高速机床直线电动机进给系统热行为分析
2019-3-13 来源:上海工程技术大学 上海理工大学 作者:吴倩倩 林献坤
摘 要: 在高速机床中,以直线电动机驱动的进给轴为对象,应用有限元工具对全闭环位置反馈的进给机构的热源分布进行了分析,给出模型的简化方法,确定了进给轴热载荷相关参数,对进给轴 Y 轴的热变形特性进行了定性分析。在自构建的实验台上,对直线电动机驱动进给轴 Y 轴的热变形特性进行了综合试验研究,确定了热电偶、激光干涉仪、电容式测微仪的热变形试验方案和试验步骤,
分析了直线进给轴稳态温度分布及其热变形规律。结果表明:主轴刀具位置热偏差是由滑台受热扭曲热位移、光栅尺膨胀热位移和导轨俯仰角偏热位移的三者综合作用的结果;短行程的主要因素是滑台扭曲变形和导轨角偏,长行程的主要影响因素为光栅尺的热变形。
关键词: 高速机床;直线电动机;热变形;有限元
效率和加工精度是当代先进制造领域的一个重要课题,高速和高加速度的切削进给轴是实现高速高精密切削加工的重要条件之一。传统的“旋转伺服电动机 + 滚珠丝杠”式进给轴的传动机构存在螺距误差、反向间隙、磨损、摩擦以及螺杆本身的弹性变形等问题。直线电动机驱动进给轴是一种不需要中间转换机构的传动装置,具有进给速度快、加速度大、响应速度快、定位精度高等优点],直线电动机驱动的进给轴突破了传统的滚珠丝杠式进给轴在速度和精度方面的限制,在高速高精密机床中得到越来越广泛的应用。
机床误差源中,热误差原本就是精密机床最主要的误差源之一,可占到机床误差的 70%。在高速进给条件下,直线电动机初级线圈发热量大,温度可达100 ℃ 以上,由于热变形因素在一定程度上影响了它在精密机床中的应用。关于直线进给轴的热变形及其带来的热误差问题,在国外已经得到较大关注,EUNI U研究了隔温层对直线进给轴热行为的作用效果;KIM J J 等应用有限动轴的热行为作用效果; 在国内,对直线电动机驱动机床进给轴及其特性的研究,主要集中在: 进给轴平台的滑模控制、直线电动机驱动进给轴的轮廓精度在线补偿方法等,但对于机床直线电动机驱动进给轴的热行为研究还较少。
本文采用有限元分析与试验测试结果分析相结合的方法,对高速直线电动机驱动进给轴进行的热行为进行研究。应用 Solid Works Simulation 对机床热源进行有限元分析,定性地分析高速机床直线电动机驱动进给轴 Y 轴的温度场分布及其变化规律,以仿真分析结果为基础,制定合理的试验方案,对进给 Y 轴的热源分布和热变形进行了试验研究,将模型仿真结果与试验测试结果进行对比分析,定量分析了由热变形引起的直线电动机驱动 Y 轴进给误差的各组成要素及其变形规律,研究成果为直线进给轴的优化设计及其在精密机床中的应用提供重要理论支持。
1 、有限元仿真分析
1. 1 建模对象
实验对象为自构建的直线电动机驱动龙门结构进给机构,该进给机构具有 X1、X2、Y、Z 多轴联动结构,本文以 Y 轴进行有限元分析对象,其结构如图 1 所示,其中 Y 轴依靠 A 与 B 两端分别固定于 X1、X2 轴上,带动主轴与 X1、X2 轴联动,其中 A 端与 X1 轴铰接,B 端与 X2 轴滑块连接,进给 Y 轴通过上、下两根导轨支撑主轴滑台高速进给运动。
