卧式车床加工中产生波纹的原因分析及解决对策
2021-12-20 来源: 哈尔滨锅炉厂有限责任公司 作者:何思琦
摘要:分析了卧式车床在加工时工件表面产生波纹的原因,从设备修理的角度出发,通过分析车床结构,提出解决方案,从而达到消除车削波纹,提高车削精度的目的。
关键词:卧式车床;波纹;修理;消除;精度
0 引言
卧式车床经长期使用后,在车削工件时,工件外圆或端面经常会出现不同程度的波纹现象。波纹的形状、形式多样,有等距离的、螺旋状的,也有杂乱无章的 。有的波纹与工件轴线垂直,有的则与工件轴线成平行状态。总之,不同波纹形状对应的产生原因也不同。但是不论哪种形式的波纹,都会影响工件的表面质量,不能满足工艺要求。所以,加工工件出现波纹必须找出产生的根源,通过调整或修理予以根除。
根据多年的设备修理经验,总结了以下几种产生波纹的原因,并列举了解决方案。
1、等距离波纹
等距离波纹是经常遇到的波纹之一,波纹成圆圈状,与工件轴线垂直,且间距相同。如用记号笔在工件上划过,每隔相等的轴向距离便出现一段记号痕迹,痕迹是断断续续的,说明产生等距离波纹的波峰和波谷的高度差较大,如图1所示。
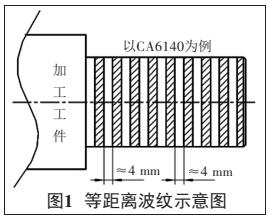
1.1 主要原因一
在工件外圆上产生等距离波纹的原因主要是:由于受车床传动件的影响,溜板在沿着床身导轨作纵向运动的同时,做周期性的上下或左右运动。致使刀具在工件上把溜板的运动曲线反映出来 。
1.1.1 原因分析
在修理的时候首先分析是否由车床的光杠所引起的。由于光杠是细长结构,且极易弯曲。并且在车床工作时,光杠与溜板箱上与之配合的光杠套由于车床转动离心力的作用,产生间隙。当光杠弯曲时,光杠和光杠套的受力点会随着光杠的弯曲而不断变化,光杠的径向跳动量就会变大,再综合床身和溜板导轨工作时产生的磨损量,致使溜板箱下沉,从而引起光杠与溜板箱上光杠带动的齿轮内孔不同心(俗称“压杠”)的现象。弯曲的光杠通过旋转带动溜板纵向进刀的同时,溜板随着光杠的周期性跳动而作上下左右运动,于是产生了等距离波纹。这种波纹的距离与光杠旋转一周而带动溜板进刀的距离是相同的。以CA6140车床为例,波纹间距为4 mm左右。
1.1.2 解决方案
1)测量光杠与齿轮内孔的同轴度误差。
此种方案需测量出光杠与齿轮内孔的同轴度误差,可用检验棒、刀口尺和塞尺测量。具体方法是:在光杠套孔和齿轮孔中插入相同直径的检验棒,移动溜板使检验棒靠近。用刀口尺分别靠在其中较高的一个检验棒的上母线和侧母线上,再用塞尺测量另一个检验棒与刀口尺的缝隙,即可得出两者同轴度的误差值。
误差值较大时,须在溜板的平导轨面上粘接比误差值稍厚的导轨板(余量用于合研修刮),角度导轨的粘接厚度则需要通过计算,粘接后,既要满足溜板抬高的需要,又要消除水平方向的误差。再经过合研修刮,使误差更小,最终达到光杠与齿轮孔同心的要求。
误差值不大时,可刨去溜板上与溜板箱的结合面与误差值相同的尺寸,使溜板箱抬高,然后再加工中拖板丝杠上的齿轮,使其负变位来保证啮合的方法。
通过上述方法,光杠与齿轮内孔的同轴度误差问题就能彻底解决。
2)测量光杠的弯曲度。
此种方案要测量光杠的弯曲度。将光杠架在两个V形铁上,采用百分表来测量,将百分表的表头触及光杠上母线的中间位置,转动光杠,百分表读数的一半就是弯曲的程度。为准确起见,可以分别测量与中间相邻的几个位置。这样做不但能够知道弯曲光杠最高点的位置;还能得出光杠弯曲度的最大值,并且在所弯曲的最高点做记号,使之一目了然。
