数控车削加工中的实用对刀方法探讨
2021-8-6 来源:四川新川航空仪器有限责任公司 作者:龙伟,唐毅
摘要:对刀方法在数控车削加工工作中发挥着重要作用,操作人员需要根据零部件特点选择适宜的对刀方法,通过适宜的对刀方法确定工件坐标系,确保刀具刀尖的协调统一,进而提高数控车削加工质量与效率。基于此,文章简要概述了数控车削加工工艺中的实用对刀方法及基本原理,并就数控车削加工工艺常用的试切法、对刀仪法及 ATC 对刀法等实用方法进行了概述分析,以期为数控车削加工工作的顺利开展夯实基础。
关键词:数控车削;零件加工;对刀方法;操作原理
利用数控车削加工工艺制作零部件时,需要针对零部件特点及类别选择适宜的对刀方法,以此确保车削加工工艺中的刀具刀尖朝向一致。为了提高数控车削加工工序精准性,需要确保刀具刀尖运行轨迹严格依照坐标程序执行。这里提到的坐标程序需要依照零部件尺寸确定横纵坐标系,用于明确工件、机床二者位置的分析方法指的就是对刀方法。对刀操作对于数控车削加工工艺而言是确定坐标体系的主要步骤之一,也是确保数控编程系统与数控原点保持一致性的重要操作。在进行对刀操作工艺的时候,操作者需要将对刀指令传输至数控车床,以此确保数控车削操作严格依照编制程序执行。对刀作为数控车削加工工艺的重要实用技能,对刀方式的精准与否直接关乎着零部件加工
质量与效率。
1、数控车削加工中的实用对刀方法及其原理
1.1 对刀方法概述
对刀方法就是测量计算程序与数控机床间的原点距离,结合实际情况设置好程序原点后,调控刀具刀尖沿着设定坐标系依照程序流程作业。简言之,就是在明确刀具刀尖起始坐标的前提下依照零部件尺寸特点搭建零部件坐标系、设定位置补偿量,以此明确制作零部件与数控机床间的相对关系。在利用对刀方法进行数控车削加工工艺时,需要依照零部件加工原点设定坐标系,随后综合考量刀具尺寸对于数控车削加工的诸多影响,以此为基础录入刀具补偿量,提高数控车削加工工艺质量。
1.2 对刀基本原理
在利用数控车削工艺进行零部件批量生产制造时需要将数控编程与车床加工分开管理,因此在进行程序编订时需要依照设计图纸确定坐标系及程序原点。我国数控车削工艺使用的数控刀架多为四工位结构,部分车床使用六工位及转塔式刀架,虽然使用刀架类别不同,但是其基本工作原理大同小异,现以四工位刀架为例就其数控车削对刀原理进行分析探究。操作人员首先需要将四把刀具安装到对应刀架上,由于四把刀具位于不同位置且存在一定偏差,此时就需要选定一把刀作为基准,以此为基础将相关参数输入其中并进行程序编制,待参数输入完毕后程序会自动对剩余三把刀具读取刀补值,并完成对刀处理。
通过与基准刀的碰触,明确偏差位移,并将测得数据录入中控系统,在进行数控车削加工工作时,编制程序会自动对每把刀具的偏移差进行补植处理。对刀操作工艺就其实质而言就是根据零部件特点设定数控车削体系、编制数控车削程序,并借助常用的 G92、G59、G54、G50等代码实现精准对刀处理。对刀方法基本工作原理如图 1 所示。由图 1 可知,设定的程序原点通常情况下需要与零部件设计基准处于同一位置,编程人员需要依照坐标系上标定的坐标数据调控编制刀尖走向。位于初始原点的刀尖与程序设定原点间存在X 向及 Z 向的偏移,由此导致刀尖在执行程序指令时也会存在类似偏移情况,此时就需要计算测定这一偏移距离,并通过数控技术调整规范刀尖运行轨迹。
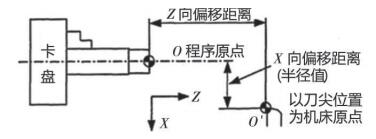
