生产制造系统,建立全制造过程可视化集成控制中心,实现对钻攻中心、机器人、物流装备等的全面支持,降低产品不良率,缩短产品研制周期,提高设备利用率,提升车间能源利用率,最终实现少人化人机协同化生产。
二、项目概况
劲胜东城厂区智能制造项目是2015年国家94家智能制造专项之一,项目名称:移动终端金属加工智能制造新模式。项目由东莞劲胜精密组件股份有限公司牵头承担,联合开发单位还包括科研单位、国内高校、设备研发制造商、软件开发企业、金融企业等,项目负责人为华中科技大学邵新宇教授。
项目实施目标是:实现生产效率提高20%以上,运营成本降低20%,产品研制周期缩短30%,产品不良品率降低30%,能源利用率提高15%。
整个项目历时1年建设,目前已建成拥有10条自动化钻攻生产线的智能车间,智能车间包括180台国产高速高精钻攻中心、81台国产华数机器人、30台RGV、10台AGV小车、1套全自动配料检测系统。同时搭载全国产化的工业软件系统,包括云数控系统平台、CAPP、APS高级排程系统、MES生产管理系统、三维虚拟仿真系统等。基于国产高档数控系统的良好开放性,建立了智能工厂设备大数据平台,通过对设备实时大数据的采集、分析,实现了机床健康保障、G代码智能优化、断刀监测等智能化功能。另外还建设有 1条普及型自动化钻攻推广线(20台钻攻中心机床和12台工业机器人),1条机器人自动抛光打磨生产线(12台工业机器人),1条用于智能制造人才培训的智能生产线(微缩版智能工厂,具备智能工厂各种要素)等。
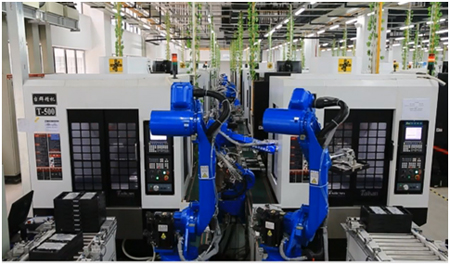
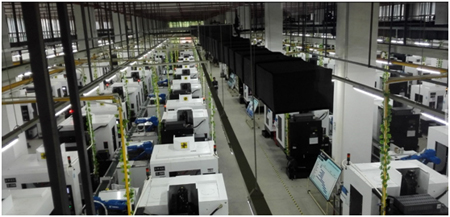
车间建设图
通过以上硬件和软件的开发建设,实现了高速高精国产钻攻数控设备、数控系统与机器人的协同工作,在业内率先实现装夹环节采用机器人代替人工操作,节省人力;建立基于物联网技术的制造现场“智能感知”系统,改造升级现有智能化系统,建立全制造过程可视化集成控制中心,实现对加工中心、机器人、物流装备等的全面支持。
三、项目特点
项目具有“三国”、“六化”、“一核心”的特点。
“三国”是指智能工厂全部使用国产智能装备、国产数控系统、国产工业软件;各参与单位充分发挥各自的特长,实行协同创新机制,基于“三国”的核心技术优势,各个硬件、软件系统之间相互深度开放并互相融合,为智能工厂的信息集成、数据集成以及各种智能化功能的实现奠定了基础,同时也保障了工业数据的安全可控。智能工厂最核心的设备——配套国产数控系统的国产高速钻攻中心机床,可与进口同类产品同台竞技,打破国外垄断。
