基于 KUKA 弧焊机器人的盾构机关键部件焊接工作站
2017-12-6 来源: 中国铁建 北京石油化工 库卡机器人 作者:孙章龙 黄继强 杨列峰 薛龙 黄军芬 等
摘要:针对盾构机关键零部件的焊接特点,基于 KUKA 弧焊机器人研制了自动化焊接工作站。利用焊接机器人接触寻位、多层多道焊和电弧跟踪等功能实现盾构机联体刀座工件的自动焊接。焊接实验结果表明,所研制的盾构机关键零部件焊接工作站能够满足离散制造企业的零部件小批量自动化焊接生产。
关键词:盾构机;弧焊机器人;电弧传感跟踪;接触寻位;多层多道焊
0 前言
盾构机刀盘是盾构机的核心部件,因其工作环境恶劣,受力情况复杂,对其设计和制造加工过程有较高的要求[1]。刀箱、刀座是刀盘上安装滚刀的关键部件,一般采用厚板拼接组焊而成,焊接工序是其加工的关键工序,焊接工作量大,但因为盾构机为非标定制产品,难以形成流水式生产作业模式。国内盾构机制造厂家在处理此类产品时还是采用手工生产作业,焊工劳动强度大,焊接质量一致性差,同时伴随着熟练焊工数量逐年减少,给盾构机厂家提出了较大的挑战。
本研究以 KUKA 弧焊机器人为基础,开发盾构机刀箱、刀座焊接工作站,以期探索盾构机等类似行业部件制造新模式,推进离散制造企业自动化、智能化水平的提升。
1、 焊接工作站系统构成
刀箱、刀座多为箱形部件,由厚板拼接而成,采用熔化极气体保护焊方法,需要进行多层多道焊接,同时为了减小变形,尽可能对称焊接[2-3],工件在焊接加工过程中需要反复变换空间位置。
根据刀箱、刀座焊接加工特点和要求,焊接工作站采用六轴关节机器人配合移动导轨和旋转变位机组合协同方案。机器人采用 KUKA 5 arc 型六轴弧焊机器人,其最大臂展 1.41 m①,不能直接用于较大部件的焊接,通过搭载移动导轨扩大机器人焊接工作范围,以适应不同大小工件的自动化焊接;旋转变位机夹持待焊工件,并可带动工件 0~360°旋转,为机器人焊接创造合适的空间位置。六轴机器人、移动导轨和旋转变位机的各驱动轴可以协同联动,方便弧焊机器人统一编程、协同作业。
刀箱、刀座焊接工作站布置如图 1 所示。
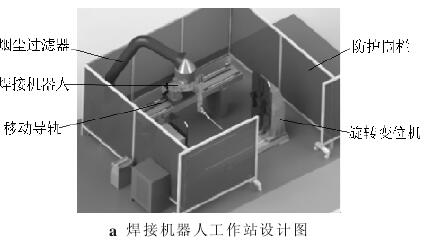
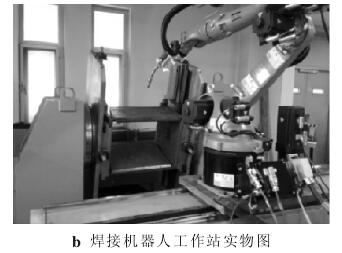
图 1 焊接机器人工作站
2、 焊接关键技术
2.1 焊接工序
以联体刀座焊接为例,因涉及厚板焊接,在考虑对称施焊的同时,需要将厚板多层多道焊接技术、机器人离线编程技术等技术相结合完成工件施焊。如图 2所示,借助离线编程技术,焊接机器人先行完成 1~12 打底焊缝及 26/27/30/31/34/ 35/38/39/42/43/46/47 角焊缝第一道。完成后,利用旋转变位机搭载工件旋转 180°后,再借助离线编程技术和多层多道焊接技术按照顺序完成 13~24 焊缝以及 25/28/29/32/33/37/40/41/44/45/48 角焊缝的焊接。
然后,变位机再反向旋转 180°,工件位置恢复到初始位置,机器人再按顺序焊完 1~12 焊缝及 26/27/30/31/34/35/38/39/42/43/46/47 角焊缝剩下的焊道,从而减小刀座焊接施工中产生的变形量和焊接应力。
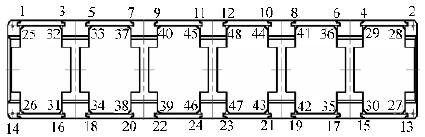
图 2 联体刀座的焊接顺序
2.2 接触寻位
