曲轴粗车刀崩刃问题浅析
2023-5-8 来源: 上汽通用五菱汽车股份有限公司重庆分公司 作者:张晓刚 许雷明
车刀崩刃是车削加工过程中常见的问题,考虑到曲轴沟槽加工表面要求高、重复定位精度等因素,崩刃件一般无法返工,且目前无其他手段监控崩刃情况,仅能通过目视判断,造成曲轴的批量报废,刀具损坏、CPU 增加等情况,存在质量风险。粗车刀崩刃影响因素多样,我司前期通过人、机、料、法及环多方向分析验证锁定设备精度、加工参数、余量分配三点关键因素,本文通过对前期攻关过程进行总结,分析关键因素对粗车刀崩刃问题的影响,找到症结,攻克崩刃问题。
生产现状
某公司一条年产 30 万件四缸铸铁曲轴生产线上,生产 N15/N12 两种机型,因两种机型皆存在崩刃问题且表现类似,下文以 N15 机型为例进行分析。OP20 工位负责曲轴主轴颈、法兰盘、芯轴端及链轮端的粗、精加工,采用的装备是配有自定心中心架的双刀盘型 5 轴联动的德国产 Boehringer 车拉机床。
生产中左刀盘负责 A4/A5/HUB/ 法兰端面、外圆面及沟槽的加工,右刀盘负责 A1/A2/A3/ 链轮 / 芯轴相应特征的加工。轴径外圆粗车刀(以下简称粗车刀)分为 A1 粗车刀、A2/A3 粗车刀、A4/A5 粗车刀。加工过程工件姿态如图 1 所示,面对机床观看法兰侧靠左,芯轴侧靠右,故下文中加工法兰侧粗车刀命名为左粗车,芯轴侧粗车刀命名为右粗车。
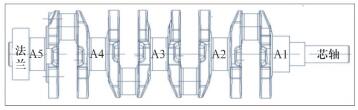
图 1 加工过程姿态、轴径命名示意图
2020 年整年 OP20 工位粗车刀崩刃 59 次,生产过程月均崩刃次数 5.4 次 / 月,相比较于2016-2017 每月平均崩刃频次为 1.1 次增加了 4.3次 / 月,崩刃频次明显变多。统计 2020 年整年粗车刀崩刃于各轴径的分布情况,绘制如图 2 所示的柏拉图。由图可知 A2/A3 粗车刀崩刃占比最大,A2/A4 左粗车和 A4/A5 左粗车崩刃次数占全年粗车刀崩刃次数的 76.72%,是 OP20 车拉工位粗车崩刃问题的症结所在。在其他问题不增加的情况下,解决 A2/A3 左粗车及 A4/A5 左粗车问题后,OP20 工位粗车刀崩刃频次将降低为 1.27 次 / 月,与 2016~2017 年崩刃频次基本持平。
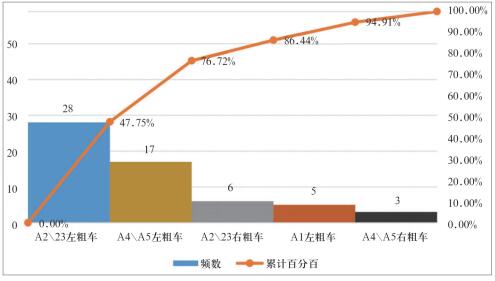
图 2 崩刃分布
车拉加工工艺曲轴车拉加工主轴颈(A1 无开槽加工)主要工步包含开槽刀加工、左右粗车加工、左右沟槽加工和拉刀修整加工,加工部位及刀具结构如图 3 所示,整个加工过程中,粗车的粗车刀加工余量最大,需加工侧壁和粗车轴径外圆面。
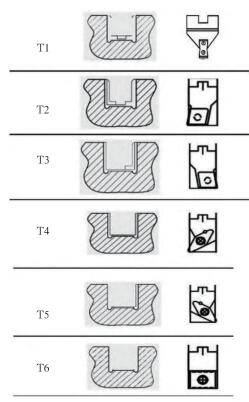
图 3 工位刀片介绍
崩刃产生的原因
