基于华中数控系统的复合加工 机床控制系统
2018-7-17 来源:南京航空航天大学机电学院 作者:王夏望,沈建新,田 威
摘要 为了提高机身大部件在装配过程中钻孔铆接的效率,并满足高精度制孔要求,设计了由五轴机床和末端执行器组成的自动化协同钻铆控制方案。机床本体及高精度转台采用华中数控系统控制,末端执行器采用倍福 PLC程序控制。在明确钻铆需求后设计了基于工业网络的硬件组态和基于多软件平台的软件组态,并利用 Microsoft Visual Studio 开发平台编写了上位机集成控制软件。控制系统分别采用 Ethernet 和 Ether CAT 工业以太网实现上位机控制系统和华中数控系统、倍福 PLC 控制程序的通信连接。在集成控制软件中通过套接字进行以太网通信接口开发,并在复合加工机床上进行试验验证。该控制系统具有稳定性好、集成度高、响应快、效率高的特点,能够满足钻铆需求。
关键词:五轴机床;末端执行器;华中数控系统;硬件组态;软件组态;通信
飞机机体构造复杂,零件和连接件数量众多。机身大部件要求长寿命、高强度、密封、抗疲劳,对连接孔的制备精度有非常高的要求。传统飞机装配中的制孔存在诸多缺点,例如孔位精度差、易形成缺陷、需要二次装配等。随着计算机技术、自动化技术的发展,开发用于机身大部件装配的复合加工机床,实现高精度自动钻铆功能,成为飞机先进制造技术的研究热点之一,也是飞机装配技术的发展方向。
用于飞机数字化自动装配的复合加工机床在国外已经得到广泛研究与应用。美国 GEMCOR 公司的G2000 型钻铆机可以铆接弧度大于180°的超级壁板。Electroimpac 公司生产的 E7000 自动钻铆系统每分钟铆接数量达到 15 个(图 1)。
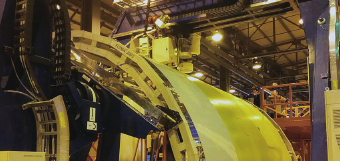
图1 E7000自动钻铆系统
我国的复合加工机床研究虽然起步较晚,但目前在实践中得到诸多应用。南京航空航天大学自主研发的基于工业机器人的自动制孔系统可以实现制孔节拍 3~4 个 /min。基于华中数控系统的复合加工机床能够实现 6 个 /min 的钻孔效率。
华中数控是国内最早开发数控系统、伺服电动机和驱动成套数控装置的企业。其自主研发的 HNC-8型全数字总线式高档数控系统采用模块化、开放式结构体系。该系列数控系统基 NCUC 工业现场总线技术,具有多通道控制、五轴加工、高速高精度等功能。
针对机身大部件钻铆的具体加工指标,复合加工机床采用上下位机控制体系。在上位层采用 C++ 高级语言开发的集成控制软件,下位层为华中数控系统、倍福 PLC 控制程序。控制系统集成了运动控制、钻铆加工、数据测量等功能,能很好地满足自动钻铆任务的需求。
控制系统硬件组态
用于机身大部件自动钻铆的复合加工机床为五轴联动数控机床,其整体结构如图 2 所示。机床本体采用华中数控系统控制,用于承载末端执行器,控制其沿 X、Y、Z 轴方向移动以及绕 X、Y 轴方向转动。高精度转台作为机床的重要附件,用以装夹工件并实现回转和分度定位,同样采用华中数控系统控制。末端执行器由倍福 PLC 系统控制,主要包括基准检测、法向找正、自动送钉、钻孔锪窝等模块用以实现钻铆加工的功能。机床本体硬件组态如图 3 所示。
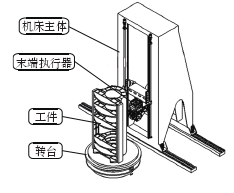
图2 复合加工机床整体结构
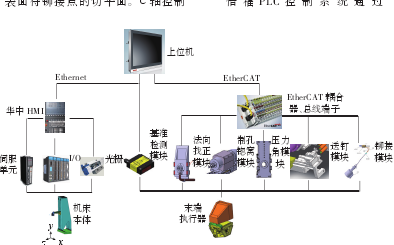
图3 自动钻铆系统硬件组态
1、基于 NCUC 总线的华中 8 型 数控系统
NCUC 现场总线适用于高速、高精的数控机床领域,是国内首个现场总线的国家标准。标准 OSI 通信参考模型具有 7 层结构,能够支持非常强大的通信需求。NCUC 总线参照该模型简化为物理层、数据链路层和应用层,具有全数字、串行、同步、双向、多站点的特点。HNC-8 数控系统是 NCUC 总线的典型应用,如图 4 所示。HMI 提供人机交互界面,其中的 IPC 单元用以运行数控装置系统软件。伺服驱动器用于控制电机运动。I/O 设备用于数字量、模拟量信号的输入输出。NCUC 现场总线将伺服驱动器、I/O设备等连接到 IPC 单元。X、Y、Z 轴为直线轴,分别控制机床本体的 x、y、z 向运动。由于 y向承载包括末端执行器、x 轴滑台等机械部件,负载非常大。所以 Y 轴运动由两个电机同步控制,通过在HNC-8 系统中设置相应参数实现,如图 5 所示。A 轴和 B 轴为旋转轴,在刀具法向找正时调整末端执行器的姿态,使刀具轴线方向垂直于蒙皮表面待铆接点的切平面。C 轴控制高精度转台运动。
