不同磨损状态下刀具车削振动特性试验研究
2016-11-21 来源:江苏师范大学机电工程学院 作者:袁冠雷,李顺才,杨 睿,吴明明
摘要:对3种磨损状态的刀具进行车削试验,利用振动测试系统、压电式三向加速度传感器及Vib’SYS振动分析系统,采集车削刀具的振动信号,分析信号的时域和频域特征,研究3种刀具各向振动的加速度最大值和自功率谱密度均值随主轴转速的变化规律.研究表明:1)初期磨损和正常磨损的刀具振动特征值随主轴转速的变化规律相似,呈现先增大后降低的趋势;2)严重磨损刀具的振动特征值随主轴转速的增加而不断增大;3)不同磨损状态的刀具沿工件径向所受冲击最大,而振动能量主要沿轴向分布.
关键词:车削刀具;三向振动;自功率谱;时域分析;频域分析
0.引言
车削加工过程中,刀具与工件接触产生摩擦导致刀具的磨损.刀具的严重磨损会降低工件加工精度,劣化其表面粗糙度,加剧车削系统的振动,造成车削环境的噪声污染,减少设备使用寿命,降低生产效率.许多学者研究了机械加工中的振动机理及特性.张正义等[1]根据细长轴车削理论建立车削加工力学模型,通过Matlab 得到的振型函数与用ANSYS模态分析得到的仿真结果一致.郭瑞琴等[2]建立了三自由度再生型颤振的动力学模型并对刀具振动响应进行仿真研究,得出刀具切向上振动最大,轴向上次之,径向上最小.邵明辉等[3]通过试验研究了不同进给速度下刀具的三向振动响应.孟华等[4]利用QLVC-ZSA1振动信号分析仪及加速度传感器,对数控车床在不同切削要素的车削过程中刀具的振动响应进行了测试及量化研究.张强等[5]利用振动信号分析仪及压电式加速度传感器,研究了数控车床在不同进给速度下刀具上下表面的振动响应,得到了刀具振动加速度信号的时域曲线及自功率谱密度曲线.吴迪等[6]采用加速度传感器对振动信号进行监测,通过信号分析实现刀具磨损与振动信号的关联.谢厚正等[7]采用振动测试的监测方法进行刀具磨损的在线研究.陈会斌等[8]对采集的振动信号进行时域、频域分析,通过提取有效的特征量并结合工件表面粗糙度来判断刀具磨损的规律.目前对于刀具振动特性的试验研究成果较多,但不同磨损状态下刀具车削振动的量化研究有待深入.本文通过3种不同磨损状态刀具的车削试验,采集车削过程中刀具的三向振动信号,利用时域和频域分析研究不同磨损状态下刀具的振动响应特性.
1.试验设备
以CJK6163-MATE-360X570型数控车床为试验平台,切削方式为干切削.工件为直径45 mm 的铝棒.采用DCMT11T302-SM IC907 型硬质合金涂层刀片,选择3 种磨损状态的刀片:D1(初期磨损),D2(正常磨损),D3(严重磨损).采用压电式三向加速度传感器拾取刀具三向振动信号.传感器的X、Y、Z 方向分别接入测振设备的9、10、11通道,其中X、Y、Z 向分别对应轴向、径向及切向振动.
2.试验方案
采用单因素试验方法对3种磨损状态的刀具分别进行不同主轴转速下的车削试验.设定进给速度f、背吃刀量e 及主轴转速n.对刀具进行车削试验时,更换不同磨损状态的刀具时要同时更换工件,每次车削试验中工件的材料及尺寸相同.设定采样频率1000 Hz,采集时间1 min.试验的编号为S1~S12,试验方案如表1所示.
表1 车削试验方案
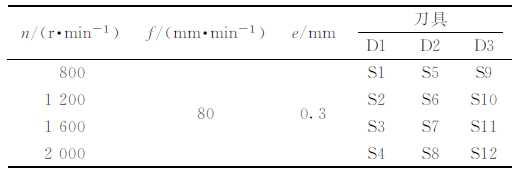
3.试验结果及分析
对振动信号一般采用时域和频域分析.时域分析的特征值包括均值、最大值、最小值、均方值等.振动信号的时域均值反映平均振动能量,而最大值、最小值指标在一定程度上反映出振动信号是否含有冲击成份.常用的频域分析方法有幅值谱、功率谱以及相位谱等.幅值谱表示了振动物理量的幅值随频率分布的情况,功率谱表示了振动物理量的能量随频率的分布.本试验中分别采用振动加速度最大值及自功率谱均值研究振动信号的时域及频域特征.
3.1 振动信号的时域分析
根据试验方案进行车削试验,利用测振设备和Vib’SYS信号采集、处理和分析软件,得到刀具振动加速度的时域曲线,记录不同磨损状态的刀具在不同主轴转速下各通道加速度的最大值amax,绘制不同状态的刀具三向加速度amax随着主轴转速n 的变化曲线,如图1所示.
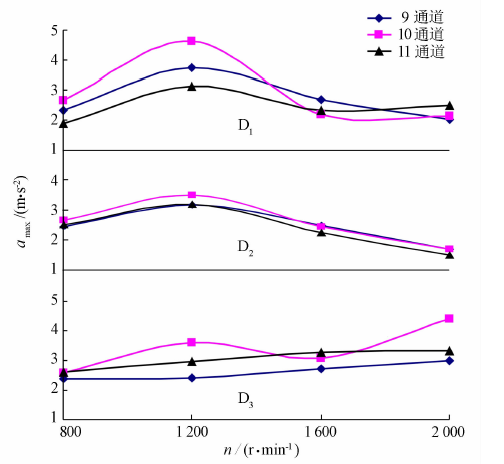
图1 不同刀具三向振动amax-n 曲线
由图1可知:
1)初期磨损和正常磨损的刀具,随着主轴转速的升高,3个方向振动的加速度amax先增大后减小;当主轴转速为1200r/min时,amax都达到最大值.