Y 轴的直线电动机型号为 SIEMENS 1FN3,位置环反馈选用 LC183 型号的光栅尺,在数控系统作用下实现进给轴全闭环位置反馈进给。
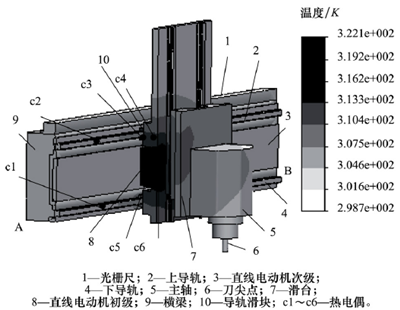
图1 进给Y轴温度场分布及温度测点布置
1. 2 模型假设
直线进给轴所具有的对象存在多个部件,结构较复杂,应用有限元直接进行建模仿真较为困难,简化对象模型是有限元分析常用方法。因此,在建模过程对模型做了如下假设:
(1) 不考虑外部热源通过热辐射对进给轴的影响,进给轴上的热源也不通过热辐射影响进给机构部件。
(2) 支撑滑台运行的所有导轨滑块直接与滑台固结一体,两者之间不存在热阻,也不产生相对热位移。
(3) 简化导轨滑块内的滚动摩擦为滑动摩擦,假设导轨和运动的滑块之间热阻无限大,但有热流量均匀作用在导轨和滑快的表面上,滑块的热变形不施加附加作用力给导轨表面。
(4) 进给轴换热表面的对流传热系数是一个常数,不受进给轴温度和机构的形状分布影响。
1. 3 热载荷参数的确定
定义进给机构的热载荷分布,包括: 直线电动机初级发热量 Qm; 初级侧的线圈与滑台之间靠螺栓连接两者之间存在热阻,用 Rt表示; 滚动摩擦产生的热量以及滑台与导轨温度差的热传导热量总
和,作用在导轨表面上,用热流密度 qG表示; 与导轨接触滑块表面的热量包含摩擦热与热传导两部分,用热流密度 qs表示,进给机构表面的热对流系数 αc。
根据数控系统中获取的直线电动机运行流Ieff,及最终热稳态温度 Td,可采用如下公式,计算电动机热损耗功率:
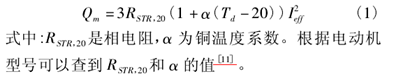
依据文献,给出的空气热对流系数计算方法,可以近似确定热对流系数 αc; 再根据热稳态试验,可以仿真计算得到图 1 中示意的 c2、c3、c5 点的温度,依据其温度和温度差分布,经过重复仿真模拟,可初步确定热流密度 qG、qs以及热阻 Rt的组合值。根据理论分析和重复验证这种方法,以最大推力 1 470 N 的1FN3 直线电动机进行计算,得到如表 1 所示热载荷参数。
表 1 热载荷参数
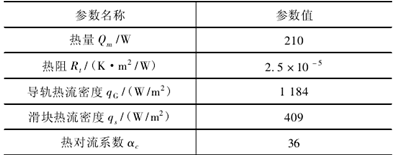
1. 4 模型分析
应用 Solid Works Simulation 有限元分析,对直线进给轴 Y 轴进行建模,选择合适的网格密度对进给轴进行网格划分,总共生成 23 813 个单元和 41 081 个单元节点。应用这些热载荷参数,以 298 K 为环境温度,计算得到如图 1 所示的进给轴热稳态分布。从图 1 中可以看出直线电动机初级温度最高,是进给轴中最主要热源,直线进给轴上、下导轨的温度场分布基本一致。