校正光杠的方法如下:将光杠架在V形铁上,用T形槽螺钉和压板压在做记号处,拧紧螺母使光杠向相反的方向变形。压紧后变形停留90 min以上。同时用铜棒轻轻敲击压板,以消除光杠本身的内应力,起到塑性变形的目的。然后松开压板,进行直线度检查,如果检查结果仍不能达到径向跳动量0.20 mm以内,就需要再一次进行压紧、停留、敲击、检查的过程。需要注意的是,每一次的压紧都要记住拧紧压板螺母的圈数,以便受力后仍然弯曲时增加圈数,使光杠受力进一步增加,从而弯曲程度加大。例如:先拧了6圈,松开后测量光杠的弯曲度,如果发现没有多大的改变,那么再压时就需多拧一圈或两圈,使光杠的弯曲度加大,达到塑性变形的程度。以此类推,如果松开后径向跳动量仍然在0.20 mm以上,就再多拧一两圈。直到发现光杠有校直的迹象时,再进行操作时就只需要半圈或小半圈地增加了。只有这样做,才能做到对光杠的校直程度心中有数,校直才会有显著效果。
通过上述方法,光杠受力弯曲的问题就能彻底解决。
1.2 主要原因二
产生等距离波纹另一原因是因加工精度或配合精度引起的,比如使用年限较久的车床,齿条、齿轮等部件容易磨损,这样,产生等距离波纹的原因可能是:齿条磨损后加工精度达不到要求、齿轮轴磨损后加工精度达不到要求(溜板箱上与齿条啮合的齿轮轴)、齿条和床身导轨面配合达不到要求、齿轮轴与溜板箱孔配合达不到要求、溜板箱纵向运动的输出齿轮与床身上的齿条啮合不良等。这时产生的波纹与上述由于光杠同轴度或直线度的原因造成的波纹形状一样,但距离有所不同,波纹的距离与齿条的周节相一致。
1.2.1 原因分析
这是由于溜板纵向运动时,齿轮轴上的齿轮与齿条相啮合,当输出齿轮与齿条接触时,与齿轮轴配合的套与齿轮轴存在配合间隙,配合间隙较大时,齿轮轴在转动时就会偏离原有的轨迹,从而在齿轮轴与齿条啮合时,齿轮轴的轴线就会发生偏移,导致啮合不良,进而产生周期性的振动状态,这是一个不正常的运动,会造成了大托板不能平稳移动,直接影响了溜板的直线运动,从而在工件上产生了波纹。
1.2.2 解决方案
在齿轮与齿条之间通过压铅丝法,具体方法为:将直径为顶间隙的1.25~1.50倍的软铅丝用油脂粘在齿轮上(注意铅丝长度不应短于5个齿距),然后用力将齿轮转动,使铅丝置于齿轮与齿条结合面上,经挤压后,铅丝变形,其厚度即为实际间隙值,用游标卡尺测量出铅丝厚度。然后根据间隙来调整齿条的位置,使输出齿轮与齿条的啮合状态达到最佳,保证传动时平稳无阻滞 。
1.3 主要原因三
在工件端面上产生等距离波纹和在外圆上产生的原因是一样的,也都是由于传动机构的影响。
1.3.1 原因分析
与上述原因一致,中拖板丝杠弯曲导致直线度误差、丝杠和丝母不同心导致的同轴度误差、中拖板导轨间隙大导致径向跳动。这3个原因使得中拖板在前进时,产生了左右的移动,走出了有规律的曲线,在工件上产生了波纹。波纹的距离和丝杠的螺距一致,即丝杠每转一圈,对中拖板就有一个周期性的影响,于是工件端面上就留下了等距离的波纹痕迹。
1.3.2 解决方案
与上述外圆波纹的操作方法一致:一是校直中拖板丝杠,采用反压紧法;二是使丝杠丝母同心,采用余量合研修刮法;三是调整斜铁,消除导轨间隙。这3个问题解决了,波纹也就随之消除了。
2 、杂乱无章的波纹
此类波纹因其杂乱而多种多样,无明显规律可寻,并且间断性地出现,因此需要深入分析产生的原因,找准切入点,才能事半功倍,快速解决问题,经总结,大致有以下6种原因可导致此类波纹。如图2所示。
