滚珠丝杠副寿命试验台测控系统设计
2017-7-13 来源:南京理工大学 机械工程学院 作者:薛 锋 杨 雪 常永寿 韩 军
摘要: 针对滚珠丝杠副寿命试验的要求,设计了滚珠丝杠副寿命试验台的测控系统。首先介绍了滚珠丝杠副寿命试验台的组成结构,然后根据试验台所需实现的功能进行分析,主要介绍了试验台的加载控制系统、驱动系统、数据采集系统的设计,并给出了测控系统的硬件结构图以及软件设计流程图。该测控系统的设计为滚珠丝杠副寿命试验提供了软硬件基础。
关键词: 滚珠丝杠副; 寿命; 测控系统; 硬件设计; 软件设计
引言
滚珠丝杠副具有传动精度高、传动效率高、同步性能好、使用寿命长、传动可逆性等优良特性,被广泛用作中小型数控机床的进给传动系统,其寿命指标对数控机床的性能有很大影响[1]。我国在中高端机床产品方面与国际先进水平有较大差距,主要体现寿命、额定动载荷等指标,限制了国产产品在中高档数控机床中的推广应用。因而希望开发一种测试滚珠丝杠副寿命的试验装置,为被测样件提供寿命参数,并为研究如何延长滚珠丝杠副使用时间,提高机床寿命提供试验平台[2]。
目前,国内滚珠丝杠副的试验装置大多针对滚珠丝杠副的综合性能,大多数试验台都不具备加载能力[3],无法模拟寿命试验所需的实际加载情况,缺乏模拟各种实际工况的能力,不能测评在不同加载情况下滚珠丝杠副的寿命。
针对这种现状,设计研发滚珠丝杠副寿命试验台十分重要。根据试验要求设计的滚珠丝杠副寿命试验台测控系统可以对滚珠丝杠副进行模拟实际工况的跑合与加载,加载力可调且调节范围较大,传感器通过数据采集卡将测得的信号传送到工控机中,数据处理软件处理分析数据,用以确定结构设计、加工方法和材料特性对寿命的影响,修正我国滚珠丝杠副寿命公式,同时研究提高寿命的途径[4],为研究如何提高国产滚珠丝杠副的性能提供依据。
1、 测控系统设计分析
1.1 试验台的结构设计
滚珠丝杠副寿命试验台由机械结构和测控系统两部分组成组成。以机械结构为硬件基础,利用测控系统进行试验台的运动控制、加载与数据的采集。试验台的结构框图如图 1 所示。
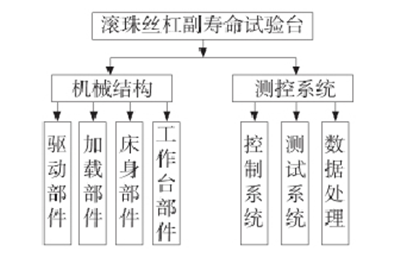
图 1 试验得结构框图
试验台的机械结构如图 2 所示,有以下四个部件:驱动部件、加载部件、床身部件和工作台部件。驱动部件和加载部件分别位于床身部件的头尾两侧,驱动部件带动中间的被测滚珠丝杠副运动,加载部件对两侧的加载滚珠丝杠副进行加载,工作台部件在床身部件上,可以在伺服电机的驱动下在床身部件上做往复运动,对被测滚珠丝杠副进行跑合。
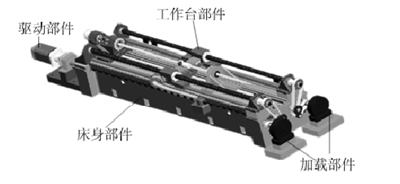
图 2 滚珠丝杠副寿命试验台机械结构
机械结构的运动由测控系统控制,滚珠丝杠副寿命试验台测控系统由加载力控制系统、驱动电机控制系统及数据采集系统组成。驱动电机控制系统控制驱动部件带动工作台部件在床身上往复运动; 加载力控制系统控制加载部件对加载丝杠进行加载,加载力作用在被测丝杠上形成轴向载荷,加载力大小可调,模拟滚珠丝杠副工况下的加载情况; 数据采集系统对相关试验参数进行采集、分析和处理。
1. 2 加载力控制系统
1. 2. 1 试验的加载力分析
