刀杆外径对热缩刀杆与刀具配合的力学特性影响分析
2016-11-25 来源:湘潭大学 作者:刘博 周后明 周友行 张高峰 彭锐涛
摘要:为探究刀杆外径对热缩刀杆与刀具配合的力学特性的影响,对热缩刀杆与刀具配合模型进行理论研究,利用有限元软件ANSYS对静态、径向力作用下及感应加热情况下的不同刀杆外径的热缩刀杆与刀具配合等效应力、接触压力、热变形及热应力等力学特性进行对比分析。结果表明,随着刀杆外径的增大,热缩刀杆与刀具配合的总的接触压力、最大等效应力及热应力增大,配合面的最小热位移差值减小。在径向力的作用下,热缩刀杆上的接触应力不再均匀,最大接触应力明显增大,刀具也因径向力的作用而产生变形。在此基础上进一步给出了热缩刀杆外径的控制方法与流程,对热缩刀杆的合理设计和选用具有一定的现实指导意义。
关键词:非线性有限元;外径;高速铣削;热缩刀杆
0. 引言
刀具在热缩刀杆中的装夹是刀具夹持系统研究的重要组成部分。在高速加工过程中,要求热缩刀杆受到的最大应力小于其材料的屈服极限,并且必须提供足够的夹持力以保证加工的正常进行。文献[卜2]对热缩刀杆与刀具配合的动态特性、热疲劳寿命进行了分析研究,文献[3—4]用有限元法对热缩配合的弹性变形进行了研究,文献[5—6-]g寸热缩刀杆的连接刚度、阻尼及频率响应进行了研究。
对于结构参数(半径及公差)确定的刀具和刀杆,影响其配合性能的结构参数有:刀杆外径、配合过盈量、接触长度及刀杆接触部分外锥角。周后明等[7]对热缩刀杆合理夹持长度和合理过盈量进行了深入研究,确定了热缩刀杆与刀具配合时夹持长度及过盈量的控制范围。本文在文献[7]研究基础之上,借助非线性有限元技术,以热缩刀杆接触面为研究对象,着重对不同外径的热缩刀杆与刀具配合的接触压力、最大等效应力、热变形及热位移差值等力学特性进行分析,在此基础上进一步给出了热缩刀杆合理刀杆外径的控制方法。
数学模型的建立
本文暂不考虑切削热对接触特性的影响,由于本文分析的热缩刀杆和刀具直径小,转速对接触的影响很小,因此将其忽略。如图l所示,在刀具的装卸过程中,热缩刀杆和刀具因受热而产生尺寸扩张,刀杆和刀具径向位移的变化决定其配合面的接触状态。
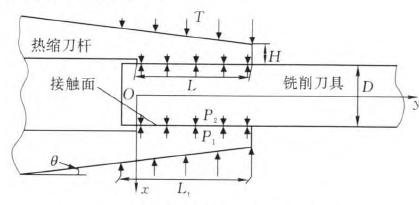
图1 热缩刀杆与刀具配合面分析
接触时,热缩刀杆与刀具接触面上应满足的变形、应力协调条件为嘲
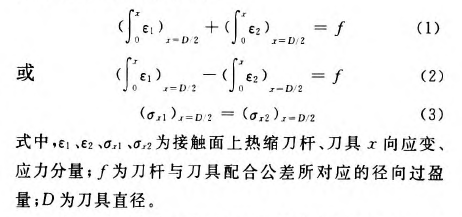
分离时,热缩刀杆与刀具接触面上应满足的变形协调条件为
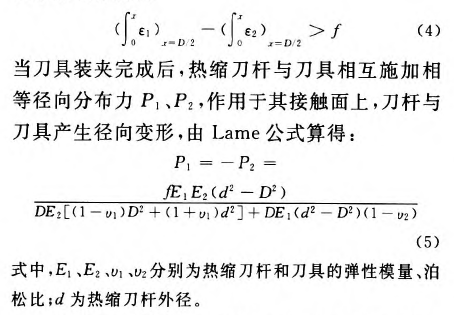
