数控加工中心刀具和切削用量的选择
2016-12-8 来源:福建三明林业学校 作者:林峰铭
摘要:刀具是机床实现切削加工的直接执行者,刀具的选择和切削用量的选择合理与否,不仅影响到被加工零件的质量,甚至可以决定机床功效的发挥和安全生产的顺利进行。所以,在编加工程序时要选择合理的刀具和切削用量,不但可以有效提高切削效率和加工质量,还可降低成本以获得最佳经济效益。在数控铣上加工零件,保证零件加工质量是非常重要的,我们不仅要充分发挥机床本身的性能,更为重要的是刀具和切削用量的确定是十分重要的,刀具的选择和切削用量的确定是提高加工质量和加工效率的关键。
关键词:数控加工中心;刀具;切削用量
引言:
刀具选择与切削用量确定是数控铣加工中十分重要的环节,直接关系到加工精度、加工表面质量、加工效率。选择合适的刀具和切削用量可使加工以最低的成本、最短的时间达到最佳的加工质量。在切削加工中,切削用量和刀具对加工精度、表面质量、生产效率和生产成本会产生较大的影响。加工速度快、生产效率高是数控加工相比传统切削加工的优势,在“优质、高产、低成本”这一大的原则下,切削用量和刀具能否正确选择和使用对数控加工发挥其优势有较大的影响。
一、数控加工刀具的选择
数控铣床的加工效率,加工质量与铣刀的选择有直接的关系。在数控铣床加工工艺中有着重要意义。数控铣床加工对刀具的要求更高,要求具备精度高、强度大、刚度好、耐用度高,而且要求尺寸稳定、安装调整方便。刀具及刀柄正确选择应根据机床的加工能力、工件材料的性能、加工工序、切削用量等因素来选择。刀具选择应遵循的原则是:安装调整方便、刚性好、寿命和精度高。在满足加工要求的前提下,尽量选择较短的刀柄,以提高刀具加工时的刚性。
(一)数控铣削加工常用刀具的种类
数控铣削刀具按结构可分为整体式、镶嵌式。镶嵌式包括焊接式、机夹式。刀具按材料可分为特殊形式、高速钢刀具、硬质合金刀具、金刚石刀具、立方氮化硼刀具、陶瓷刀具。加工工艺分为钻削刀具、铣削刀具、镗削刀具。按刀具形状分为平底刀、球头刀、锥度刀、T 形刀、桶状刀、异形刀。
(二)数控加工刀具的选择
1、刀具的选择
在进行自由曲面(模具)加工时,由于球头刀具的端部切削速度为零,因此,为保证加工精度,切削行距一般采用顶端密距,故球头常用于曲面的精加工。平头刀具在表面加工质量和切削效率方面都优于球头刀,因此,只要在保证不过切的前提下,无论是曲面的粗加工还是精加工,都应优先选择平头刀。另外,刀具的耐用度和精度与刀具价格关系极大,必须引起注意的是,在大多数情况下,选择好的刀具虽然增加了刀具成本,但由此带来的加工质量和加工效率的提高,则可以使整个加工成本大大降低。在加工中心,各种刀具分别装在刀库上,按程序规定随时进行选刀和换刀动作。因此必须采用标准刀柄,以便使钻、扩、铰、镗、铣削等工序用的标准刀具迅速、准确地装到机床主轴或刀库上去。编程人员应了解机床上所用刀柄的结构尺寸、调整方法以及调整范围,以便在编程时确定刀具的径向和轴向尺寸。
2、刀具切削寿命与切削用量之间的关系
制定切削用量时,先应考虑刀具寿命,根据刀具寿命选择刀具的原则是:根据刀具复杂程度、制造、磨刀成本选择。复杂和精度高的刀具寿命应选得比单刃刀具高些。对于机夹可转位刀具,由于换刀时间短,为了充分发挥切削性能、提高生产效率,刀具寿命可选得低些,一般取15 ~ 30min。对于装刀、换刀、调刀比较复杂的多刀机床、组合床与自动化加工刀具,刀具寿命应选得高些,尤其要保证刀具可靠性。大件精加工时,为保证至少完成一次走刀,避免切削时中途换刀,刀具寿命应按零件精度和表面粗糙度确定。
3、刀具材料的选择
所选择的刀具要有足够高的硬度,以适应高压力、高温度和和剧烈摩擦,一般情况下刀具材料的硬度至少要在工件材料的硬度以上60HRC;要有较好的耐磨性,较好的耐磨性可以减少刀具的磨损,从而延长刀具的使用寿命;要有较高的韧性,只有具有足够好的韧性,才能承受切削力、冲击和工艺系统的振动;为保证刀具的硬度、耐磨性和韧性在高温下不发生或仅产生较小的变化,要求刀具材料的耐高温性能要好;刀具材料良好的工艺性也是重要的一个方面,这有利于刀具的维修和制造。如表1 所示。
表1 常用刀具材料的性能比较
