高频破碎器主轴应力分析及结构优化
2020-4-3 来源: 贵州大学 机械工程学院 作者:王新旺,蔡家斌,肖齐洪
摘要: 主轴作为高频破碎器的关键部件对于力的传递以及使用寿命具有重要的影响。为了使高频破碎器的主轴部件具有强度高、变形小、寿命长等特点,首先根据某厂现有的 60 型高频破碎器的实际工况,计算出主轴受力的大小; 其次根据高频破碎器的主轴结构特征,应用 ANSYS Workbench 有限元分析软件对其进行静力分析,通过静态应力分析、疲劳寿命分析发现主轴存在断裂失效的可能; 最后结合 Response Surface 模块,通过改变轴肩处倒角的大小以及增加卸载槽对主轴进行结构优化。结果表明,主轴轴肩处应力降低了 57% ,疲劳寿命提高了 183. 9% ,对于提高高频破碎器的使用寿命具有一定的实际意义。
关键词: 高频破碎器; 主轴; 应力; 结构优化
0 引言
高频破碎器是将挖掘机的液压能转化为机械能从而进行高频破碎的设备,它因为有着较高的打击频率和较低的噪音在矿山开采、道路建设等国民经济建设中受到广泛应用[1]。由于其工况非常复杂,加上高频振动的特性,所以高频破碎器关键部件的强度设计和可靠性设计就变得非常重要。在高频破碎器的设计过程中,主轴作为其关键部件,其弯曲特性直接影响到齿
轮的啮合能力,其强度特性直接影响到高频破碎器的使用寿命,主轴力矩传递处应力过大,会存在一定的安全隐患[2]。
某厂生产的 60 型高频破碎器,在使用了一段时间后,主轴轴肩部分出现了断裂现象,因此分析其断裂失效的原因,彻底解决主轴断裂失效的问题,对于克服现有主轴设计的不足,提高高频破碎器的使用寿命和和厂家的经济效益具有重要的意义。本文首先利用 AN-SYS Workbench 静态结构模块,分析主轴在受力情况下的强度、刚度、疲劳特性以及扰度,检验主轴设计是否合理,然后利用其优化设计模块,改变主轴的相关设计参数,找出目前高频破碎器主轴方面的缺陷加以改进,提出一种新的解决办法,从而提高其使用寿命,使其符合高频破碎器的使用条件。
1、 高频破碎器及其主轴结构
高频破碎器的基本组成部分由壳体、振动箱体( 包括齿轮、偏心块) 、上拉支架、下拉支架、斗齿、空气弹簧等组成[3],如图 1a 所示,其工作原理是由振动箱里面的一对斜齿轮相互啮合,使连接在一起的偏心块产生转动,从而产生交变的偏心力,偏心力由轴传递给振动箱体,最终传递到斗齿,使斗齿产生打击岩石的破碎力。主轴通过键槽与齿轮偏心块相连,如图 1b 所示,其理论转速在 1200r/min 左右,主轴两端通过两个调心滚子轴承安装在振动箱的轴承座上,调心滚子轴承具有高的径向承载能力,而且还能承受一定的轴向载荷,特别适用于高频破碎器这种重载和高频振动的工况,除此还具有调心功能,能补偿一定的加工误差,并且能够承受主轴受力后轻微的变形。
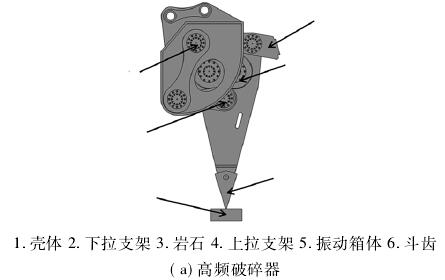
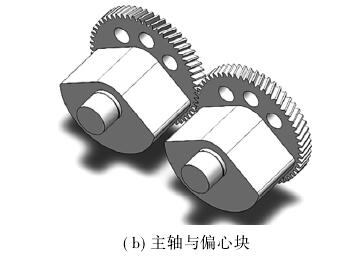
图 1 高频破碎器与主轴
2 、主轴静态特性分析
2.1 静力分析
