强国复兴有我|广州数控设备有限公司
2024-9-27 来源:机床协会 作者:-
【编者按】中华人民共和国成立75年来,随着中国工业化进程不断推进,机床工具工业随之发展壮大,总体水平快速提升,正向着机床工具工业强国的目标迈进。在庆祝新中国75周年华诞之际,中国机床工具工业协会策划组织以“强国复兴有我”为题的主题宣传活动,集中报道机床工具行业及企业取得的成果及未来高质量发展目标规划。
一、企业概况
广州数控设备有限公司(简称广州数控)成立于1991年,是国家级智能数控系统、工业机器人产业链双链主企业,是中国机床工具工业协会第八届/第九届理事会轮值理事长单位,中国机器人产业联盟副理事长单位。拥有员工1800余人,其中研发与技术800人。主营业务包括:数控系统和伺服驱动及电机、工业机器人、全电动注塑机、数控机床营销。
广州数控拥有国家认定企业技术中心、博士后科研工作站等研发中心,是国家科技重大专项“高档数控机床与装备制造”、国家“863”科技计划承担企业,首批高新技术企业,并与哈尔滨工业大学、上海交通大学、南开大学、天津大学、华南理工大学、广东工业大学等高等院校成立了联合研究中心(实验室)。
广州数控的前身是荔湾区工业公司属下的小型集体所有制企业——广州华南电子仪器厂,在1991年正式登记成立广州数控设备厂。历经33年的锐意进取和诚信经营,广州数控已发展成为集科、教、工、贸于一体的国家高新技术企业,作为国内专业技术成熟的成套智能装备解决方案提供商,被誉为中国南方数控产业基地。1991-2000年期间,广州数控自主研发出第一套GSK928车床数控系统,研发生产的DA98交流伺服装置迫使国外同类产品降价50%。2000年广州数控正式转制为民营股份制,迈入发展新阶段。在此过程中,广州数控坚持创新,先后启动工业机器人和全电动注塑机的研发,成立博士后科研工作站和院士工作站,荣获广东省装备制造业重点企业和广东省创新型企业等称号。在2003年数控系统产销量突破一万套,并正式更名为“广州数控设备有限公司”。
2011年,广州数控被认定为国家企业技术中心,先后被授予第五批国家创新型试点企业、成为中国机器人联盟副理事长单位、获评国家技术创新示范企业,并在2014年筹建第二园区高精密部件加工园。依托全公司上下一心的坚持创新,2016年至今,公司先后荣获国家科学技术进步奖、制造业单项冠军企业(机床数控系统)等荣誉,公司领导何敏佳董事长成为中国机床工具工业协会理事会轮值理事长等。
党的二十大以来,广州数控响应国家号召,紧跟政策潮流,稳步前进,深入推进数控系统智能化转型升级,发展新质生产力,加强核心关键技术的高端突破,研究投产一批标志性产品。同时,广州数控实行了产学研用一体化创新机制,促进科技创新成果转化,产品结构优化调整,技术水平稳步提高,取得了一系列领先成果。自2018年广州数控实现第100万套数控系统线下交付,广州数控以每年近10万套标准型及高档数控系统配套,支持国内大批机床制造企业的健康运行。
近年来,广州数控深耕制造,尊重培养了大批一线工匠,为发展新质生产力、提高自主创新、可持续发展提供了有力保障。机床制造基础和共性技术研究不断加强,产品开发与技术研究同步推进。机床产品的可靠性设计与性能试验技术、多轴联动加工技术等多项关键技术的成熟度大幅提升。数字化设计技术研究成果在高精度数控产品设计上进行实际应用;多误差实时动态综合补偿和嵌入式数控系统误差补偿等软硬件系统在多个企业、多个产品上进行了示范应用,使数控机床精度得以明显提升。
同时,广州数控作为数控系统先进企业,致力于与数控机床和基础制造装备的主机、数控系统和功能部件等产业链关联企业组建长期稳定的战略合作伙伴关系,建立数控系统、功能部件与机床企业长期的配套关系,打造完整机床配套产业链,共建国内机床产业“内循环”生态体系,满足国家战略新需求。
“打造百年企业,铸造金质品牌”是广数人的共同愿景。未来,广数人仍将勇毅笃行,踔厉奋发,倡导勤奋努力的创业精神,勇于探索的创新精神,做深、做细、追求卓越的敬业精神,团结、互助、勤学、进取的员工精神,奉献诚信的团队精神,精工细作、精益求精,提供让用户满意的产品与服务,持续推进民族数控产业发展。
二、发展成果
广州数控经历了30余年的不断创新,加强人才队伍建设,不断培育与提升技术创新能力,实现了技术人才由少到多、技术成果由无到有、技术含量由低到高、技术管理由“开放式”到“体系化”、技术组织由“作坊式”到“专业型”的持续发展,拥有专利141项,主持或参与制定技术标准167项。