2)对于严重磨损的刀具,随着主轴转速的升高,三向加速度amax不断增加.
3)对于不同磨损状态的刀具,3个通道中第10通道(对应于径向加速度)的amax变化最显著.考虑到3种不同磨损状态的刀具其径向振动的变化最显著,绘制不同刀具的径向加速度amax-n 曲线,如图2所示.
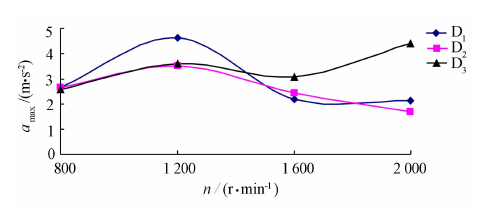
图2 不同磨损刀具的径向加速度amax-n 曲线
由图2知:
1)较低转速下,初期磨损刀具径向振动加速度amax值最大.这是因为初期磨损状态的刀具由于表面粗糙度和应力分布的不均匀等原因,在车削过程中磨损速度较快,其振动变化也比较显著.增大主轴转速,可以有效降低初期磨损刀具的加速度amax.
2)正常磨损的刀具,由于刀具表面粗糙度和应力分布比较均匀,因而随着主轴转速的增大,刀具的振动加速度amax逐渐减小.
3)严重磨损状态的刀具,已无法正常使用.随着主轴转速的增大,刀具的径向振动加速度amax显著增大.
3.2 振动信号的频域分析
利用Vib’SYS系统进行频域分析,得到相应于图1的自功率谱曲线,计算各信号的自功率谱均值¯ρ,并绘制不同主轴转速下的变化曲线,如图3所示.
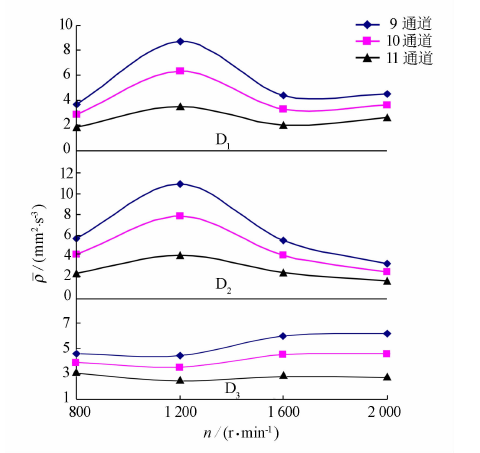
图3 不同刀具各通道的 ̄ρ-n 曲线
根据图3分析可得:
1)初期磨损和正常磨损刀具的自功率谱均值随主轴转速的变化趋势基本一致,其值随主轴转速先增大后减小,在转速为1200r/min时达到最大。
2)严重磨损刀具的自功率谱均值随着主轴转速的增大而增大,当主轴转速增大到1600r/min后趋于稳定。
3)相同转速下,3种磨损状态的刀具在9通道(对应于轴向振动)的自功率谱均值最大.考虑到3种不同磨损状态的刀具其轴向自功率谱均值¯ρ 最大,绘制不同刀具轴向振动的¯ρ-n 曲线,结果见图4。
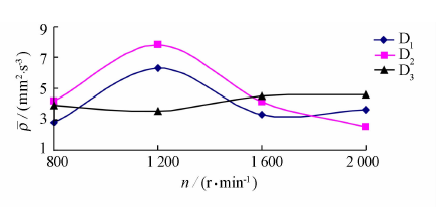
图4 不同刀具轴向振动的 ̄ρ-n 曲线
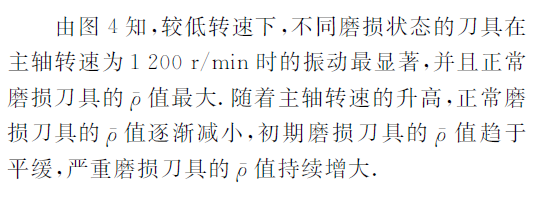
4.结论
在给定进给速度及背吃刀量时,改变主轴转速,研究3种磨损状态刀具的车削振动特性.对振动信号进行时域分析和频域分析,得出以下结论:
1)随着主轴转速的升高,初期磨损和正常磨损的刀具所受冲击不断减小,而严重磨损的刀具所受冲击不断增大.当主轴转速为1200r/min 时,3 种磨损状态的刀具在径向所受冲击最大.
2)在车削过程中刀具的振动能力主要分布在轴向,且在主轴转速为1200r/min 时振动能量最大.
3)相同车削条件的较高转速的车削试验中,严重磨损刀具的振动最剧烈,初期磨损刀具次之,正常磨损刀具振动最弱.
投稿箱:
如果您有机床行业、企业相关新闻稿件发表,或进行资讯合作,欢迎联系本网编辑部, 邮箱:skjcsc@vip.sina.com
如果您有机床行业、企业相关新闻稿件发表,或进行资讯合作,欢迎联系本网编辑部, 邮箱:skjcsc@vip.sina.com
更多相关信息