图 1 数控车削对刀方法工作原理
2、数控车削加工中的实用对刀方法及操作技巧
不同类别的数控机床对应的对刀方法存在较大差异,基本对刀流程及操作技巧也存在一定偏差。一般情况下,数控对刀操作主要分为机外对刀、机内对刀这两大类,其中机内对刀在数控车削加工工艺中最为常见。下面就数控车削加工工艺中常见的实用对刀方法及操作技巧进行简单概述与分析。
2.1 试切法
试切法在数控车削加工工艺中的应用最为广泛,采用试切法进行对刀测定时无须其他辅助工具,只需要确保零部件紧密安装到卡盘中即可。零部件安装完毕后,机床与工件在坐标系中没有位于同一位置,为了后续编程计量工作的顺利进行,编程人员需要综合考虑多方因素,在此基础上设置建立工件坐标系,划定刀具运行范围,以确保对刀操作精准无误,也将刀具走向划分到合理范围内,以免影响零部件的数控车削质量。刀具刀尖准确放置在起刀点后,数控机床自动回归到原始位点,操作人员将绿色指示灯开启后,系统进入开启状态;在操作界面下的 MDI 模式中确定基准刀具,通过切换机床画面的方式对其他刀具的补偿值分别进行设定;在进行手动对刀操作时需要确保对刀方向维持不变,及时记录 X 轴坐标,并将测量获得的零部件孔径及外部直径输入到数控机床编程系统中;以同样方式对平断面进行试切处理,并确保退刀过程的平稳性,尽量避免出现位置偏移情况,将获得的补偿值转换为 Z 轴坐标并录入系统中。剩余刀具的对刀补偿与前面所述的方法基本一致,只需加工处理零部件端面即可,无须再进行切削处理。为了提高试切对刀操作工艺准确性,操作人员还需仔细确认刀具半径、输入对应补偿数值,并将处于不同假想位置的补偿数值录入数控编程系统中。
综上可知,试切法属于手工对刀范畴,具有对刀方式简单、精度控制较高、对刀时间较长的特点,其中刀具尺寸及圆弧半径的测量精准性直接关系着数控对刀质量。
2.2 对刀仪法
对刀仪法隶属于机外对刀范畴,操作人员需要整合分析刀尖假想位置、刀具与两轴间距,并利用对刀仪在数控机床上完成刀具校对工作,随后才能进入后续的装机使用操作。对刀仪主要由精度较高的测头、信号传输模块及兼具硬性、耐磨性的对刀探针这三大核心部件组成。对刀探针直接与刀具接触,在绕性支撑杆的作用下能够将其与刀具的作用力传输到高精测头;信号传输模块能够自动接收来自高精测头的通(断)指令,将识别、获取的刀具参数及补偿信息传输给数控系统。在利用对刀仪进行对刀控制工作时需要搭建工具台,安装刀具台,并确保刀具台与刀架尺寸一致,以提高对刀工艺精准性。具体操作流程如下:首先将刀具固定在刀具台上,顺次摇动 X 向、Z 向手柄,确保放大镜能够在这两个方向上平稳移动到与刀尖向重合的位置;随后利用微型读数仪采集对应数据,以准确获得刀具长度信息;最后操作人员需要将刀座一并装入数控机床上,并将获得的刀具长度及补偿数值输入数控程序,以便后续的数控车削工艺得以顺畅进行。
操作人员在利用对刀仪进行对刀处理时不会使用到数控机床,因此不会影响数控车削工作的正常进行。调查显示,利用数控车削加工零部件的时间,约有 55% 的占比为纯机动时间,剩余的 45% 则是对刀、装夹等工具的辅助时间,由此可见对刀仪的优越性。综上可知,对刀仪法相较于其他对刀方法而言具有较高的工作效率,但是由于刀具、刀座需要配合使用,因此需要准备两份一样的刀具与刀座,相对而言成本会有所增加。就我国数控车削加工企业而言,为了节省前期生产制造成本,在进行数控车削对刀操作时往往会忽略这一对刀方法,因此这一方法常出现在研究机构中。
