车床尾座丝杆的数控车削加工工艺分析
2020-11-20 来源:盐城市经贸高级职业 盐城工业职业技术 作者:费美扣 王元生
摘要:针对传统的车床尾座丝杆加工工艺的不足,在分析丝杆零件工艺特点的基础上,探讨了应用 FANUC0i-mate系统数控车床加工丝杆的两种车削工艺方案,采用螺纹循环指令及用户宏程序编制了梯形螺纹加工程序并进行了试切。结果表明:运用左右切削法编程加工丝杆,显著提高了丝杆零件的加工质量和生产效率,提高了丝杆产品的互换性,降低了劳动强度。
关键词:车床尾座;丝杆;数控加工
0 引言
尾座是卧式车床的重要附件,主要用于安装顶尖,对长轴类零件定心和夹紧,确保加工精度和表面粗糙度;也可用于安装麻花钻或镗刀刀杆等,完成对工件孔的加工。
市场调研结果显示,现有卧式车床绝大多数使用了手动套筒式尾座,该类尾座利用丝杆螺母副传动机构调整套筒的伸缩行程,实现顶尖夹紧或刀具进。显而易见,丝杆是影响尾座精度的关键零件之一。
传统的尾座丝杆加工是在通用车床上进行,这种加工方法存在两方面缺点:一是对机床操作人员的技能要求非常高,产品生产效率较低;二是丝杆产品的尺寸一致性差,后续加工螺母时需要与丝杆进行配合加工,产品的互换性较差,维修成本高。
本文针对尾座丝杆传统生产工艺的不足,在详细分析丝杆工艺难点的基础上,探讨应用FANUC 0i-mate系统数控车床的两种加工方案,并采用螺纹循环指令及用户宏程序进行编程和试切加工,以提高丝杆的加工质量和生产效率,提高产品的互换性。
1 、丝杆工艺性分析
车床尾座丝杆如图1所示,材料为45钢,中小批量生产。
1.1 零件图分析
丝杆零 件 长 315±0.2(mm),最大外圆 Φ35 0-0.03mm。加工内容包括外圆、倒角、退刀槽、三角螺纹和梯形螺纹。3处外圆相对于两端中心孔的圆跳动度小于0.040mm 或0.025mm,2处外圆表面粗糙度为Ra1.6。丝杆上梯形螺纹 Tr20×4-7h-L 是常用的传动螺纹,公称直径为20 mm,螺距为4 mm,中径公差带代号为7h,长旋合长度。
梯形螺纹的大径相对于两端中心孔的圆跳动度小于 0.025 mm,螺牙顶面及两侧面表面粗糙度为Ra1.6。
1.2 加工难点分析
由上述对零件尺寸和工艺结构的分析可知,丝杆零件存在以下工艺难点:
(1)丝杆最小直径为 Φ10 mm,位于螺纹退刀槽处,长径比为31.5∶1,属细长轴,刚性较差。在车削加工时,因受切削力、切削热和振动等作用和影响,极易产生弯曲变形,出现直线度、圆柱度等加工误差,导致切削加工很困难。
(2)梯 形 螺 纹 Tr20×4-7h-L 为 左 旋 螺 纹,车 削时,应使用左偏刀沿主轴轴线由卡盘向尾座方向走刀,或在后置刀具数控车床上车削。
梯形螺纹刀进行成型切削时,切削力较大,容易产生振动,使工件受力变形,因而难于加工。
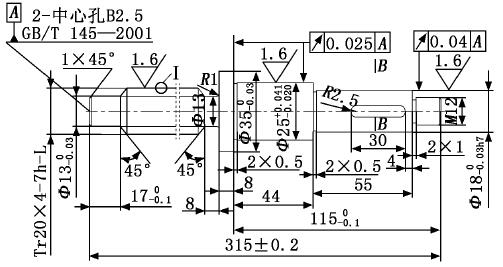
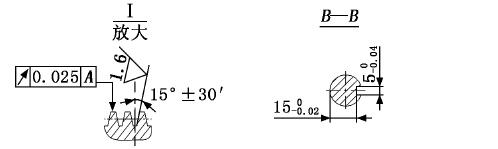
图1 车床尾座丝杆
2 、数控加工工艺设计
为保证丝杆加工精度,采用“粗车—精车”的加工工艺步骤,以下着重讨论丝杆加工难点———梯形螺纹加工工艺设计。
2.1 装夹与定位
为提高丝杆的刚性,采用一夹一顶装夹方式。工件的一端用三爪卡盘夹持,轴肩紧靠卡爪外端面,以固定工件的轴向位置,防止发生轴向窜动,另一端以顶尖支撑。
