轴承前盖、后挡智能测量选配系统的研制
2019-11-12 来源:神华铁路货车运输责任公司包头车辆维修等 作者:秦春林 孙宝民 尹建锋
轮轴是铁路车辆中的重要互换部件之一,其技术状态直接影响铁路车辆的运行安全和速度。轴承、轴承附件与轮对的选配压装,其技术状态直接影响车辆的运行安全。轴承与轮对轴径的选配压装一直被作为保障安全的关键指标,所以历来受到重视,轴承选配压装的各种自动化设备发展比较快,目前已比较齐全,自动化程度高。但是轴承附件一直以来都没有得到足够的重视,然而轴承附件的选配压装也至关重要,后挡选配不合适,压装产生裂纹、断裂同样影响铁路车辆的运行安全,但是目前还没有一套自动系统能够完成轴承附件检修的所有工序,以及选配工作。
本文阐述研制一套系统完成轴承前盖和后挡的检修选配工作,根据《铁路货车轮轴组装检修及管理规则》(铁总运[2016]191 号)及其相关文件规定的检修项目及选配原则,设计轴承前盖、后挡智能测量选配系统。该系统可对货车 60 t,70 t 轴承前盖、后挡,进行自动清洗、烘干、测量、智能分类并按规格公差存放(不合格品直接放入废料箱) 和计算机自动化管理的智能系统。
1、预期目标
(1)设计完成一套适用于铁路货车轮轴检修的轴承前盖、后挡输送、清洗、烘干、测量、选配、存放系统,实现对轴承前盖、后挡检修的流水线作业。
(2)清洗、烘干、测量装置技术满足工艺要求,均达到行业较高水平。
(3)系统作业节拍≥1.6 件/min。
(4)系统大修周期达到 5 a,系统整体使用寿命≥10 a。
(5)轴承前盖、后挡清洗、烘干、智能测量选配系统的设备日常检查标准和设备检修标准。
2、系统工艺过程及布局(图 1)
3、系统主要组成及主要参数
(1)系统的主要组成。输送线、清洗室、烘干室前、后挡测量机、盖测量机、上下料机械手、机器人智能选配及存储、存储库、工控机、电控柜、气路系统和工作软件。
(2) 系统主要技术参数。系统总功率:<75 k W;电源:AC380 V/220 V±10%,50 Hz,三相五线制,保护接地;气源种类:
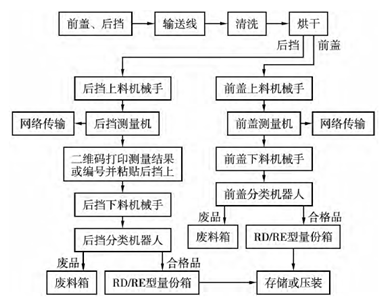
图 1 工艺流程
压缩空气(经过净化);气源压力(0.35~0.7)MPa;工作压力 0.4MPa;生产能力:一班(7 h)检修 60 辆车的前盖、后挡;生产形式:双工位;系统作业节拍≥1.6 件/min,系统运行方式:连续/
间歇;系统运行控制方式:手动/自动;系统运行速度:可调。
主要部件的组成和主要技术参数
4.1 输送线
(1)主要组成。减速机驱动装置总成、头部传动总成、链条总成、尾部张紧装置总成、结构钢支撑架总成、网状托物架、电器控制总成和安全保护装置等几大部件构成。
(2)输送线的主要技术参数。
①输送线形式:传送带(不锈钢网链)结构;立体循环形式;
②驱动形式:电机驱动;
③调速方式:变频调速(无极调速);
④运行方式:连续和间歇式(可切换);通过式流水作业;
⑤运行速度:(0.1~6)m/min(可调);
⑥传送带承载能力:≤250 kg/m2;
⑦输送线长 10 000 mm、宽(500~550)mm、高700 mm;
⑧工作温度:(-20~60)℃;
⑨工作噪声:≤50 d B。
