全铝风冷发动机缸套一缸体的制备技术及其传热性能研究
2018-2-5 来源:重庆工程职业技术学院机械工程学院 、教务 作者:林雪冬 何彼
摘要:采用离心铸造工艺制备了自生初SifM92Si颗粒增强A1.Si.Mg复合材料汽缸套,并与铝合金缸体进行压铸成形,形成了全铝合金缸套.缸体。应用热电偶埋设法,在自制的五点测温传热实验装置上分别检测并对比分析了风冷发动机铝合金缸套.铝合金缸体与铸铁缸套.铝合金缸体的传热性能。研究表明:相比铸铁缸套一缸体,铝合金缸套-缸体具有更佳的传热性能;通过实验测温.数据曲线拟合法,推算获得了全铝合金发动机工作时汽缸的内表面温度为231℃,比铸铁缸套内表面温度低11℃。
关键词:AI.Si—Mgg套;铝合金缸套一缸体;传热性能;热电偶
为了达到减重降排增效的目的,近年来,汽车行业已逐步采用轻合金(如铝合金)材料来制备汽车零部件,如发动机缸体、活塞均已采用铝合金材料【l-2]。将铸铁缸套镶铸在铝合金缸体中使用是目前我国绝大部分摩托车发动机、通用机械发动机和小排量汽车发动机等采用的方式。利用该种方式制备的气缸,其缸套的内表面耐磨性能优越;然而,由于铸铁缸套与铝合金缸体材质上的不同,使得这种气缸存在诸多问题,如热传导性能一般,铸铁缸套与铝合金缸体压铸成形冶金结合效果欠佳等,使气缸在使用过程中易出现变形、漏气。鉴于此,国内外纷纷开展铝合金缸套的制备技术研究[3-”],成形全铝发动机缸套一缸体,以解决此类I司题。
作者在前期的研究工作中采用离心铸造工艺制备了自生初晶Si/M92Si颗粒增强Al—Si—Mg合金铸件,获得了硬质颗粒增强铸件内壁的铝合金缸套,具有较好的摩擦学性能和综合力学性能【协阍,为实现成形全铝发动机缸套.缸体奠定了较好的基础。本研究就全铝发动机缸套.缸体的制备技术进行了详细报道,并在这一研究基础上,应用热电偶埋设法,在自制的五点测温传热实验装置上,分别对风冷铝合金缸套一铝合金缸体与铸铁缸套一铝合金缸体的传热性能进行检测并对比分析。通过实验测温.数据曲线拟合法推算全铝合金发动机工作时汽缸的内表面温度,验证铝合金缸套缸体在传热方面的优越性,为实现全铝发动机缸套缸体的推广应用提供实验数据。
1 、实验方法
1.1 缸套尺寸与模具设计尺寸
如图1a所示,149cc发动机缸套内径为62 mm,外径75 IIllll,高度110.5 mm;在考虑了毛坯车削加工余量后,设计本实验离心模具内径为76 mm,高度130 mnl,如图1b所示。
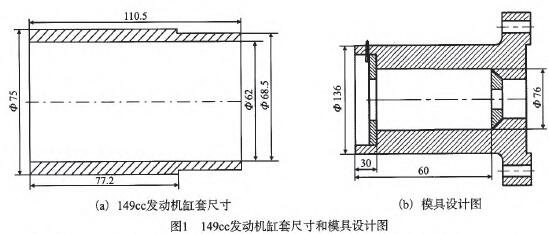
1.2 材料准备与铸件制备
实验以工业纯Al、纯si、纯Mg及A1—18Si一1.2Mg合金为原料,在井式电阻炉中加热熔炼配制A1.22Si一7Mg合金浆料,采用P—Cu变质剂进行变质处理。浇注工艺为:浇注温度720~760℃,模具温度150~200℃,离心转速R=4 200 r/min。离心铸造获得高度129 mm,外圆直径76 mill,厚度10~1 1 mm的筒状零件,如图2所示。

1.3 铝合金缸套一缸体压铸