广州数控主营业务也增加到四类,数控系统和伺服驱动及电机、工业机器人、全电动注塑机、数控机床营销。其中,自主研制的机床数控系统(含伺服驱动器和伺服电机),可实现五轴联动加工、复合加工,在数控机床上批量配套应用,服务于航空航天、国防、模具、汽车制造等领域,具有年产机床数控系统20万套、伺服电机40万台的产能,累计配套数控机床达160万台。掌握核心技术的工业机器人,最大抓举500kg,面向搬运、焊接、码垛、装配、加工等应用领域,已累计推广应用近万台,助力汽车、家电、航空、机床、五金等行业的智能制造转型升级。
广州数控始终坚持自主创新,致力于打造国产高端装备,取得了卓越成绩。连续三次获得制造业单项冠军示范企业称号,并多次获得国家科学技术进步二等奖、中国机械工业科技进步类一等奖、技术发明类一等奖、科技进步类二等奖、自主创新十佳产品等众多荣誉。
三、典型案例
1. 搅拌摩擦焊解决方案
通过重大专项研发,形成搅拌摩擦焊解决方案,完成1台九轴五联动重载搅拌摩擦焊接装备,用于5米直径运载火箭贮箱箱底生产,实现在航天制造企业中的示范应用。填补 5m直径零件搅拌摩擦焊接国产加工装备的空白,单件焊缝长度为40m。焊接厚度8mm-9.5mm。
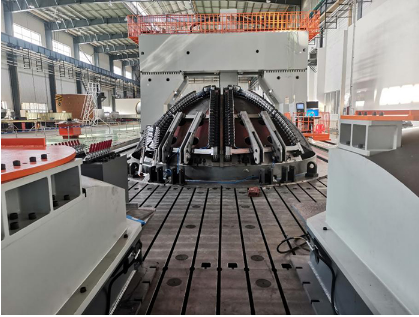
摩擦焊接加工
该机尺寸大,大龙门横梁跨度大,横梁上移动的重载主轴模组自重大,焊接加工施加到工件表面的压力大,机床结构件和工件都存在空间误差或搅拌摩擦焊接过程受力变形问题,需要研究其空间误差和进行误差补偿。
课题主要研究机床设计和制造引起的空间误差和搅拌摩擦焊过程主轴顶锻力变化引起主轴轴向(工件表面法线)变形导致加工尺寸位置变化两方面因素。其误差分析包括机床X、Y、Z轴三个方向上位置度误差,每个轴向有两个直线度误差和三个角度误差,以及X、Y、Z各轴间三个垂直度误差,对以上误差进行测量和补偿;另外对重载主轴顶锻力进行测量并对焊接轮廓尺寸影响进行分析研究,采用自适应PID法线偏移量控制,进一步提高加工尺寸精度,最终实现高精度焊接加工,满足工件尺寸要求和焊接表面质量要求。
本课题研制的GSK25i系统,技术成果适用于多种机型,支持车铣复合加工、5轴叶轮等加工应用,目前已在航空航天、汽车制造、能源动力、五金模具、3C等领域广泛应用,为各行业提供高效、精准的运动控制及工艺解决方案,参与多项国家科技重大专项,提高了重点领域数控系统的国产化率。
2. 航发叶片加工解决方案
通过重大专项课题的研发,已完成三大用户企业6种叶片的应用验证。经对比,使用本课题的数控系统,生产效率提升30%。加工质量达到图纸设计要求,叶片型面和进/排气边加工精度控制在图纸公差要求范围以内。
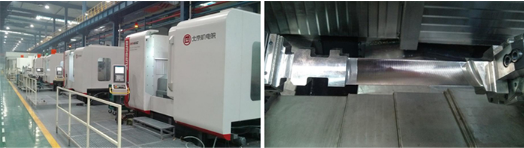
用户机床现场及叶片加工
本项目联合多家单位,形成由共性技术研究机构、国产装备与系统生产商、用户单位组成的联合研究团队,开发叶片高效精密加工工艺软件系统,与国产五轴联动叶片加工中心以及国产数控系统配套使用,实现多个型号航空发动机叶片的批量化生产,加工精度、效率和表面完整性等达到国际同类产品水平。系统形成了成熟、可靠的五轴联动机床配套相关技术。GSK25i系统已累计完成配套五轴联动机床50台以上,机床结构形式涵盖了双摆头结构、双转台结构及摆头转台等,也包括了旋转轴正交及非正交结构;应用范围包括叶片、闭式叶轮、涡轮增压器、三维搅拌摩擦焊、石油勘探钻头、曲轴油孔、刀具磨等多种应用场合。
完成了双B样条曲线刀具路径自适应进给技术的研究及开发工作,可针对五轴RTCP功能,采用双B样条进行综合光顺优化,消除由于进给速度方向突变引起的机床振动。针对综合光顺后路径的自适应进给速度规划,满足机床各轴的动态特性(加速度、跃度等)约束,提高了机床运动平稳性。已在GSK25i系统配套的北京机电院五轴叶片加工机床XKH800Z上,完成了应用验证,获得良好效果,满足用户要求。
(来源:广州数控 责编:黄韶娟)
投稿箱:
如果您有机床行业、企业相关新闻稿件发表,或进行资讯合作,欢迎联系本网编辑部, 邮箱:skjcsc@vip.sina.com
如果您有机床行业、企业相关新闻稿件发表,或进行资讯合作,欢迎联系本网编辑部, 邮箱:skjcsc@vip.sina.com
更多相关信息