当式(5)中其他变量不变时,对d求导可知,接触面的接触压力与d正相关。由于热缩刀杆夹头以外的部分对接触压力集中现象的影响较大,且接触边界条件随着外加载荷的变化而变化。因此,热缩刀杆与刀具之间的过盈配合属于一种几何及状态高度非线性问题,单纯用理论分析较为复杂。
2. 热缩刀杆结构有限元分析
2.1有限元模型的建立
采用商用有限元软件ANSYS作为参数化建模与分析工具。根据式(1)~式(5)建立刀杆及刀具的有限元模型,并对接触面上接触应力分布进行分析。由于所分析的问题满足轴对称条件,为节省计算资源,所以只对热缩夹头部分的1/2进行建模分析。表1所示为热缩刀杆和刀具的材料属性。
表1 热缩刀杆和刀具的材料属性
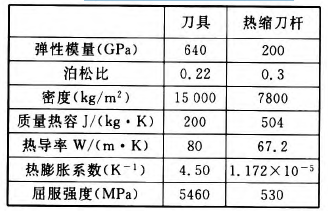
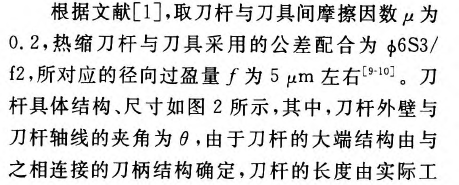
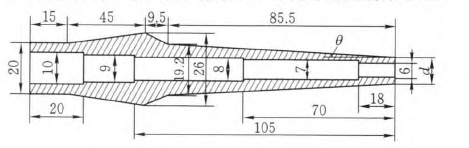
图2 热缩刀杆结构
况需要选择,所以口不是一个独立变量,当长度确定时,口随外径的改变而变化,因此,在后续分析中不予考虑。实体单元类型采用SOLIDl86三维实体单元,以刀杆配合面为接触目标面、刀具接触面为接触面创建接触对,接触单元类型为三维接触单元,其中采用接触单元TARGEl70来模拟刚性目标面,接触单元CONTAl74来模拟柔性接触面。为了提高计算精度,确保结果的准确性,网格划分采用细化的六面体网格,图3为刀杆与刀具配合的对称分析有限元模型。文献[1]已通过实验对模型的准确性进行了实验验证。
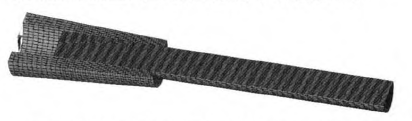
图3热缩刀杆与刀具配合的对称分析有限兀模型
2.2静态仿真分析
从理论上说,接触刚度系数越大越能避免接触穿透问题的产生,所得到的分析结果就越精确、越接近于真实解,但过高的接触刚度系数将引起总刚矩阵的病态,造成分析过程收敛困难而耗费大量的计算资源,甚至得不出分析结果;而过低的接触刚度系数又将导致接触穿透问题的产生而得到错误的结果。由于本文中模型的网格数较多,故由文献[7]的分析结果可知,接触刚度系数取l在本文的分析中是比较合适的。
对d分别为7.0,7.5,8.0,8.5,9.0,9.5,10.0,10.5,11.0,11.5,12.0 mm的热缩刀杆进行仿真分析。考虑到整个刀杆模型为锥体结构,热缩刀杆内孑L面小端到大端沿轴向的扩张量逐渐变大而形成喇叭口状,因此应力也应呈喇叭口状分布。图4为d一9 mm时等效应力分布云图,由于热缩刀杆锥面型外壁刀杆外径不均,所以接触面上等效应力分布也不均,在热缩刀杆的轴线方向上,随着刀杆外径的增大,等效应力逐渐增大。
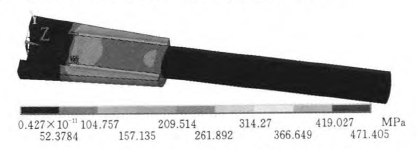
图4杆外径d-=9肿时的等效应力分布云图