149CC发动机缸套将使用在风冷发动机上,一般采用高压压铸,以形成薄而密集的散热片。压铸采用3 000 kN高压铸造机,压铸铝合金材料为ZLl 13Y。高压压铸时,只需对缸套进行简单预热或不预热。压铸时,使用压铸模具的芯棒对缸套进行定位。
1.4 缸套一铝合金缸体组合体的传热性能测试一
图2离心铸造Al—Si—Mg缸套毛坯Fig.2 The AI-Si—Mg liner castings fabricated by centrifugal casting1.3铝合金缸套一缸体压铸149CC发动机缸套将使用在风冷发动机上,一般采用高压压铸,以形成薄而密集的散热片。压铸采用3 000 kN高压铸造机,压铸铝合金材料为ZLl 13Y。高压压铸时,只需对缸套进行简单预热或不预热。压铸时,使用压铸模具的芯棒对缸套进行定位。本实验设计了一种传热实验装置,对比检测了铝缸套.铝缸体组合体与铸铁缸套.铝缸体组合体的传热性能,如图3所示。整套装置由热源、上下圆形隔热铁块、缸套.缸体、热电偶一测温仪组成。
其中,图3a所示为热源,由陶瓷棒与缠绕其上的电阻丝组成,电阻丝与外部交流电源接通,对缸套.缸体进行加热,电阻丝功率为1.5 kW,陶瓷棒直径略小于缸套内径。上下圆形铁块用于隔绝热量散失,同时也对整套实验装置起到固定支撑作用。沿缸体径向方向,在其中部位置由外向内钻有不同深度的测温盲孔,直径为1.6 Ilq/lq,用于埋设端头经打磨后的铠装NiCr-NiSi热电偶(K型,多1.6 mnl,精度:±1℃),测试缸体径向方向上不同位置的温度,如图3b所示。实验时,热源被套在缸孔内部,热电偶插在测温孑L内并以高温绝缘密封胶密封,热电偶另一端联接由重庆川仪十八厂生产的数字温度显示仪(型号:XMZ.H8—01一000A,精度:±1℃),读取同一时刻缸体不同位置的温度。
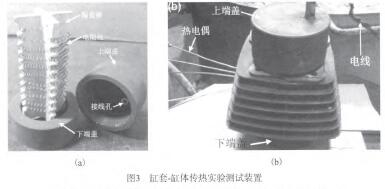
2、结果与讨论
2.1 铝合金缸套加工
本实验中,铝合金缸套铸件中的微观组织主要有灰色颗粒状初晶Si相、黑色颗粒状初晶M92Si相、共晶si、共晶MgESil)2及基体仅相。其中,在铸件内层的初晶颗粒增强区域,初晶Si、M92Si颗粒的体积分数可达30%t旧。
对经过热处理后的铸件进行一系列机械加工,为铝合金缸套.铝合金缸体的压铸做准备。铸件的机加工主要包括铸件外表面粗车、内表面粗车/半精车、外表面螺旋槽车削、端部车削以及倒角等。根据前期研究成果【151,在经过了工艺优化后,铸件的端部车削量控制在6 mm以内。本实验中,首先应对铸件的两端进行车削,去除端部夹渣,保证剩余部分铸件的质量。在后续的压铸过程中,为了使零件的外表面与缸体在高压或低压作用下实现良好的冶金结合,缸套应具有粗糙的外表面,因此,在对铸件外表面进行车削时,应保持较大的进刀量,并适当降低机床的主轴转速,尽可能使零件的外表面形成大量的毛刺。并且,为了进一步增强铝合金缸套.缸体的冶金结合能力,本实验在缸套零件的外表面车削有一系列的螺旋槽,如图4所示,设计槽深1~2 mm,槽距3~5 mm。
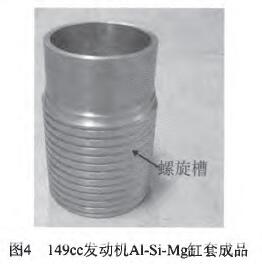
2.2 缸套一缸体压铸成形