静力分析是用来确定主轴在各种力的综合作用下的变形情况以及应力集中情况,主要包括刚度计算与变形量计算。60 型高频破碎器的主轴采用的材料为42CrMo 超高强度钢,经过调制处理,具有较高的疲劳极限和多次抗冲击能力,适用于大冲击高频振动的工况。材料具体属性如表 1 所示。
表 1 材料属性
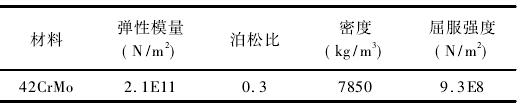
2.1.1 模型建立与网格划分
建立正确的有限元模型能够提高有限元仿真的精度,因此为了真实模拟主轴各处的受力分布情况,建模时不能忽略主轴中容易产生应力集中的倒角,凹槽等,如轴肩处的倒圆角、轴中间的键槽。但为了简化有限元模型,提高收敛能力,忽略主轴两端的倒角、螺纹孔等小特征[4]。利用 ANSYS Workbench 自带的 Design-Modeler 模块建立主轴的三维模型,然后对模型进行网格划分。
网格划分质量的好坏对计算结果的准确性是至关重要的,若网格质量好,可以将误差降低到最小[5]。由于模型的复杂性,为了避免网格划分失败,因此采用适应性好的四面体网格划分法( Tetrahedrons) ,网格尺寸设置为全局 4mm,将跨度中心角设置为 Fine。划分结果如 图 2 所 示,模 型 节 点 数 为 517210,单 元 数 为369835。模型的单元质量为 0. 957( 1 最好) ,雅克比为1. 345( 1 最好) ,倾斜度为 0. 132( 0 最好) ,说明网格划分质量很好。
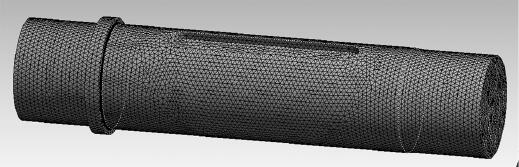
图 2 网格划分
2.1.2 设置边界条件与施加载荷
对于模型的边界约束以及载荷的施加应该按照实际情况来确定,高频破碎器的主轴分别由两个调心滚子轴承支撑,且由轴承端盖限制轴承的轴向位移,因此在主轴两端轴承支撑的地方添加圆柱约束( CylindricalSupport) ,用来提供轴向和径向支撑[6]。高频破碎器的工况非常复杂,其主轴受到多个大小与方向均不同的力,综合起来主要受到四种力: 斜齿轮啮合产生的径向力与轴向力,偏心块的偏心力、偏心块和齿轮的重力以及打击岩石时所受到的冲击力。由分析可知,当偏心力与冲击力在竖直方向重合时,主轴所受的力最大,也最容易产生失效,此时,对主轴进行受力分析有:
( 1) 竖直方向的合力由重力、偏心力、冲击力组成:
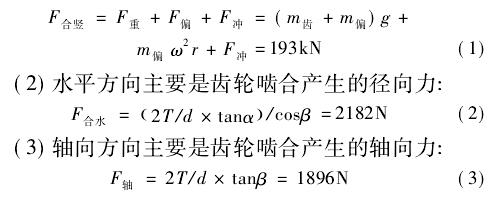
其中,T 为马达最大转矩; d 为齿轮分度圆; α 为齿形角; β 为螺旋角; ω 为旋转速度; r 为偏心距。从上述公式结果可以看出,齿轮啮合产生的径向力与轴向力相对于竖直方向的合力来说可以忽略不计,因此在给从动轴施加载荷时忽略啮合力。结合实际情况,给主轴施加远程力( Remote Force) ,将力的作用点施加在偏心块的质心。
2.1 3 结果分析