由于不同外径热缩刀杆的应力分布云图相似,只是应力大小不同而已,本文就不再赘述。图5为不同刀杆外径下刀杆上节点的最大等效应力分布图,对比分析不同刀杆外径时的结果可知,随着刀杆外径的增大,接触面上节点的最大等效应力增大,但都小于材料的屈服强度540 MPa。可见,所分析的刀杆在不受外力时,其强度均满足要求。
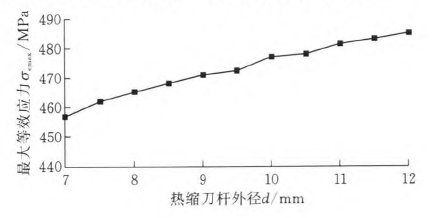
图5不同刀杆外径时的最大等效应力
图6为不同刀杆外径下z方向上总的接触压力Fx,由图6可知,随着刀杆外径的增大,接触压力Fx增大。在加工过程中,由文献[8-1可知,所需要传递的安全扭矩M。与总接触压力P。的关系为
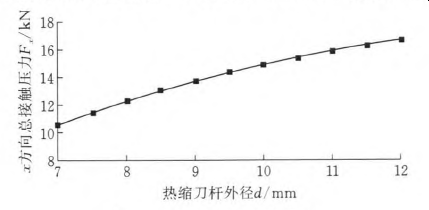
图6 32方向上总接触压力
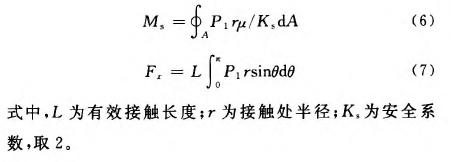
由式(6)、式(7)可算得热缩刀杆所能传递的最大安全扭矩(图7)。对于热缩刀杆与刀具配合来说,精确、安全可靠的切削取决于两者之间合理的接触压力。由图7可知,随着刀杆外径的增大,刀杆所能传递的安全扭矩增大。
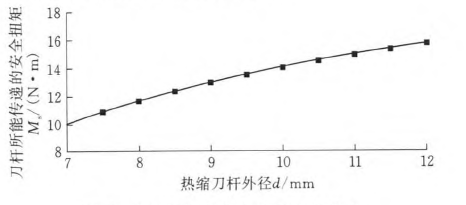
图7热缩刀杆所能传递的安全扭矩
2.3在径向力作用下的仿真分析
在实际切削过程中,由于切削力的存在从而导致热缩刀杆与刀具接触面上的等效应力不再均匀,刀具也因切削力而产生变形,从而引起加工误差。根据文献[11]及加工实践可知,在利用小直径铣刀对模具进行半精加工或精加工时,刀具所受的径向铣削力通常不超过250 N。而小直径热缩刀杆一般只用于小加工余量的精加工工艺中,其径向铣削力更小。由于模型具有对称性,本文中仅对刀具尖端z方向上的一个节点施加100 N的径向力(图8)。
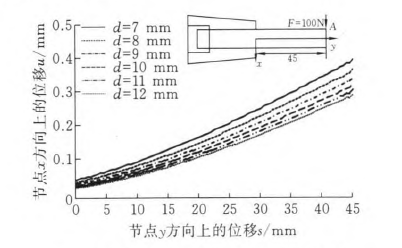
图8切削力作用下节点的最大等效应力
图8所示为不同刀杆外径条件下,在施加径向力F时,刀具外壁(Y坐标0~45 mm之间)节点z向的径向位移。可以看出,刀具的径向位移随刀杆外径的增大而减小,刀具最大径向位移从0.399 98 mm减小至0.298 62 mm,减小幅度达到25.34%,说明增大刀杆外径可提高热缩刀杆与刀具配合的径向夹持刚度,减小刀具因外力冲击而产生的变形。
不同外径的热缩刀杆在径向力的作用下节点的最大等效应力曲线如图9所示。对图5、图9进行对比分析可知,在径向力的作用下,热缩刀杆上节点的最大等效应力增大;刀杆外径越小,应力的增大幅度越大;外径为7~10.5 mm的热缩刀杆,在径向力的冲击下,其节点的最大等效应力已经超过了材料的屈服强度。分析可知,随着热缩刀杆外径的增大,节点的最大等效应力减小,热缩刀杆抗冲击能力增强,外力对刀杆夹持稳定性的影响减小。