(3)输送线功能。该输送线承担轴承前盖、后挡进行清洗、烘干、测量作业工序的衔接和输送物料的功能,输送线根据轴承前盖、后挡外形尺寸结构设计为双排双工位(一排放置前盖、一排放置后挡),输送线材料选用不锈钢,设计高度符合现场人工作业易上料操作,输送线长度根据现场位置、工作节拍及作业量进行设计,传输速度及存放工位数量根据清洗、烘干及测量节拍合理配置,输送速度范围内可调,输送线设计结构合理、故障率低,易于后期保养和维修。
(4)工艺过程。人工上料时采用连续模式,当清洗机前的所有工位放满后,输送线自动进入间歇模式,此时系统开始进入清洗、烘干、测量等工作状态;当最后一组工件被运至测量机工位时,输送线重新转入连续模式,如若有人工上料,则输送线继续运行,否则输送线停止工作。
4.2 清洗、烘干机
轴承前盖和后挡清洗、烘干机是按照铁总运[2016]191 号文件规定的清洗、烘干标准,对货车轴承前盖和后挡进行自动清洗、烘干的智能系统。该系统可用于清洗工件表面的铁屑、油污、废尘等;吹干后工件表面无滴油、磕碰伤等现象。
清洗效率高,清洗后配件表面无残留污渍,效果符合现场检修要求,清洗机整体材料采用不锈钢,设计污水槽、清水槽、过滤装置及高压水泵装置,结构设计合理,布局紧凑,换水作业方便。
烘干装置用于清洗完成后的烘干作业,烘干后配件彻底干燥,符合现场测量要求。清洗、烘干装置的工艺节拍与测量机构配合设计,保证流水线作业流畅。
(1)主要组成。该设备有 2 个喷淋清洗室、1 个风干室、1 个热风烘干室,共 4 个工位。
(2)主要性能
①设备用途:满足轴承前盖、后档清洗和烘干的要求;
②适应范围:新造、检修 60 t,70 t 货车轴承前盖和后挡;
③清洗方式:前盖、后挡成套,工件同时进行高压喷淋清洗;
④清洗效果:用于清洗工件表面的铁屑、油污和废尘等;
⑤烘干方式:循环热风加常温压缩空气风刀;
⑥吹干效果:吹干后工件表面无滴油、磕碰伤等现象;
⑦工艺流程:人工上料→在线输送→喷淋粗清洗→喷淋精清洗→风泵吹干→热风烘干→过渡→风泵吹匀、降温→测量工位。
(3)设备技术参数。清洗工件:前盖、后档;清洗能力(产量):日工作量满足 49 台车;生产节拍:≥1.6 件/min;零件通过最大高度:250 mm;设备工作时间:7 h/d;
清洗液:水剂、清洗剂、防锈剂;作业方式:流水线作业,通过式,风源压强(0.4~0.6)MPa;工作噪声≤50 d B;污染环境:无;工作速度 0.5 m/min;线速度(0.1~5)m/min 可调(变频调速);喷淋段水压(0.5~6)MPa,流量 10 m3/h,电机功率 4 k W;加热功率 45 k W/380 V(交流);设备总功率:约 65 k W;加热功率:45 k W/380 V(交流);总重量:约 3 t;电源电压 AC380 V/220 V±10%,50 Hz,三相五线制,保护接地;控制方式:手动和自动可切换;指示方式:温度指示,喷淋槽温度显示;过载保护:电机、泵、风机过载;温度异常;急停保护。液位报警:液位控制欠
液报警指示。
4、前盖测量机
(1)主要组成部分。机架总成、测量部及定位机构、上料机构、下料机构、气路系统、电控部、工控机、故障诊断系统和工作软件。
(2)各部分功能介绍。机架总成:测量部基础、设备的基础与框架;定位机构及测量部:对前盖进行定位并对轴颈配合面直径和台阶高度进行测量;上料机构:将前盖从输送线上,运至测量位置,完成前盖的自动上料;下料机构:对测量完成的前盖下料;工控机:完成测量全过程的控制及测量数据的处理、贮存、打印输出;电、气控制部:设备电源、电气控制;气源及气动控制;气路系统:支持测量部动作;故障自诊断系统:在系统运行过程中,进行监控,出现故障时,报警,自动停机。