我国目前的寿命试验台存在加载方式单一,加载力不可调,不能提供高加载等问题[5]。为了模拟实际工况,寿命试验的加载力的范围应能保证是滚珠丝杠副额定动载荷的 20% 左右[6]。经过分析,设计外力加载方案,加载力可以调节且范围大,可以很好的模拟实际加载情况。
外力加载原理如图 3 所示: 伺服电机输出扭矩 M3,转化力 F5传递给工作台,两根加载丝杠对称布置于被测丝杠两侧,加载丝杠副轴端分别与电涡流制动器连接,分别控制两侧电涡流制动器的电流使输出扭矩 R3相等,电涡流制动器输出扭矩 R3等效转化力 F6,二者之和作为试验加载力。受力分析得出: 被测头架受力为 F5,工作台受力为 0,被测尾架受力为 F5,加载头架与加载尾架受力均为 F6,工作台受到扭转力矩为 0[7]。
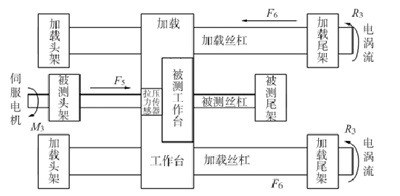
图 3 外力加载原理图
负载选用电涡流制动器,利用涡流损耗原理来吸收功率,提供加载,其输出转矩与激励电流具有优良的线性关系,加载力平稳,大小可调,同时配套了制冷机对电涡流制动器进行水冷。
1. 2. 2 加载力控制系统设计
试验台进行寿命试验时,需要对被测丝杠进行加载,模拟实际工作情况,并且系统能够实现对加载力的控制。电涡流控制器型号为 WLK-5A,控制器控制信号电流 0 ~ 5A,通过改变电流大小可以改变阻力大小。操作时,输入工控机试验预计所需的加载力对应的控制器控制信号电流值,PCI-1716 输出卡给电涡流控制器相应的电流信号,控制电涡流制动器输出预置的加载力,力传感器实时监测被测丝杠所受的加载力并反馈给工控机,提示操作人员输入的电流的值是否对应合适的加载力。
1. 3 伺服控制系统
1. 3. 1 伺服控制控制的分析
滚珠丝杠副寿命试验台的运动控制通过调节驱动电机的转向与转速,来控制工作台的运行速度和换向动作。驱动电机选用伺服电机,与编码器组合交流调速,改变信号电压即可精确改变输出转速和扭矩,同时具有快速响应,机电时间常数小、线性度较高等特点。
电机控制卡控制电机转速,控制卡通过接收相应的脉冲信号控制电机的启动和停止,根据输入的脉冲量控制电机的转速,从而控制工作台部件的移动速度。同时对工作台部件的位置进行控制,在床身一侧布置两个非接触式光电开关控制正反向和两个接触式限位开关控制极限位置,给出换向信号以及极限位置的急停保护。
1. 3. 2 伺服控制系统设计
选用固高控制卡控制伺服电机,输出两路脉冲信号,一路控制伺服电机的启停,另一路控制伺服电机正反转。光电开光安装在工作台的运动起点,作为原点信号 HOME,当工作台不在原点但需要回原点时,光电开关给固高控制卡发出信号,使伺服电机带动工作台运动回到原点。两个限位开关安装在工作台可运动的最大范围的起点和终点,直接与固高控制卡连接,作为运动位置的正极限和反极限。一旦试验台接触或是人工触碰到任意限位开关,试验台都会当即停止,防止工作台失控,造成事故[8]。
1. 4 数据采集系统
1. 4. 1 数据采集分析
寿命试验时,试验台受加载力进行往复运动,被测丝杠的动态扭矩、行程误差、振动、噪声等参数是体现滚珠丝杠副寿命的表征。通过监测动态扭矩、行程误差、振动信号、噪声等参数相对时间的变化曲线,分析被测丝杠的磨损疲劳状况,从而判断被测丝杠是否到使用寿命。同时,拉压力传感器实时监测被测丝杠的加载力,确保被测丝杠的负载与预设的相同。