曲轴主轴径外圆加工粗车刀崩刃原因主要为方法和机床两个方面 : ①在方法方面包括机床加工参数、各把刀具间的余量分配等因素 ; ②在机床方面包括刀盘垂直度、顶尖圆跳动等设备精度问题和设备原点变动等因素。
设备精度对崩刃问题的影响
对 OP20 车车拉设备刀盘垂直度、卡盘圆跳动进行检查,检查结果见表 1。
表 1 设备精度检查结果
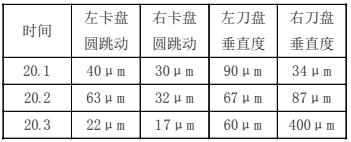
供应商推荐刀盘垂直度及卡盘圆跳动小于20 μm,检查结果有明显超差情况,结合设备结构分析,刀盘垂直度、卡盘圆跳动会导致刀片加工过程中局部切削余量变大,瞬时加工应力增加引发崩刃。团队对设备精度进行调整后,调整过程及精度变化见表 2。调整 OP20 三台设备刀盘垂直度、卡盘圆跳动至≤ 20 μm,跟踪生产一个月累计崩刃 4 次,措施有效,精度对问题解决贡献率为 :1-[4( 次 / 月 )/5.4 次 / 月)]=26%。
表 2 调整前后进度对比
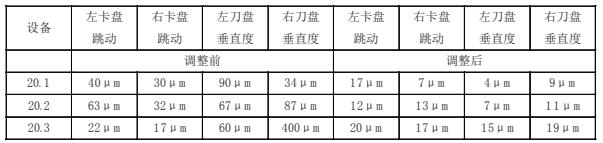
表 3 粗车刀 Z 向加工余量
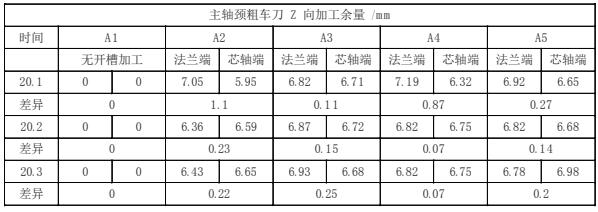
加工余量对崩刃问题的影响刀片的加工余量(图 4)直接关系到加工过程中刀片受热、应力变化。结合上文介绍的加工工艺,开槽刀的加工深度、轴向加工位置会影响左右粗车刀的加工余量,粗车刀和拉刀(最终尺寸加工刀)的余量分配也直接影响了粗车刀的加工余量。
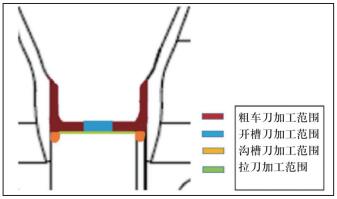
图 4 工位刀片加工余量示意图
结合毛坯(图 5)及 OP20 成品尺寸计算和测量各个轴径左、右粗车刀在轴向(Z 向)和径向(X 向)的加工余量如表 3、表 4 所示。
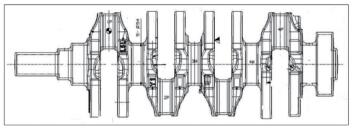
图 5 产品毛坯尺寸
表 4 粗车刀 X 向加工余量
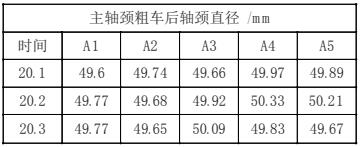
我司通过多次测量收集粗车刀轴向、径向的加工余量发现 :
(1)OP20.1 设 备 主 轴 颈粗车加工 Z 向余量,A2 左粗车加工余量比右粗车加工余量大1.1mm,A4 左粗车比右粗车大 0.85 mm,其他轴径最大差异皆小于 0.3 mm,与上文统计信息中左粗车崩刃频次大于右粗车现象相呼应。
(2)观察主轴颈粗车后轴颈直径,三台设备部分轴径完成粗车加工后直径小于 49.7 mm,已经达到 OP20 工位成品尺寸要求(49.6±0.1)mm,并且主要集中 A2/A3 轴径,与上文统计的粗车崩刃频次统计相对应。
分析加工程序,主轴径粗车刀加工毛坯面,将主轴径从 φ54 mm 加工至 φ49.9 mm(实际加工靠设备原点保证),理论轴 向 加 工 余 量4.1 mm。 拉 刀保证最终成形尺寸,将轴径由φ49.9 mm 加工至 49.6 mm,理论加工余量 0.3mm。部分轴径实际加工余量与理论加工余量差异较大,通过重新调整设备原点后解决。