(3)主要性能。主要功能:实现自动上、下料及前盖尺寸的自动检测,判定是否合格;
测量项目:轴颈配合面直径,轴颈配合面台阶高度;适应范围:新造、检修货车 60 t,70 t 轴承前盖;测量机采用开放式数据库:系统采用 Windows2000 以上版本(以方便和其他子系统联网和数据共享);测量具体位置及标准:测量的具体位置和标准按相关规定执行;附属配置:测量装置配备有自动上、下料装置,能够自动完成测量机的上、下料工作,实现设备生产的自动化。
(4)主要技术参数。节拍时间<1 min(上、下料、测量);电源AC 380 V/220 V±10%,50 Hz,三相五线制,保护接地;额定电流 2 A/AC 380 V,3 A/AC 220 V;功率消耗<2 k W;气源种类:压缩空气(经过净化);气源压力(0.35~0.7)MPa;工作压力 0.35MPa;测量精度:检测重复精度 0.01 mm;测量精度±0.01 mm;分辨率 0.001 mm;测量方式:相对测量原理接触式测量方式。
(5)系统工作原理。系统基本工作原理如图 2 所示,测量工艺过程:输送线输送前盖至测量机上料工位→上料机械手把前盖抓放至测量位→各测量单元进入测量位→各测量单元进行测量取值→测量结束各测量单元复位→保存测量数据并分析测量结果→下料机械手下料。
(6)参数的测量方法。本测量系统采用的是相对测量原理,采用接触式测量方式。全部测量及动作过程均由计算机自动控制,自动完成。
4.4 后挡测量机
该系统可提高轴承后挡检测的精度、选配可靠性、稳定性及可追溯性;配合铁路车辆计算机网络化管理系统,为保障铁路车辆的运行安全,提供了快捷、准确、可靠的手段;可与HMIS 联网,并可与上下位机联网与数据共享。
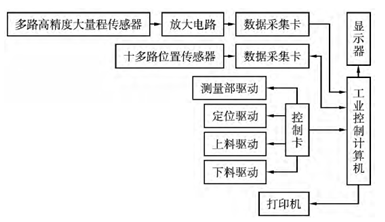
图 2 系统基本工作原理
(1)主要组成部分。机架总成、测量部 1、定位机构及测量部2、上料机构、下料机构、气路系统、电控部、工控机、故障诊断系统和工作软件。
(2)各部分功能介绍。机架总成:测量部基础、设备的基础与框架;测量部 1:对密封座配合面及台阶高度等部分进行测量;定位机构及测量部 2:对后挡进行定位并对防尘板座配合面直径进行测量;上料机构:将后挡从输送线上,运至测量位置,完成后挡的自动上料;下料机构:对测量完成的后挡下料;工控机:完成测量全过程的控制及测量数据的处理、贮存、打印输出。电、气控制部:设备电源、电气控制;气源及气动控制;气路系统:支持测量部动作;故障自诊断系统:在系统运行过程中,进行监控,出现故障时,报警,自动停机;
(3)主要性能。主要功能:实现自动上、下料及后挡尺寸的检测,判定是否合格;测量项目:防尘板座配合面直径,密封座配合面直径,端面高度、槽深度,后挡翘曲度;适应范围:新造、检修货车 60 t,70 t 轴承后挡;测量机采用开放式数据库:系统采用Windows2000 以上版本 (以方便和其他子系统联网和数据共享);测量具体位置及标准:测量的具体位置和标准按相关规定执行;附属配:测量装置配备有自动上、下料装置,能够自动完成测量机的上、下料工作,实现设备生产的自动化;
(4)主要技术参数。节拍时间:<1 min(上、下料、测量);电源电压:AC 380 V/220 V±10%,50 Hz,三相五线制,保护接地;额定电流:2 A/AC 380 V,3 A/AC 220 V;功率消耗<2 k W;气源种类:压缩空气(经过净化);气源压力(0.35~0.7)MPa;工作压力 0.35 MPa;测量精度:检测重复精度 0.01 mm;测量精度±0.01 mm;分辨率:0.001 mm;测量方式:相对测量原理接触式测量方式。