1. 4. 2 数据采集系统设计
测控系统能够接发信号,进行运动、加载信号的传送和测试信号的采集,需要一个上位机与各个模块之间实现通讯[9]。图 4 所示为滚珠丝杠副寿命试验台测控系统的硬件结构图,硬件结构的搭建包括上位机、控块三部分。
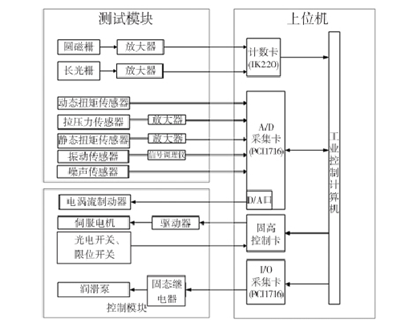
图 4 测控系统硬件结构图
上位机包括工业控制计算机、计数卡 IK220、研华数据采集卡 PCI1716 以及固高运动控制卡等。
控制模块中,工业控制计算机通过固高控制卡控制伺服电机实现工作台的往复运动。拉压力传感器监测被测滚珠丝杠副所受到的轴向载荷,使电涡流制动器提供合适的负载。工业控制计算机通过给 PCI1716 采集卡发信号,控制固态继电器使润滑泵完成试验的润滑。
测试模块中,振动传感器、扭矩传感器以及噪声传感器采集到的信号通过 PCI1716 的模拟量输入口采集到工控机中; 圆磁栅和长光栅的编码器与 IK220 计数器配套使用,将试验采集到的编码器信号和计数器信号传入工控机,直线行程误差的计算函数输出曲线采集到电压电流信息传入工控机,以直线行程误差的计算函数输出曲线,分析出行程误差; 根据采集到的扭矩、加载力、振动、噪声和行程误差等信号,分析被测丝杠的寿命。
2、 测控系统软件设计
为使用户界面直观、友好,测控系统软件用 VisualBasic 作为开发工具,软件主要用于实现控制、测试和数据分析三个功能。控制软件主要用于控制伺服电机、润滑泵和电涡流制动器; 测试软件主要是监测被测丝杠的加载力、动态扭矩、行程误差、噪声和振动等性能指标; 数据分析软件完成对测试软件采集到的数据的存档、分析和处理。
2. 1 系统主程序流程图
测控系统主程序流程图如图 5 所示,试验前,打开试验软件,输入试验环境参数以及被测滚珠丝杠副的参数; 接着把被测丝杠通过工装安装在试验台上,开启润滑系统进行润滑,做好试验准备工作; 接下来,根据所需的加载力输入电涡流制动器的控制电流值对被测丝杠进行加载,来模拟丝杠实际工况; 然后对传感器上电,开始监测性能指标参数; 启动电机控制系统,使伺服电机驱动被测丝杠进行跑合。在测试软件里,可以对扭矩、振动、噪声和行程误差等信号进行采集,经过滤波处理和软件分析后显示在程序界面上,通过观察各项性能指标参数相对时间变化的情况来分析丝杠寿命。当参数数值有异常时,检测被测丝杠是否出现点蚀,如果出现点蚀并且被测丝杠的试验行程没有达到额定值,说明此产品寿命指标不达标,为不合格品,数据分析软件记录下此不合格丝杠的信息; 若被测丝杠没有出现点蚀并且试验行程达到额定值,则说明被测丝杠的寿命合格,数据分析软件记录下此合格丝杠的信息。以上述的流程进行滚珠丝杠副寿命试验。
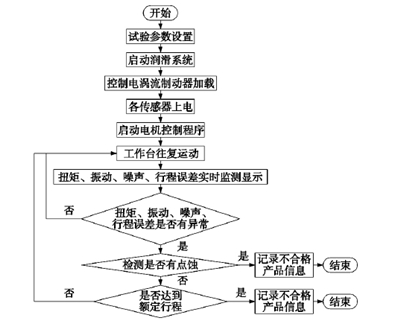
图 5 测控系统主程序流程图
2. 2 试验台程序主界面
程序的主界面如图 6 所示,界面上包括参数设置、
运行与加载、行程误差、扭矩测试、数据采集卡测试、综合查询、用户管理、试验台调试等功能。
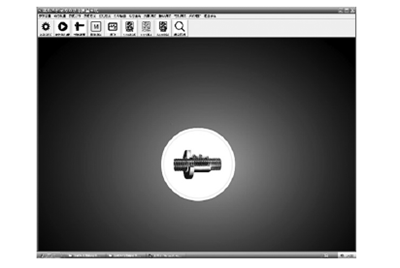
图 6 程序主界面
