基于UG的复杂模具零件编程技术的研究
2018-12-29 来源:宜宾职业技术学院 作者:刘 勇,宋 宁,刘存平
【摘要】结合UG软件在CAM编程模块上的强大功能,以典型的模具型腔零件为例,重点研究复杂模具零件的编程设计方法。包括制定合理的加工工艺方案,选择合适的加工刀具,正确创建加工工序。经仿真加工验证,设计有效合适的刀路,可提高工件的整体加工精度与光洁度。
关键词:UG软件;型腔;编程;设计
1 、引言
UG 是模具数控加工行业最常用的编程软件之一,具有强大可靠的刀具轨迹生成方法,可以完成铣削(2.5轴~5轴)、车削、线切割等的编程。对同类零件的编程,UG软件可设计一个编程模板与主模型相关联,当编程对象发生改变后,只需重新计算刀轨即可,提高了编程效率。数控铣削是复杂模具零件最主要的加工方法,要达到模具零件的高精度,除了要有高精密的数控加工设备以外,还需编制出高质量的数控加工程序,这是因为程序中不仅包含了零件的加工工艺过程,还包括了加工工艺参数,如切削用量、刀具形状尺寸、走刀路线等。本文以一个典型的模具型腔零件为例,介绍利用 UG 软件对其进行数控编程过程与应用的特点。
2 、零件加工工艺分析
型腔为整副模具的关键运作的精密部件,其结构形状复杂,加工难度非常大,往往制造的人工成本就超过了材料的本身 。模具型腔零件的二维、三维图如图1、图2所示,在运用UG软件对零件生成刀轨前,需对零件进行加工工艺分析,制定出合理的加工工艺方案。模具型腔零件结构形状复杂,在制定加工顺序中需充分考虑零件的结构形状、尺寸、刚度和加工精度等,选择合适的刀具切削,以先面后孔、先基准后其它、先主后次及尽量减少换刀次数提高切削效率为原则,制定出模具型腔零件的加工工艺方案。加工顺序如下:首先用 D30R4mm 刀具对其进行开粗→D12mm 刀具二次开粗→D16R0.8mm刀具半精加工平面→D8R4mm半精加工胶位与枕位,留 0.1mm 余量→D8R4mm 刀具半精加工顶面曲面,留 0.06mm 精加工余量→D12mm刀具精加工平面→D6R3mm刀具精加工胶位及枕位→D6R3mm刀具精加工顶面曲面→D6mm刀具清角加工,清 D6R3mm 加工不到位的胶位、枕位侧边→D6R3mm刀具加工流道。零件加工工艺过程如表1所示。
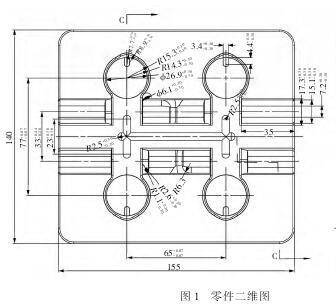
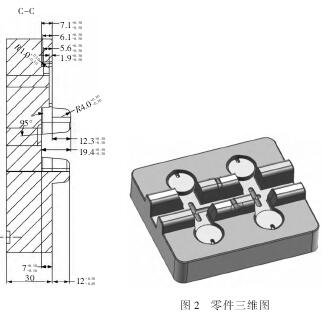
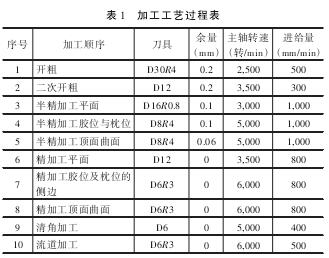
3 、编程设计
3.1 粗加工
创建粗加工工序时为了提高加工效率,在机床刚性及刀具强度允许的情况下尽量选择较大直径的切削刀具、较大的切深与进给速度对其进行切削。测量出毛坯尺寸为 157×142×45mm,编程坐标系创建在毛坯上平面中心处,粗加工工序的切削刀具为D30R4牛鼻刀,铣削方法采用[型腔铣],切削模式选择“跟随周边”,每刀切削步距为“6mm”,每刀切削深度为“2mm”,切削方向采用“逆铣”,切削顺序选用“层优先”,侧壁与底部余量统一为“0.2”;非切削参数设置中的进刀与退刀方式均采用“螺旋进刀”,主轴转速与进给速率按表1对应的参数设置,生成粗加工走刀轨迹,如图3所示。
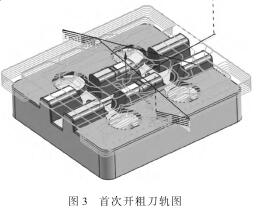
首次开粗时为了提高加工效率,一般选择的是较大直径的刀具进行切削,对于较小距离的特征区域刀具便无法进入切削。创建二次开粗工序,选择一把直径为12mm 的立铣刀对首次开粗未加工的部份进行二次开粗,铣削方法与首次开粗一致,每刀切削深度为“1.0mm”,侧壁与底部余量仍然为0.2mm,根据刀具刚性对切削用量参数进行重设。为了避免刀具对已加工面进行重复切削,将处理中的工件(IPW)选择“使用3D”,UG 软件便以先前工序切削后的模型作为此道工序的毛坯,此道工序仅加工部件上遗留的材料,生成二次开粗走刀轨迹,如图4所示。
