一种弯头管嘴类零件车削加工的工艺优化
2020-12-3 来源:航空工业庆安集团有限公司 作者: 李 涛
摘要: 介绍了某航空产品120°弯头管嘴零件的加工工艺及工装设计方案优化过程,重点论述了工艺流程中如何选择定位基准及夹紧方式,如何通过正确的基准转换来确保零件加工质量,提高加工效率,进而形成规范的工艺流程及典型工装设计。
关键词:弯头管嘴;定位夹紧;车削加工;快换系统
长期以来,无工艺附加弯头管嘴类零件的加工过程中,始终存在零件定位不可靠、夹持不紧、跳动量超差的问题。本文涉及的某管嘴零件如图 1 所示,依次加工两油孔相贯错位量大,形位公差超差严重,零件加工质量差,效率低,严重影响产品生产进度。
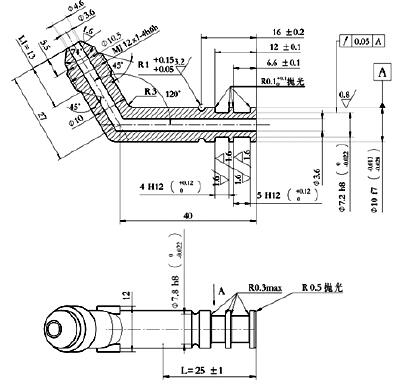
图1 零件图样
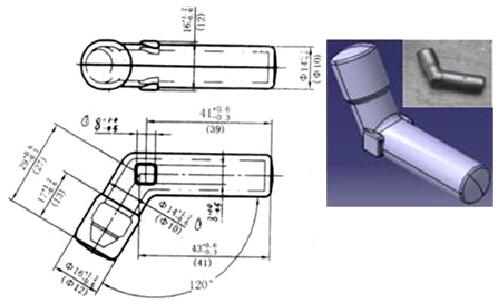
图2 锻件毛坯
1、 工艺分析
零件锻件毛坯见图 2 所示,锻件表面错移,表面不 规则,且无工艺附加,弯头呈 120°夹角,颈部尺寸短,夹具难以设计可靠的定位、夹紧结构。现场采用自制夹具加工,经常出现零件尺寸超差,质量不稳定,效率低等现象,严重影响了零件的正常交付。图 3 为原工艺流程。
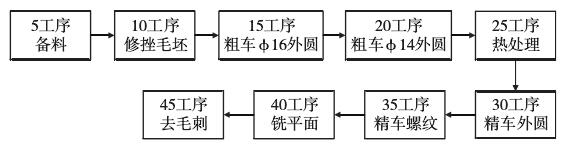
图3 原工艺流程
1.1 原工序分析
15、20 工序,使用自制夹具见图 4。工序基准为零件两个外圆和其中心线交点,工件在夹具上的定位基准选择与工序基准相同,符合基准重合原则的要求,但零件毛坯为锻件且缺陷较重,零件两次装夹,定位基准选择与工序基准均无法保证重合,定位夹紧不可靠,加上自制夹具没有经过热处理,使用时间长产生变形,导致粗车的两端有偏移,不能保证零件两端轴线在同一基准面上,120°夹角误差较大,实际加工的工件表面形位误差不能满足后续加工要求。
30、35 工序,使用自制两爪卡盘装夹见图 5,夹紧比较牢靠,但此夹具两道精车工序分别使用 15、20 工序的两个粗基准进行定位夹紧,理论上粗基准只能选用一次,而且自制卡盘两爪材料未热处理,长期使用后接触面产生变形,夹具中心偏移,导致车削时外圆跳动量大,螺纹表面车削不出来,且难以保证零件两端轴线在同一基准面上,120°夹角误差也较大。导致零件两中心油孔交叉错位,造成成批量报废、严重影响产品交付。
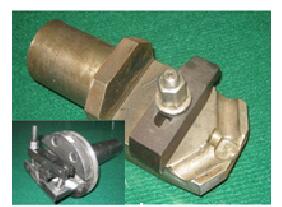
图4 自制车外圆夹具
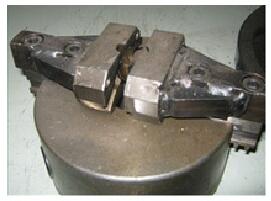
图5 自制两爪卡盘夹具
