数控机床故障诊断方法探讨及应用
2020-7-2 来源:首都航天机械有限公司 作者:关进良 喻晓浩 岳维超
摘要:在了解数控机床组成和工作原理的基础上,针对数控机床各类复杂故障,提出了模块互换法、机电分离法、比较法、排除法以及PMC在线诊断法等五种典型的故障诊断方法,并结合实际维修经验,分别介绍了诊断方法的应用实例,最后总结了故障诊断的一般思路,具有较强的工作指导性和实用性。
数控机床是集机、电、液、气为一体的典型机电系统,结构复杂且自动化程度高,在我国制造业尤其是装备制造业的发展中,起到了不可替代的作用。由于数控机床本身的复杂性和多样性,使得机床故障受机械、电气、控制系统以及检测装置等多因素影响,引起同一种故障的原因也可能是多种多样的,而且故障停机直接影响着设备利用率和业的生产制造能力,因此在理解工作原理的基础上,总结分析故障诊断方法,并从根本上寻找快速排除故障的途径尤为必要。本文结合工作实践中的具体案例,对典型故障诊断方法进行深入分析和探讨。
1. 数控机床组成、工作原理
采用数控技术进行控制的加工设备称为数控机床,其基本组成如图1所示,现代数控机床一般采用计算机或微型计算机作为控制系统,称之为计算机数控系统(简称CNC)。数控机床加工工件时,将工件图样上的几何信息、工艺信息数字化,用NC代码编写加工程序并存储到程序载体内,然后借助输入装置将程序输入到CNC单元,并由CNC单元对程序进行译码、运算等综合处理后,向伺服系统和其他辅助控制装置发出指令信号,以驱动各运动部件和辅助动作,从而完成工件加工任务。数控机床可实现一次装夹、多工序连续加工,同时具有自动化程度高、加工精度高以及生产效率高等特点。
2. 数控机床故障诊断方法在实际维修中的应用
(1)模块互换法。数控机床的某一个模块(一般指编码器、光栅尺、伺服放大器及其电缆等)出现故障导致机床报警或异常现象,把该模块与另外一个同类(尽量是同型号)正常的模块互换,再观察故障现象并与互换前对比,来帮助维修人员定位故障点。
应用实例。故障现象:某数控龙门铣床在自动加工过程中,出现25000号报警:Y轴主动编码器硬件错误,下电重起后故障依旧。
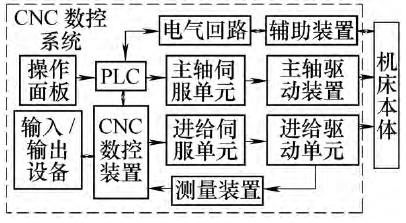
图1 数控机床组成框图
故障分析和方法应用:一般情况下,引起该报警的原因可能是光栅尺故障、编码器故障、反馈单元损坏以及中间连接电缆断裂或破损。若针对以上所有情况拆下逐一检查,则需耗费大量故障诊断时间。采用“互换”法,根据大量的维修记录得知,导致此报警最有可能的因素是光栅尺脏污或读数头损坏,现将Y 轴和X 轴光栅尺电缆线互换(电缆经测试正常,相当于把光栅尺互换),开机后X轴出现25000号报警,显然是Y 轴的光栅尺故障。进一步检测后发现,其读数头上一个“小钢珠”脱落,导致读数头在读取反馈数据时信号不稳定,更换读数头后故障排除。
小结:该方法的核心是“互换”,应用比较简单,前提是在交换某一模块时,机床的其他部件不能同时交换,即保证互换前后对比判断的可靠性。当引发某一报警的因素较多时,暂时缺少备件,可逐一对“可疑因素”与正常机床上同型号部件互换。如:伺服模块、检测模块、主轴模块以及各种电气元件均可进行交换。
(2)机电分离法。因数控机床是典型的高度机电一体化设备,故障原因可能是电气、机械甚至机电同时存在问题,很难直接判断故障点所在,可把机械部分和电气部分相对分离(脱开),再根据机电分离后的现象判断故障。
应用实例 。故障现象 :
