宏程序在微小孔加工效率提升的应用研究
2017-11-13 来源: 南京科技职业学院 作者:吴苗苗
摘 要:本文通过对微小孔加工过程研究,根据实际钻孔参数,运用数控系统中固定循环指令编程,实际加工效率低,小钻头容易断。通过我们改进编程,运用宏程序模拟钻孔循环运动轨迹,优化各阶段进给速度编程,从而提高微小孔加工的效率。达到实际生产的高效性和安全性。
关键词:宏程序;微小孔加工;优化编程;提升效率
在教学和实际生产过程中遇到过这样一批产品,加工ф0.2mm的小孔,如图1所示:
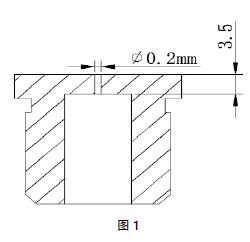
1、 工艺分析
如图1所示,这是一件化工喷嘴零件加工,材质是碳钢,先前工序都已加工完成,最后一道工序是加工ф0.2mm的通孔,理论深度3.5mm,我们将运用ф0.2mm的钻头对其进行加工,为保证是通孔,实际加工深度大于3.5mm。我们运用的设备是数控立式加工中心,系统是FANUC 0i-MC。
2 、实际加工过程研究
2.1 钻孔固定循环(G83)编程加工
2.1.1 由于首次遇到此类产品的加工,没有实际的加工经验,固先运用数控系统中孔加工固定循环编程,对产品进行试切,主体程序如下所示:
G0G54G90G17G40;(调坐标系)
M3S10000;(主轴转速设定)
G43H1Z50;(FANUC系统调刀具长度)
G98G83X0Y0Z-3.7R1Q0.05F3(钻孔固定循环编程)
G80Z50;
M5;
M30;
2.1.2 根据孔的实际大小,材质,选用的钻头及加工设备等因素考虑,确定加工的切削参数,主轴转速为10000转,每次钻深为0.05mm,钻切速度为3mm/min,以此参数运用固定循环编程加工,第一件成功完成,单间加工耗时28分钟,由于此产品要加工1000多件,这样的速度完全达不到生产的要求,由于钻孔固定循环参数的局限性,只能改钻深深度和钻切速度来提高钻孔效率,而且钻切的速度是恒定的不能分阶段改变速度,我们试切了好几个产品,都没有成功,钻头总是断,改回原来参数加工,可以生产,就是速度太慢,因此我们想到了宏程序,利用宏程序的灵活性,替代固定循环编程。
2.2 宏程序编程
2.2.1 总结钻孔固定循环(G83)规律
宏程序是指采用宏变量及利用公式来编写的程序,只要我们能找到钻孔循环的规律,就能编写出宏程序,替代钻孔固定循环。
钻孔固定循环G83指令格式:G83XY-Z-R-Q-F-I-K-P-;指令各参数含义:X-Y-:孔位数据;Z-:从R点到孔底的距离;R-:从初始位置到R点的距离;Q-:每次切削深度;F-:切削进给速度;I-:前进或后退的移动速度;K-:重复次数;P-:在孔底停留时间。指令钻孔分步图解,如图2所示。
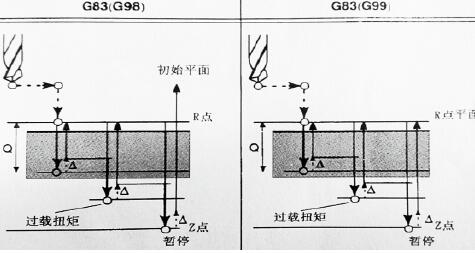
图2
根据图解分析,钻头沿X和Y轴定位,沿Z轴定位到R点,沿Z轴钻孔,第一次钻孔,切削深度Q,增量值,后退(孔底到小空程□),增量值,后退(孔底到R点),前进R点到离孔底空程高度□的点,钻孔第2次或以后的钻孔,切削深度Q+□,增量值,暂停,沿Z轴返回到R点或初始平面,循环结束。
根据图样分析,得出钻孔固定循环运动轨迹规律,由规律转化成宏程序语言,其中钻孔深度设为变量,用#1表示,切削起始点为#1+0.1mm,空程速度用F2表示,钻孔速度用F1表示,抬刀排削速度用F3表示,实际用宏程序编程钻头运动轨迹,如图3所示。
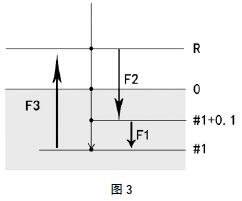
2.2.2 宏程序编制
根据实际生产加工经验,其中空程速度F2设定为50mm/min,钻孔速度F1设定为3mm/min,抬刀排削速度F3设定为100mm/min,每次钻孔深度变量为0.05mm。根据运动轨迹图,编制宏程序如下:
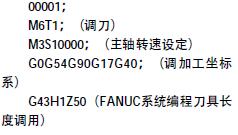
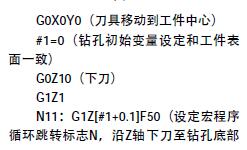
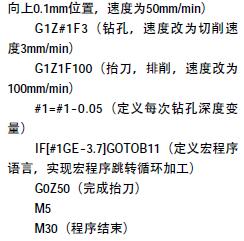
运用此程序,对工件上的小孔进行重新加工,由于进刀速度的变化,减少了空程运动的时间,切削起点的设定,减少了空程运动的长度,优化了运动轨迹,单件加工完成,实际耗时只需8分30秒的时间,钻头使用了合理的加工切削参数,也不容易断,加工效率大幅度的提高了,给企业创造了更多的经济价值。
结语
本文通过对宏程序在微小孔加工中编程的应用研究,体现了宏程序在这一类微小孔加工编程中的优势,替代系统固有的钻孔循环,减少了加工时间及加工损耗,提升了加工效率,希望能给这些领域的企业在加工方面有一定的启发和帮助。
投稿箱:
如果您有机床行业、企业相关新闻稿件发表,或进行资讯合作,欢迎联系本网编辑部, 邮箱:skjcsc@vip.sina.com
如果您有机床行业、企业相关新闻稿件发表,或进行资讯合作,欢迎联系本网编辑部, 邮箱:skjcsc@vip.sina.com
更多相关信息