基于改进 PID 控制的数控机床主轴动态特性监测研究
2021-5-31 来源:陕西国防工业职业技术学院 作者:潘冬
摘要: 现有的数控机床主轴动态特性监测方法得到的监测数据计算量过大,导致计算得到的主轴刚度数值过小,针对这一不足,研究一种基于改进 PID 控制的数控机床主轴动态特性监测方法。首先计算主轴动态特性系数,提取数控机床主轴动态特性的监测信息,利用改进 PID 控制器控制特性数据的计量,完成对基于改进 PID控制的数控机床主轴动态特性监测的研究。采用嵌入式实验平台作为实验环境,以测力仪与千分表得出的数值为基准。实验结果表明: 与传统的监测方法相比,文中的监测方法得到的主轴变形量更准确,计算得到的刚度数值更大且符合实际值,适合在实际监测工作中运用。
关键词: PID 控制; 数控机床; 主轴; 动态特性; 监测
0 引言
数控机床已经渗透到各种现代制造的领域中,其发展和自主创新的水平,对我国未来科技和经济的发展有着重要的指导意义。动态特性指的数控机床主轴在运行时,输出量与输入量之间的关系,一般使用微分方程表示,表示输入量与输出量之间的传递函数。国外针对数控机床主轴动态特征检测研究较早,在二十世纪六十年代末,美国宇航局建立机械监测小组,标志着检测研究进入到应用阶段。但依照现有的技术水平来讲,欧洲国家在监测技术的某方面占据一定的领先地位。
我国虽然在监测研究方面起步较晚,但目前发展迅速,各个高校的研究小组都取得了一系列的研究成果。针对现有的监测技术而言,还需向高速、超精、智能化方向发展。
数控机床主轴动态特性,一般指的是主轴同步,也就是通过控制主轴电机,维持主轴的转速和位置。按照主轴同步的特性,主轴同步一般有 3 种运行方式。
第一种为基本同步方式,一条加工线上的不同主轴,在加工同一零件时,需要双主轴的转速保持同步,两主轴的角速度相等; 第二种则是维持比例的动态特性,也就是主轴间 的转速维 持一定 的 比 例,存在整数倍的数量关系; 第三种则是主轴间的动态特性有一定的线性关系,也就是主轴之间存在 n 倍加上一个固定值,按照不同的数控机床的工作实际,设置不同的固定值。所以针对这 3 种不同的动态特性,研究一种基于改进 PID 控制的数控机床主轴动态特性监测方法,准确地分析机床主轴的结构及性能,改进现有动态特性监测方法的不足,促进我国数控机床走向高速、高精度的设计方向。
1、基于改进 PID 控制的数控机床主轴动态特性监测研究
1. 1 计算主轴动态特性系数
1. 1 计算主轴动态特性系数
监控数控机床主轴动态特性系数时,按照主轴的工作特性,选取动态刚度作为数控机床动态性能指标,由达朗伯原理可知,主轴的动力基本表达式为:
[M]{x(t)}+[C]{x(t)}+[K]{x(t) ={ F(t)} ( 1)
上式中,[ M] 表示中轴的质量,[ C] 表示阻尼系数,[ K] 为刚度矩阵,x( t) 表示中轴节点的位移,F( t) 表示外力力量。去掉主轴相应的惯性力,此时就可得到主轴受到的静态力,计算公式为:
[K]{x}={F} ( 2)
由上式可知,主轴在实际工作时动态刚度表现在轴向与径向方向。轴向会使主轴产生单位位移,定义主轴的弯曲刚度 K 为主轴前端产生单位径向位移 s 时,位移方向所施加的力为 P,所以此时的刚度计算公式为:

按照如上所示的计算公式,计算得到随着转速变化,主轴的刚度值,如表 1 所示:
表 1 主轴随转速变化的刚度值
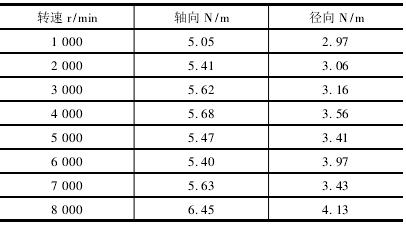
按照上述,不同转速下的刚度计算结果,综合主轴的各项参数,如表 2 所示:
表 2 主轴的各项参数
