民机粱类典型零件的高效加工
2016-8-10 来源:沈阳飞机工业(集团)有限公司 作者:苏艳 孙树强
摘要:文章介绍了在航空工业中高速切削的大量应用,当前以高速加工技术为代表新的加工工艺已经显示很多的优点和强大的生命力,成为航空制造技术提高加工效率和质量、降低成本的主要途径。高速加工不但可以成倍地提高生产效率,还可进一步改善零件的加工精度和表面质量,解决一些常规加工中难以解决的某些特殊材料的高效加工问题。以具体实例出发从机床、刀具、材料、数控编程、仿真检查等方面对高速加工的关键技术进行了阐述。
关键词:高速加工;变形控制;仿真检查;高效加工
由于现代飞机高性能的要求,其结构具有轻量化、薄壁化和整体化的特点,并且为满足飞机装配以骨架零件为定位基准的要求,零件须实现精确加工,做到具有较高的精度和表面质量。肋零件是飞机上非常重要的结构件和受力件。肋零件由于其特殊的零件结构及所使用的材料等原因,在加工中易产生较大变形,特别是需两面加工的肋零件,数控精加工到位是非常困难的,高速加工则为肋零件的数控精加工提供了保证。
1、高速切削技术的概述
高速切削机床是高速切削发展的首要条件。其主轴要求有很高的转速、进给速度和加速度,机床结构应有很高的静、动刚度和优良的力学性能。由于高速切削加工时存在离心力和振动的影响,对刀具的几何精度、装夹重复定位精度、刚度和高速动平衡的安全可靠性有较高要求。目前应用较多的是HSK 高速刀柄和热胀冷缩紧固式刀柄。合适的CAM 编程软件在高速切削中也是至关重要的。
高速切削的优点有:(1)随切削速度提高,材料切除效率增加,大幅度提高加工效率,降低加工成本。(2)切削力减少,平均切削力可下降30%。这对降低高转速主轴的功耗有明显影响,并有利于低刚性和薄壁零件的加工。(3)高速切削采用小切深,大进给,使加工表面质量明显提高。(4)高速切削90%以上切削热随切屑排出,加工工件的温升小,有利于降低工件的热变形和减小加工的残留内应力。(5)从切削动力学分析,机床转速提高,使切削系统的工作频率远高于机床的低阶固有频率,这有利于降低加工表面粗糙度。(6)高速切削时,一般不使用切削液,有利于环境保护。
2、零件分析
为了更加合理有效地控制加工方案的全过程,在零件工艺准备进行之前必须进行周密严谨的零件分析,找到影响零件加工的关键环节及难点所在。
2.1 零件典型结构特征
(1)双面肋零件。(2)零件一边宽(最宽216mm)一边窄(最窄127mm),容易产生侧弯。(3)变角度外形(最大106.352°),一面外形为开角,另一面为闭角,且角度变化大。4)图纸要求零件直边外形平面度0.2mm。(5)该零件为关键件。
2.2 材料分析
零件材料为铝合金挤压型材,材料牌号:7B04 T6。该合金属于高强度铝合金,与其他结构铝合金相比具有最高的强度性能。在静载荷下,T6 状态的合金对应力集中(孔)的敏感性较低,在小半径弯曲或偏心拉伸条件下,截面过渡部位合金的静强度下降。在厚度不大于75mm 情况下,力学性能:бb=510~590MPa;бp0.2=450~530MPa。
2.3 新工艺方案的分析与论证
零件整个加工过程中,合理的工艺流程设计是十分重要的一个环节。工艺流程设计主要从零件分析、加工过程分析、工装(包括刀具和量具)分析入手。高速切削加工对切削刀具、切削用量、工艺方案、数控编程等方面提出了新的要求。新工艺方案的制定要充分体现数控高速加工的优越性,最终要实现的目标主要有:(1) 控制变形;(2)申请专用工装铣夹;(3)数控加工一次到位;(4)选择非对称编程加工零件;(5)数控加工程序优化设计,运行时到达无人干预状态;(6)提高零件加工效率。
2.3.1 机床选择
选用Y2K811 高速铣。机床Y2K811 参数:双主轴头,双控制机;控制系统:FIDIA C20;主轴最高转速:28000r/min ;工作台尺寸:10000mm ×2200mm;A/C 角,A:+95/-110,C: ±200; 主轴功率:42kw/h。
2.3.2 工艺装备的选择
第一面夹具选用真空平台。真空吸附的同时,在周围适当加压压板,以增强夹紧力。
真空吸附装夹优点有:(1)零件放置平稳,装夹后零件受力均匀。(2)方便零件找正。(3)真空吸附,有利于公差较小的薄壁腹板的尺寸保证。(4)装卸迅速方便,可缩短辅助时间。(5)加工方便,零件加工区无障碍物限制加工过程。
第二面选用专用工装进行装夹定位零件。
专用工装装夹优点有:(1)专用工装确定压板位置和数量,规范加工步骤,提高零件加工效率。(2)减少零件数控加工为躲避压板的空行程走刀。
2.3.3 刀具的选择与参数确定
刀具是高速切削加工中最活跃的重要因素之一,在高速加工过程中要承受高温、高压、摩擦、冲击和振动等载荷,因此其硬度和耐磨性、强度和韧性、耐热性、工艺性能和经济性等基本性能是实现高速加工的关键。本例选择适合K811 数控机床的高速铣刀。