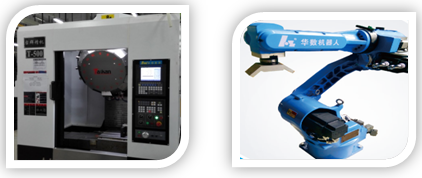
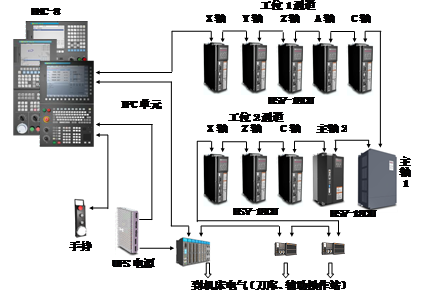
国产智能装备:国产高速钻攻中心和国产工业机器人
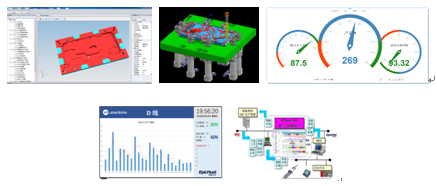
国产数控系统:华中8型总线式高档数控系统
国产工业软件:云数控、PLM、CAPP、MES、APS等
六化”是指:装备自动化、工艺数字化、生产柔性化、过程可视化、信息集成化、决策自主化。
1)装备自动化:配套国产高档数控系统的高速钻攻中心机床,实现高速高精加工,与进口同类产品同台竞技,实现机床装备高端化;利用6关节工业机器人取代现场操作工人,实现加工过程自动化,提升产品一致性;通过AGV定点、自动配送混流物料,实现车间物流自动化;现场采用非接触光学自动检测,自动采集检测数据及时反馈结果,实现产品检测自动化。
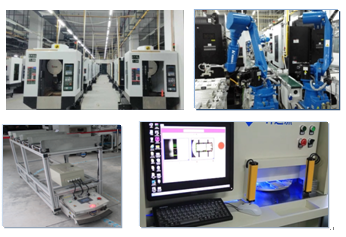
各种自动化设备
2)工艺数字化:采用三维CAPP软件系统实现机加工艺的三维数字化设计与仿真,大大提升工艺设计效率和设计质量;使用国产PLM软件,实现从设计到生产制造的产品生命周期数字化管理。
3)生产柔性化:实现多品种、多工序混流生产,不同产品快速切换。基于RFID系统进行定点投料,实现物料有序配送;采用机器人加RGV模式实现工时动态匹配;设计通用料盘和夹具,满足产品快速换线需求;使用APS智能排程系统,实现线体间、机台间混流生产排程,多目标协同优化。
4)过程可视化:通过车间底层各种传感器和物联网,实时采集并上传数控机床、机器人、RFID料盘、AGV、RGV等各种设备数据、物料数据、生产状态数据等各种数据,在本地云服务器上建立工厂的“数字双胞胎”,通过轻量化的三维仿真软件系统,实时监控、管理、操作车间设备;上层各种设计、管理软件系统通过网络下发生产与物料指令、工艺数据、质检标准等给车间设备,实现了工厂各种数据流的双向流通,保证了生产过程的可视化、透明化。
8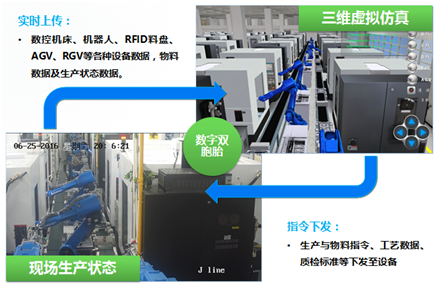
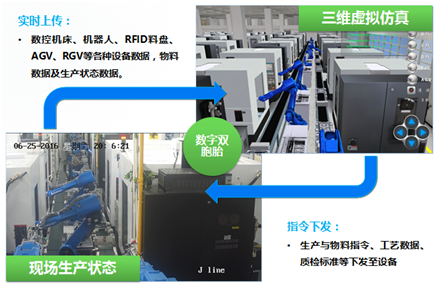
智能工厂“数字双胞胎”