缸套压铸时,需要定位在压铸模具的芯棒上,既要保证压铸过程中缸套内孔不“跑水”,又要保证铸件压铸成形后能够顺利取出,因此,铸件的内表面在加工时具有一定的精度要求。不同缸套产品的压铸内孔尺寸的精度要求不一样。工厂中,铸铁缸套.缸体的压铸设备同样适用于铝合金缸套.缸体的压铸,只是在工艺方面有所变化。缸套在压铸前可进行简单预热处理以保证在压铸时缸体缸套之间的冶金结合度。由于铝合金的熔点比铸铁低,其预热温度相对较低,一般以不超过300℃为宜。在预热时,由于材质的不同,铝合金缸套与铸铁缸套的膨胀量显然不同。A1.Si.Mg合金的线膨胀系数为20.48x106/"C(20~300℃),而铸铁的线膨胀系数一般为(8.5~l 1.6)xlO-6/℃(20~300℃),二者相差较大,铝缸套受热更易膨胀。因此,在车削铝合金缸套内孔时,其尺寸偏差范围一般取公差下偏差,使得铝合金缸套的内孑L尺寸在总体上相比于铸铁偏小。如图5所示为铝合金缸套压铸成形件,图6所示为两种缸套压铸成形件经机械加工后的成品,图7是将铝合金缸套一缸体成形件沿缸套轴向方向由中间位置剖开后打磨、抛光后的形貌图。由图7中可以看到,经压铸后,铝合金缸套与铝合金缸体间的结合效果良好,这为全铝合金缸套一缸体呈现优越的传热性能奠定了基础。
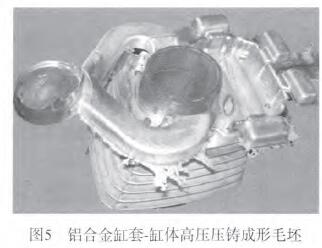
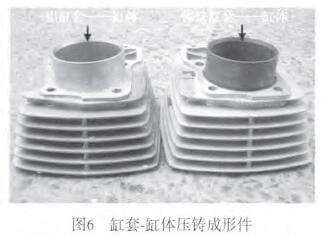
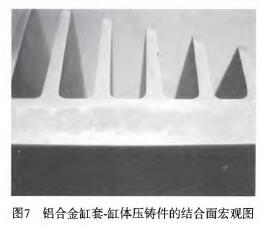
2.3 缸套一缸体组合体的传热性能
与铸铁缸套相比,铝合金缸套尤其在传热性能方面具有明显的优势:铝合金缸套材料的热导率为A铝=70w/(m·K),铸铁缸套的导热系数为A铁=55 W/(m·K),压铸铝合金的热导率为A=177 W/(m·K)t181,即:铝缸套与压铸铝合金缸体的热导率基本相等,是铸铁缸套热导率的3倍。较高的热导率有利于缸体的整体散热,特别是风冷系列发动机,将极大地改善热机的工况。关于模拟铸铁缸套一缸体工况并测算缸体内壁温度的研究已有不少,然而,对于镶铸有铝合金缸套的全铝发动机汽缸体在这方面的报道尚未见到。为了获得风冷发动机铝合金缸套的传热性能指标,在实验室进行了风冷发动机的工况模拟实验,并与铸铁缸套进行了对比。按1.4节所述方法,分别对铝合金缸套.铝合金缸体,铸铁缸套.铝合金缸体组合体进行了发动机工况模拟、并分别测量缸体不同位置的温度,从而对比两种缸套的传热性能。实验时,通过套在缸体缸孔内部的电阻丝加热来模拟发动机工作产生的热量,通过缸体正前方的电风扇转动来模拟空气对流对缸体的散热作用。铸铁缸套一缸体发动机在正常工作一段时间后,其外表面温度将达到相对平衡状态。此时,缸体外表面上部(缸体大端面)温度达180--一200℃,缸体外表面下部(缸体小端面)温度达140 150℃(企业数据)。根据这一平衡温度区间,本实验制定了模拟发动机燃烧室工况的热源加热工艺,即1.5 kW电阻丝每加热14 s,断开电源5 S,依次反复进行,使埋设于铸铁缸套发动机缸体外表面的热电偶A的温度处于平衡温度区间内,两种缸套发动机均采用相同的加热频率进行测试。经测量,在缸套.缸体中部,组合体的最大壁厚约12 nllYl。依此,热电偶偶头埋设在距离缸体外表面不同的深度,如图8所示,埋设点A、B、C、D、E分别距缸体外表面的距离为2.0 rain、3.5 mm、5.0 rtlln、6.5 mrfl、8.0 nllTl。测试时,在不同时刻,同时记下所有点的温度读数。