应用该稳态热力算例和所建立有限元网格,进一步建立静态热位移算例,参考建模对象的装配约束方式,定义横梁 A 端为固定几何体型约束,B 端为滚柱/滑杆约束。求解静态热位移算例可得到热合位移,经过三维分量独立分析可知,Y 轴向的热位移明显比 Z轴向和 X 轴向的热位移大,因此 Z 轴向和 X 轴向在热变形中不再考虑。图 2 中以 1 776 倍的变形比例表示了 Y 轴向的热变形图解示意图,图中 Y 轴向的最大热变形量已达到了 40 μm 以上,主轴刀尖点沿 Y 向的热误差值最大。
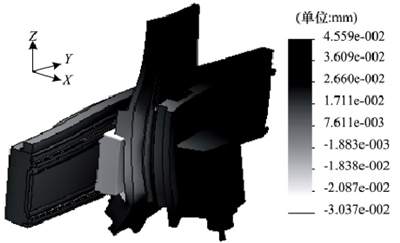
图2 热变形示意图
综合分析图中主轴刀尖在 Y 轴进给运动过程中的热位移,热位移由光栅尺膨胀热位移、Y 轴向俯仰角偏热位移和滑台本身在 Y 轴向的扭曲热位移三个部分组成。其中进给轴采用全闭环位置定位反馈,导轨受热沿 Y 向伸长不会影响刀尖点的轴向定位,但光栅尺膨胀变形在 Y 向的热位移量则直接决定进给轴的定位精度; Y 进给轴上、下导轨对称安装,温度分布基本一致,上、下导轨在 Z 方向的膨胀量相当,膨胀方向相反,在 Z 向的变形,作用到 Y 向上的位置误差可以相互抵消不产生轴向旋转偏差,但在 X 方向上,上下导轨膨胀的方向相同,这种膨胀对刀尖点在 Y 向的定位通过轴向俯仰角偏产生影响,具体作用机理如图 3所示。图中进给轴导轨在 X 方向上的膨胀导致进给轴发生角偏,假设大小为 θ,刀尖点也随之发生 Y 轴向位置偏差 e,可表示为:

式中: L 为刀尖点到 Y 轴导轨的垂直距离; e 为 Y 轴向偏差; θ 为角偏。
由式(2) 可知,Y 轴向偏差 e 受 L 和 θ 两个因素影响。
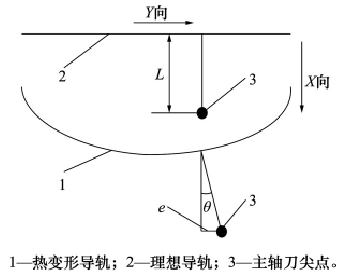
图3 导轨角偏示意图
2 、实验研究
2. 1 试验测试系统的构建
为了进一步对模型仿真结果做定量验证,本文通过构建如图 4 所示的试验系统进行试验研究。
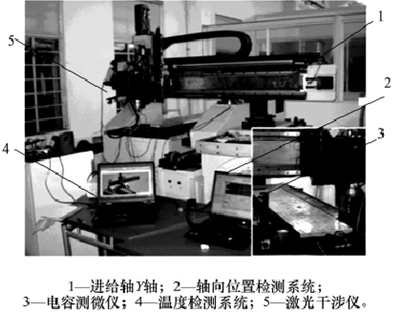
图4 热行为实验系统
图 4 中温度检测系统由热电偶、XMDA - 16 智能多点温度巡检仪与 Visual C + + 开发的温度数据采集软件实现,试验拟采用 8 个热电偶,其中热电偶 c1 ~c6 的分布位置如图 1 所示,热电偶 c7 位于标尺光栅上,用来测试标尺光栅温度,c8 用于测试环境温度,设置温度采集周期为 15 s。进给 Y 轴定位误差由 MCV- 500 激光干涉仪测量,该传感器的测量精度为 0. 1μm,测量行程可达数十米,激光干涉仪配备 X、Y 两套激光头组件,为了理清光栅尺变形的影响成分,把 X激光头组件的反射镜固定在标尺光栅附近,用来测量标尺光栅位置误差; Y 激光头组件的反射镜固定在主轴上,用来测试主轴位置误差,试验中选用 Y 轴向定位自动检测系统测量位置误差数据。另外选用 ca-pa NCDT6100 电容测微仪测量滑台变形。
2. 2 试验方法
编写机床 G 代码,使进给轴 Y 轴带动主轴滑台在坐标 Y( 200,800) 区间作高速往复进给,设置进给速度为 60 m/min,进给加速度为 3 m/s2。为了配合激光干涉仪测试进给轴位置误差,每隔