5)信息集成化:车间采用实时工业以太网技术,实现“一网到底”,实时采集现场所有信息,通过设计统一的数据模型、统一的接口规范、统一的数据平台,实现各种多源异构数据和信息的集成,并使用服务器虚拟化技术,采用健壮性设计与配置,实现对海量信息的存储与处理。
6)决策自主化:基于车间大数据,实现设备状况的自检测、制造过程自执行、生产管控自组织,企业管理自决策。
智能工厂的“一核心”是指智能工厂大数据,包括工厂的人员数据、物料数据、设备数据、工艺数据、质量数据等等,通过对这些数据的集成、统计分析和应用,最终实现工厂的数字化和智能化。
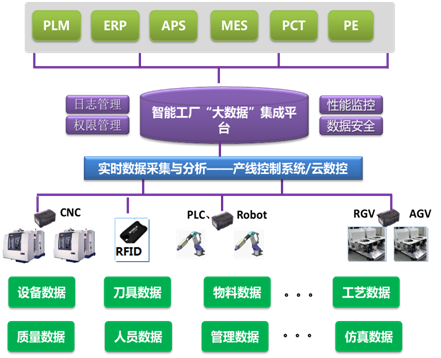
智能工厂“大数据”
四、华中数控主要工作
1)用自主化的国产设备装备智能制造车间
高速钻攻中心机床:
3C行业对数控机床的高速高精加工性能有很高的要求,国外机床数控系统成本高、开放性差、不能提供定制化开发。智能工厂180台钻攻中心,全部配置华中8型数控系统,自主研发,支持SOP、 RFID刀具实时管理、G代码远程管理,可采集机床实时毫秒级大数据,为工艺优化、机床健康保障、断刀监测提供支持,同等条件下加工效率高于进口系统,打破国外垄断。配套华中8型数控系统的高速钻攻中心机床具有以下优良特性:
a)高速:快速移动可达60米/分钟、单轴加速度1G、主轴从0加速到2000r仅需1.9s、刀具转换仅需1s,能实现5000r/分钟以上的高速刚性攻丝。
b)高精:加工精度达5 ‰mm,能连续运转,加工产品表面光洁度高,可靠性高,高速通过拐角不产生震动。
c)定制化:可根据客户需求配置设备部件,如机械手、自动门、丝杆、主轴等核心零部件。
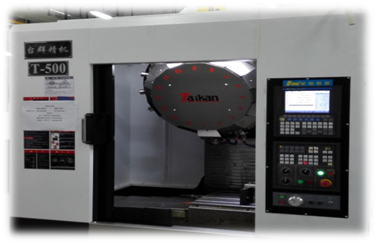
钻攻机配备国产数控系统
工业机器人:
整个劲胜智能车间配置的是国产华数机器人,华数机器人整机产品的自主国产化率已达到80%以上,除了RV减速机为进口,其余核心零部件均为国产达到了安全可控的条件。车间目前已经使用了93台机器人用于上下料,组成了柔性生产系统;使用了12台机器人应用于手机壳打磨线,实现了国产机器人应用于复杂轨迹打磨的突破,在国产机器人应用上属于首创。
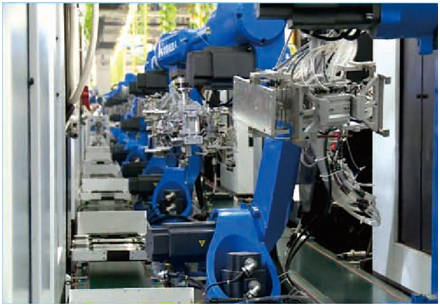
华数机器人
目前华数机器人的产品主要在冲压、注塑、机床上下料、喷涂、焊接、装配、3C自动化等行业中大量使用。华数机器人目前发展势头迅猛,已经将华中数控多年机器人相关技术沉淀成功产业化,机器人已经大批量生产,已在众多客户现场批量使用。