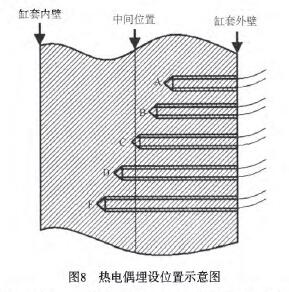
在同样的加热条件下分别测试两种缸套一缸体上不同位置的温度,记录并绘制如图9所示的温度一时间曲线图。可以看到,随着加热时间的延长,两缸套一缸体不同位置的温度均呈现逐渐上升的趋势。并且,经过长达1 415 s的吸热、传热的循环过程后,缸套.缸体的温度处于一种相对平衡状态。从图9a可以看到,处于平衡状态的铸铁缸套一缸体的E点(最深测温位置)的最后温度达223℃,而同样位置的铝合金缸套.缸体的最后温度为206℃,如图9b所示,其温差达到17℃。而在距离缸体外表面最近的测试点A点,其温差更是达到了20℃。显然,在同等工况下,铝合金缸套.缸体具有更低的温度,其传热性能更佳。
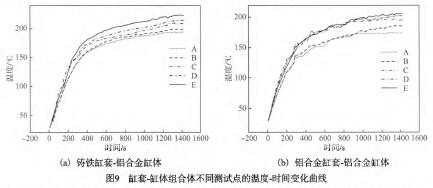
图10所示是两缸套.缸体温度达到平衡态后,不同为:测试点的温度值。可以看到,无论是铸铁缸套一缸体,还是铝合金缸套二缸体,其不同位置的温度值近似呈现线性变化规律。
分别对两缸套一缸体温度变化曲线进行拟合,则得铸铁缸套.缸体不同位置的温度变化曲线方程为:Y=4.866 7戈+1 83.47 (1)铝合金缸套一缸体不同位置的温度变化曲线方程Y=5.4x+1 66 (2)根据这一拟合曲线方程,可以近似预测发动机在正常工作后,缸套.缸体温度达平衡态后,缸套内壁的平均温度。据式(1),则得铸铁缸套内表面的平衡温
度为242℃;据式(2),则得铝合金缸套内表面的平衡温度为231℃。可见,铝合金缸套的内表面温度更低,这有益于减轻汽缸内部的燃烧积炭现象。并且,这也是首次在实验的基础上,预测获得的全铝合金发动机工作时汽缸的内表面温度,对于进一步研究全铝
发动机的工况具有参考价值。
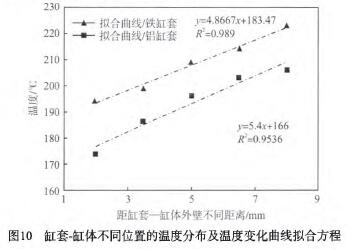
3、结论
(1)通过离心铸造法成功制备了自生初晶Si/M92Si颗粒增强A1.Si.Mg复合材料汽缸套,并经高压压铸机与铝合金缸体进行了压铸成形,得到全铝风冷发动机缸体。且铝合金缸套与铝合金缸体间的结合效果良好,为全铝合金缸套.缸体呈现优越的传热性能奠定了基础。
(2)应用热电偶埋设法,在自制的五点测温传热实验装置上分别检测并对比分析了风冷铝合金缸套一铝合金缸体与铸铁缸套.铝合金缸体的传热性能。研究表明:相比铸铁缸套.缸体,铝合金缸套.缸体具有更佳的传热性能
(3)通过实验测温一数据曲线拟合法获得了全铝合金发动机工作时汽缸的内表面温度为231℃,比铸铁缸套内表面温度低11℃。对于进一步研究全铝发动机的工况具有参考价值。
投稿箱:
如果您有机床行业、企业相关新闻稿件发表,或进行资讯合作,欢迎联系本网编辑部, 邮箱:skjcsc@vip.sina.com
如果您有机床行业、企业相关新闻稿件发表,或进行资讯合作,欢迎联系本网编辑部, 邮箱:skjcsc@vip.sina.com
更多相关信息