30 min,设置进给轴在Y( 200,800) 区间沿 Y 正向等步长间歇进给,步长为 30mm,每进给一个步长暂停 4 s,测试过程的进给速度为500 mm / min。具体的试验步骤如下:
步骤 1 采用激光干涉仪对主轴刀尖点和 Y 轴光栅尺,进行一次机械安装偏差对位置影响的测定,作为机床的初始偏差;
步骤 2 控制机床使主轴停在起点 Y200 处,用电容测微仪测试机床主轴刀尖点位置一次;
步骤 3 编写机床工作 G 代码,驱动 Y 轴在 Y( 200,800) 区间连续作高速往复运动,30 min 后中止;
步骤 4 编写测试 G 代码,驱动滑台沿 Y 轴正向作30 mm 等步长间歇进给,同时激光干涉仪采集 Y 轴位置误差数据一组;
步骤 5 重复步骤 3 和 4,直至各测点温度上升曲线趋平缓,达到热平衡,最后采集一组位置数据。
整个测试过程历时 270 min,共采集 8 个 测 点1 243个时间点的温度数据、9 组主轴位置误差数据、9组标尺光栅位置误差数据和 2 组滑台扭曲变形数据。
3、 结果分析
3. 1 温度场分析
采用上述的试验方案完成对 Y 轴的温度测试,各测点的时间 - 温度曲线如图 5 所示。图中曲线表明,在高速重复进给过程中,机构的各个测点温度均呈逐步上升趋势,在 180 min 后,曲线变得平缓,说明测点达到了热平衡。由图 5 可知,直线电动机初级附近测点 c5、c6 的温度明显高于其他测点温度,说明直线电动机初级是机床直线进给系统的主要热源,c5 比 c6更靠近热源,所以 c5 比 c6 的温度高。
上、下导轨测点 c1、c2 及两个滑块测点温值相差不大,说明作用在上下导轨摩擦产生的热量基本一致。通过分析比较热电偶所有测量点的温度与有限元仿真得到的温度,二者基本吻合,其中最大的偏差小于 1℃ ,所用的有限元模型较好地仿真了进给轴温度分布。另外,温度曲线存在周期性的毛刺,毛刺发生的时间点对应测试位置误差的时间点,主要原因是低速进给造成对流换热表面的传热系数降低导致温度升高。
3. 2 热变形分析
在机床产生热变形前,采用激光干涉仪对主轴刀具位置和光栅尺进行一次测定,用以排除机械安装误差。如图 6 所示,图中曲线 1 和曲线 4 分别为激光涉仪测量的热变形前光栅位置偏差和滑台沿 Y 方向移动的主轴刀具位置偏差。为了消除机械安装误差的影响,利用最小二乘法拟合光路直线,将测量曲线减去拟合直线,得到光栅尺和主轴位置轴向机械偏差,为图6 中的曲线 2 和曲线 3 所示。
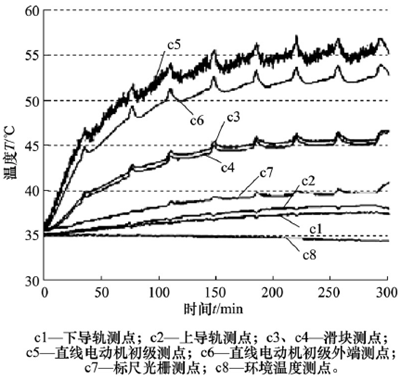
图5 时间-温度曲线
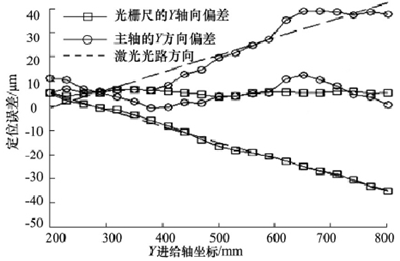
图6 Y轴安装误差的测量