盾构机刀座等部件由多个零件拼装而成,因拼装误差等原因,每个部件的焊道可能会存在差异,不能直接调用已编好的程序进行焊接,在焊接前需要通过接触寻位来获得当前焊缝的信息,以实现自动焊接。
焊接机器人的接触寻位通过机器人在焊丝上叠加一个 24 V 信号,当焊丝接触到工件,则通过焊丝形成电流回路,通过传感器发送回机器人,机器人记录下焊丝与工件接触时所处点的位置。
重复动作使机器人在一个平面上获取三点(不在同一条直线上),就能获得工件平面的坐标位置,同样利用接触寻位的传感方式,可获得待焊坡口位置、方向和起始点,方便机器人自动搜寻焊缝位置并进行自动焊接。
2.3 多层多道焊
盾构机的许多零部件均是由厚板拼接而成,由于材质和焊接质量等要求,不能采用效率较高的埋弧焊,通常采用熔化极气体保护焊,在单个焊缝实施多层多道焊接。
手工进行多层多道焊接时,需要基于焊工的经验规划焊道并保持合适的焊枪位姿。机器人进行多层多道焊时,关键也是要保证合理的焊道规划和合适的焊枪位姿。
本研究基于KUKA弧焊机器人提供的多层多道焊软件包 KUKA.Multi-Layer 工艺程序包,以根部焊道轨迹为基础,通过编程的偏移量计算出新的焊道轨迹,并根据坡口形式
优化焊接机器人的位姿。
基于 KUKA.Multi Layer 工艺程序包编写的一段自动完成两道焊缝焊接的程序如下。

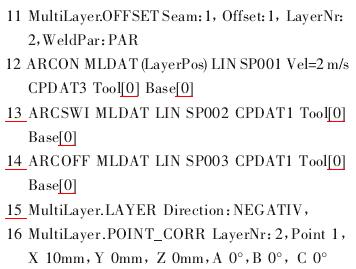
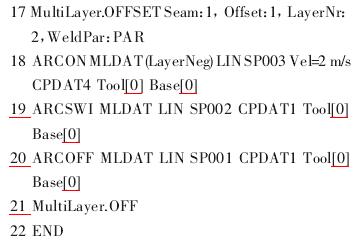
2.4 电弧传感跟踪
盾构机零部件在加工、装配过程中的尺寸误差,位置偏差以及工件加热变形等因素会造成接头位置偏离示教路径,有时需修正原有的轨迹。KUKA 提供的 Arc Sense 工艺程序包借助电弧传感提供焊缝高低和左右信息,修正原来示教轨迹以适应工件实际焊接需求。Arc Sense 通过焊接过程中电流变化获得实际焊接过程中电弧的变化记录,结合焊枪的摆动可以确定和纠正其与实际轨迹中心的偏差。电弧跟踪框图如图 3 所示
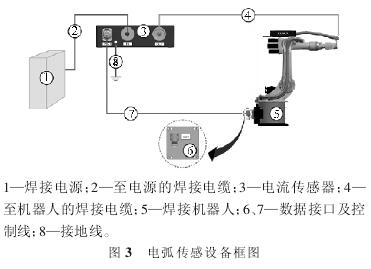
3 、焊接实验
采用研制的焊接工作站进行联体刀座的实际焊接,采用交替焊接顺序进行对称施焊,利用接触寻位技术初始定位,将电弧跟踪和多层多道自动焊技术相结合,完成一个五联体刀座的焊接,焊接完成的工件如图 4 所示。
实验证明,开发的焊接工作站系统能够满足相对复杂的工件多焊缝、多层多道对称施焊。同时配合不同的安装卡具,焊接工作站可以进行其他种类工件的自动化焊接,从而适应离散制造企业进行零部件小批量自动化焊接生产的需求。
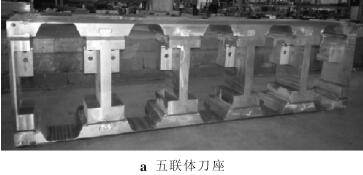
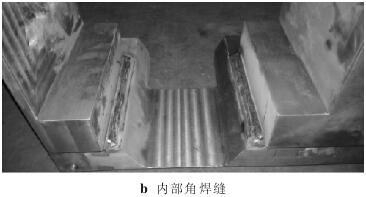
图 4 拼焊完成的联体刀座
4 、结论
(1)针对盾构机关键零部件的焊接特点,以KUKA弧焊机器人为核心,研制出盾构机零部件自动化焊接工作站。
(2)利用焊接机器人接触寻位、多层多道焊和电弧跟踪等功能实现盾构机联体刀座工件的自动焊接,验证了所研制的盾构机关键零部件焊接工作站能够满足离散制造企业的零部件小批量自动化焊接生产。
投稿箱:
如果您有机床行业、企业相关新闻稿件发表,或进行资讯合作,欢迎联系本网编辑部, 邮箱:skjcsc@vip.sina.com
如果您有机床行业、企业相关新闻稿件发表,或进行资讯合作,欢迎联系本网编辑部, 邮箱:skjcsc@vip.sina.com
更多相关信息