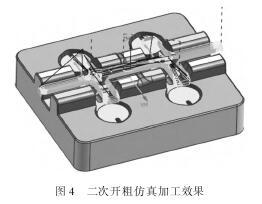
3.2 半精加工
模具零件的材料硬度很高且形状复杂,在完成粗加工后精加工前,需对各表面进行半精加工,保证精加工的切削余量均匀,提高工件各表面加工质量。各平面半精加工编程方法采用 [ 面 铣],刀具选用D16R0.8mm 牛鼻刀,加工余量为“0.1mm”,生成平面半精加工走刀轨迹,如图5所示;带有拔模角度的胶位与枕位的编程方法选用[深度轮廓加工],刀具选用D8R4mm球头刀,设置最小切削长度为“1mm”,每刀切削深度恒定为“0.15mm”部件余量为“0.1mm”,切削采用混合铣、深度优先方式,其余切削参数根据加工工艺过程表设定,生成胶位与枕位刀轨图,如图6所示;顶面曲面的半精加工编程方法采用[区域轮廓轮廓铣],驱动方法选用“区域铣削”,刀具选用 D8R4mm 球头刀,部件余量为“0.06mm”,在切削参数中指定切削方向为“顺铣”、剖切角指定与 XC 的夹角为“45°”,延伸路径在边上延伸“0.2mm”,进刀与退刀类型均采用“插削”方式,生成顶面精加工走刀轨迹,如图7所示。
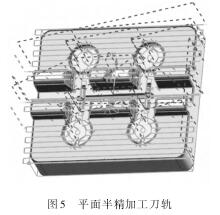
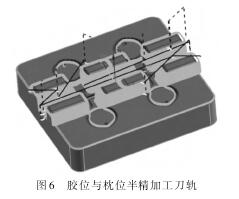
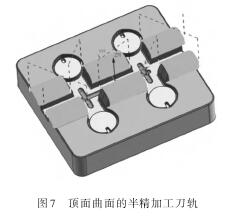
3.3 精加工
在完成半精加工后制定精加工工序时,首要考虑的是如何保证零件的尺寸精度和表面质量。精加工切削用量参照表 1 设置,用 D12mm 立铣刀精加工平面 ,编程方法采用 [ 面 铣],加 工 余 量为“0mm”;用D6R3mm球头刀精加工胶位及枕位的侧边,编程方法采用[深度轮廓加工],部件余量为“0mm”;用D6R3mm球头刀精加工顶面曲面,编程方法采用[区域轮廓铣],部件余量为为“0mm”;用 D6mm 立铣刀精根加工D6R3mm刀具加工不到位的胶位、枕位侧边及D12mm刀具加工不到的平面,清根加工刀轨如图8所示;最后对流道进行加工,加工刀具为 D6R3mm 球头刀,编程方法采用[固定轮廓铣],以流道中心拉伸一个面作为驱动曲面,驱动方法选用“曲面”,生成刀具加工轨迹,如图9所示。
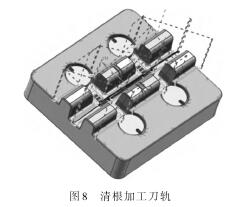
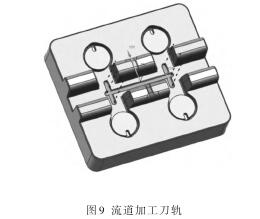
4 、仿真加工
UG 软件提供零件的仿真切削功能,能够观察刀具切削加工过程,判断是否存在干涉等情况,同时在仿真切削中,软件会给出有关的加工过程报告,这样可省去试切加工过程,降低成本,提高了加工效率。对零件进行仿真切削,仿真切削结果如图10所示,仿真加工过程中未出现干涉、欠切、过切等情况,加工结果达到了预期效果。
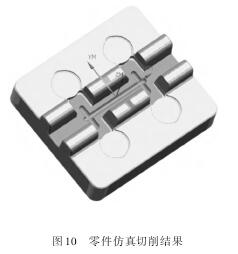
5 、结语
采用UG软件能快速方便地进行复杂模具零件的数控加工编程,并通过仿真切削功能,可实时观察零件在加工过程中出现的各种情况,减少零件的试切加工次数,降低加工成本。上述实例为典型的复杂模具零件,结合模具零件自身的特点及 UG 软件的编程方法,创建用于数控机床加工的加工工序,针对不同的加工表面选择适当的编程方法,解决了加工复杂曲面下刀难、走刀路径不易控制等问题,在提高加工效率的同时也保证了零件表面质量。
投稿箱:
如果您有机床行业、企业相关新闻稿件发表,或进行资讯合作,欢迎联系本网编辑部, 邮箱:skjcsc@vip.sina.com
如果您有机床行业、企业相关新闻稿件发表,或进行资讯合作,欢迎联系本网编辑部, 邮箱:skjcsc@vip.sina.com
更多相关信息