2.3 ATC 对刀法
ATC 对刀法(Automatically Tool Calculated)又被称为光学对刀法,隶属于机内对刀法范畴,主要利用显微镜技术对刀具长度、刀尖位置、圆弧直径、主(幅)偏角进行测定分析。一般情况下,操作人员需将显微镜及刀架拆卸下来,只有进行对刀操作时才需要将它们重新安装到主轴箱上。操作人员需要将刀尖放置在显微镜合理检测范围内,并通过手动移动的方式调整刀架位置,以确保假想刀尖与显微镜中心相重合,此时点击分析按钮获得刀具在X 轴及 Z 轴的长度,计算获得刀具补偿值。具体操作流程:操作人员依照测定规范安装好基准刀及显微镜,确保刀具处于基准点位置,手动调节刀架、转动刀位,预留出安装镗孔刀具的位置;根据镗孔刀具外形特点确定安装位置、设定对刀程序,缓慢移动刀架到对刀位置后点击暂停按钮,并完成镗刀安装工作;待镗刀刀尖与中心位点重合时点击对刀按钮,对刀结束后确保刀架归位才能在对其余的刀具进行对刀处理。
ATC对刀法相较于其他对刀法而言表现出较高的品质、较高的精度,且刀具之间不会相互接触,因此常被用于螺纹、仿形等特殊角度刀具的对刀处理,且不会对刀具刀尖造成不良影响。但是该对刀方法价格成本更高,需要操作人员妥善保管显微镜等测量工具;操作工序较为复杂,每次对刀操作前需要装卸显微镜模块,极易因安装误差影响数控车削对刀工艺精准性。除此之外,操作人员在进行零部件加工时需要将偏移量准确录入数控程序中,一旦出现录入错误也会影响对刀操作准确性、稳定性。
2.4 全自动对刀法
为了进一步提高对刀操作工序的工作效率与质量,研究人员成功将计算机数控系统(Computer Numerical Control,CNC)应用到了数控车削对刀工序上。CNC 系统中的存储器涵盖了多个智能程序,能够通过接口电路及伺服驱动装置与特定计算机网络相连,并通过对操作人员输入的加工程序进行数据处理及插补运算,计算获得最佳运动轨迹,并将相关新型传输到执行模块,以此控制数控车床加工生产出特定的零部件。数据机床在这一智能系统的支持下能够自动对 X 轴、Z 轴长度进行测定分析,并通过后台系统计算出刀具补偿值,不会因后台计算而导致数控车削工序出现停顿问题,由此进一步保证了数控车削质量与效率。自动对刀装置涵盖了硬件系统及软件程序两大模块,常由 CNC 制造厂家负责刀尖检测程序的安装与调试。为了确保对刀操作精准性,至少需要连续进行两次对刀操作工序,两次的刀检差值只有在 2um 的合理范围内才可进行后续的数控车削操作。全自动对刀法相较于其他对刀操作而言精准性更高、操作更为简便,因此已然成为新兴对刀方法,并在多个数控车削机床上得到了广泛应用。
3、结束语
数控车削加工工艺涉及到多个类别的刀具,由于刀具尺寸、规格不同,需要根据实际情况选择适宜的对刀方法,并在此基础上调试好数控程序,保证对刀参数及补偿数值的精准性。操作人员在进行数控车削对刀工艺时需要调试好刀具安装位置、准确录入补偿参数,以加工制造出符合规定标准的零部件,进而提高数控车削加工的工作效率与质量。
投稿箱:
如果您有机床行业、企业相关新闻稿件发表,或进行资讯合作,欢迎联系本网编辑部, 邮箱:skjcsc@vip.sina.com
如果您有机床行业、企业相关新闻稿件发表,或进行资讯合作,欢迎联系本网编辑部, 邮箱:skjcsc@vip.sina.com
更多相关信息