V M C850立式加工中心空载时,数控系统负载监控界面显示主轴负载达到50%以上(过大,存在很大故障隐患),而正常值是5%左右,影响机床正常运行,不知是机械故障还是电气故障。故障分析和方法应用:该机床采用FANUC18-M数控系统,主轴和电动机使用同步带直连,示意图如图2所示,现采用“机电分离法”,将连接电动机与主轴的同步带拆掉,使机械部分(主轴本身)与电气部分(主轴电动机)完全脱开(见图3),手盘丝杠正常,再单独测试电动机,发现负载仍然是50%左右,从而判断是电动机本身问题,更换新电动机测试,负载显示是4%,故障排除。后续进一步检测电动机,发现根本原因是电动机轴承损坏,同时遥测定子绕组的绝缘电阻过小。
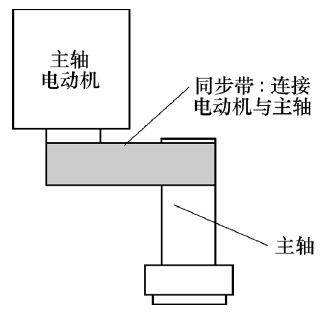
图2同步带直连示意图
小结 :机电分离法“ 化整为零”思想在故障诊断中的应用。机电分离后,“隐藏”在整体中的故障直接显现出来,起到了化繁为简的作用。此方法可延伸为“分离法”,除机电分离外,还可将其他需要“分离”的部分单独脱开来帮助诊断故障,如:全闭环改为半闭环,把光栅尺从测量反馈系统中分离。
(3)比较法。若机床的某一轴出现故障后,可通过测试本机床或同型号机床的同类型轴,加以对比发现问题的不同点,从而找出故障点并迅速排除故障。
应用实例。故障现象:
某数控龙门铣床在自动加工过程中,出现“A 轴电动机温度过热”报警而停机,停机2h后重起,报警仍旧存在。故障分析及方法应用:该机床采用西门子840D数控系统,有X 、Y 、Z 三个直线轴和A 、C两个旋转轴,一般情况下造成此报警的原因有3种:A轴3过载或过流导致电动机过热。电动机本身故障。温度传感器或其信号线损坏。首先,用温度仪测试电动机本身温度为室温,正常;然后分别测量A、C轴温度传感器的反馈线电阻,分别是60 000多Ω(接近断路状态)和650Ω,二者进行比较,A轴和C轴是同类型的旋转轴,二者阻值一般相差不大,但C 轴无报警,由此快速判A 轴温度传感器反馈线可能已经断路或破损,更换反馈线,故障排除。
小结:比较法可把“定性分析”转化为“定量分析”,并借助现场实测数据来诊断故障。选取比较对象时,要首选“同类对象”,保证具备可比性。
(4)排除法。引起某一故障有多项并列的原因,其中一项或几项均可导致相同的报警或故障现象。首先去掉所有可能的原因项,再依次单独接入电路,分别观察对应的现象,逐一排除“可
疑”项来诊断故障。
应用实例 。 故障现象 :
某数控镗铣床在执行加工程序过程中 , 突然出现 1 0 4 4 号报 警 ( M A C H I N E I S N O T READY),按复位键无法消除,同时电气柜中空开QF91跳闸,机床下电合上空开,重起机床约
5~10s后故障复现。
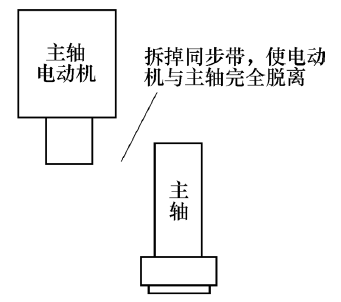
图3主轴与电动机脱开示意图
故障分析及方法应用:该机床采用FANUC18i-MB数控系统,具有x、Y、Z、W四个直线轴和B 、C 两个旋转轴。针对空开跳闸现象查阅机床电气图样(见图4),空开Q F91(D Z47-60 C6)上端接
DC24V电源,下端经中间继电器KA103和KA105,分别通过KA11至KA14控制四个直线轴的伺服电动机刹车装置。由于四个刹车线圈电源都来源于同一个空开QF91,任何一路长时间过载或者短路都有可能导致Q F91跳闸。采用排除法,首先将四个直线轴的刹车(虚线方框中)全部退出电路,即拔掉11、12、13和14号线,再分别恢复刹车电路并单独测试,结果是Y、Z、W三个轴的刹车正常(每路电流均小于1A),X 轴刹车接入电路时约5~10s后跳闸,电流约12A,已远远超过正常值,排除正常电路,故障定位在X 轴刹车。经进一步检测,X 轴刹车线圈已烧毁(电阻约为2Ω),因过流导致空开跳闸,更换刹车装置后故障排除。