刀具参数确定原则:(1)力与扭矩必须尽可能小;(2)小切深ap,中等进给fz;(3)分层切削,高的进给速度vf;(4)高的加工比例时间,少的非加工比例时间。
经过上述综合分析对比确定刀具参数如表1。
表1 加工用刀具参数
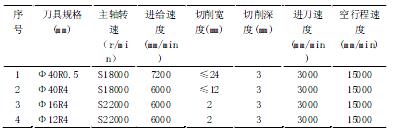
2.3.4 工艺流程设计
分析可看出,控制变形是加工此零件的难点,工艺流程设计应将变形量控制到最低。
2.3.4.1 定位基准和程序坐标原点的选择
零件第一面加工定位基准为真空平台面;数控程序原点选择为毛料相邻两直角边和毛料底面建立数控程序原点坐标系。
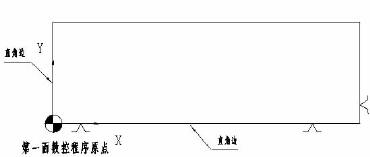
图1 零件第一面定位孔示意图
零件第二面加工定位基准选择“二孔一面”。“二孔”零件两个Φ12H12 基准孔,“一面”零件底面。数控程序原点选择:以基准孔2的中心和两基准孔中心拉直线建立数控程序原点坐标系。
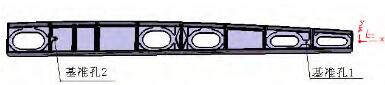
图2 第二面定位孔示意图
2.3.4.2 工艺流程的主线
粗铣———校正———时效———半精铣———校正———时效———精铣。
在粗加工、半精加工、精加工后一定要安排校正工序,同时必须要给予充分的自然时效,这两个环节必不可少,目的是消除其内部大部分的残余应力,以利于后续加工。
2.3.4.3 加工中各环节的分析及加工过程中余量的分配
粗铣:粗铣直边缘条和筋条内外形,留2mm 余量。粗铣变角度缘条内外形,留3mm 余量。
粗加工环节,零件从毛坯状态过渡到初具雏形。此过程金属去除率大,并因所使用材料的加工性能,会产生很大的残余内应力,而残余内应力是引起零件变形的根本原因。在大量去除切削余量时,要不对称加工,以达到消除毛料内应力的作用。所以粗加工的编程方法很重要,合理的编程方法会减小零件的变形量。
半精铣:内、外形均留1mm 余量,腹板到位。
安排半精铣工序,一是因为零件材料是铝合金挤压型材,加工性能亚于板材;二是因为半精铣中逐渐去除余量会逐渐减小零件的残余内应力,对控制变形十分有利是非常有好处的。半精铣后留1mm 余量,主要是考虑到零件结构一头宽一头窄,加工时容易产生侧弯,校正很难消除零件侧弯变形,需给精加工留有足够的余量。精铣:缘条、筋条厚度到位。
精铣金属去除率较低,主要任务就是保证零件外缘及壁厚。
2.4 数控程序的编制
前文提过高速铣削加工对数控编程系统的要求越来越高,这里采用CATIA 软件,此软件容量大、处理能力强。
高速切削编程首先要注意加工方法的安全性和有效性,其次,要尽一切可能保证刀具轨迹光滑平稳,这会直接影响加工质量和机床主轴等零件的寿命,最后,要尽量使刀具载荷均匀,这会直接影响刀具的寿命,为此采用了如下措施:
(1)采用顺铣方式进行分层铣削;
(2)路径规划,以及粗加工、半精加工、精加工的编程策略;
(3)避免刀具轨迹走刀方向的突然变化,保持刀具轨迹平稳,避免突然加速或减速;
(4)下刀或行间过度部分采用斜式下刀或圆弧下刀,避免垂直下刀直接接近工件材料;
(5)刀具轨迹编辑优化,避免多余空刀;
(6)粗加工不是简单的去除材料,要注意保证本工序和后续工序加工余量均匀;
(7)在切削量大的地方,比如转角前后,降低走刀速度,使加工平稳,单位时间内的切削量保持恒定(K811 数控机床本身具备转角降速功能,这里无须设置。);
(8)尽可能减少程序块,提高程序处理速度;
(9)程序分层、进给速度、切削宽度、切削深度均严格按照刀具参数设定,另外为了避免转角余量过大、余量不均匀特意增加半精铣清转角程序,并将小刀修腹板残留放在精铣内形后面,防止产生干涉;
(10)程序开头:①粗加工,加指令G302;②精加工,加指令G301或G304。
3、结论
高速加工技术是世界范围内倍受关注的前沿技术,它将极大地促进加工效率的提高和产品品质的改善。目前数控加工厂高速加工技术主要用在壁板类零件的加工上,而型材、模锻件和铸件零件的高速加工技术还在探索之中。文章为粱类零件的高效加工增加了宝贵经验。
参考文献
[1] 何永利.铝合金高速切削表面粗糙度的实验研究[J]. 机械设计与制造,2006(1).
[2] 贾秀杰.铝合金高速铣削过程切屑成形机制研究[J].轻合金加工技术,2009(7).
[3] 艾兴. 高速切削加工技术[M].北京:国防工业出版社,2003,10.
[4] 王先逵.机械制造工艺学[M].北京:机械工业出版社,2013,6.
投稿箱:
如果您有机床行业、企业相关新闻稿件发表,或进行资讯合作,欢迎联系本网编辑部, 邮箱:skjcsc@vip.sina.com
如果您有机床行业、企业相关新闻稿件发表,或进行资讯合作,欢迎联系本网编辑部, 邮箱:skjcsc@vip.sina.com
更多相关信息