分析工艺方案,找出造成零件加工超差,不稳定的三点原因,见表 1,并有针对的提出改进措施,保证零件顺利加工。
1.2 优化后的工艺流程
优化后的工艺流程如图 6 所示,保证零件顺利加工完成。
表1 方案优化措施表
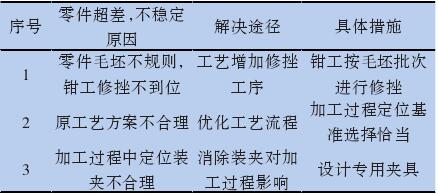
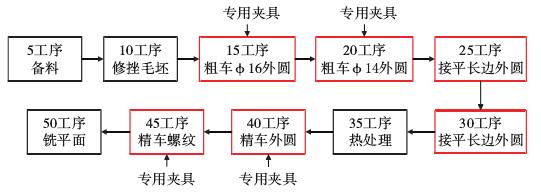
图6 优化后工艺流程
2 、工艺及工装优化过程
通常情况下,在机床上加工工件时,为保证加工精度,首先需要保证工件在夹具上正确定位、夹紧,使工件在机床上占有正确的位置[1],才能加工出合格的零件。为此梳理优化工艺流程,改变原加工策略,最终形成工艺及配套工装如下。
2.1 粗车 Φ16 外圆
15 工序,粗车 Φ16 外圆至 Φ14。夹具设计如图 7所示,采用了过定位原理,用双 V 型同时定位,双面夹紧的结构,其中一个活动 V 型块可以调节夹具中心高,弥补锻件毛胚来源不规则带来的中心偏移问题,且材料选为耐磨性好的 Cr WMn,方便磨损后更换。另一固定 V 型起辅助定位夹紧作用。在通常情况下,过定位是不能使用的,但在某些特定情况下采用过定位方式能解决工件在机械加工中难以解决的一些问题 , 从而可获得良好的加工效果 , 保证加工质量。
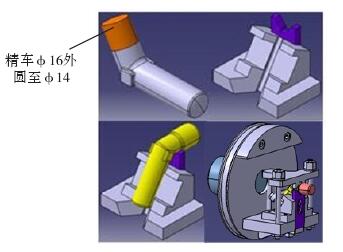
图7 粗车毛坯一端外圆
2.2 粗车 Φ14 外圆
20 工序,粗车 Φ14 外圆至 Φ13。夹具设计如图 8所示,用零件 15 工序车削外圆 Φ14 定位,120°夹角和活动 V 型块定向的结构,其中活动 V 型块可以调节夹具中心高,弥补中心偏移问题,且材料选为耐磨性好的 Cr WMn,方便磨损后更换。
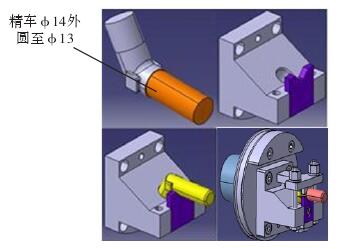
图8 粗车毛坯另一端外圆
2.4 精车 Φ10 外圆
40 工序,精车 Φ10 外圆、钻中心油路孔,夹具设计如图 10 所示,用双 V 型同时定位,双面夹紧的结构,其中一个 V 型限制车削零件中心高,侧边 V 型起辅助夹紧作用,定位块材料选用耐磨性好的 Cr WMn,保证工件定位准确、夹紧牢固,夹紧部位对主轴跳动量应控制在Φ0.03 内,车间使用非常稳定。
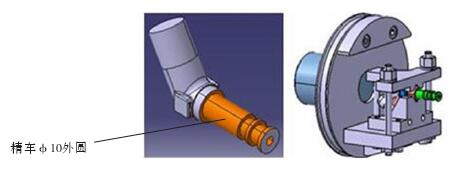
图10 精车外圆面
2.5 精车螺纹
