双头深孔枪钻控制模型研究
2017-3-30 来源:湖北大学计算机与信息工程学院 作者:胡东红,刘景源,张玲,王平江
摘要: 根据工件所需钻孔的总排数、每一排的总孔数以及相邻排之间的距离,按照最优的加工模式,自动确定双头钻之间距离,自动确定钻孔模式,并自动生成 G 代码加工程序。提高钻孔加工效率而且避免用户繁杂的 G 代码程序编写和调试过程。
关键词: 双头钻; 深孔枪钻; 钻床; 数控中图分类号: TP391 文献标志码: A 文章编号: 1671—3133( 2016) 03—0037—04
0.引言
钻削直径较小、深度较大的孔,尤其是在钢件材料上钻深孔、小孔时,通常存在钻屑排除困难、刀具冷却困难以及钻孔轴线易歪斜等问题[1]。能否妥善解决这些问题,直接关系到深孔、小孔加工的质量、生产效率、加工精度和刀具热变形等,若处理不当,甚至可能使加工无法正常进行[2-3]。对此类深孔、小孔问题,枪钻是一个非常有效的解决方法[4-5],其主要特点是钻头中空细长,高压钻削油通过钻头中空管向钻头高速喷出,从而携带钻屑从枪钻的排屑槽向外喷出。深孔枪钻无需通过反复拔出钻头的方式进行排屑,相对于麻花钻有着无可比拟的优势[6],从而提高了加工工效。此外,深孔枪钻还采用钻头保护套,避免钻头歪斜。目前深孔枪钻广泛应用于汽车、模具、印刷机械、包装机械、食品机械和航空航天等装备制造领域的机械加工中[1]。此外,一些较复杂的工件排孔数很多,往往有几万个孔需要钻削,如果采用单头深孔枪钻,加工一个工件往往需要昼夜 24 小时连续加工半个月左右。
双头深孔枪钻的优势在于可以用两个钻头同时对工件进行钻削加工,理论上讲,可以节省加工时、提高加工工效近 50% 。但是,双头深孔枪钻编程较为复杂,需要确定钻孔模式。如果工件类型改变,排孔数发生变化,则需要重新进行编程、调试。用户使用起来较为麻烦,因此,本文提出了双头深孔枪钻的最优加工模式,可以根据工件的总排数、每排的孔数以及排间距等相关参数自动生成最优加工模式的 G 代码程序。从而极大地简化用户的编程和调试。
1.问题描述
1.1 双头深孔枪钻钻床的主要结构
数控双头深孔枪钻主要部件结构示意图如图 1 所示。左钻头和右钻头之间的距离可以通过手工调节后,保持固定。当左右钻头同时沿 X 轴方向移动时,可以分别同时对准圆筒工件上的两排孔; 当工件绕 C 轴旋转时,左右钻头可以分别对准圆筒工件上位于同一列的两排孔; 当左右钻头同时沿 Z 轴移动时,左右钻头可以对圆筒工件上位于同一列的两排孔进行钻孔。
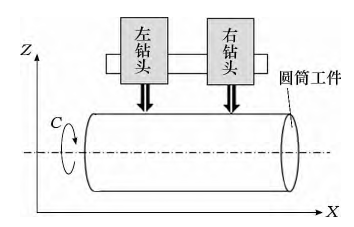
图 1 双头深孔枪钻主要部件结构示意图
1. 2 最优化钻孔模式要求
最优的双头深孔枪钻钻孔模式应该是: 尽量采用双钻模式进行钻孔,即左右钻头同时钻孔,以提高加工效率。若实在无法采用双钻模式钻孔的孔位,采用单钻模式钻孔,即只用左钻头或只用右钻头钻孔,因此,如何根据工件的总排数、每一排的总孔数以及排间距,自动确定左右钻头之间的距离,确定哪些排孔采用双钻模式,哪些排孔采用单钻模式,是双头深孔枪钻实现自动最优化钻孔模式的关键所在。