小结 : 机床的刹车电路直接关乎到设备和人身安全,机床维护人员必须重点关注,一旦出现故障立即停车,切不可强制运行。除适用于上述一般电路外,排除法的适用范围可进一步延伸,如某些故障与CNC伺服模块或者PMC的I/O单元有关,每模块上接有多个插头(分别控制对应的功能),也可利用排除法,首先拔掉全部插头,再依次插上,逐个进行排除,当接上某一插头后故障复现,即可把故障定位于此。
(5)PMC在线诊断法。在数控机床加工过程中,C N C和P M C 协调配合共同完成对机床的精确控制,其中PMC主要完成与逻辑运算有关的功能,如刀具更换、主轴起停、换向变速、冷却液开断、工作台交换等辅助动作。
PMC梯形图能实时在线监测这些辅助动作,一旦某一动作在逻辑上出现问题,从梯形图中能及时显现出来,有助于故障的快速定位。
应用实例 。 故障现象 :
V M C 1 6 0 0 立式加工中心在刀库换 刀 过 程 中 , 出 现 1 0 1 2 # 报 警(MAGAZINE ORI. UP/DOWN ALARM)。按复位键报警消失,重新换刀仍然反复出现该报警。
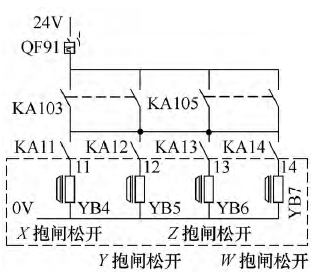
图4 机床电气图
故障分析及方法应用:此机床采用FANUC 0i-MC数控系统,刀库采用无机械手换刀方式,刀库的左、右和上、下移动由气缸驱动,旋转由调速马达驱动,自动换刀的一般步骤是:当数控系统接到换刀指令后主轴回到换刀位并准停→刀库向右移动到主轴处→主轴上的刀具进入刀盘卡槽→主轴松刀→刀库下移脱离主轴→刀库备刀(定位销抬起,刀盘旋转至指令对应的刀位)→刀库上移使刀具进入主轴锥孔内→刀具夹紧→刀库退回到原位。根据报警提示,在P M C中查询到1 0 1 2 # 报警对应的梯形图,如图5 所示,当刀盘转动之前,其定位销(固定刀盘,保证刀盘的定位精度)向上拔起,上端限位开关信号X7.6接通(X7.6→1),此时下端限位开关还未完全弹起(信号X7.7有一瞬间还处于1的状态),造成地址A1.4接通而报警,当按下复位键F1.1后,此时因下端限位开关已完全弹起(X7.7已由1→0),报警消失。经上述分析可知,故障原因显然是限位开关X7.7损坏失灵(内部锈蚀,弹起速度过慢),更换后故障排除。
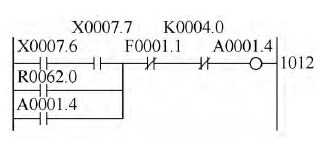
图5PMC梯形图
小结:加工中心换刀过程和P M C 程序比较复杂,逻辑性较强,利用P M C在线诊断法能直观地排查出“逻辑错误之处”,可快速从众多可能原因中找出故障点,达到捋清逻辑关系和追根溯源之目的。对于一些随机性、瞬间出现的故障,若梯形图中一些信号的“通断”(通断保持的时间极短)肉眼无法分辨,可使用PMC的信号跟踪功能(T R A C E),观测信号的时序和波形,来“捕捉”瞬间信号状态。
3. 结语
在对机床有一定认知的基础上,当数控机床故障出现时,进行诊断的一般思路是:大脑保持清醒,切不可手忙脚乱,根据报警提示或者故障现象,通过认真询问机床操作人员和查阅相关的机床资料,初步了解故障情况;大致判断出该故障可能和哪些因素有关,并根据自身的知识范围和工作经验,运用其中一种或综合运用几种诊断方法,做到有“法”可依并尽快定位故障点,
排除故障;针对该故障或者这一类故障进行总结(包括故障类型、诊断方式、维修细节以及注意事项等),这一点特别重要,对快速提高机床维修人员(尤其是初学者)的技术水平有“事半功倍”的作用,即先认真了解、再分析解决,最后总结经验。
投稿箱:
如果您有机床行业、企业相关新闻稿件发表,或进行资讯合作,欢迎联系本网编辑部, 邮箱:skjcsc@vip.sina.com
如果您有机床行业、企业相关新闻稿件发表,或进行资讯合作,欢迎联系本网编辑部, 邮箱:skjcsc@vip.sina.com
更多相关信息