2)产线总控系统
产线控制系统是智能工厂“大数据”核心层,主要负责产线设备数据采集、设备监控、生产计划执行管理等,并将“大数据”、生产完工信息反馈至管理系统,帮助企业生产部门做出科学、有效的决策。
主要功能:
. 车间设备管理网络化
. 数据采集:毫秒级实时数据
. 设备实时监控
. 生产任务自组织自执行
. 产线运行前智能化检测
. 生产派工、报工、工单管理
产线控制系统架构:
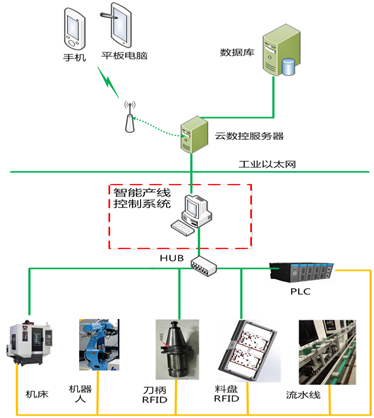
产品总控系统架构
3)建立智能制造车间CPS
智能制造本质是基于“信息物理系统(CPS)”实现“智能工厂”, 核心是动态配置的生产方式。
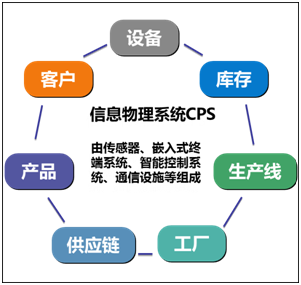
信息物理系统CPS
CPS利用大数据、物联网、云计算等技术,将物理设备连接到互联网上,实现虚拟网络世界与现实物理世界的融合(数字双胞胎),让物理设备具备计算、通信、精确控制、远程协调、自治、数据采集等功能,从而实现智能制造。
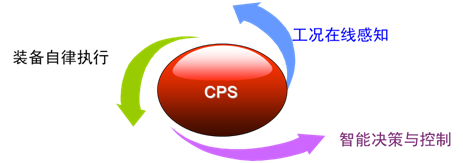
信息物理系统CPS核心
基于指令域电控大数据CPS模型体系架构如下:
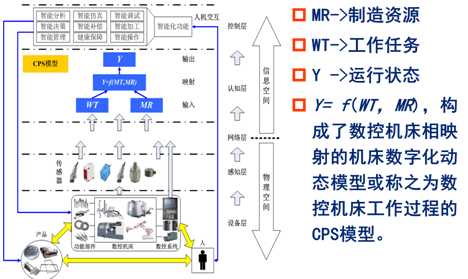
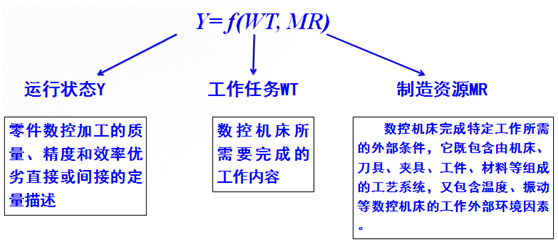
基于指令域电控大数据CPS模型体系架构
4)基于云计算的数控机床大数据中心
以数控机床CPS模型、大数据采集与存储、开放式云计算应用架构、机床互联通信协议为技术基础,实现对数控机床7×24小时监控和实时数据采集,建立数控机床的“数字双胞胎”,开创了大数据在数控加工领域应用的新途径,为机床智能化应用集成提供必要基础。
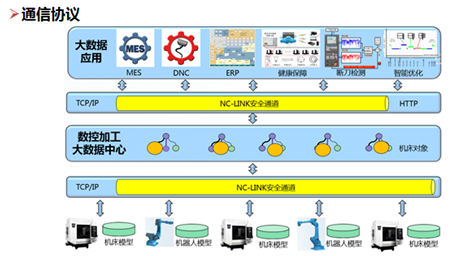
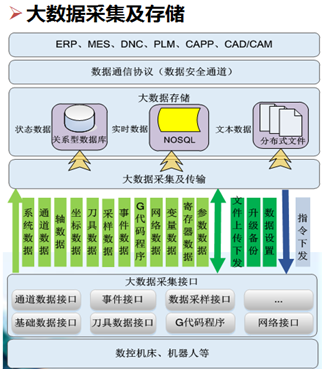
基于云计算的数控机床大数据中心
5)构建智能车间“云数控”系统
云数控系统是运用物联网、大数据、云数控等关键技术,围绕数控机床加工效率和质量的提升以及机床的智能化管理,整合国内各项领先技术而开发出的先进车间信息化管理系统。主要有“云管家、云维护、云智能”三大功能,实现制造设备从日常生产到维护保养、改造优化的全生命周期管理,为用户提供设备及产品相关信息的“大数据”。
