薄壁零件的数控车削
2020-5-1 来源: 韶关市乳源瑶族自治县中等职业技术学校 作者:崔 毅
摘要:薄壁零件的加工由于夹紧力、车削力、车削热、内应力、振动与变形等因素的影响,使工件产生较大的变形,导致零件的加工质量难以保证。笔者从工件的装夹、刀具要求、程序的编制等方面进行综合考虑,解决了薄壁零件的车削加工难题,从而有效提高了零件的精度,保证了产品的质量。
关键词 : 薄壁零件 车削加工 夹具 程序
薄壁零件因其结构紧凑、质量轻、节省材料等特点,在各工业部门日益得到广泛应用。但由于薄壁零件强度低刚性差,加工过程中极易变形,难于保证零件的加工精度,所以薄壁零件加工难成为一个凸显的问题。下面以某型号产品的一薄壁套筒为例,对薄壁零件的数控车削加工工艺进行研究。
1、 影响薄壁零件加工精度的主要因素
影响薄壁零件加工精度的因素有很多,但归纳起来主要有以下三个方面:
1.1 易受力变形
因壁薄,在夹紧力的作用下,容易产生变形,从而影响工件的尺寸精度和形状精度。如图1 所示。
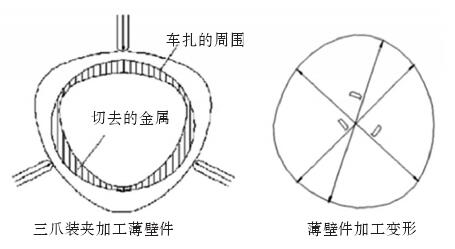
图 1 工件振动变形
1.2 易受热变形
因工件较薄,切削热会引起工件热变形,使工件尺寸难以控制。
1.3 易振动变形
在切削力 (特别是径向切削力) 的作用下,容易产生振动和变形,影响工件的尺寸精度和形状、位置精度和表面粗糙度。
2 、薄壁零件加工案例分析
如下图 2 所示,是企业接单生产的薄壁零件。为了提高产品的合格率,我们从工件的装夹(夹具的设计加工)、工艺路线分析、刀具几何参数、切削用量等方面进行综合考虑。实践证明,有效提高零件的精度,保证了产品的质量,提高了生产效率,为企业赢得了经济效益。
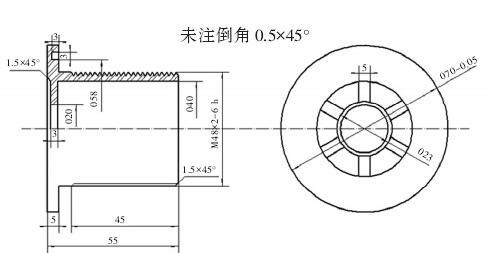
图 2 薄壁零件
2.1 图样、毛坯及加工难点的分析
2.1.1 图样分析 该零件是一个套类薄壁零件,左端为一个70 mm、 厚度为 5 mm 的薄大凸外圆,在外圆右端面上有一 58 mm、宽度和深度都为 3 mm 的端面槽,左端中间由壁宽为 5 mm、厚为 3 mm 的六块肋板组成,肋板中间有 20 mm、厚为 1.5 mm 的圆孔。零件右端为一个圆筒,壁厚为4 mm, 在48 mm 的圆筒外圆面上加工有M48 × 2 的三角螺纹,整个零件的工艺倒角为 0.5× 45°,总长为 55 mm。
2.1.2 零件毛坯分析 毛坯是由生产厂家铸造成型的粗坯,材料为 45#钢,需要加工零件的外圆、端面、端面槽和螺纹部分,其中螺纹是加工重点,每个面的加工余量小,只有 0.5~1 mm,而加工的批量又较大。
