直线七轴工业机器人搬运系统在冲压生产线上的应用
2021-3-20 来源:东风汽车集团技术中心 作者:董锴
【摘要】随着我国汽车工业的高速发展,金属板材冲压自动化技术取得长足进步,尤其是工业机器人搬运系统在自动化冲压生产线上的广泛应用,为高柔性、高效率的冲压生产线提供了很好的解决方案。本文通过分析在某汽车公司冲压车间所采用的
机器人直线七轴技术,阐述了该技术的特点和优势。现代汽车工业具有生产规模化、车型批量小、品种变化快和多车型共线生产的特点,这些趋势要求冲压自动化技术不断向高柔性和高效率方向发展。串列式单机联线自动化冲压线是当前我国汽车厂冲压生产线采用的主流方案。采用机器人搬运系统的串列式单机联线自动化冲压生产线,具有低投入、高效率以及高柔性等优点,并且随着工业机器人技术不断发展,冲压机器人搬运系统的性能也在不断提高。
1. 在冲压自动化生产线上的运用
在采用机器人搬运系统的自动化冲压生产线上,机器人主要完成板料拆垛、各工序压力机之间的冲压工件传送、线尾工件输出等工作。通过PLC控制系统的协调,机器人与压力机之间,上下料机器人之间,机器人与输送设备之间具有准确可靠的运动协调关系,各机器人的功能布局如图1所示。
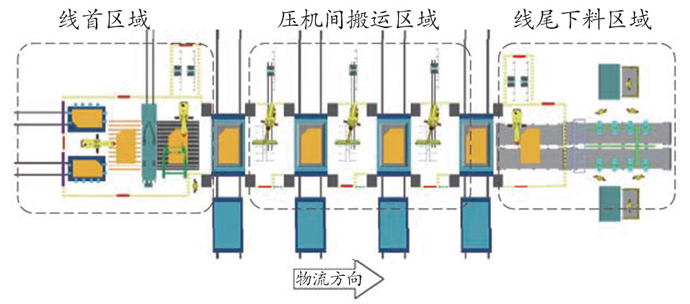
用于冲压生产线的工业机器人,从国内已经投产的自动化冲压生产线来看,大部分为标准六轴工业机器人,其优势在于采购成本较低,柔性化程度高,后期维护简便。但六轴工业机器人因为运动姿态的限制,冲压工件在从上一台压力机向下一台压力机传递过程中,冲压工件必须进行180°的水平旋转,导致机器人运动轨迹复杂,冲压工件在旋转过程中容易脱落等问题,这就限制了机器人的运行速度,进而限制了生产节拍的提高。冲压工件的水平旋转动作,需要较大的空间,尤其在搬运“车身侧围”等大型冲压件时,这个问题更加明显。这就导致前后工序压力机之间的间距较大,增加了生产线的占地面积,进而增加厂房基建投资。
机器人直线七轴技术正是为了克服标准六轴工业机器人的上述问题而开发,其基本原理就是在机器人第六轴的法兰盘上增加外部轴平移装置,该装置配置有独立的伺服电机和编码器,通过电缆接入机器人控制电柜内,由机器人的控制系统协调该直线七轴装置与机器人的其他六个轴的协调运作,如图2所示。
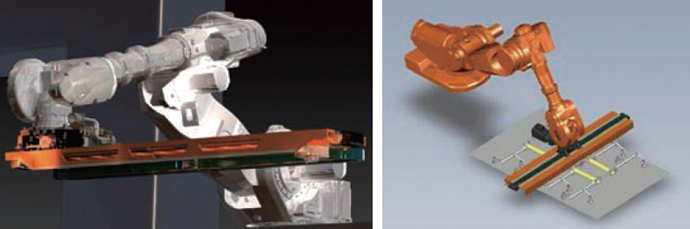
通过在机器人第六轴上加装直线七轴装置,实现工件在前后压力机之间的平行移动,大大简化了机器人的搬运轨迹,不仅可以提高生产效率,还可以节省空间,如图3所示。
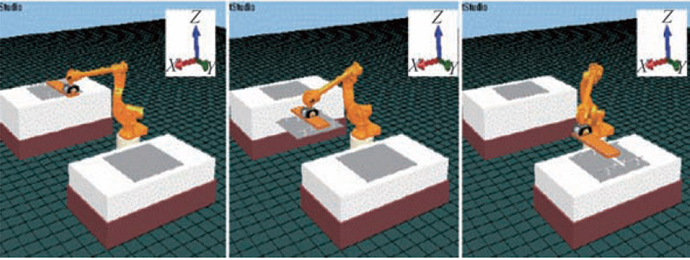
2. 冲压生产线规划时注意事项
笔者在多个冲压自动化生产线建设项目中采用了配置直线七轴技术的工业机器人搬运系统,积累了一些经验,规划期间的经验重点总结如下:①如何选择前后压力机之间的中心间距。②如果选择压力机滑块行程和模具开口度。③有效的防碰撞措施。
(1)前后压力机的中心距的选择。采用直线七轴技术的工业机器人对运行空间的要求不高, 当首台压力机吨位不小于2000t,压力机工作台前后宽度设定为2500mm时,前后压力机之间的最小间距可以设定为约5800mm,间距越小,对节拍的提升更好,但在实际规划时,还需要综合考虑以下三个因素。
如果生产线还需要配置“机器人自动更换未端执行器” 功能,当压力机中心距过小时,必然会导致前后压力机的立柱之间没有足够的空间,无法实现机器人原地转身到机器人底座后方来更换未端执行器,只能配置未端执行器移载小车,增加土建和设备投资,并降低设备的运行稳定性。
配置未端执行器移载小车,机器人底座也就不得不更换为门型底座,导致前一台压力机的左后立柱和后一台压力机的左前立柱,与机器人的底座距离很近,压力机立柱上的维修门将难于打开。
压力机中心距过小,压力机底座前后就没有足够的空间用于配置维修平台,给布置在压力机底座下的工作台夹紧顶起油缸的维修带来困难,降低压力机日后维修的方便性。