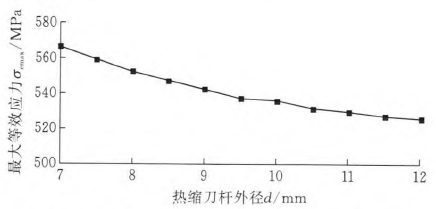
图9径向力的作用下刀杆节点的最大等效应力
3 .热缩刀杆热一结构有限元分析
3.1在感应加热作用下的热变形
在感应加热的情况下,由于加热过程中温度载荷均匀地分布在热缩刀杆前端的外环面上,因此所分析的结构及载荷均满足轴对称条件,为节省计算资源,只需要对完整模型截面的1/2进行轴对称分析即可。采用热单元PLANE55对不同加热温度下热缩刀杆与刀具稳态时的温度分布进行分析;采用结构单元PLANEl82加载前述分析的热载荷,并对热缩刀杆及刀具的热变形进行计算。刀杆刀具材料属性如表1所示,在刀杆与刀具的接触处,采用接触单元CONTAl72、TARGEl69模拟刀具装夹过程中的接触行为,由文献[12]可知,热缩刀杆与刀具直接的接触热传导系数T。。取40 000,对流传热条件为20℃气体强制对流。
过盈配合和感应加热都将影响热缩刀杆与刀具配合面的径向位移,而配合面的径向位移变化也最终决定了热缩刀杆与刀具的接触状态。为了直观地表示不同感应温度下热缩刀杆与刀具的接触状态,选取配合面上热缩刀杆节点的最小径向位移U。和刀具节点的最大节点位移U。及其热位移差值e(图10)来表示结合面接触状态分布规律。
为验证有限元仿真结果的有效性,刀具与热缩刀杆材料属性同表1,采用热缩刀杆加热器对刀杆进行加热,逐渐提高加载温度直到刀具能在热缩刀杆中进行装夹并记录此温度值(图11)。经反复实验测量取平均值,刀具能快速装入的温度为268.5℃,取出温度为281.25℃,与仿真数据e—f一5且m时对应的283.1℃(图10中直线,一5肚m与热位移差值曲线的交点)基本一
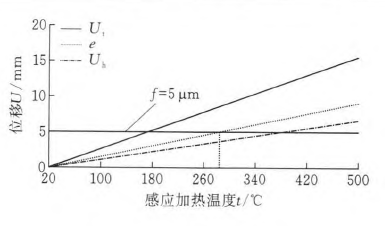
图10 L,h、U,及P分布图
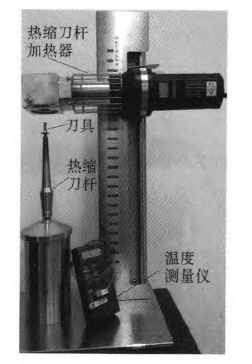
图11 装夹温度测试买验图
致。由实验可知,刀具的装入温度稍低于刀具的取出温度。当感应加热温度高于装入温度而低于取出温度时,刀具在装入过程容易受热使径向尺寸增大而造成刀具卡住的现象发生,刀具在热缩刀杆中的最小装卸温度以取出刀具时的温度为准。
图12为不同刀杆外径时热缩刀杆与刀具的最小热位移差值的仿真结果。由图12可知,在不同刀杆外径的情况下,最小热位移差值随温度的分布呈线性分布;在相同温度条件下,最小热位移差值随着热缩刀杆外径的增大而减小;在相同的型号刀具及尺寸公差的情况下,外径越大的热缩刀杆装夹所需的温度越高。
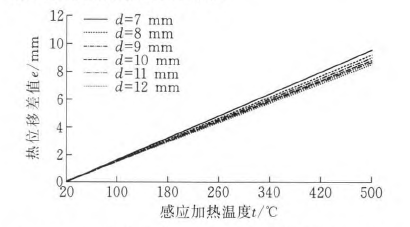
图12 刀杆外径对最小热位移差值分布的影响
3.2在感应加热作用下的热应力
