未来轴承智能制造的几点思考
2018-3-20 来源:北京发那科机电有限公司 作者:景喜瑞
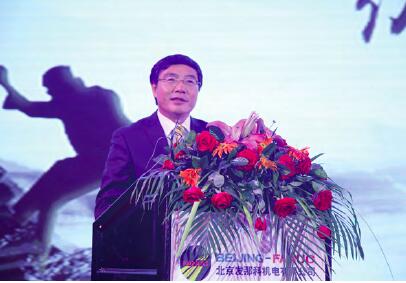
北京发那科机电有限公司总经理景喜瑞先生北
2016年9月19日,北京发那科总经理景喜瑞先生出席2016上海国际轴承峰会,针对“要实现智能制造,作为世界制造业大国的中国应该走什么样的道路?”、“轴承行业作为制造业的基础行业,未来又将会面临怎样的挑战?”等峰会议题,景总做了深入的演讲解读,简要分析了中、德、美三国制造业战略的异同,并提出中国必须走出一条具有中国特色的上下融合之路,即《中国制造2025》中提出的“两化深度融合”。
在全球一体化的压力下,制造业在一段时期内将遭遇一些挑战,主要包括:更短的产品生命周期、高度定制化的产品需求、以及来自全球不同市场的激烈竞争。在这种产品越来越复杂但产品生命周期日益受限的情况下,计算机辅助技术(CAx)在产能爬坡优化和加速阶段的重要性越来越高。更高的产品多样性和更短的产品生命周期需要一种更灵活和柔性的生产结构,在这种结构下可快速根据新产品的需求重新配置生产方式。在当前传统的自动化生产方式下肯定无法达到这样的柔性程度。取而代之的是,作为物联网(Io T)的一部分,由智能设备组成的模块化工厂结构将是实现可调整生产场景并克服现有挑战的关键因素。轴承行业作为制造业的一个基础行业,也会面临一系列的挑战。景总举了两个例子与大家共同分析探讨。
1 、高柔性大规模生产
现代轴承行业的制造生产,特别是中小型轴承的制造生产,其产品基本上具有少品种大批量的特点。因此,此类大批量轴承的生产线自动化程度很高,生产效率和设备利用率也很高。但只能加工生产线设计时对应的一种或几种非常相似的产品。随着如今产品的高速更新换代,客户需求的不断精细甚至定制,市场对多品种小批量轴承产品(10~1 000件/批次)的需求越来越多。面对这样的情况,这种“刚性”或低柔性的生产线要么无能为力,要么调整成本过高。因此,提升生产线的柔性,并保持大规模生产一样的低成本——即高柔性大规模生产是未来轴承智能制造的一个重要挑战。
景总认为,要实现高柔性大规模生产,可以从如下几个方面着手。
(1)CNC替换PLC。在轴承生产中使用了大量的磨削机床。因一些低柔性生产线中的磨床生产工艺比较单一,因此其控制系统并未使用专门用于机床控制的数控系统(CNC),而是使用了可编程逻辑控制器(PLC)。PLC与CNC在机床控制方面一个重要的差异就是加工程序的编写和修改方法。PLC只能通过编写PLC程序的方式来编写加工程序,而PLC程序的编写和修改都需要在专门的PC软件中完成,无法方便地在人机界面(HMI)中进行。每次编写或修改后都需要经过专用软件编译,下载到PLC控制器中方能使用。而CNC作为专门的数控机床控制器,可以方便地在HMI中通过标准G代码编写和修改加工程序。因此,应用在机床上时生产柔性明显高于PLC.
(2)增加机器人的应用。在当前少品种大批量轴承的生产线中,因为产品类型比较单一,所以产品在生产线的运输以及在各个设备上的装卸往往都是通过传送带、滚道或专用装置完成的。很少引入机器人参与生产加工。因为在单一品种大批量生产的情况下,这种方式的效率较高,而将机器人引入的话,反而会降低整条生产线的效率。但是,这样的生产线要么几乎无法换型,要么一旦换型,所耗费的时间和人工精力也将是巨大的。而机器人天生就具有高柔性的特点,比如发那科的智能机器人,具有类似于眼睛的视觉传感器和类似于触觉的力传感器,可以根据现场和工件的具体情况自主地完成所需工作。如果应用得当,则完全可以在满足效率要求的前提下,大幅提高生产线的加工柔性。
虽然人是柔性最高的生产参与者,但是与机器相比人具有生产效率较低和自由散漫的特性。因此,如果只追求高柔性生产,当然由全人工组成的生产线最合适。但是,如果追求的是高柔性大规模生产,那么在生产操作部分减少生产效率较低、且可能带来不可控因素的操作人员应该是更好的选择。何况,中国的用工成本逐年递增的趋势愈来愈明显。在市场竞争和波动加剧的今天,人员流动的风险和企业对用工需求调整的难度也越来越高。未来,以合理的成本雇佣合格的生产操作人员将越来越困难。因此,企业应未雨绸摸,为应对这些变化早做准备。
(3)发展通用工装。目前在轴承生产线上使用得大多是根据产品类型制作的专用工装,价格昂贵,用途单一,生产换型时也需要更换。当产品品种增加时,工装的种类和数量也得相应增加。因此,发展通用乃至万用工装是提高生产柔性的必备条件。