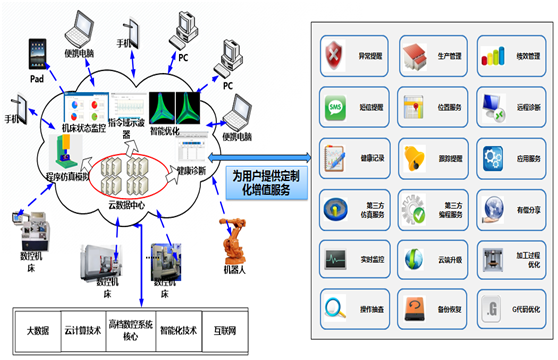
云数控系统
6)产品加工品质问题攻关
影响产品品质的关键因素有:机床的稳定性、刀具磨损/断刀、铝屑问题。
针对机床稳定性问题,华中数控开发了基于大数据的机床健康保障功能,通过“铁人三项”对数控机床进行定期“体检”,提升机床稳定性、可靠性,保障加工产品质量,通过“云服务平台”可随时随地掌握机床健康状态。
健康保障功能将数控系统与云数控平台的优势进行互补与整合,充分发挥云数控平台的存储、计算、管理、跨平台和远程通信功能,对数控数控系统产生的海量电控数据进行处理、分析与可视化,帮助用户管理机床的健康状态。
此外,用户还可以通过手机、平板等移动终端掌握机床的健康状态及其变化趋势,及时作出决策,保障数控机床的健康。
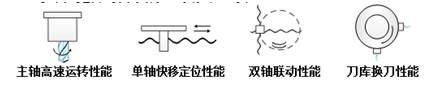
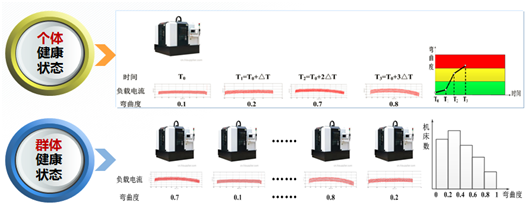
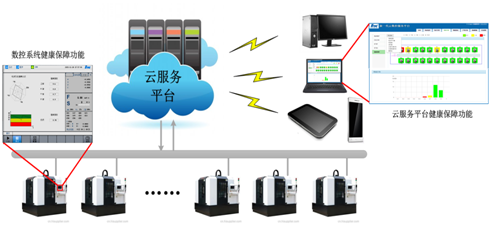
云服务平台健康保障
针对刀具磨损/断刀问题,通过基于“RFID”及刀具管理系统实时监控刀具寿命,实现刀具从采购、仓储、领用、使用、维修、报废的全生命周期管理,机床RFID刀具管理与数控系统无缝集成,同时通过基于周期1毫秒的机床 “大数据”实时监控刀具寿命及断刀检测,进行7×24小时监控,对机床断刀情况进行准确判断与及时反馈。
对数控机床加工过程进行7×24小时监控,实时采集机床设备大数据,获取机床设备“心电图”,实现对机床断刀情况进行准确判断与及时反馈,降低企业成本,提高零件直通率。
刀具断裂检测基于指令域分析方法,提取刀具断裂时及断裂后的机床主轴“心电图”的特征,并与正常切削时的“心电图”模板比较,再结合机器学习算法进行学习与分类,进而实现刀具的断裂与否的检测。
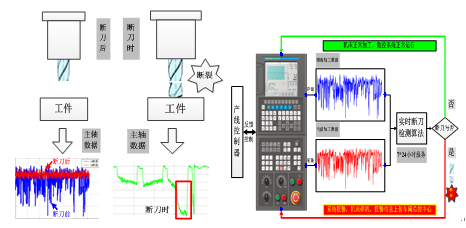
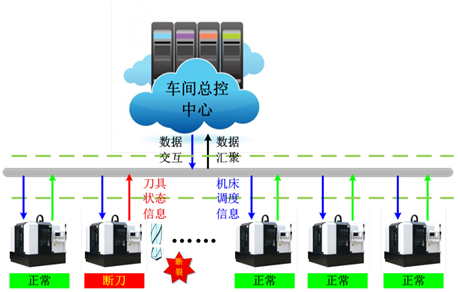
基于大数据的数控机床智能化断刀检测技术
在零件的一个加工工序中,先后会有不同直径、不同类型的刀具参与加工,实现既定的加工任务。而在实际的生产加工中,特别是在无人看守的自动化车间中,往往会因为其中的一把刀具的断裂而产生两种主要的不良后果:①由于刀具断裂剩余的切削余量将导致后续刀具的连续断裂;②形成废品,影响自动化线的产品直通率。以上两种不良的后果,均直接增加了企业的生产成本和降低了企业的生产效率。因此,刀具断裂的自动检测功能将具有非常直接的现实意义。