由文献E23可知,热缩刀杆节点热应力的大小直接影响其热疲劳寿命,而感应加热温度又决定着热应力的大小。因此,本文采用稳态热传导与应力耦合的分析方法对不同感应加热温度下热缩刀杆的热应力问题进行分析。
热缩刀杆上节点应力变化越大,该点越容易疲劳破坏。图13所示为不同感应温度下热缩刀杆节点的最大热应力曲线。由图13可知,热缩刀杆的最大热应力随着感应加热温度的增大而增大;在相同感应加热温度下,热缩刀杆外径越大,其内部最大热应力越大。
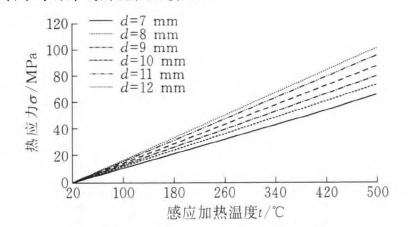
图13热缩刀杆节点的最大热应力
对相同型号的铣削刀具与热缩刀杆进行配合,在配合公差相同的情况下,刀杆外径越大,其所需的装夹温度越高,装夹过程中的热应力越大。过大的刀杆外径不但容易造成刀具装入困难,而且直接影响热缩刀杆的疲劳寿命。而且随着热缩刀杆外径的增大,刀杆容易与工件产生干涉,对实际加工非常不利。在此分析中,对于公差配合为巾6S3/f2的热缩刀杆与刀具,在满足夹持强度要求的情况下,最合理的刀杆外径应该在11~12 mm,这样才能既保证热缩刀杆与刀具配合间夹持均衡而具有很好的夹持刚度,又不至使刀杆上的应力超过其屈服强度而降低刀杆的使用寿命和精度,更有利于提高热疲劳寿命。
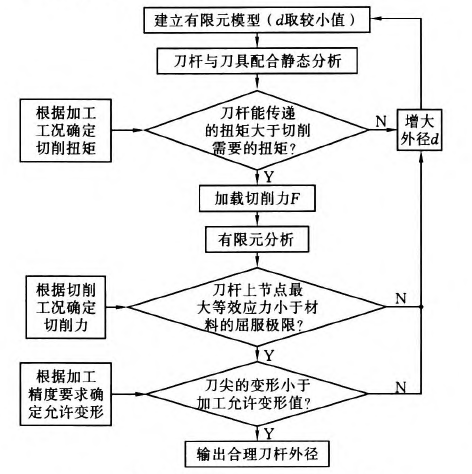
图14确定热缩刀杆合理刀杆外径流程图
利用ANSYS参数化语言(APDL)把热缩刀杆的结构设计与有限元分析有机结合起来,能实现对热缩刀杆外径的合理控制。图14为确定合理刀杆外径的单周期有限元分析迭代流程图。按照此方法,针对热缩刀杆与刀具接触的实际情况,在给定刀杆内孔直径、过盈量、接触长度及材料的情况下就可以给出热缩刀杆的合理外径值。
4. 结论
(1)随着刀杆外径的增大,热缩刀杆与刀具配合的总的接触压力和节点的最大等效应力增大,所能传递的安全扭矩加大。
(2)在径向力的作用下,热缩刀杆上节点的最大等效应力较无径向力时增大,甚至超过了刀杆材料的屈服强度,此最大等效应力可为热缩刀杆的结构设计提供参考。
(3)在径向力的作用下,随着刀杆外径的增大,刀杆上的最大接触应力及刀具的径向位移减小,刀杆与刀具夹持刚度增强,刀具的抗变形能力增强。
(4)随着热缩刀杆外径增大,配合面最小热位移差值减小,刀具所需的装夹温度升高;热缩刀杆最大热应力增大,刀杆的热疲劳寿命缩短。
(5)利用ANSYS参数化语言(APDL)把热缩刀杆的结构设计与有限元分析有机结合起来,能实现对热缩刀杆外径的合理控制。
投稿箱:
如果您有机床行业、企业相关新闻稿件发表,或进行资讯合作,欢迎联系本网编辑部, 邮箱:skjcsc@vip.sina.com
如果您有机床行业、企业相关新闻稿件发表,或进行资讯合作,欢迎联系本网编辑部, 邮箱:skjcsc@vip.sina.com