(4)以物联网为核心的智能工厂。正如德国工业4.0报告中描述的那样,未来工厂中的产品、设备、资源和人将通过物联网(CPS)有机地结合在一起,智能产品根据各自的工艺需求自主地在模块化结构的工厂中移动,实现高柔性高效率的制造。当然,工业4.0的这个描述是制造业的一个长期目标,一个远景,无法在短期内实现。企业可以先将比较容易接入物联网的节点连接起来,将物联网的架构搭建起来,再慢慢实现将产品等现阶段不容易接入的节点连接到网络中。
发那科在今年4月联合思科、罗克韦尔和PFN公司共同发布的FIELD(Fanuc Intelligent Edge Link & Drive)系统就是一个专业的工业物联网平台。这个系统可以接入数控机床、机器人、PLC以及传感器等众多现场设备(不局限于发那科品牌)。在现在非常热的“云计算”之外,FIELD系统更强调离用户现场更近的“雾层”的应用。因为“云”服务通常都部署在远离用户现场的地方,甚至是其他国家。在应用时,如此长距离的大数据传输就有数据通讯和数据安全方面的风险。而且,很多时候对大数据的处理无需发送到“云端”。在离用户现场更近的“雾层”通过合适的应用软件就能完成数据的分析处理。另外,FIELD系统是一个开放的平台,它就好比是智能手机的i OS或者安卓操作系统,允许第三方公司在其上开发应用软件(APP),满足多种多样的智能制造需求。比如,发那科的SCADA软件Link-i和ZDT就可以视为FIELD系统上的APP。同时,FIELD系统还持PFN公司开发的人工智能应用,将机器学习和深度学习应用到工厂的实际生产中。
2 、更好的质量一致性
随着我国轴承行业的发展,我国生产的轴承产品逐渐进入了国内外一些非常注重产品质量的用户的采购范围。不过这些客户不仅重视产品的质量等级,更看重产品的质量一致性。比如美国通用汽车公司,如果产品能满足其GMW14840和GMW16311轴承检测标准,则意味着有很高的质量水平。不过,一旦有一件产品被通用汽车发现质量问题,则供应商就会面临极大的换货成本压力。做一件高质量的产品不难,难的是高质量地生产每件产品。而未来,将有越来越多的客户注重这方面的要求.
另外,轴承套圈和滚动体的精密磨削工艺是一个经过了多年应用、实验和分析的,非常成熟的工艺过程。到目前为止,很多应用磨削工艺的公司都认为这一技术已经接近顶峰,几乎没有什么新的或重大的技术发展空间了。然而一台典型的轴承磨床生产的套圈和滚动体的质量,会随着砂轮的磨损而发生恶化。随着砂轮的磨损,被磨削工件的表面质量的变化将会增加。对于轴承套圈和滚动体来说就意味着表面粗糙度、工件直径和锥度的变化。而且,这些质量不一致的零件在装配后又将导致更大的偏差。
可见,实现更好的产品质量一致性是轴承行业未来的一个挑战。要克服这一挑战,可以从如下几个方面着手。
(1)改善磨削加工的一致性。现在的数控系统已经具备智能机床控制的一些功能,可以通过在磨床上增加一些过程传感器和测量设备,来获取一些信息。比如声发射、磨削功率和磨削力等。再将这些信息发送到数控系统控制器,以便持续评估每一个砂轮的过程状态,并自动且及时地调整机床设定。当然,如何调整机床设定需要轴承企业总结多年的制造经验。如果设置得当,即意味着每一个零件都有自己独特的磨削参数,从而使每一个零件达到完全一致的表面质量。
(2)提高产品检测的自动化程度。检测是保证产品质量一致性的重要手段,而首先要实现的应该是对产品在生产过程中100%检测。如果100%检测对生产效率产生了影响,则应考虑改善检测的方式,提高检测的自动化程度。另外更为关键的是,不论是自动检测还是人工检测,都应尽早实现将检测设备接入物联网,使检测结果实时上传、保存,以便减少人工检测的人为干扰因素,实现产品质量追溯管理。
(3)最佳实践的总结与推广。在物联网的帮助下,企业可以从各地工厂的大数据中总结获得更好质量一致性的生产工艺、生产管理、运营方式等最佳实践。同时也可以通过网络,将这些最佳实践迅速推广到各个工厂中,形成新的标准体系。从而确保各个工厂生产的一致性。综上,在通往实现《中国制造2025》的道路上我们任重道远,我们除了关注机器人、信息化等新技术的应用,更要注重工装卡具等基础方面的研究,持续改进工艺,为不远的“智造”夯实基础。 中国机床制造业依然大有可为,整个轴承行业也在正确的道路上前行。北京发那科愿与所有合作伙伴一起 “携手共赢,赢在智造”。
投稿箱:
如果您有机床行业、企业相关新闻稿件发表,或进行资讯合作,欢迎联系本网编辑部, 邮箱:skjcsc@vip.sina.com
如果您有机床行业、企业相关新闻稿件发表,或进行资讯合作,欢迎联系本网编辑部, 邮箱:skjcsc@vip.sina.com