断刀检测功能遵循CPS系统“感知→分析→决策→反馈”的闭环控制原理:获取数控系统内部的当前主轴功率指令域数据,与数控系统内存的历史模板数据进行比较分析,通过机器学习算法进行决策,如果决策出断刀则一方面反馈给数控系统进行报警停机,另一方面反馈给产线控制器用于生产调度。
因此,断刀检测的功能将对刀具状态做出及时的判断,减少后续加工中的刀具断裂数量和零件废品率,进而降低企业的生产成本,提高零件生产的直通率,最终实现企业经济效益的最大化。
针对铝屑问题,原材料铝材经过高速中心加工后产生铝屑残留,自动化作业无法判断处理,严重影响产品加工精度,导致产品良率低,一度阻碍了项目的推进。后来我们特别成立了攻坚小组,历时一个月尝试各种办法,通过反复试验验证,最后我们终于找到一套方法来克服铝屑问题:设计专用夹具、设计机器人专用自动化吹屑装置,优化吹屑路径、实时在线清洗。
通过反复试验验证,解决了铝屑残留的难题,良率由原来的70%多提高到现在98%。
7)加工效率问题攻关
影响加工效率的关键因素有:机床加工效率有待进一步挖掘提高;工艺加工参数,人工设计,缺少优化。
针对机床加工效率进一步挖掘,国产高速钻攻中心配套华中数控系统,加工效率高于进口产品,经用户使用验证和第三方测试,其功能、性能和可靠性达到国外同类系统水平,可替代进口,整体技术水平全面达到国际先进水平。
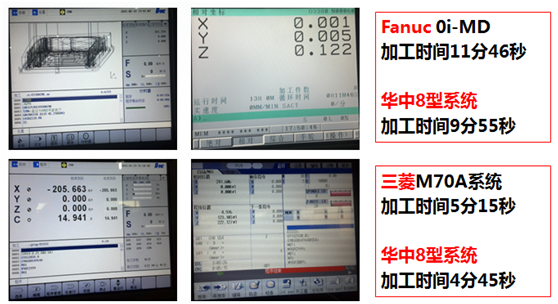
华中数控系统与进口系统加工效率对比
针对工艺参加及工艺路径优化,通过采集数控加工过程中数控系统的内部电控大数据,借助于指令域分析工具,建立实时数据、材料去除率和加工程序行之间的对应关系,基于实测数据优化进给速度,在均衡刀具切削负荷的同时,可有效、安全地提高加工效率。
通过采用优化后的加工代码加工,可以将原始的主轴电流中的最大值降低、最小值提升、波动值减小,实现刀具负载均衡,而且粗加工效率可以提升10%~15%,精加工效率可以提升3%~5%。
3C行业对数控机床的高速高精加工性能有很高的要求,对加工效率尤其敏感。对一个3000台机床规模的3C加工车间,若单件加工效率提升10%,意味着可节省300台机床的费用。
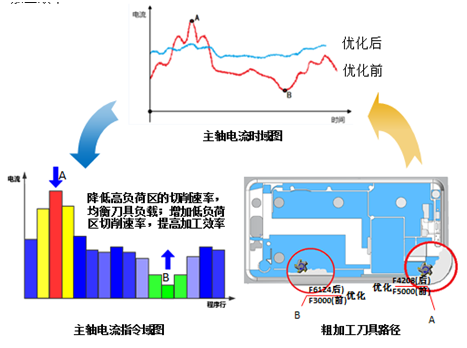