加工余量过大是导致崩刃的直接因素,综合我司多年的加工情况,极少发生拉刀崩刃情况,故团队通过多次调整优化将粗车刀加工尺寸由 φ49.9修改为 φ50.2(增加拉刀加工余量 0.3mm),优化后跟踪粗车刀崩刃频次明显好转。
加工参数对崩刃问题的影响
加工参数主要指切削速度、加工进给,切削速度对刀具寿命有很大的影响,切削速度过高时,导致切削温度上升,刀具寿命大大缩短 ;相反切削速度过低,切削易产生振动,切削过程中刀具和工件不停敲击使刀尖产生微小裂纹
和崩刃,刀具寿命缩短。
调整加工参数,在满足生产节拍的情况下验证加工参数对粗车刀崩刃的影响。我司多次调整设备加工参数,跟踪验证粗车刀崩刃频次,粗车刀崩刃次数明显改善,表 5 为参数优化情况。优化设备粗车加工切削速度,G97S1100(1100 r/min)调 整 为 G96 S180(180 mm/min),G96 为恒线速度加工,加工过程中自动调整主轴转速保证切削线速度不变(多用于外圆直径加工)。G97 为恒转速加工,加工过程中主轴转速一致(多用于端面加工),G97 随着工件轴径直径变小,切削线速度会变低,考虑粗车加工过程将曲轴轴径由 φ54 mm 加 工 至φ50.2 mm,切 削 线 速度 将 由 186.5 mm/min 降 低 为 172.3 mm/min,下刀位置切削线速度过大,且与毛坯面(氧化层)接触,加工应力大,易崩刃。参考刀具耐用表要求(线切削速度 Vc ≤ 185 mm/min),采用恒线速加工方式 G96 S180。
表 5 设备加工参数优化
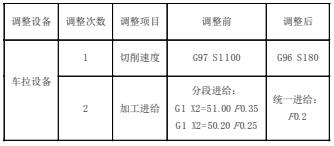
当刀具进给量增大时,刀具与工件之间的接触面积增大,导致摩擦力增大,从而引起切削力稳态分量增大,增加崩刃风险,故在满足生产节拍要求的前提下,粗车加工过程中的进给 F0.35、F0.25 降低为统一的进给 F0.20,跟踪生产崩刃频次显著降低。
结论
我司进行曲轴车拉加工工位加工过程中粗车刀崩刃频繁,比正常加工情况多 4.3 次 / 月。通过人、机、料、法及环分析,锁定设备精度、加工参数及加工余量,并对其进行优化验证。最终通过调整刀片余量分配、机床加工参数及调整设备精度将曲轴线 OP20 车拉工位粗车刀崩刃频次降低为 1 次 / 月以内。为预防问题再发生,优化维修 PM,定期检查、调整设备精度及原点位置,更新 PCP,要求定期监控OP20 粗车余量并写入经验教训。
投稿箱:
如果您有机床行业、企业相关新闻稿件发表,或进行资讯合作,欢迎联系本网编辑部, 邮箱:skjcsc@vip.sina.com
如果您有机床行业、企业相关新闻稿件发表,或进行资讯合作,欢迎联系本网编辑部, 邮箱:skjcsc@vip.sina.com