2.1.3 从零件图样要求及材料分析 加工此零件的难度主要有两点:①主要因为是薄壁零件,材料为 45#钢,批量较大,既要考虑如何保证工件在加工时的定位精度 , 又要考虑装夹方便可靠。而我们通常都是用三爪卡盘夹持外圆或撑内孔的装夹方法来加工。但此零件较薄,车削受力点与夹紧力作用点相对较远 , 还需车削M48 × 2 螺纹,受力很大,刚性不足,容易引起
晃动 。 因此要充分考虑如何装夹和定位的问题。②螺纹加工部分厚度只有 4 mm,而且精度要求较高。
2.2 夹具的设计
2.2.1 右端外圆的装夹设计 此端为薄壁,厚度为 4 mm。从图 3 中可以看到零件是在三爪自定心卡盘上装夹 , 零件只受到三个爪的夹紧力,夹紧力不均衡,会出现图 1 的情况,使零件变形。如图 4 所示,采用开缝套筒装夹,增大零件的装夹接触面,零件的变形小,此方法可行。
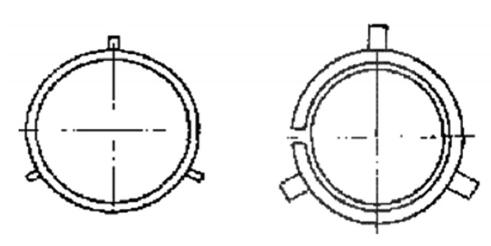
图 3 三爪自定心卡盘装夹 图 4 开缝套简装夹
2.2.2 装夹采用的办法 对于毛坯上 5 mm 凸圆的右端面以及端面槽、右端外圆和螺纹的车削,装夹采用的办法就是先在卡盘的三个卡爪上按要求车削一个直径为80 mm、 深度为 2 mm 的圆孔。之后,分别焊接一个扇型凸台,凸台厚度为5 mm,将卡爪改进成如图 5 所示的情况,用来夹住零件的左端,然后在零件的右端设计一个专用夹具如图 6 所示,把其放入内孔中,用来固定并顶住零件右端,从而形成一夹一顶的牢固装夹,其装夹示意图如图 7 所示。当加工完成后,右端专用夹具可从零件内孔抽出,如图 8 所示,从而完成零件的装卸。
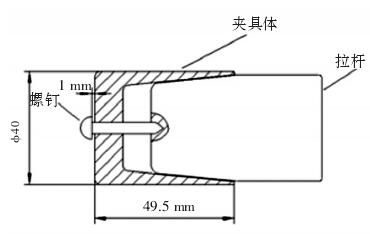
图 5 卡爪改进
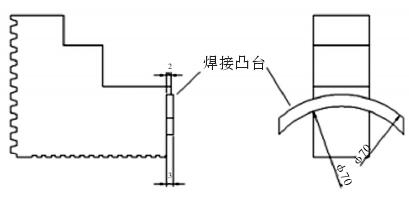
图 6 专用夹具
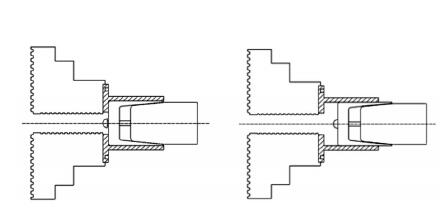
图 7 装夹示意 图 8 专用夹具
2.3 加工工艺的制订
2.3.1 螺纹的加工工艺分析 螺纹的加工是该零件的重点和难点,加工部分厚度只有 4 mm,而且精度要求较高。在加工螺纹的时候,要非常的小心,加工螺纹的切削速度和进给量都要充分考虑。另外,数控加工螺纹的指令也要选择恰当,可以根据工件的具体情况,分析一下采用哪种程序指令进行螺纹的数控加工。
FANUC 数 控 系 统 螺 纹 编 程 指 令 有 G32、G92、G76。G32 是简单螺纹切削,显然不适合。G92 螺纹切削循环采用直进式进刀方式,刀具两侧刀刃同时切削工件,切削力较大,而且排屑困难。因此在切削时,两切削刃容易磨损。从以上对比可以看出,只简单利用一个指令进行车削螺纹是不够完善的,采用 G92、G76 混用进行编程,即先用 G76 进行螺纹粗加工,再用 G92 进行精加工,在薄壁螺纹加工中,将有两大优点:一方面,可以避免因切削量大而产生薄壁变形。另一方面,能够保证螺纹加工的精度。