(2)压力机滑块行程和模具开口度的的选择。当生产线采用直线七轴技术,在进行压力机和模具设计时,滑块行程和模具开口度可以按照以下原则进行设定。
如图4所示,G=A+B+C+D式中, A 是零件厚度, 单位为m m; B 是下模安全距离, 取50mm;C是直线七轴装置+端拾器的厚度,取250mm;D是上模安全距离,取50mm。
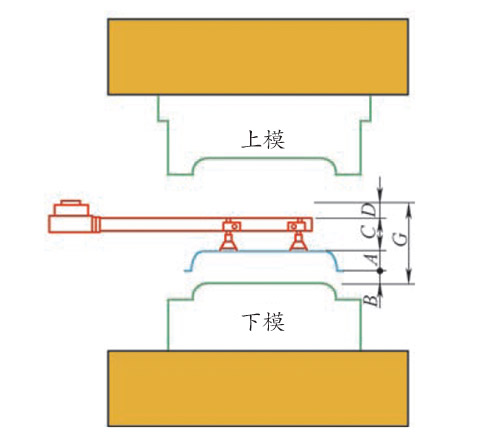
模具的有效开口高度必须要大于G,机器人才可以顺利的将冲压件从模具内送入或取出。当模具的有效开口高度小于G时,则需要对模具和冲压件进行具体分析,才能确认冲压件是否能在该冲压线上生产。
(3)有效的防碰撞措施。直线七轴工业机器人,在进行冲压生产过程中,直线七轴装置要伸入到模具型腔内进行上下料,所以在软硬件系统上必须采用以下有效措施来减少发生碰撞的风险。
在压力机控制系统中,设置合理的保护角度,并留出足够的滑块制动距离;当压力机滑块运行的行程次数发生变化时,自动取消“下料机器人的提前进入取料”和“压力机滑块提前下行”的优化动作;当下料机器人的速度设定低于100%时,自动取消“上料机器人的提前进入上料”的优化动作; 当上料机器人的速度设定低于100%时,自动取消“压力机滑块提前下行”的优化动作;当压力机滑块在上行过程中突然停止时,立即自动停止“下料机器人的运行”;当下料机器人在模腔内取料时,如因故障突然停止,应立即停止上料机器人的运行。并且故障排除后,必须手动将下料机器人移出模腔后,再启动生产循环。
全线自动换模时,第一个流程必须是全部机器人先回HOME位, 然后才允许压机工作台开动;必须是在压力机的换模流程全部完成后。由人工确认后,按下“生产线循环启动按钮”,才允许机器人运行到“等待下料位置”。
在压力机上增设一个检测滑块位置的绝对值编码器,并与压力机自身的滑块角度编码器信号进行实时对比,如果出现偏差,立即停止滑块和机器人的运行;在直线七轴装置的两端配置橡胶防撞块,当发生轻微碰撞时,保证七轴本体不会损坏。
3. 优点及问题总结
(1)工件在生产过程中始终保持平行移动,无须旋转。这有益于提高工件在上下工序压力机之间的传送速度,进而提高生产线的效率,尤其是在生产“车身侧围”等大型覆盖件时,优势更明显。
(2)工件在上下工序压力机之间传递时保持平行移动方式,可以使大型工件在较小的空间内传递,减小压力机之间的间距,进而减少整条冲压线在厂房内的占地面积,降低厂房建设成本。
(3)采用直线七轴技术的机器人搬运系统适应性强,柔性化高,小至轮罩,大至“车身整体侧围”等冲压件均可以全自动高效生产。
(4)配合大型机器人,直线七轴装置的有效负载能力强。例如配置直线七轴技术的机器人选用的是ABB IRB7600 325/3.1型机器人,直线七轴装置端部的负载能力可以达到90kg。减去未端执行器和未端执行器快换夹具的质量,还可以提供至少60kg的负载能力给冲压工件,这已经远远超过了一般轿车和SUV的整体侧围冲压件质量。
机器人直线七轴技术存在的局限性如下:基于承载能力的考虑,直线七轴装置的长度是有限制的,这就对前后压力机的最大中心距存在限制。一般情况下,前后压力机中轴线之间的间距不能大于8.5m。如果是老式手动冲压生产线改造,前后压力机中心距大于上述数值,将无法采用机器人直线七轴技术。此外,冲压生产过程中,直线七轴装置需要伸入到压力机模腔内,如果发生机器人与机器人、机器人与模具的碰撞,可能造成七轴装置的损坏,修复难度较大。
4. 结语
随着我国汽车市场竞争的不断加剧,汽车的制造成本和品质成为各汽车制造厂家角逐市场的先决条件,因此,采用机器人搬运系统进行冲压生产是降低汽车制造成本,提高车身制造品质的重要手段。机器人直线七轴技术更是充分发挥了冲压机器人搬运系统的优势,将高柔性、高效率,低投入的特点更推进了一步。
投稿箱:
如果您有机床行业、企业相关新闻稿件发表,或进行资讯合作,欢迎联系本网编辑部, 邮箱:skjcsc@vip.sina.com
如果您有机床行业、企业相关新闻稿件发表,或进行资讯合作,欢迎联系本网编辑部, 邮箱:skjcsc@vip.sina.com
更多相关信息