2. 3 参数设置界面
参数设置程序界面如图 7 所示,用户可以在这个界面输入被测丝杠型号和尺寸等基本参数以及精度等级等参数,并且可以输入试验环境参数。
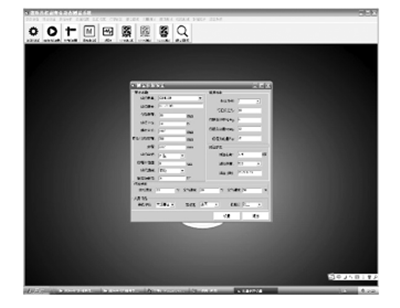
图 7 参数设置界面
2. 4 加载力及扭矩界面
加载力及扭矩界面如图 8 所示,改变加载设定中的加载电流大小可以控制加载力大小,加载力由拉压力传感器实时测定,输入输出扭矩由扭矩传感器实时测定。
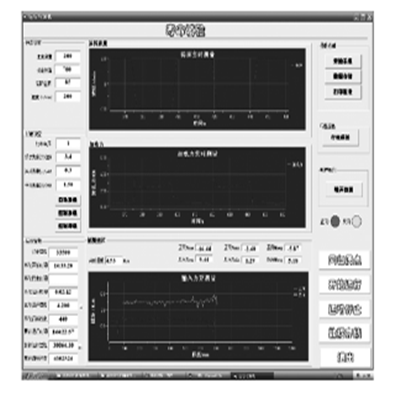
图 8 加载力及扭矩界面
2. 5 行程误差检测界面
行程误差检测界面如图 9 所示,点击开始采集,会弹出行程误差测量界面实时检测正向和反向的行程误差并分析数据。
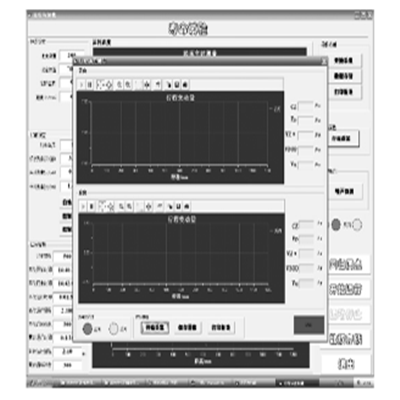
图 9 行程误差检查界面
2. 6 振动检测界面
如图 10 所示,可以实时观测试验台运动过程中的振动参数的变化,对振动信号进行分析,判断被测丝杠是否发生点蚀和故障。
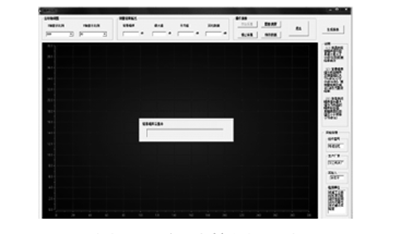
图 10 振动检测界面
2. 7 噪声检测界面
如图 11 所示,可以采集被测丝杠试验过程中的噪声情况。采集时背景噪声和试验噪分开测量,通过数据处理软件排除背景噪声对试验噪声的干扰。
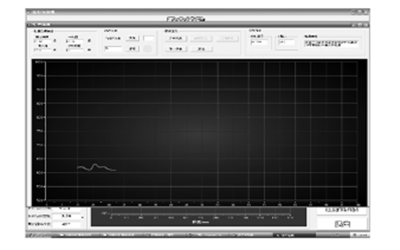
图 11 噪声检测界面
2. 8 数据处理软件
本测控系统的数据处理软件以Access 数据库为基础设计了滚珠丝杠副寿命信息数据库以及数据库管理软件[10],用来保存滚珠丝杠副基本参数、试验设置参数、寿命试验结果原始数据,分析结果,能很好的帮助试验人员完成试验。
3 、试验台设计成果
如图 12 所示,为滚珠丝杠副可靠性试验台,滚珠丝杠副寿命试验台机械结构已经设计搭建完成,并根据试验要求对测控系统进行设计和调试; 试验台已经可以模拟滚珠丝杠副的工况进行跑合与加载,电涡流加载系统可以为被测丝杠提供 0 ~ 20000N 的负载; 扭矩传感器、拉压力传感器、振动传感器、噪声传感器和长光栅、圆光栅等的信号正常,可以被数据采集系统采集并显示; 数据库保存寿命试验的数据并且可以被数据分析软件调用处理。
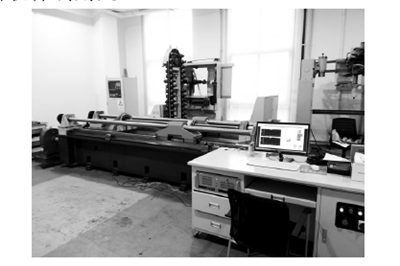
图 12 滚珠丝杠副寿命试验台实物图
4 、结束语
本文针对滚珠丝杠副寿命试验台所需达到的性能指标,分析和研究了其测控系统。结合滚珠丝杠副寿命试验装置,提出了试验台测控系统的设计方案,用以实现模拟被测丝杠在工况下的跑和、丝杠的加载以及性能指标的的检测。本文提出的滚珠丝杠副寿命试验台测控系统的设计方案,能够达到滚珠丝杠副寿命试验的软硬件要求,有助于国内厂家开展滚珠丝杠副寿命研究,为研究如何提高滚珠丝杠副寿命提供了试验基础。
投稿箱:
如果您有机床行业、企业相关新闻稿件发表,或进行资讯合作,欢迎联系本网编辑部, 邮箱:skjcsc@vip.sina.com
如果您有机床行业、企业相关新闻稿件发表,或进行资讯合作,欢迎联系本网编辑部, 邮箱:skjcsc@vip.sina.com
更多相关信息