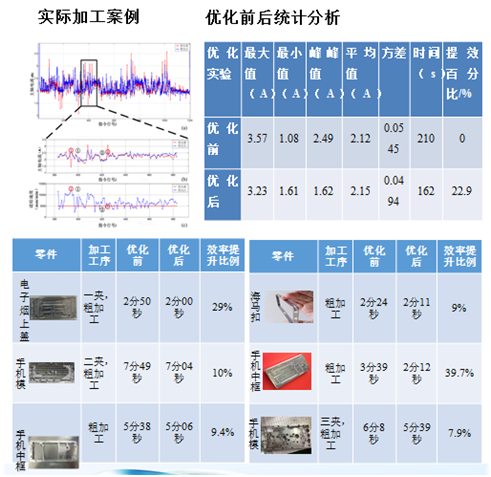
基于大数据分析的工艺参数智能优化方法
8)基于机器人离线编程系统,建设3C产品打磨线
机器人是实现智能制造的基础,机器人离线编程是机器人技术发展的重要方向。研发的机器人离线编程系统与应用领域的工艺知识深度融合,满足了机器人应用领域扩大和任务复杂程度增加的迫切需求。在3C产品金属部件、航空航天零件、汽车覆盖件、激光焊接与切割、模具制造、五金零件、喷涂、多轴加工、石材和板材加工等专业领域得到广泛应用 。系统主要特点包括:
. Robot/CAM/一体化
. 支持机器人库的扩展
. 工件和零件编程模式
. 速度和加速度的校验
. 奇异点的检查与控制
. 工件的自动快速标定
. 外部轴运动协调优化
. 运动仿真与碰撞检查
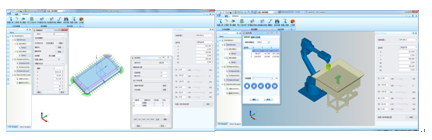
机器人离线编程系统
打磨抛光线实现:湿抛模式,单线配置12台机器人。
优势:
1.使用湿抛技术减少粉尘,有效改善作业环境。
2.使用离线编程技术,能实现产品“零切换”。
3.机器人替换人力作业,实现100%标准化作业,品质稳定、效率高于人工。
4.无需过于依赖经验丰富的技术工人,节省人工成本。
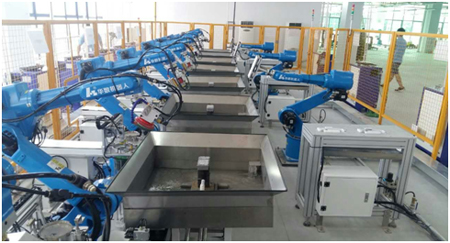
华数机器人打磨线
五、总结
项目实施达到良好效果:1.人机比1:12,车间直接人力由实施前204人减少至33人 ;2.设备负荷稼动时间由20小时/天提升到24小时/天 ;3.产品良率由95%提升至98%。
国产智能装备、国产数控系统、国产工业软件不仅能满足企业的生产制造需求,而且能够自主采集加工数据,并逐步形成大数据,确保大数据的安全可控和应用。
国家正大力实施“中国制造2025”,全面推进智能制造,实现制造业转型升级,数控系统、机器人、工业大数据、工业云平台等,具有广阔的发展前景。华中数控将凭借不断创新智能制造车间经验、和多年的丰富经验,助推中国工业在转型升级过程中不断提升竞争力,为国家实现从“工业大国”到“工业强国”的目标作出贡献。
投稿箱:
如果您有机床行业、企业相关新闻稿件发表,或进行资讯合作,欢迎联系本网编辑部, 邮箱:skjcsc@vip.sina.com
如果您有机床行业、企业相关新闻稿件发表,或进行资讯合作,欢迎联系本网编辑部, 邮箱:skjcsc@vip.sina.com
更多相关信息