2.3.2 合理安排加工工艺路线 (见下表)。
合理安排加工工艺路线表
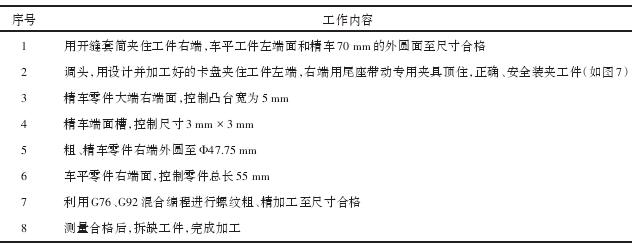
2.3 加工工艺
2.4 刀具的选择
该企业所用数控车床与高速钢刀具都是从外国进口的,其质量与性能都能得到保证。在薄壁零件的车削中,合理的刀具几何角度对车削时切削力的大小,车削中产生的热变形、工件表面的微观质量都是至关重要的。刀具前角大小决定着切削变形与刀具前角的锋利程度。前角大,切削变形和摩擦力减小,切削力减小。但前角太大,会使刀具的楔角减小,刀具强度减弱,刀具散热情况差,磨损加快。所以,一般车削钢件材料的薄壁零件时,用高速钢刀具,前角取 6°~30°,用硬质合金刀具,前角取 5°~20°。
2.5 切削参数的选择
薄壁零件车削时变形是多方面的,装夹工件时的夹紧力、切削工件时的切削力、工件阻碍刀具切削时产生的弹性变形和塑性变形,使切削区温度升高而产生热变形。所以粗加工时,背吃刀量和进给量可以取大些;精加工时,背吃刀量一般在 0.2~0.5 mm,进给量一般在 0.05~0.1 mm/r,甚至更小,切削速度 60~120 mm/min,不宜过高。根据切削用量的选用原则,合理的确定数控车床的各项切削参数 : ① 粗车时 , 主轴转速600~800 r/min,进给速度 F120~F160,留精车余量 0.3~0.5 mm。②精车时,主轴转速 1 200~1 500 r/min,进给速度 F60~F80,采用一次走刀完成。③螺纹加工时,用 G76 粗车完成后,留给精车余量 0.1~0.2 mm, 再用 G92 指令精车三次,主轴转速 500 r/min
2.6 切削液的选择
在车削薄壁工件时 , 切削液是必不可少的, 应根据加工材料、加工性质和刀具材料等具体情况选用适当的切削液, 才会更有利于加工的进行。该企业他们统一用专用的冷却油,冷却效果明显,对工件和刀具的润滑作用很好。最后,进行科学编程并进行单件试制加工后调整,再批量生产。
3 、加工时的注意事项
①要遵守安全操作守则,安全文明生产。
②工件要夹紧,以防在车削时打滑飞出伤人和扎刀。
总之,通过实际加工生产,以上措施很好地提高了薄壁零件的加工精度,减少了工件装夹与校正的时间,降低了操作者的劳动强度,提高效率并保证加工后零件的质量,经济效益十分明显。
投稿箱:
如果您有机床行业、企业相关新闻稿件发表,或进行资讯合作,欢迎联系本网编辑部, 邮箱:skjcsc@vip.sina.com
如果您有机床行业、企业相关新闻稿件发表,或进行资讯合作,欢迎联系本网编辑部, 邮箱:skjcsc@vip.sina.com
更多相关信息