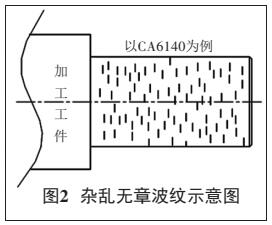
2.1 主要原因一
主轴轴承磨损,主轴旋转时由于受力不均衡形成振源引起主轴振动。
2.1.1 原因分析
主轴轴承在主轴上高速运转,产生轴承磨损。
2.1.2 解决方案
更换主轴磨损轴承,新轴承装配时,要注意应根据误差相消的方法。即:轴承外圈跳动的最高点对准主轴箱孔跳动的最低点;轴承内孔跳动的最高点对准主轴轴径跳动的最低点。这样可以减小误差,装配精度也会随之提高。
2.2 主要原因二
主轴与与之相配合的零件存在误差,导致主轴在高速运转时产生轴向窜动。
2.2.1 原因分析
主轴轴肩端面的直线度误差;主轴轴肩端面与轴承承载端面对主轴回转轴线的垂直度误差;主轴壳体轴承孔与主轴回转轴线的垂直度误差等。
2.2.2 解决方案
调整主轴后端的圆螺母,调整并消除平面轴承、壳体等零件的间隙,减少主轴轴向窜动量。调整时,先脱开主轴上的传动齿轮,然后一边旋转主轴一边调整圆螺母,直至调整至松紧合适即可。
2.3 主要原因三
主轴壳体轴承孔与主轴轴承的外圈产生间隙。
2.3.1 原因分析
主轴箱体孔因长期磨损变形导致主轴壳体轴承孔与主轴回转轴线产生垂直度误差,使壳体与轴承间产生间隙。
2.3.2 解决方案
将主轴箱在数控镗床上按主轴后轴承孔找正,将主轴箱前轴承孔镗大8~10 mm,用冷缩法将外径加工好而内径留有加工余量的钢套镶入。待温度升至常温后,按与主轴轴承外圈过盈0.005~0.020 mm的尺寸镗成即可。
2.4 主要原因四
四方刀台与刀架上平面接触不良。
2.4.1 原因分析
四方刀台因长期使用导致变形,与刀架上平面产生平行度误差,致使四方刀台与刀架上平面接触不良。
2.4.2 解决方案
四方刀台夹紧刀具后,可用涂色法检查底面与刀架上平面的接触精度。通过修磨修刮,保证刀台夹持刀具后,其底面与刀架上平面仍能均匀地全面接触。
2.5 主要原因五
使用尾座支持工件进行加工时,顶尖套不稳定。
2.5.1 原因分析
顶尖锥柄与套筒锥孔磨损不能严密贴合,顶尖轴承因磨损出现间隙。
2.5.2 解决方案
检查顶尖锥柄与套筒锥孔的接触情况,通过修磨或研磨,使其接触良好。检查顶尖轴承间隙,通过调整或更换,保证顶尖的旋转精度。
2.6 主要原因六
因电动机运转不平稳而产生振动。
解决方案:可校正电动机转子的平衡,有条件的可以进行动平衡。
3 、螺旋状波纹
螺旋状波纹像螺纹一样,有间距但不重合,包络在外圆上,如图3所示。
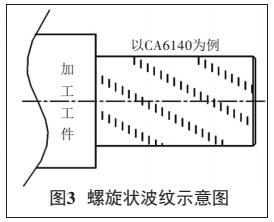
3.1 主要原因
其原因主要是主轴间隙大、刀具夹持不紧或刀杆刚性差。纵向进刀时,工件和刀具因产生共振而相互作前后方向的位移,使切屑厚薄不均,工件表面高低不平,同时发出刺耳的响声。
3.2 解决方案
一是调整主轴轴承,使主轴的径向间隙和轴向窜动量合乎精度标准的要求;二是压紧刀具,消除松动现象;三是选择刚性好的刀杆。
4、结 论
综上所述,总结分析了卧式车床车削加工时产生3种主要波纹的原因,并从设备修理的角度提出了解决方案,不仅提高了故障诊断的准确率,还缩短了诊断时间。
投稿箱:
如果您有机床行业、企业相关新闻稿件发表,或进行资讯合作,欢迎联系本网编辑部, 邮箱:skjcsc@vip.sina.com
如果您有机床行业、企业相关新闻稿件发表,或进行资讯合作,欢迎联系本网编辑部, 邮箱:skjcsc@vip.sina.com
更多相关信息