(5)系统工作原理。系统基本工作原理如图 3 所示,测量工艺过程:输送线输送后挡至测量机上料工位→上料机械手把后挡抓取放至测量位→定位机构对后挡进行夹紧定位→测量装部1 下降到位→测量部 1,2 各测量单元同时对后挡测量取值→测量结束各测量单元复位→保存测量数据并分析测量结果→下料机构下料。
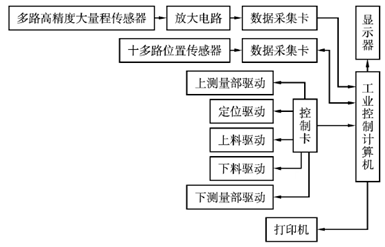
图 3 系统基本工作原理
(6)参数的测量方法。本测量系统采用的是相对测量原理,采用接触式测量。全部测量及动作过程均由计算机自动控制,自动完成。
4.5 机器人智能分类存储系统
分类存储系统用于轴承前盖、后挡的智能分类,免去人工选配工作,为后续轴承压装工位服务。轴承前盖、后挡尺寸经测量机检测完成后,测量机自动判别合格与否并判定品种和降级规格,由机器人接受测量机传输的前盖、后档数据进行分类,不合格品放置于不合格品区域,同时对合格的后挡要实现按公差带范围和类别分别存放在各自的运料小车上,10 个为一份,每辆小车可存放 8 份,计 80 件工件。测量机测量结果并与现有HMIS 系统资源共享、与现有轴承压装机实现轴承前盖、后挡的智能分类功能。
(1)机器人主要功能。对测量机传输来的前盖、后挡数据进行分析和执行,根据前、后挡选配原则进行分类存放,实现从检测工位拿取工件、旋转、移动将合格品放置在指定的位置。
(2)机器人技术参数。轴数:3 轴;重复定位进度±0.1 mm;腕部连接法兰:ISO 9409-1-A100;抓取重量 8 kg;防护等级:IP65/IP67;运动范围 1300 mm(最大前后跨度);电源频率(50~60)Hz(±2 Hz);电器容量 12 k V·A;工作环境温度(+5~+45)℃;环境温升要求 1.5 ℃/min。
(3)完成一个工件单个循环节拍 20.5 s。
(4)机器人自动化分类方案。设备通信:工件检测机跟机器人交互作业时,工件检测机提供呼叫、完成两组信号;工件检测机检测完毕呼叫机器人抓取零件,以及机器人抓取完成退到安全区后给工件检测机完成信号;工件类型、选配相关数据由检测机判断比较完成,机器人只接收,分类好的产品编码。例如:当前检测一个零件,检测完成后,检测机告诉机器人,这个零件是前盖或后挡的原型或降几级。
5、结束语
该系统可提高轴承前盖、后挡检测的精度、选配可靠性、稳定性及可追溯性并且提高劳动生产率、降低工人劳动强度、改善了作业环境;配合铁路车辆计算机网络化管理系统,为保障铁路车辆的运行安全,提供了快捷、准确、可靠的手段;可与 HMIS(Hmanagement Information System,铁路货车技术管理信息系统)联网,并可与上下位机联网与数据共享。
该系统在铁路车辆检修中具有创新性。测量使用先进、成熟的测量技术;选配和存放使用工业智能机器人,效率高、稳定可靠。配合铁路系统的网络化管理、减员增效保障铁路车辆的安全运行具有重要的现实意义。
投稿箱:
如果您有机床行业、企业相关新闻稿件发表,或进行资讯合作,欢迎联系本网编辑部, 邮箱:skjcsc@vip.sina.com
如果您有机床行业、企业相关新闻稿件发表,或进行资讯合作,欢迎联系本网编辑部, 邮箱:skjcsc@vip.sina.com
更多相关信息