基于精雕系统的七级叶轮加工技术实践
2024-3-7 来源:北京精雕科技集团有限公司 作者:张欢龙
1. 序言
叶轮是涡轮增压器最关键的零件之一,广泛应用于航空、船舶、汽车和真空泵等行业的发动机中,其中七级叶片的复杂叶轮是涡轮分子泵内部的核心部件,而涡轮分子泵则广泛应用于真空镀膜(PVD)、半导体制造等行业中,这些行业需要在超高真空环境(10-7Pa 以下)中才能工作。
考虑到叶片结构复杂、曲面变化大以及精度高等特点,目前一般采用 Mastercam、PowerMill、UG及CATIA等国外软件结合五轴联动机床加工,这些五轴联动机床一般采用海德汉、西门子等国外高档数控系统。为打破国外软件和数控系统在叶轮制造方面的垄断地位,北京精雕科技集团有限公司(以下简称北京精雕)开发了拥有自主产权的 SurfMill 软件以及北京精雕五轴联动系统,并采用在线检测、在线补偿功能加工叶轮。
本文采用北京精雕的 SurfMill 软件造型并采用 JDGR400 五轴联动精雕机,对七级叶轮的五轴编程、工艺规划和实际加工进行探讨与实践。
2.七级叶轮结构及加工难点分析
七级叶轮(见图 1)的基本特点 : 叶片分为7 级,共 249 个叶片,材料为 7075 铝合金,尺寸f360mm×286mm。该零件上的叶片是由铝合金整体加工而成,叶片加工完成后整体质量 14kg。
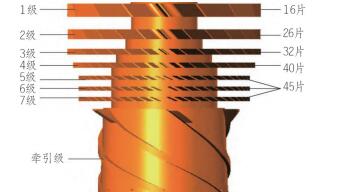
图 1 七级叶轮
经分析,七级叶轮五轴联动加工的难点如下。
1)该叶片属于典型的薄壁件,叶片高度与厚度比> 30:1,叶片刚性差,加工时受力易变形,极易产生振动,弹刀过切风险很大。
2)相邻叶片间距小,导致加工所需刀具最大长径比为 14:1(见图 2),加工时刀具的切削刚性差。
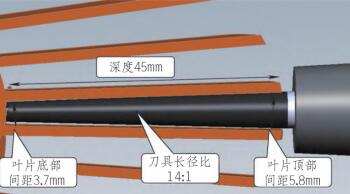
图 2 刀具长径比示意
3)叶片数量多达 249 个,叶片间距小,每一级之间距离小,刀具和叶片之间的安全距离最小只有 2mm,加工时极易产生干涉,如图 3 所示。
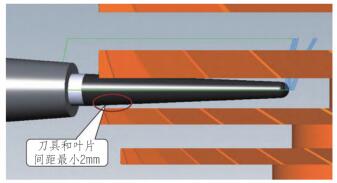
图 3 刀具与叶片干涉示意
3.七级叶轮五轴加工工艺规划
3.1 设备及软件的选用
叶轮加工设备需要有强大的运算能力,且加工时主轴转速高、摆动角度范围大、联动精度高,本次选用北京精雕的 JDGR400_A15SH 机床,配置在机测量系统、激光对刀仪等设备,并采用北京精雕自有的软件 SurfMill 进行建模和编程。
3.2 刀具的选用
针对薄壁件,刀具的选择需要从减小切削力的角度出发,因此选择角度较大的前角和后角、较大的螺旋角(见图 4)来减小切削力 ; 刀具结构采用短刃刀具(见图 5),锥度避空,提升刀具刚性 ; 涂层选用 DLC 涂层,涂层厚 1μm,提高刀具锋利度,减小切削力,提高刀具寿命及长时间加工时的稳定性。
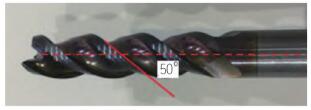
图 4 大螺旋角

图 5 锥度平底短刃刀具
3.3 加工工艺方案
针对长径比大的难题,为了增加刀具的刚性,在深度上采用多把刀具分段加工的方式,以保证切削刚性,提高加工效率。刀具型号及加工参数见表 1。
表 1 刀具型号及加工参数
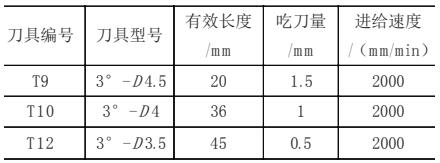
3.4 编程加工方案
七级叶轮叶片数量多、间距小,刀具极易产生干涉和过切。为避免在实际加工中出现问题,采用北京精雕的 DT 编程技术,在软件中实现过切检查、干涉检查和机床模拟,在计算机端确保加工程序的安全,从而避免机床实际加工中的过切、干涉和碰撞等问题,如图 6 所示。
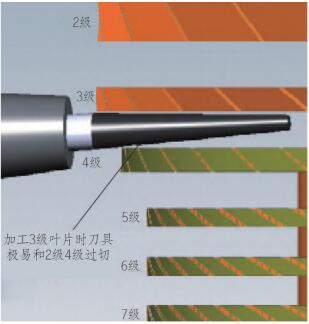
a)刀具与工件干涉示意
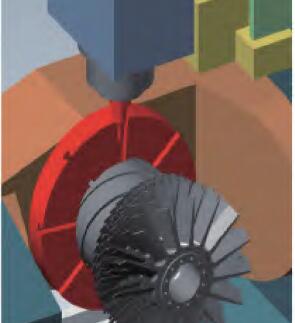
b)DT 仿真加工
图 6 叶轮加工模拟