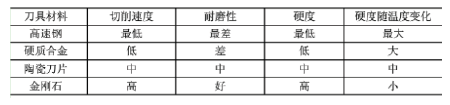
二、切削用量的选择
铣削加工切削用量包括切削速度、进给速度、背吃刀量、侧吃刀量。切削用量主要影响切削力、切削功率、刀具磨损、加工质量和加工成本。切削用量的选择应遵循以下原则:在保证零件加工精度和表面粗糙度的前提下,应充分发挥刀具的切削性能和刀具的耐用度,同时充分发挥机床的性能,对于不同的加工方法需选用不同的切削用量,编程人员在编程时应确定每到工序的切削用量,这样可最大限度提高生产效率、降低加工成本。
(一)背吃刀量ap 的选择
车削加工一般情况下可以分为粗车、半精车和精车。粗车(Ra 为50 ~ 12.5μm)时,全部加工余量尽可能在一次走刀过程中切除,在中等功率的机床上,背吃刀量可以取为8 ~ 10mm。半精车(Ra 为6.3 ~ 3.2μm)时,背吃刀量可以取为0.5 ~ 2mm。精车(Ra 为1.6 ~ 0.8μm)时,背吃刀量可以取为0.1 ~ 0.4mm。在碰到以下情形时,粗车一般最好分几次走刀。首先,工件所留的加工余量过多时,一次走刀会使切削力太大,会出现机床功率不足或刀具强度不够的情况。其次,工艺系统的刚性不够,或者工件的加工余量非常不均匀,这两种情况造成车削过程中引起很大的振动时。第三,在断续切削中,刀具因受到很大冲击而打刀时。在以上情形中,如果需要分两次走刀,那么第一次走刀的背吃刀量要尽可能取的大一点,第二次走刀的背吃刀量要尽可能的取小一点,才能保证精加工的刀具具较长的刀具使用寿命,高的加工精度和较小的表面粗糙度。第二次走刀时,背吃刀量可以取加工余量的1/3 ~ 1/4 左右。
(二)进给速度f 的确定
在数控车削加工中,粗车时,一般没有太高的工件表面粗糙度要求,这时切削力一般情况下很大,所以合理的进给量f 等于是工艺系统能承受的最大限度的进给量。这一进给量受到下列一些因素的限制:车刀刀杆的强度及刚度、车床进给机构的强度、刀片的强度和工件的装卡刚度等。进给量包括进给速度(fυ)和每齿进给量。切削刃上的的选定点相对于工件的进给的瞬时速度称为进给速度。刀具在进给运动方向上相对工件的位移量称为进给量,单位mm/r。半精加工和精加工主要目的是提高零件的表面质量和加工精度,不能盲目增大切削深度,依据粗加工时剩余的余量,采用切削深度逐刀减小的方法,使得加工精度和表面质量逐步提高。进给速度选择的过大会降低加工精度和表面质量,在半精加工和精加工时一般20 ~ 50mm/min 是合理的选择区间。
(三)切削速度vc 的确定
1)切削速度vC与积屑瘤高度Hb 的关系。因为积屑瘤的顶部特别不稳定,易破裂,并且破裂的一些碎片可能会粘在已经车过的表面上;积屑瘤使刀具切入深度增加了一个Δh,且积屑瘤会周期性的产生、生长、脱落,导致Δh 也周期性的增加和减小,它变化有可能引起振动,所以在精车时应该选择合理的切削速度,以避开积屑瘤的最易生成的车削速度区域。在低速车削Ⅰ区不产生积屑瘤;在Ⅱ区中积屑瘤高度随切削速度增大而加大到最大值;在Ⅲ区内积屑瘤高度随车削速度增加而减小;在Ⅳ区内积屑瘤不再产生。因此,在实际生产加工中,切削速度要尽可能避开中速区。2)切削速度的确定。根据选定的背吃刀量ap,进给量f 及刀具寿命T,按下列公式计算

但是大多数时候,人们往往是选择直接从切削速度经验参考值表直接查询而得(见表2)。
表2 铣削加工切削速度参考表
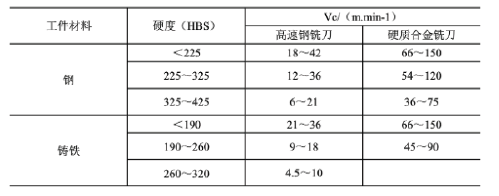
三、结束语
随着数控加工中心机床的发展,加工工艺要求的不断提高,数控加工的方法也更加多样化,从简单的手工编程到复杂的曲面软件编程,同时对切削刀具的要求也更加精确、多样。在某些加工环节,实现了加工工艺的要求就是任务完成,而有些加工生产任务,是讲质量、讲效益、讲效率的。只有合理地选择切削刀具和切削用量,才能保证任务的顺利完成,同时也使效益最大化。
投稿箱:
如果您有机床行业、企业相关新闻稿件发表,或进行资讯合作,欢迎联系本网编辑部, 邮箱:skjcsc@vip.sina.com
如果您有机床行业、企业相关新闻稿件发表,或进行资讯合作,欢迎联系本网编辑部, 邮箱:skjcsc@vip.sina.com
更多相关信息