2.双头深孔枪钻最优钻孔模式分析
一个圆筒工件及其展开后的排序号和孔序号示意图如图 2 所示。由于奇数排的孔和偶数排的孔沿 X轴线方向不在一条直线上,且相互错位半个孔间距,因此,左钻头和右钻头无法分别钻奇数排的孔和偶数排的孔。左钻头和右钻头只能同时钻奇数排的孔,或者同时钻偶数排的孔。
如图 3 所示为工件总排数为 8 排时的钻孔模式。如果工件的总排数为 8 排,显然,最合理的钻孔模式是左钻头和右钻头的间距为孔的排间距的 4 倍最为合理。这样,左钻头对准第 1 排时,右钻头对准第 5 排。在左右钻头同时完成对第 1 排和第 5 排的全部钻孔之后,左右钻头分别对准第 2 排和第 6 排,同时完成第 2排和第 6 排的全部钻孔。同理,左右钻头可以同时完成第 3、7 排,第 4、8 排的全部钻孔。可以将该过程描述为: 用双钻模式,第 1 轮完成对第 1、5 排的钻孔; 第2 轮完成对第 2、6 排的钻孔; 第 3 轮完成对第 3、7 排的钻孔; 第 4 轮完成对第 4、8 排的钻孔。一共进行 4轮钻孔,所花时间相当于钻 4 排孔的时间。
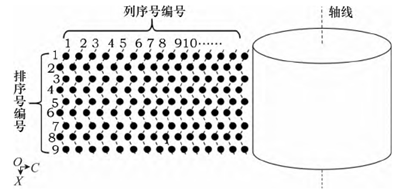
图 2 圆筒工件展开后的排序号和孔序号示意图
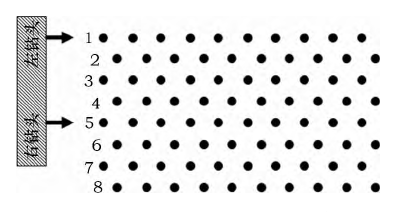
图 3 工件总排数为 8 排时的钻孔模式
如果工件的总排数为 9 排时,显然,最合理的钻孔模式是: 按照总排数为 8 排的模式,完成对 8 排孔的钻孔之后,拆掉一个钻头,用剩下的一个钻头进行第 5 轮钻孔,完成对第 9 排全部孔的钻孔。一共进行 5 轮钻孔,所花时间相当于钻 5 排孔的时间。
如果工件的总排数为 10 排,显然,最合理的钻孔模式是: 按照总排数为 8 排的模式,完成对 8 排孔的钻孔之后,拆掉一个钻头,用剩下的一个钻头进行第 5轮、第 6 轮钻孔,完成对第 9、10 排全部孔的钻孔。一共进行 6 轮钻孔,所花时间相当于钻 6 排孔的时间。
但是,当工件的总排数为 11 排时,如果仍然按照总排数为 8 排的模式,完成对 8 排孔的钻孔之后,拆掉一个钻头,用剩下的一个钻头进行第 5、6、7 轮钻孔,完成对第 9、10、11 排全部孔的钻孔。这样一共进行 7 轮钻孔,所花时间相当于钻 7 排孔的时间。事实上,当工件的总排数为 11 排时,最合理的钻孔模式是: 左右钻头的间距设定为孔的排间距的 6 倍,图 4 所示为工件总排数为 11 排时的最优钻孔模式。这样,左钻头对准第 1 排时,右钻头对准第 7 排。钻孔过程可以描述为:用双钻模式,第 1 轮完成对第 1、7 排钻孔; 第 2 轮完成对第 2、8 排钻孔; 第 3 轮完成对第 3、9 排钻孔; 第 4 轮完成对第 4、10 排钻孔; 第 5 轮完成对第 5、11 排钻孔;第 6 轮拆掉一个钻头,用一个钻头采用单钻模式完成对第 6 排的钻孔。这样一共进行 6 轮钻孔,所花时间相当于钻 6 排孔的时间。