DT 编程技术最大的特点就是改变原有的调试模式,将原来需要在机床上进行的操作(包括试切加工、人为观察过切和碰撞,以及机床行程检测等),全部加载到计算机中进行,减少人员机床上的操作,减轻调试人员的心理压力,降低调试出错的成本,缩短产品调试周期。
4. 加工试验及方案改进
按照规划的方案进行加工试验,试制结果见表 2。通过表 2 数据可看出,试制结果不满足工艺要求,需要优化改进。
表 2 试制结果
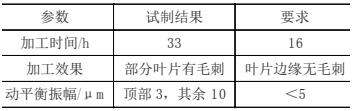
4.1 方案优化改进
经分析,需要从 4 个方面进行优化改进 : ①优化加工效率。②改善表面质量。③改进夹持治具。④管控毛坯精度。
1)利用 CAM 软件优化叶片间连刀高度。第一阶段为保证绝对的安全,将叶片之间路径安全位置设置在 Z 轴原点位置 ; 优化阶段依靠 DT 编程技术,将刀具连刀高度抬至叶片最高高度之上30mm,加工时间缩短了 6.5h。
2)优化 T9、T10 刀具有效长度,增加刀具刚性。试制用的 T9、T10 刀具有效长度过长,刀具刚性差,切削参数无法提升,严重影响加工效率。依靠 D T 编程技术,精确计算 T9、T10 刀具所需的最短有效长度,从而提升刀具刚性,增加刀具切削用量,将叶轮加工时间缩短了 55min。
3)优化表面质量,缩短人工处理时间。叶轮加工完成后,其叶片锐角边留下了大量的毛刺,需要手工清理,工作量较大,并且毛刺会影响工件整体动平衡性能,因此在加工时加入去毛刺程序,节省去毛刺的时间。另外,在机测量刀具锥度,减轻不同刀具间的接刀痕,使用激光对刀仪准确测量刀具锥度和直径,将刀具偏差补偿在加工路径中,确保各刀具间的接刀痕< 0.008mm。
4.2 解决动平衡问题
对于产品的批量生产,动平衡振幅能否控制在 5μm 以内是生产的关键。目前机床精度、温度管控都是合格的,针对动平衡偏大问题,经过分析判断,是治具锥面和毛坯锥面配合误差较大,使得毛坯安装后毛坯轴线倾斜引起的。毛坯轴向圆跳动> 0.04mm,直接影响叶轮加工后的动平衡。治具夹持如图 7 所示。
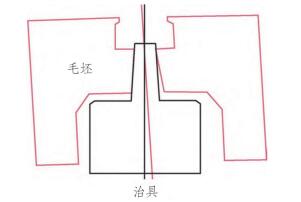
图 7 治具夹持示意
重新精磨治具,其锥度达到 5° 43′ 9″,毛坯安装后跳动得到大幅改善,结果见表 3。
表 3 精磨治具后跳动改善结果
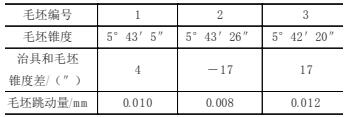
4.3 曲面加工方案
叶片曲面根据曲率可分为自由曲面和直纹曲面,自由曲面采用五轴点铣方式加工,直纹曲面采用五轴侧铣方式加工,如图 8 所示。
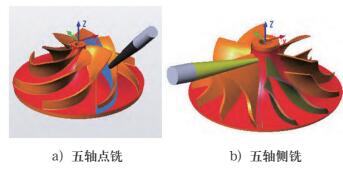
图 8 曲面加工方式示意
在 SurfMill 中建模和编程。分层粗加工如图9 所示,流道精加工如图 10 所示。
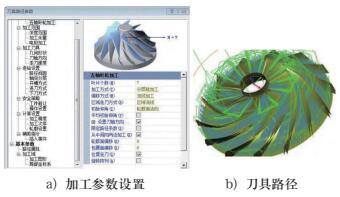
图 9 分层粗加工
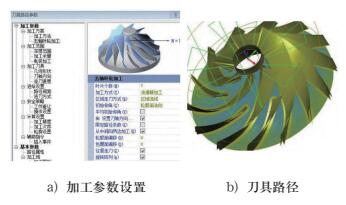
图 10 流道精加工
4.4 改进后的实际加工验证
利用 DT 技术和软件编程,优化了刀路和加工程序,避免了干涉,消除了动平衡,提高了加工效率,同时零件的加工质量得到提升。加工后的零件如图 11 所示,经检测,达到了叶轮尺寸精度和表面粗糙度的要求。
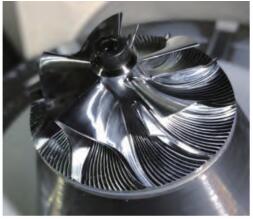
图 11 加工后的七级叶轮
5. 结束语
本文在分析七级叶轮结构特点和加工难点的基础上,对机床选用、刀具选择、工艺修正以及治具改进等做了深入分析。为提高效率,避免干涉,采用北京精雕特有的 DT 技术进行模拟校正,并通过试件的研制,优化一系列工艺参数,最后在北京精雕五轴联动机床上完成七级叶轮的加工,加工精度、表面粗糙度以及动平衡等都符合要求,给类似的叶轮及复杂零件的加工提供了参考。
投稿箱:
如果您有机床行业、企业相关新闻稿件发表,或进行资讯合作,欢迎联系本网编辑部, 邮箱:skjcsc@vip.sina.com
如果您有机床行业、企业相关新闻稿件发表,或进行资讯合作,欢迎联系本网编辑部, 邮箱:skjcsc@vip.sina.com
更多相关信息