获得机械本身的安装偏差后,对进给轴 Y 轴达到热平衡时的变形进行测量,得到图 7 所示的变形趋势。图 7 中曲线 1 是主轴刀具进给位置去除机械偏差之后的 Y 轴向定位热变形偏差,曲线 2 是光栅尺去除机械偏差之后的 Y 轴向定位热变形误差,为了比较分析热变形的分量,图中引入有限元仿真的变形结果并作对比。图 7 中曲线 4 是有限元仿真计算得到光栅尺膨胀热变形,曲线 5 是导轨俯仰角偏带来了主轴位置 Y 轴向偏差分量,曲线 3 是 Y 轴滑台热变形、光栅尺膨胀热变形和导轨俯仰角偏带来的主轴刀具位置 Y 向偏差三者变形的总和。
综合分析图 7 中的比较结果可见,曲线 3 和曲线 1基本接近,最大偏差不超过 10 μm,且曲线 1 都落在偏离实际测量的 Y 轴向偏差带范围( 图中两虚线之间) 之内; 曲线 2 和曲线 4 两者之间偏差更小,在 800 mm 处的偏差也只有 3. 2 μm; 由电容测微仪测得的 Y 轴滑台热变形 9. 1 μm,而用有限元分析的 Y 轴滑台热扭曲变形在刀尖点处的偏差是 8. 8 μm,这些比较表明,有限元仿真分析过程所采用的热载荷参数是准确的。
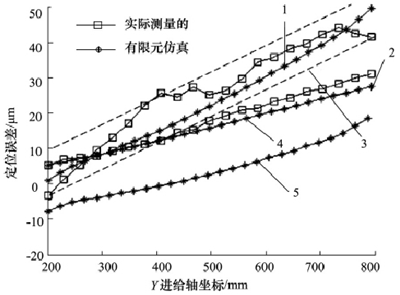
图7 Y轴变形测量与仿真比较
对比曲线 1 和曲线 2,光栅尺热变形是影响进给轴误差的关键因素,因此在设计中减少对光栅尺传热量对于提高定位精度具有重要作用。另外,曲线 3 和曲线 1 的偏差较小,进一步表明: 光栅尺热膨胀变形、滑台热扭曲变形和导轨俯仰带来的进给偏差是共同导致主轴刀具定位位置热误差的主要因素。图 7 中曲线2 可知,由于受到热膨胀的影响,光栅尺的定位发生偏差,行程越长,偏差越大,且偏差基本是线性。
为了对进给系统热变形进行定量的分析,取机床Y 坐标 800 mm 处的点,进行对比分析,因热膨胀光栅尺变形引起的偏差 26. 9 μm,导轨角偏引起的偏差13. 5 μm,滑台受热扭曲变形 9. 0 μm。由此可见,在重复短行程的定位中,主要热误差是滑台受热扭曲变形和导轨角偏引起的; 在超过 600 mm 的长行程重复进给中,光栅尺的热变形影响主轴刀具位置的比例将大于 50% ,光栅尺的热膨胀变形是引起进给轴 Y 轴热误差的关键因素。
4 、结语
(1) 通过试验和理论分析相结合,应用有限元模型可以较好地分析直线进给轴热稳态温度分布和进给轴热变形趋势。
(2) 直线电动机初级线圈发热是导致机床进给系统热误差的主要原因。为减小直线电动机驱动进给系统热误差,可以优化机床结构设计,采取良好的冷却和隔热系统。
(3) 直线进给系统热变形引起的主轴刀具位置定位误差主要是由光栅尺受热膨胀变形误差、导轨俯仰角偏差带来的进给偏差和滑台热扭曲变形偏差三个部分组成。
(4) 热误差的主要影响因素,根据行程的长短有所不同,短行程的主要因素是滑台扭曲变形和导轨角偏,长行程的主要影响因素为光栅尺的热变形。
投稿箱:
如果您有机床行业、企业相关新闻稿件发表,或进行资讯合作,欢迎联系本网编辑部, 邮箱:skjcsc@vip.sina.com
如果您有机床行业、企业相关新闻稿件发表,或进行资讯合作,欢迎联系本网编辑部, 邮箱:skjcsc@vip.sina.com
更多相关信息