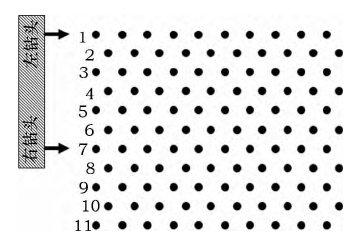
图 4 工件总排数为 11 排时的最优钻孔模式
从上述分析可以看出,工件总排数为 4 的整数倍,即 4n( n = 1,2,…) 时,左右钻头的间距应该为排间距的 2n 倍。一共进行 2n 轮双钻模式钻孔。总排数为4n 时的最优钻孔模式如表 1 所示。
表 1 总排数为 4n 时的最优钻孔模式
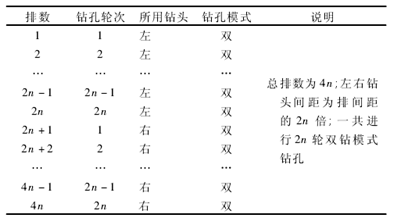
工件总排数为 4 的整数倍余 1,即 4n + 1,( n = 1,2,3,…) 时,左右钻头的间距应该为排间距的 2n 倍,钻孔的轮次数 2n + 1 轮次。其中 2n 轮次为双钻模式,1 轮次为单钻模式,总排数为 4n + 1 时的最优钻孔模式如表 2 所示。
表 2 总排数为 4n + 1 时的最优钻孔模式
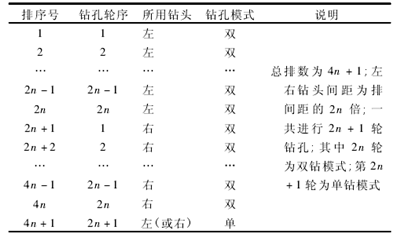
工件总排数为 4 的整数倍余 2,即 4n + 2,( n = 1,2,3,…) 时,左右钻头的间距应该为排间距的 2n 倍,钻孔的轮次数 2n + 2 轮次。其中 2n 轮次为双钻模式,2 轮次单钻模式。总排数为 4n + 2 时的最优钻孔模式如表 3 所示。
表 3 总排数为 4n + 2 时的最优钻孔模式
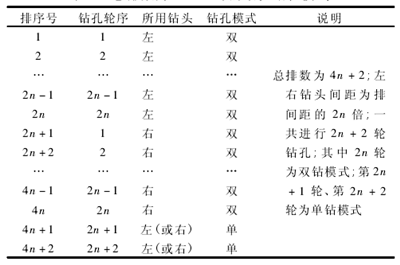
当工件总排数为 4 的整数倍余 3,即 4n + 3,( n =1,2,…) 时,左右钻头的间距应为排间距的 2n + 1 倍,钻孔的轮次数 2n + 2 轮次。其中( 2n + 1) 轮次为双钻模式,1 轮次为单钻模式。总排数为 4n + 3 时的最优钻孔模式如表 4 所示。
表 4 总排数为 4n + 3 时的最优钻孔模式
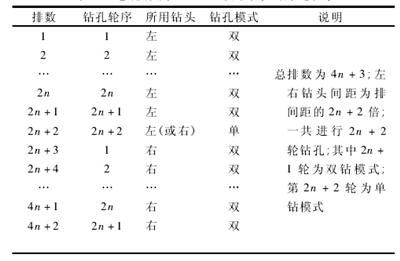
3.结语
根据上述双头深孔枪钻最优钻孔模式算法,在华中 21 型数控系统平台上进行二次开发,实现了本方案的应用。用户只需输入工件的总排数、每排的孔数、排间距和钻孔时的速度等相关参数,数控系统即可自动生成最后的钻孔加工程序,从而极大地简化了用户的编程和调试。
加工后尺寸精度难以把控的特点,创新性地提出了运用五轴联动数控砂带磨床对其表面进行高效高精度打磨,机床的工艺灵活性与加工适应性均得到了较高程度的提升。最后进行了实际加工实验,结果证明叶片型面磨削效果与磨削效率远高于现阶段高强度且磨削质量难以管控的手工作业方式。
2) 本文在不牺牲数控砂带磨床原有加工效率的前提下优化了磨削工具进入叶根圆角难加工区域的位姿形态,使磨削工具的可达磨削区域得到了一定程度上的提升。
投稿箱:
如果您有机床行业、企业相关新闻稿件发表,或进行资讯合作,欢迎联系本网编辑部, 邮箱:skjcsc@vip.sina.com
如果您有机床行业、企业相关新闻稿件发表,或进行资讯合作,欢迎联系本网编辑部, 邮箱:skjcsc@vip.sina.com
更多相关信息