主轴的有限元分析云图如图 3 所示,从图 3a 可以看出,主轴的应力集中主要发生在轴承支撑圆柱面与轴肩的交接处,大小为299. 57MPa,安全系数为0. 83454,如图 3c 所示。虽然 42CrMo 合金结构钢材料的屈服强度为 930MPa,大于所产生的应力,但由于安全系数小于 1,仍然存在断裂失效的可能,这与实际中厂家的部分高频破碎器轴肩处断裂失效的情况是相符合的。而键槽处的应力值很小,说明主轴的键槽设计是合格的; 从图 3b 可以看出,应力集中出的最大等效应变为 1. 5 μm,变形量较大,说明主轴结构在应力集中处存在着断裂的危险性; 图 3d 为主轴在受力后的扰度曲线,由图可以看出,主轴的最大变形量为0. 0312mm,结合主轴的长度,算得主轴的扰度为: θ =arctan(x/y )= 0. 0075° ,远远小于调心滚子轴承所允许的1 ~ 2. 5° 的范围,所以主轴的刚度设计是足够的,优化设计时不需要改变主轴的横截面积,只需要解决主轴轴肩处应力集中问题。

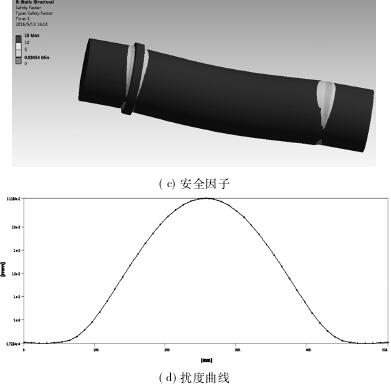
图 3 静力分析结果
2 .2 疲劳分析
由于主轴旋转,偏心块产生了大小为 F =mω2esinωt 的偏心力,式中 m 为偏心块的质量,e 为偏心块偏心距,ω 为马达旋转角速度,ω =2πn/60。虽然前文分析到主轴所受的最大应力小于材料的屈服极限,但主轴在偏心力的作用下,工作一段时间后会产生裂纹或突然发生完全断裂,这种现象称为金属疲劳,所以需要对主轴进行疲劳寿命分析[4]。载荷与疲劳失效的关系,采用的是应力-寿命曲线,根据合金刚材料42CrMo 的强度极限和弹性模量,可以通过 Fe-Safe 软件按 Seeger 近似方法得到 S-N 曲线[7],如图 4 所示。
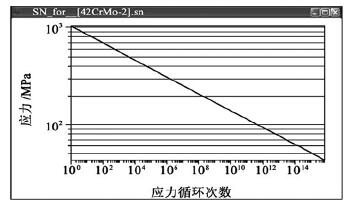
图 4 S-N 疲劳寿命曲线
在 ANSYS Workbench 的 Solution 模型树中,添加Fatigue Tool 疲劳工具,在疲劳工具下插入 Life 和 Safe-ty Factor 模块,得到的仿真结果如图 5 所示。
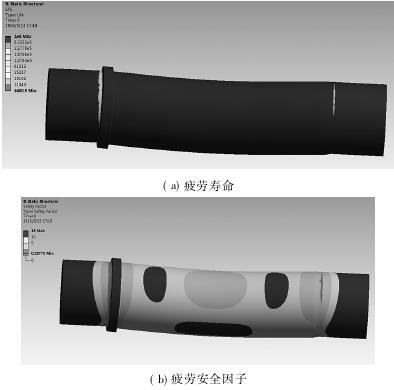
图 5 疲劳分析云图
从图 5a 可以看出主轴的最低疲劳寿命只有 7000个循环,从图 5b 中可以看出其疲劳寿命安全因子只有0. 28775,说明主轴轴肩应力集中处在交变力作用下,容易产生疲劳损害,因此消除主轴轴肩处的应力集中问题对于解决主轴断裂失效问题是非常有必要的。
3 、优化设计
应力集中主要是由于截面突变造成的,当构件有台阶、沟槽、孔等缺口时,在这些部位的近旁,由于截面的急剧变化,将产生局部的高应力,应力峰值远大于其他部位的应力值[8]。降低主轴轴肩处的应力集中主要是避免形状突变。对于主轴而言,一方面可以通过添加过渡曲线来减少应力集中; 另一方面可以添加卸载槽来增加应力集中处个数,从而减少应力的最大值[9]。过渡曲线有很多种,一般是用圆弧曲线,此外还有圆弧蜕变曲线[10],双曲率圆弧曲线[11]等都能有效地降低应力集中,本文选用圆弧过渡曲线和增加一个卸载槽来解决应力集中问题,如图6
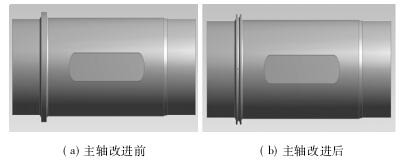
图 6 用卸载槽降低应力集中
3. 1 优化模型建立
