基于 ADAMS 的数控机床进给系统动力学仿真
2017-6-23 来源:沈阳化工大学机械工程学院 作者:赵艳春,李尚帅,李铁军,王丹
摘要: 为了分析机床进给系统在零件加工时对其精度影响,利用三维造型软件 Solid Works 建立数控机床进给系统的动力学模型; 利用 Ansys 分别建立丝杠和工作台的有限元模型,将模型导入 Adams,对数控机床进给系统进行振动仿真。结果表明: 固定转速下,工作台在不同位置的振幅不同,改变转速其规律相近; 在不同转速下,速度越大,工作台振幅越大,并呈线性关系。
关键词: 工作台振动分析; Adams; 数控机床; 进给系统
0.前言
随着企业效率的提高和自动化程度的提高,人们对高速机床的需求越来越大。国外有些发达国家的先进水平可以使机床的主轴转速最高可达到 100 000 r/min,但在运用机床高速运转的同时不得不考虑其高转速引起的大振动问题,而振动超过一定范围时就会使机床的稳定性下降,加工精度下降,机床的使用寿命也会减少。所以,研究机床的振动性能对于减小振动,提高机床稳定性是必不可少,也是至关重要的。
数控机床的进给系统是机床的重要组成部分,也是影响数控机床加工精度的重要因素,影响机床进给系统的精度因素有丝杠的导程、工作台和导轨之间的支撑刚度、丝杠的预拉伸力等等[1 - 2]。
文中主要通过虚拟样机技术研究进给系统在不同的转速下对工作台振动的影响。
1.数控机床进给系统模型的建立
考虑到在 Adams 中建模过程比较繁琐,采用三维造型软件 Solid Works 对进给系统进行建模。把装配体模型文件导入到 Adams 中,构成虚拟样机的几何模型,通过给几何模型中的零部件施加约束、运动、力等,完成数控机床虚拟样机的建立[3]。由于 Solid Works 软件建立的模型是刚形体,在仿真中对于大部分零件是符合实际工作情况的,而丝杠和工作台则与进给系统在实际工作中的情况不符,为了使仿真的结果更真实可靠,接近进给系统的实际工作情况,需要对丝杠和工作台进行柔性化处理,运用Ansys 软件对丝杠和工作台进行网格划分[4],处理后导入 Adams 中模型如图 1 所示。
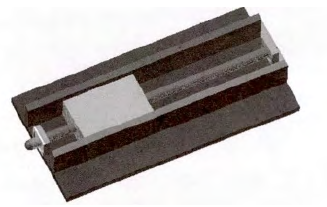
图 1 进给系统在 ADAMS 中模型
2.进给系统虚拟样机仿真
文中研究直径为 40 mm 的丝杠在不同转速下对工作台的振动影响情况。丝杠的转速从 500 r/min 到4 000 r / min,每加 500 r 仿真一次。并且在丝杠上分别取 10 个等距的点为工作台仿真初始位置点,研究的目的就是工作台在不同转速下某一点的振动情况和同一转速时不同位置的振动情况比较。仿真系统其他参数[5]设置见表 1。
表 1 系统参数设置
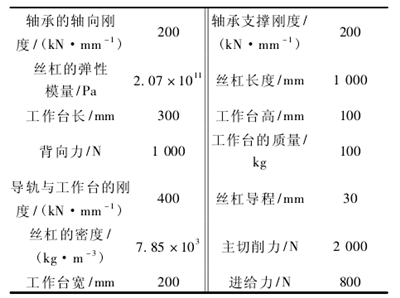
在丝杠上分别取 10 个不同的点作为工作台振动分析起始点,分别命名为 X1,X2,…,X10。它们的间距分别为 50 mm,X1代表工作台停在距离丝杠左端的 250 mm 处,而 X2,X3,…,X10是从 X1依次向右取。当工作台的质心停在 X1时突然给丝杠一个速度,也就是给丝杠一个冲击,仿真结束得到一组数据后,通过改变转速值得到在 X1处不同转速下仿真结果,按此法依次得出十个点的仿真数据,最后通过Adams 的后处理模块进行分析。
(1) 工作台同一点在不同转速下的轴向振幅在 X1及 X5处,不同转速对工作台的轴向振动情况如图 2 及图 3 所示。
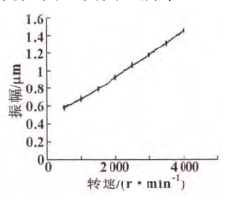
图 2 X1处最大振幅值变化幅度
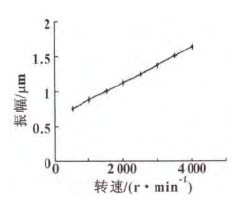
图 3 X5处最大振幅
从图 2 可以得到在位置 X1处随着转速的增加工作台的振幅随之增加,大致呈线性规律。从图 3 可以得到在位置 X5处随着转速的增加工作台的振幅也随之增加,与在 X1相比,振幅值大小相差不大,且斜率相近。
(2) 同一转速下工作台不同位置的轴向振幅各转速下不同位置的轴向振动情况如图4—6 所示。
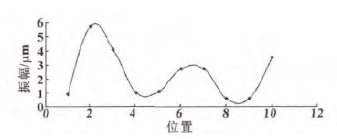
图 4 转速为 2 000 r/min 时不同位置的轴向振动
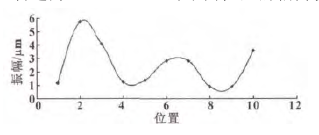
图 5 转速为 3 000 r/min 时不同位置的轴向振动
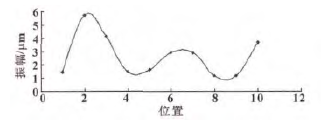
图 6 转速为 4 000 r/min 时不同位置的轴向振动
从图 4—6 可看出,在同一转速不同位置的下,工作台振幅大致呈现为 “波浪状”,随着位置的变化,其振幅先增大,随之减小,然后再次增大。
3.结论
通过利用 Solid Works 和 Ansys 软件完成了数控机床进给系统零部件和装配体的建模,然后将装配体导入 Adams 中建立了进给系统虚拟样机仿真模型,设置约束和参数,完成对数控机床进给系统动力学分析。得出工作台在丝杠不同转速激励下的轴向振动响应曲线,并且得出同一位置不同转速的最大振幅规律,以及根据同一转速不同位置最大振幅的变化规律曲线,得出随着转速的增加各位置的最大振幅随之增加呈线性关系; 转速一定时规律比较明显,工作台在开始的时候振幅最大,在丝杠中后部和后端振幅较大。为以后的误差补偿提供一定的依据,同时对工作台的结构优化设计和丝杠转速最佳值的选取有一定指导价值。
投稿箱:
如果您有机床行业、企业相关新闻稿件发表,或进行资讯合作,欢迎联系本网编辑部, 邮箱:skjcsc@vip.sina.com
如果您有机床行业、企业相关新闻稿件发表,或进行资讯合作,欢迎联系本网编辑部, 邮箱:skjcsc@vip.sina.com
更多相关信息