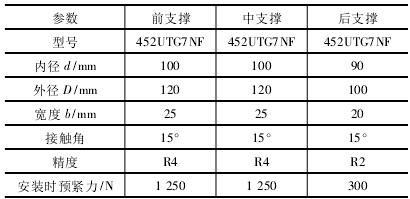

使用上述两表所示的各项系数,计算主轴在工作过程中的接触变形,主轴接触轴的球体与外圈滚道的接触符合赫兹接触。所以,此时主轴的点接触的接触变形,计算公式为:
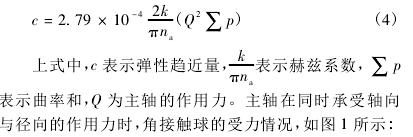
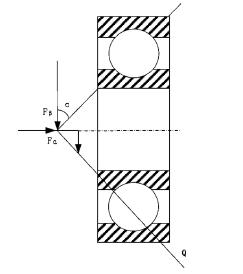
图 1 主轴角接触球的受力情况
由上图所示的受力情况,主轴内的滚珠所受的压力线相交于虚拟一点,此时滚轴受力平衡就可表示为:

上式中,Fr为轴向载荷,Fa为径向载荷,α 表示主轴的接触角,β 为滚轴中心与最大负荷滚珠之间的夹角。根据力的分析,建立力分析坐标系,叠加同一方向的外力值,最终联立上式( 3) 、( 4) 、( 5) 式,计算得到主轴动态的主轴动态特性系数,以得到的主轴动态特性系数为基础,结合主轴工作时的振动情况,提取监测信息,控制监测过程中的计算量,完成对监测方法的研究。
1. 2 提取监测信息
实际工作时主轴内部的各部件会产生振动,不同的动态系数主轴动态特性有着不同的振动信号,所以在提取监测信息前,首先按照主轴的振动形式自由振动、强迫振动和自激振动获取主轴的振动来源。机床主轴在数控机床正常工作时,发生突然的外力的概率较小,所以自由振动这部分不予分析。除此之外,主轴在正常工作时会受到数控机床各部分振动的影响,将主轴受迫干扰力划分为机床各个电机的振动,机床回转零件不平衡,运动传递过程中引起的振动、往复运动的冲击。主轴的负荷不均匀引起的切削力的变化以及机外振源部分进行获取。转换上述的振动方式形成四阶段的磨损能量,如图 2 所示:
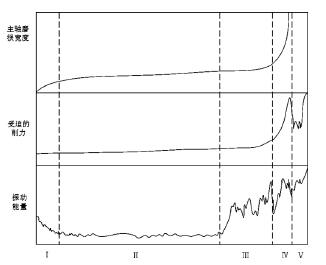
图 2 振动所对应的磨损能量
分析上图所示的振动以及振动所对应的磨损能量变化,假定上图采集到的数控机床主轴振动是含有趋势项的非平稳信号,先求出振动信号的均值,计算公式如下:
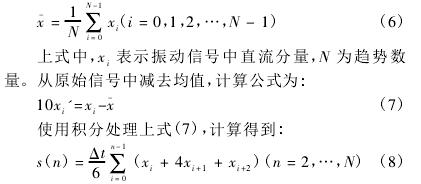
上式中,s( n) 为积分后的时间序列,Δt 为检测单元的采样间隔。综合处理上述主轴的振动,完成对主轴动态监测信息的提取。利用改进 PID 控制监测过程,完成对数控机床主轴动态特性监控的研究。
1. 3 利用改进 PID 控制器控制监测过程
利用改进 PID 控制器控制监测过程时,将上述提取的监测信息作为控制器的实际输入信息,假设经过改进PID 控制后的输出信号为 c( t) ,控制后的输出信号为:
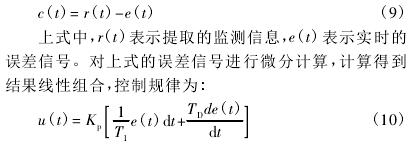
上式中,Kp为比例常数,T1为积分时间常数,TD为微分时间常数。设定一个 P 参数,用于 PID 控制器中产生的即成比例中的偏差。产生后立即成比例的作用于控制器,使其在最短的时间内消除偏差。为了降低 PID控制过程中产生的静差,降低控制过程的误差度,设定一个 D 参数,代入上式( 10) 中,积分控制积分时间常数,增大积分控制监测信息的强度。积分控制过程中,轴的监测信息偏差会获得较大的波动,需要在控制监测过程前对其进行一定程度的修正,为此设定一个 I 参数,代入到( 6) 公式中,缩短因偏差波动导致控制过程失调浪费的时间。
完成上参数的设定后,汇总所有得到的监测信息,采用位置式 PID 控制算法控制监测过程,控制算法计算公式为:

上公式中,k 表示监测序号,u( k) 为时刻 k PID 的控制输出值,e( k) 与 e( k-1) 为控制监测的输入与输出偏差,K1表示积分常数,KD为微分常数。综上即为位置式PID 控制数控机床主轴动态特性监测过程,但此算法输出采样时刻需要监测过程中的所有数据,并且与上一时刻输出数据相关,导致控制过程的计算量增大。所以设置 k 直接作用于被控监测单元,避免控制过程中的巨大计算量,保证控制过程的正常进行,最终实现利用改进 PID 控制监测的过程。完成对基于改进 PID 控制的数控机床主轴动态特性监测研究。
2 、实验
2. 1 实验准备
采用嵌入式实验平台作为实验环境,使用嵌入式监测单元采集数控机床的振动信号,依照信号来判断主轴内关键部件的动态特性信息。先利用嵌入式平台进行多通道采集,将采集到的数据经分析模块分析监测指标,处理监测数据,实现对监测数据的处理及分析。最终传输至计算机中予以计算显示,设置此过程监测环境的性能参数,如表 3 所示:
表 3 监测环境的技术参数
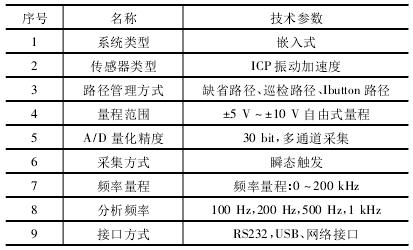
在上表中的各项参数的控制下,在数控机床主轴处安置千分表与测力仪,安置位置如图 3 所示:
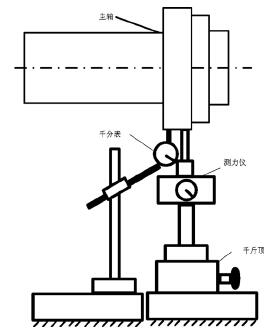
图 3 测量仪器的安置位置
利用卡盘装卡工件,在距离主轴前端 5 mm 位置( 有限元计算变形最大处) 加载,分别使用两种传统监测方法与基于改进 PID 控制的数控机床主轴动态特性监测方法进行实验,对比 3 种监测方法得到主轴的前端变形量结果。
2. 2 实验结果分析
分别控制 3 种方法在不同载荷下分别加载 3 次,以主轴的轴心为基准,测量主轴在受力点处的 3 次变形量,并取其平均值,记录不同载荷下的变形量,变形量结果如表 4 所示。
表 4 主轴前端变形量
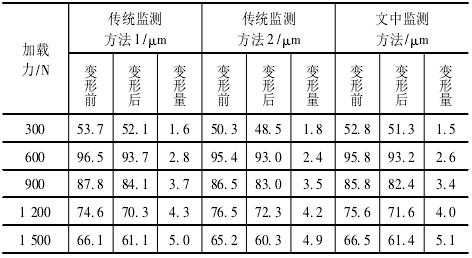
按照上表测量得出的变形量,计算出主轴系统的刚度,作为最终实验结果,3 种监测方法得到的刚度值,如表 5 所示。
表 5 刚度实验结果
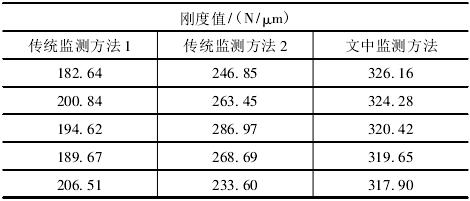
由上述实验结果可知,以千分表与测力仪测量数据为标准数据,3 种预测方法针对主轴同一位置,两种传统监测方法在获取主轴前端量变化量数值较大,明显大于标准数据,变形量数据获取不准确。而文中设计的监测方法获取得到的变形量与标准值相差不大,变形量数据获取较准确。基于获取的变形量数值,分别使用数据对应的监测方法计算主轴的刚度数值,结果表明: 传统监测方法 1 获取刚度平均值为 195 N/μm,传统监测方法 2计算得到的刚度平均值为 260 N/μm,而文中的监测方法计算得到的刚度值为 320 N/μm。综合上述计算结果可知,与两种传统监测方法相比,文中监测方法得到的主轴变形量数值准确,刚度值计算值更大,符合主轴刚度数值的实际,适合在数控机床主轴动态特性监测中实
际运用。
3 、结束语
机械制造业竞争日趋激烈,对数控机床的需求也就越大,按照现有的生产趋势,对数控机床主轴的动态特性进行监控已经是制造行业发展需要解决的共性及关键性技术。研究数控机床主轴动态特性监测方法,可以保证机床的生产效率以及产品的生产质量。传统的监测方法在获取主轴动态偏差量时存在误差,导致最终得到的主轴刚度数值过小,无法得到准确的主轴刚度数值,针对这一不足,引用改进 PID 控制算法,研究一种基于改进 PID 控制的数控机床主轴动态特性监测方法,改进了传统监测方法存在的不足,增强了监测方法的实用性。
投稿箱:
如果您有机床行业、企业相关新闻稿件发表,或进行资讯合作,欢迎联系本网编辑部, 邮箱:skjcsc@vip.sina.com
如果您有机床行业、企业相关新闻稿件发表,或进行资讯合作,欢迎联系本网编辑部, 邮箱:skjcsc@vip.sina.com
更多相关信息