曲轴复合车床随动刀架动平衡分析及优化
2017-1-20 来源:武汉理工大学机电工程学院 作者:黄继雄,晏少亚,赵黎明
摘要:曲轴复合车床采用随动刀架对连杆颈进行随动车削加工具有诸多优点,由于刀架在随动车削时随工件高速转动,若设计不当或平衡不好时会产生较大的惯性力与惯性力矩,严重影响加工效率和加工精度。提出针对随动刀架的一种新的动平衡配重方法,将刀架三维模型导入ADAMS仿真,并对平衡块质量进行优化,取得了良好的动平衡效果,为刀架的动平衡设计提供了一种新方法。
关键词:随动刀架;动平衡;动力学仿真;优化
发动机曲轴连杆颈的传统粗加工工艺具有以下特点:以连杆颈轴线为工件旋转中心对其进行车削加工,导致整个曲轴的质心偏离旋转中心轴线,从而产生较大的惯性力及惯性力矩。为避免因工件惯性力过大而导致工艺系统振动,一般设置切削速度为40~60r/min,仅为最佳切削速度的1/10,生产效率较低。而曲轴复合车削机床以曲轴主轴为工件旋转中心,随动刀架随动切削的方式对连杆轴颈进行加工。理论上工件在旋转过程中不存在惯性力,因此工作转速范围可达300~600 r/min.,是一种加工速度、效率、精度都比较高的切削加工设备。由于其随动刀架为平行四边形机构,当刀架高速工作时,属于偏心旋转,会产生很大的惯性力和惯性力矩,从而产生扎刀、冲击载荷与振动等现象,降低刀架机构的传动效率和缩短使用寿命,严重降低了曲轴连杆轴颈的加工精度。因此必须对刀架进行动平衡,消除或者减小刀架机构的惯性力和惯性力矩,从而减少刀架振动,保证工件的加工精度。
1.随动车削加工原理
曲轴复合车床随动刀架采用平行四边形的形式,其曲柄的长度与加工曲轴连杆轴颈中心线偏心距一致[2],连杆一端延伸部分安装刀具。工作时,曲轴绕其主轴中心线高速旋转,刀架的曲柄与曲轴的曲柄作同相位同转速的旋转运动:曲轴连杆轴颈相对于随动刀架上的刀具作定轴转动,转动半径为曲轴连杆轴颈半径,从而实现对轴颈的车削。刀架加工原理简图如图1所示。
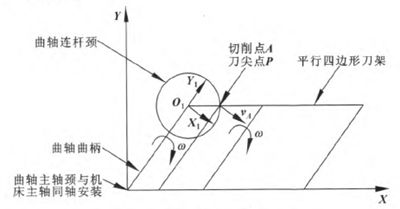
图1刀架机构加工原理图
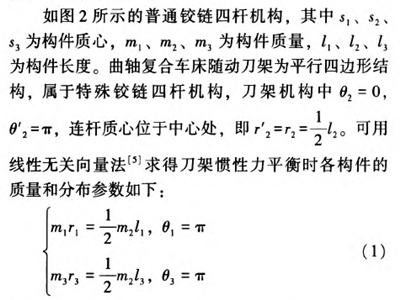
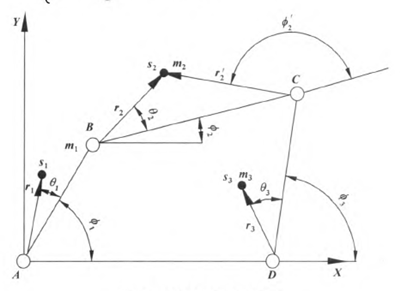
图2普通铰链四杆机构
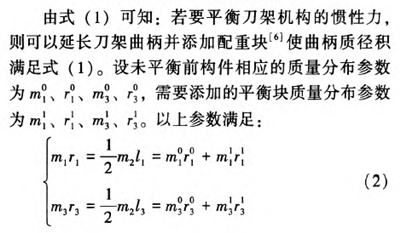
由式(2)可确定平衡惯性力所需的配重参数。通过以上分析采用在前后曲柄两端添加配重块的方式对刀架机构进行惯性力、惯性力矩的平衡。设计曲柄为滑板形式可实现曲柄长度的调节,配重块亦通过滑板连接。通过SolidWorks设计的平衡刀架三维模型见图3。
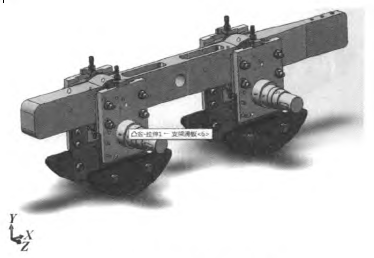
图3平衡刀架三维模型
刀架模型质量分布数据见表1,将表1中参数代入刀架平衡公式,可求得单块配重块质量为3.90 kg。
表l刀架模型质量分布参数
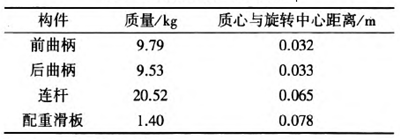
3.刀架动平衡优化
将平衡刀架三维模型以ParaSolid格式导入到ADAMS中¨]。为了降低仿真模型的复杂程度.不考虑螺栓的质量。统一将螺栓连接的两构件通过布尔操作结合在一起,在其余各构件连接处添加约束关系,添加的约束见表2。
表2模型之间的约束
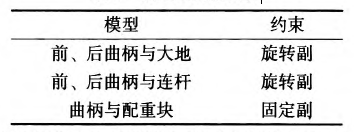