2.2 选择刀具
选择梯形螺纹车刀,采用 SEL2020K22型机夹刀杆,安装22EL4.0TR 型可转位刀片,刀片材料为涂层硬质合金,刀尖角为30°,取左刀尖为编程刀位点。梯形螺纹左偏车刀如图2所示。

图2 梯形螺纹左偏车刀
一般情况下,梯形螺纹车刀有3个刀刃参与切削,承受的切削力较大,容易崩刃,其加工精度和表面粗糙度不易保证,因此,进刀量宜小而均匀。
采用左右切削法可以获得较理想的切削效果,此时,应在牙槽两侧边各留0.15mm左右的精车余量,同时选择主切削刃宽度略小于牙槽底宽的刀片,确保能够进行左右切削加工。
2.3 切削方式
结合 FANUC系统 G 功能的螺纹切削指令,既可以采用螺纹切削复合循环指令 G76进行成型切削加工,也可以采用螺纹切削固定循环指令 G92进行左右切削加工。两种切削加工方法的进刀路线和适用场合有所区别。G76成型切削法,刀具沿牙槽一侧边斜进切入,这种进刀方法实际是使该侧副切削刃与工件处于摩擦状态,有效地减小了螺纹车刀承受的切削力反力,适合于小导程梯形螺纹加工。G92左右切削法,刀具沿径向直进切入,为避免3个切削刃同时切削而产生振动,利用用户宏程序条件循环指令编程,控制刀具分别向右、向左偏移一个距离,进行螺纹车削,该方法尤其适合车削大导程梯形螺纹。
当螺纹牙型较深时,还应将螺纹的切深分为多个切削层,在每个切削层,当刀具正常切到该层的切深后,再使用左右切削法加工螺纹。
3 、数控编程与工件试切
3.1 成型切削法编程应用
G76指令编程,成型切削加工梯形螺纹的主要程序如下:
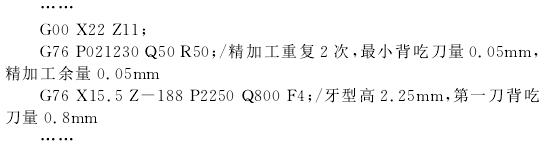
3.2 左右切削法编程应用
G92指令编程,左右切削梯形螺纹的主要程序如下:主程序:

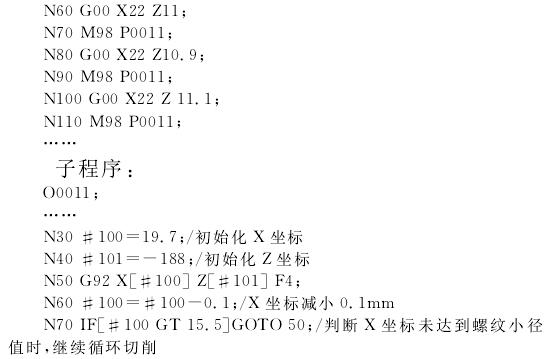
应用上述两种编程方法,在精度较高、磨损较少的机床上进行试切加工,并使用千分尺、梯形螺纹样板、螺纹环规及表面粗糙度仪等量具和设备,对梯形螺纹的牙型与尺寸进行检验分析。分析结果表明:应用两种工艺方案加工丝杆零件均为合格;应用左右切削法加工尾座丝杆,获得梯形螺纹尺寸精度较高,牙型两侧面表面粗糙度值较小,加工质量优于应用成型切削法加工。加工的尾座丝杆如图3所示。
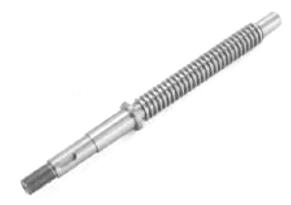
图3 车床尾座丝杆
4、结论
在数控车床上加工尾座丝杆,显著提高产了品质量和生产效率,提高了丝杆产品互换性,并大幅度减轻了劳动强度。应用 G76循环指令成型切削加工丝杆时,切削效率较高,切削力较大,振动大,容易产生腰鼓形误差和表面振纹;使用 G92循环指令及用户宏程序编程进行左右切削加工时,每次进给切削量小而均匀,但编程难度高,车削时间较长。应用左右切削法加工尾座丝杆的梯形螺纹,所获产品的尺寸精度和表面质量显著优于应用成型切削法加工的。
投稿箱:
如果您有机床行业、企业相关新闻稿件发表,或进行资讯合作,欢迎联系本网编辑部, 邮箱:skjcsc@vip.sina.com
如果您有机床行业、企业相关新闻稿件发表,或进行资讯合作,欢迎联系本网编辑部, 邮箱:skjcsc@vip.sina.com
更多相关信息