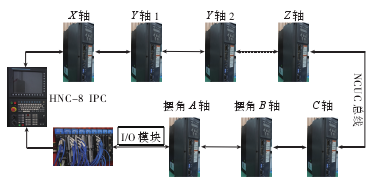
图4 华中数控系统总线
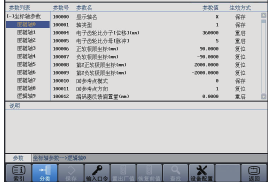
图5 HNC-8系统参数
2、系统通信链路架构
为保证整个钻铆加工系统的协调性与一致性,采用在上位层系统中集成控制华中数控系统和倍福 PLC控制程序。由于华中数控系统和倍福 PLC 控制系统使用的通信方式和协议不兼容,构建系统控制网络时采用双通信主线的架构,具体通信链路如图 6 所示。华中数控系统主要负责完成非实时的点位运动控制。HNC-8 数控系统 IPC 单元提供以太网接口,因而采用 Ethernet 网络将上位机控制系统与华中数控系统连接通信。Ethernet 遵循 TCP/IP 协议,具有传输速度快、稳定性好以及使用简单的特点。Ethernet 通信接口采用 Socket组件开发,实现华中数控系统的运动指令自上而下传输以及华中系统自身状态信息的自下而上反馈。末端执行器所有的输入输出设备都由倍福公司的 Twin CAT 软件进行控制。Twin CAT 自动化软件是倍福基于 PC 控制系统的核心部分,与工业计算机结合在一起,可以将现有的 Windows 系统改造为实时控制系统,构建功能强大的基于 PC 的全软件控制系统。倍 福 PLC 控 制 系 统 通 过EtherCAT现场总线将I/0模块及总线藕合模块与TwinCAT控制软件相藕合,形成完整的通信网络EtherCAT现场总线是倍福公司自主研发的实时工业以太网。该总线以以太网为基础,具有超快的数据传输速度,灵活的拓扑结构,出色的调试诊断性能,因而极大地提高了系统的实时性能。上位机PC通过网卡2,借助以太网线与倍福EK1100藕合器连接,实现上位机控制系统对末端执行器的实时控制。
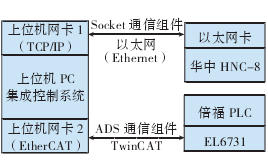
图6 系统通信链路
控制系统软件组态
在软件层面,主要有上位机集成控制软件、倍福 PLC 控制程序、HNC-8 系统软件等。当同时运行这几种软件时,需要进行主从结构设定,时序控制规划,通信接口开发等,从而使软件系统能够稳定、有序地协同执行各部分指令,完成既定任务。
1、软件组态整体方案设计
上位机集成控制软件在系统软件组态中处于主导地位,负责规划整个钻铆系统的加工任务,监测现场加工任务的执行情况,如图 7 所示。上位机集成控制软件向 HNC-8 数控系统发送点位指令,控制各坐标轴运动到指定位置;向倍福 PLC 控制程序发送加工指令,获取现场数字量模拟量数据并调用相应算法程序处理,进而控制完成调姿、钻铆等加工任务。HNC-8 数控系统获得上位机控制系统发送的点位信息后执行完成指定运动,并向上位机反馈此时的位姿信息。
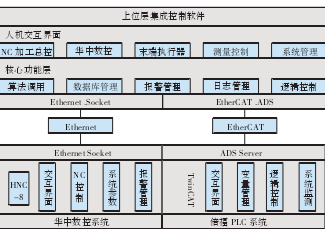
图7 控制系统软件组态
倍福 PLC 控制程序接收上位机控制系统加工参数设置、被控设备动作等加工指令,从而实现加工任务。同时完成对各数字量与模拟量的数据采集与控制并向上传输给上位机控制系统。
2、上位机集成控制软件架构
上位机集成控制软件采用界面层与逻辑层相分离的设计思想。用户界面层独立于核心功能层设计,以XML文件为载体与核心功能层相关联。用户界面层选用 Duilib 界面库进行开发设计,按照自动钻铆控制系统功能划分为 5 个模块,以分层页面的形式加以设计和管理。核心功能层选用 UML 可视化语言构建软件的整体框架,将整个底层分为通信控制、数据库管理、报警管理、日志管理等模块,并设置统一函数接口调用上述功能模块,方便用户在界面上的操作能得到快速、准确的传达和执行,如图 8 所示。
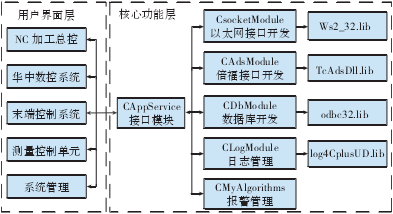
图8 集成控制软件架构
数据库管理模块作为数据库应用的接口,主要用于存储管理用户信息、刀具库信息、现场测量数据以及系统关键信息等。采用微软公司推出的关系型数据库管理系统 SQL Server 作为数据库软件,同时在控制软件中要包含其静态库文件。