设计前曲柄的旋转轴通过同步带带动后曲柄的旋转轴实现驱动的传递,以减少冲击。所以要另外创建1个由2个旋转副组成的耦合副。创建约束后,将切削力载荷添加到连杆安装车刀的一端,x方向切削力为790 N,Y方向为一2 900 N【8 J。刀架的转动速度为600 r/min。创建设计变量DV一1,初始值为3.90 kg,在一定范围内进行变化∽J。设置单块配重块质量关联设计变量DV一1。由于惯性力平衡后,惯性力矩能同时平衡,且惯性力在x、】,方向变化规律相同,故以惯性力在x轴分量为优化对象,建立惯性力X轴分量测量函数。以单块配重块质量为优化变量,以惯性力x轴分量最大值最小为优化目标进行优化Ⅲ1。考虑最大速度工况,在前曲柄与大地之间的旋转副添加旋转驱动,转速设为3 600。/s,并设置仿真时间0.2 s、仿真步数100。虚拟样机见图4。
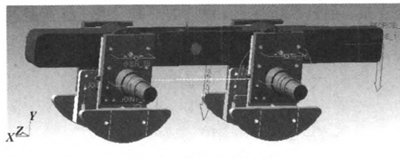
图4刀架虚拟样机
经过多次优化计算得到优化过程见图5。从图6可看出单块配重块质量对惯性力x分量最大值的影响,得到最优配重质量3.876 kg,此时惯性力x分量最大值为0.77 N。同理可得出惯性力y分量变化图及惯性力矩变化图。
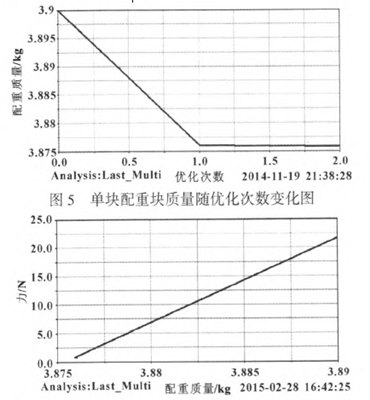
图6惯性力X分量最大值随单块配重块质量变化图
由图7—9可看出惯性力x、y分量变化图。图10、11显示惯性力矩变化图。瞌线均呈现周期性变化,体现刀架旋转运动的特点,也是刀架振动的原因。添加配重块后惯性力x、y分量及惯性力矩最大值明显减小,平衡效果显著。
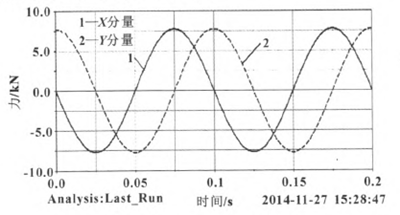
图7未平衡前惯性力随时间变化图
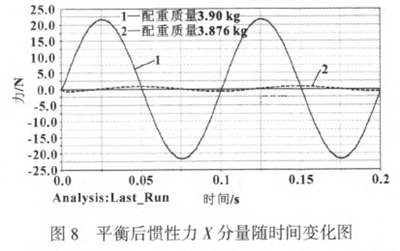
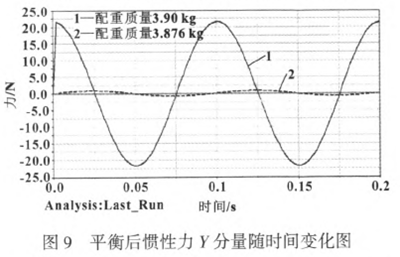
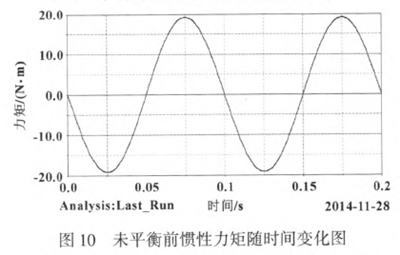
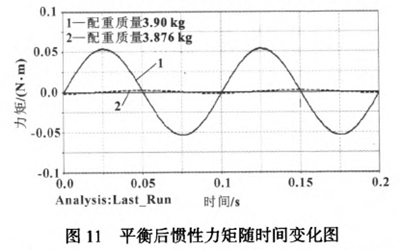
优化的配重块质量、理论计算配重块质量与未加平衡质量的刀架惯性力及惯性力矩仿真结果见表3。
表3平衡效果表
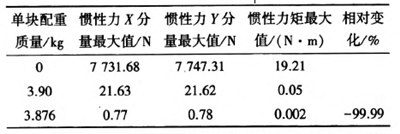
通过表3可知添加配重块的方法能大幅度减小惯性力及惯性力矩。在理论计算的基础上,通过虚拟样机技术对配重质量进行优化,得到最优配重,基本能消除惯性力及惯性力矩对刀架正常工作的影响。优化结果能明显提高刀架运动的平稳性,从而可以有效减小机床振动与噪声,提高曲轴加工效率与精度。
4.结束语
采用配重法对刀架惯性力及惯性力矩进行平衡,用SolidWorks设计平衡刀架模型后导入ADAMS对理论配重质量进行优化。通过仿真对比,不仅验证了配重法可以大幅度减小刀架惯性力及惯性力矩,而且得到更优化的配重质量。基本消除了惯性力及惯性力矩,对刀架的动平衡设计有一定的指导意义,同时可为其他连杆机构的动平衡以及机床减振提供一种新的研究方法。
投稿箱:
如果您有机床行业、企业相关新闻稿件发表,或进行资讯合作,欢迎联系本网编辑部, 邮箱:skjcsc@vip.sina.com
如果您有机床行业、企业相关新闻稿件发表,或进行资讯合作,欢迎联系本网编辑部, 邮箱:skjcsc@vip.sina.com
更多相关信息