在 ANSYS Workbench 中,可以通过 Design Explor-er 来实现产品性能的快速优化设计[12]。文章选用 De-sign Explorer 里的响应曲面( Surface Responce) 项目来进行优化设计,通过图表形式动态反应输入与输出参数之间的关系。根据主轴的结构特性,将轴肩两边的倒圆角和卸载槽的大小作为优化变量,将最大等效应力,最小安全因子以及最低疲劳寿命作为目标函数,具体取值范围如表 2 所示。
表 2 变量取值范围
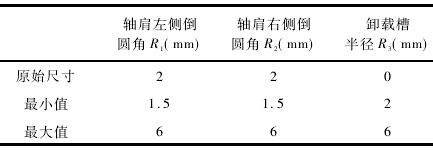
3.2 优化结果分析
3.2.1 变量点对输出参数的影响
图 7a 反映的是各设计变量与输出变量之间的局部敏感性关系,对于主轴而言,轴肩左侧倒圆角大小的变化对于等效应力、安全因子以及疲劳寿命具有决定性的影响,而轴肩右侧倒圆角以及卸载槽的大小对三个输出变量影响很小。

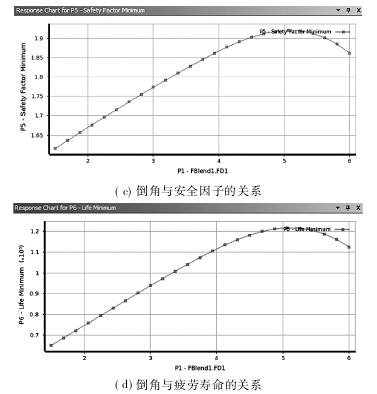
图 7 优化结果
图 7b ~ 图 7d 分别反映的是主轴轴肩左侧倒圆角的变化对三个输出变量的影响。随着左侧倒圆角的增大,主轴最大等效应力逐渐减小,最小安全因子与最低疲劳寿命也逐渐增加,但超过 5mm 左右的零界点后,主轴所受到的最小等效应力又逐渐增大,最小安全因子与最低疲劳寿命逐渐减小。因此从分析得出,对于主轴而言 5mm 的倒圆角是最优设计。
3.2.2 最佳设计点分析
对于高频破碎器的主轴而言,卸载槽对于降低应力集中并没有什么实际的影响,因此优化设计时将其舍去。为了方便加工,将主轴轴肩左右两侧的倒圆角都圆整,统一设置为 5mm,再一次通过静力分析后,得到结果后统计相关数据,得到表 3。表 3 主轴优化前后对比通过优化前后的数据对比,主轴最大等效应力有所下降,最小安全因子以及最低疲劳寿命都有所提高,最大等效应力降低了 57% ,最小安全因子提高了133. 7% ,最低疲劳寿命提高了 183. 9% 。从优化后的百分比可以看出,主轴轴肩左侧的倒圆角大小对于主轴的应力集中问题是至关重要的,倒圆角大小的微动变化就会使主轴特性有很大的不同,因此,后期对主轴进行设计时,倒圆角不但不能省去,而且还要进行应力分析,以期达到最好的效果。
4、 结论
( 1) 通过建立精确的 60 型高频破碎器主轴模型,分析其应力、应变与疲劳寿命,最终发现 60 型高频破碎器的主轴设计存在应力集中问题,其疲劳寿命过短,容易产生疲劳断裂失效,这与实际存在的问题是相符的。
( 2) 通过改变倒圆角、增加卸载槽等消除应力集中的方式对主轴进行优化设计,结果证明主轴轴肩左侧的倒圆角对于消除应力集中具有至关重要的影响。
( 3) 通过优化设计,降低了主轴最大等效应力,大幅度提高了最小安全因子、最低疲劳寿命,延长了主轴使用寿命,节约了成本。
投稿箱:
如果您有机床行业、企业相关新闻稿件发表,或进行资讯合作,欢迎联系本网编辑部, 邮箱:skjcsc@vip.sina.com
如果您有机床行业、企业相关新闻稿件发表,或进行资讯合作,欢迎联系本网编辑部, 邮箱:skjcsc@vip.sina.com
更多相关信息