报警管理和日志管理模块作为日志和报警管理接口,主要用于软件、设备操作日志管理和系统故障报警信息管理。选用 C++ 开源日志库log4cplus 进行日志管理。log4cplus将日志信息和报警信息分别生成两份 Text 文件,并对这些信息进行编号和等级划分。同时重点开发通信控制模块,选用高效、稳定的通信方式和协议完成上位机集成控制系统与下位层HNC-8 数控系统、倍福 PLC 控制程序之间的数据交互,切实发挥上位机集成控制软件在加工控制系统中的主导作用。
系统通信接口开发
上位机控制系统与华中数控系统的通信采用 Socket 套接字方式,根据钻铆加工需求开发出多种工作模式。上位机控制系统既可以作为服务端,也可以作为客户端,从而获得更强的兼容性。
1、Socket 通信基础
网络中进程之间进行相互通信的基本前提是能够对进程实现唯一的标识。IP 层的“IP 地址”可以唯一标识网络中的主机,而 TCP 层的“协议 + 端口”可以唯一标识主机中的一个进程。因而 TCP/IP 协议族可以通过 3 个以上参数在网络中对进程进行唯一标识。Socket 把 TCP/IP 层复杂的操作化简为几个简单的接口,直接调用这些接口就可以实现进程在网络中的通信。它将一个 Socket 与TCP/IP协议的 3 个参数绑定,在不同主机间建立双向通信的端点,协议的应用层就可以通过套接字接口区分来自不同网络连接或不同应用程序进程的通信,从而使数据并发传输。
2、上位机软件通信接口开发
在 windows 平台下进行 HNC-8 的通信接口开发,需要将 HNC-8 的相关软件包文件加载到软件的工程文件夹中。然后在上位机软件中调用华中数控提供的接口函数完成通信。上位机与华中数控通信采用Socket 通信具体实现过程:
(1)设置 HNC-8 数控系统参数。将系统 NC 参数中“是否启动网络”值设置为 1,即允许进行网络通信。
(2)配置 Microsoft Visual Studio开发环境。在附加包含目录中加入接口函数头文件的路径;在附加依赖项中加入 lib 库文件路径;在生成的目标文件所在文件夹中加入 dll 文件。
(3)绑定本地 IP 地址和端口。调用 HNC_Net Init Net Init(const Bit8 *ip, u Bit16 port)函数,将两个参数分别设置为上位机的 IP 地址和端口号,完成与套接字的绑定。
(4)向华中数控系统发送连接请求。调用 HNC_Net Connect(constBit8 *ip, u Bit16 port)函数,将两个参数分别设置为向华中系统 IP 地址和端口号。华中系统接受请求后完成连接。
在完成接口开发后,便可以利用HNC-8 数控系统预留的函数接口完成上位机与华中系统的数据交互,实现上位机对华中系统的控制。常用函数接口如表 1 所示。华中数控以太网通信试验针对复合加工机床控制系统,以上述软件架构进行上位机集成控制软件编写。同时完成华中数控通信接口的开发,并在复合加工机床上进行通信试验验证。
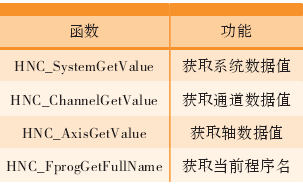
表1 华中数控系统接口函数
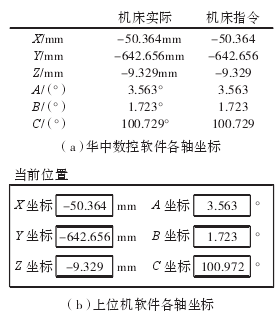
图9 通信试验结果
结果如图 9 所示,华中数控系统成功与上位机软件完成通信连接,能够执行上位机软件下发的运动指令。同时上位机软件能够读取华中数控系统当前的状态信息,并以 100ms 为
函数 功能HNC_System Get Value 获取系统数据值HNC_Channel Get Value 获取通道数据值HNC_Axis Get Value 获取轴数据值HNC_Fprog Get Full Name 获取当前程序名刷新周期在软件界面上显示。
结论
(1)对机身大部件复合加工机床控制系统进行总体架构设计,采用Ethernet 和 Ether CAT 两种通信方式实现系统由上而下的控制。
(2)华中 HNC-8 数控系统能够满足钻铆系统的运动控制要求,完成加工任务。
(3)集成控制软件运行稳定,通信响应迅速,充分发挥了其主导作用。
投稿箱:
如果您有机床行业、企业相关新闻稿件发表,或进行资讯合作,欢迎联系本网编辑部, 邮箱:skjcsc@vip.sina.com
如果您有机床行业、企业相关新闻稿件发表,或进行资讯合作,欢迎联系本网编辑部, 邮箱:skjcsc@vip.sina.com