45 工序,精车 M12 螺纹、钻中心油路孔,夹具设计如图 11 所示,用零件 40 工序精车外圆 Φ10 作为主定位,零件 120°夹角定角向位置,15 工序粗车 Φ14 外圆为辅助定位,压板采用圆弧形式,保证了零件定位、夹紧可靠。该夹具由主体、配重、定位板、压板、螺钉、圆柱销组成。在结构上,定位部分镶入衬套,材料为黄铜,以免划伤前道工序外圆表面,定位板和压板均选用硬度高、耐磨性好的 Cr WMn 做为制造材料,且定位板用螺钉和圆柱销连接在主体上,以便磨损后更换,夹具装配时,夹紧部位对主轴跳动量应控制在 Φ0.03 内。经过本次工艺改进及工装优化验证,在车间加工过程中,未发生之前加工的质量问题,零件的尺寸都符合设计图纸要求,满足了产品的配套交付任务。
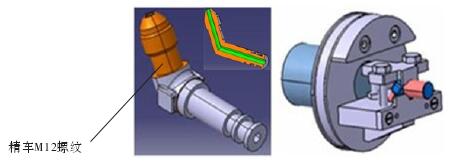
图11 精车螺纹面
3 、车床夹具的模块化实现
夹具模块化实现过程是在进行各工序需求分析的基础上,对其夹具结构形式进行评估,确定模块化设计方案,主要包括专用模块设计、通用模块设计、模块间组合[2]。首先进行专用模块的设计,四道工序使用的车削夹具因基准选择、定位方式不一样,对其单独进行结构设计,车床夹具主体、配重块、压板等可设计成通用模块,便于相互间的互换,最后进行各模块间的组合,形成最终夹具。
而目前以外圆或者内孔定位的车削工序,粗加工都是用三爪卡盘定位装夹,三爪的自定心差,每次换爪都要重新找正,在半精加工或精加工定位一般采用软爪定位装夹,但是软爪更换,需要重新镗削软爪,换装、找正、调整时间长,效率低,另外三爪卡盘装夹离心力大,无法获得高转速。
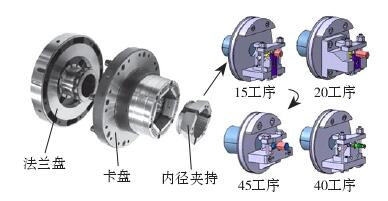
图12 车床夹具快换过程
通过瀚柏格夹具快换系统实现车削夹具模块间的快速更换。如图 12 所示,车床主轴与法兰盘连接,法兰盘与卡盘连接,卡盘内预留标准接口实现内径夹持、外径夹持等,重复定位精度保证在 0.01 以内,实现各工序夹具模块间的快速更换。经生产车间实际验证,运用快换系统实现各工序间的加工能够满足工艺要求,做到机外装夹工件,机床不停机加工,缩短了辅助准备时间,降低了工人劳动强度,提高了零件加工质量和生产效率。
4、结束语
通过对某管嘴零件车削加工的工艺优化及工装设计,彻底解决了以往该零件加工多次返工,成批报废的问题,车间生产过程中,零件加工质量稳定,效率明显提升,一次合格率达 98 ﹪,为后续类似零件的加工提供了重要的参考依据。
投稿箱:
如果您有机床行业、企业相关新闻稿件发表,或进行资讯合作,欢迎联系本网编辑部, 邮箱:skjcsc@vip.sina.com
如果您有机床行业、企业相关新闻稿件发表,或进行资讯合作,欢迎联系本网编辑部, 邮箱:skjcsc@vip.sina.com