面向智能制造的数控机床联网技术研究
2019-4-24 来源:厦门海洋职业技术学院 南昌航空大学 作者:余运昌 杨词慧
摘 要: 针对当前制造企业数控设备与企业信息系统直连薄弱、数控系统种类较多且互不兼容、远程预警式故障诊断缺乏等问题,本研究在分析数控系统主要通信接口的基础上,提出一种面向智能制造的数控机床联网方案,解决设备层级、车间层级与企业层级的联网问题。设计的基于ESP8266的物联网低成本数控机床通信网关为实现远程DNC加工和远程、预警式故障诊断提供了硬件平台。该技术方案适合FANUC、三菱、西门子的系列化数控系统,是面向智能制造的一种低成本组网方案。
关键词: 数控系统接口;智能制造;集成数据服务器;通信网关
引言
数控技术是衡量一个国家综合国力和工业现代水平的重要指标。在“两化融合”和“中国制造2025”背景下,物联网、云计算和大数据技术得到空前发展,制造技术正经历着由自动化、数字化、网络化向智能化方向发展的过程,数控机床联网技术是制造业向智能化转型的关键技术之一。
目前,大部分数控加工制造车间的生产现状是: (1) 底层数控加工设备与企业信息系统直连环节比较薄弱,工厂数字化程度不高,不利于设备统一管理、增强加工柔性和提高效率; (2)数控系统种类较多,其接口及通信差异较大且互不兼容; (3) 远程、预警式故障机制缺乏,对于数控设备的维护通常停留在定期检修层面,无法精确进行故障排查,且设备故障维修周期较长。鉴于以上现状,本文将详细分析数控系统通信接口,提出一种基于物联网的面向智能制造的数控机床联网解决方案。设计的基于ESP8266的无线通信网关,兼容FANUC、三菱、西门子等品牌系列化数控系统,实现利用数控系统窗口功能和特定寄存器功能进行数据采集,并通过机床网关与数据服务器之间的数据交换,从而实现智能制造环境下数控机床与企业信息系统的互联互通。
1、数控系统通信接口分析
数控系统是数控机床的核心部件,可通过RS-232C接口、以太网接口、PLC的I/O接口、现场总线接口等方式与外部设备进行数据交换。
1.1 RS-232C接口串行通信接口
RS-232C是中低端数控系统与计算机通信的主要通道。通常数控加工企业采用WINPCIN软件实现数控机床与计算机之间加工程序、宏程序、PLC程序及各种参数的传输和DNC加工。该接口传输距离短,因此每台数控机床必须需配置一台计算机。数控机床的网络化通信实现了数控机床的远程DNC加工和远程设备管理,一台计算机可以管理若干台数控机床,但是需要一个RS-232接口与TCP/IP、OPC、DDE或其他网络通信接口进行协议转换的网关。
1.2 以太网接口
高端数控系统具备以太网接口,通过该接口数控机床可与计算机快速组网。数控系统公司提供的以太网专用软件可实现NC数据传输、远程控制及远程DNC加工等,但是专用软件收费昂贵且不与其它数控系统兼容,使用受到一定限制。Serv-U是一款基于FTP传输协议的服务器专用软件,数控加工企业通常将其用于远程计算机与多台数控机床之间进行NC数据传输和远程DNC加工。Serv-U软件具有高安全特性且支持多种数控系统,广泛使用于远程DNC加工。此外,通过对以太网接口进行软件二次开发还可实现数控机床远程控制、诊断、无人化操作和维修服务。
1.3 I/O接口
PLC是数控系统的辅助控制器,通过I/O接口对机械侧进行辅助控制与信号检测。采用编码式通信不仅可以节约I/O资源,还可实现PLC与其他设备进行数据交换。PLC与CNC之间可以通过特定寄存器访问和窗口功能实现控制信号、状态信号、报警信息、刀具信息、参数信息及位置信息等数据的交换。
1.4 现场总线接口
高端数控系统具有现场总线接口,用于与其他自动化设备组成现场网络。常用的总线标准主要有Profi Net、Profi Bus、CC-link、Can Bus等,不同品牌的数控系统使用的现场总线标准不同。现场总线具有数据交换的实时性、稳定性和可靠性,在自动化设备中广泛使用。总线协议转换器可以将不同总线标准的数控系统连接到同一个设备网络。
2、面向智能制造的数控机床联网设计
2.1 智能制造的内涵
智能制造是把传统的制造技术和智能技术、数字技术、网络技术相互融合,应用于产品的设计、生产、管理和服务过程,在制造过程中进行感知、分析、推理、决策、控制,实现产品需求的动态响应、产品的快速开发与优化的制造活动。工业化与信息化及互联网的融合是实现智能制造的基础,而智能制造作为一个现代化制造系统,是多个系统的融合,包括智能设计、智能生产、智能管理、智能制造服务等内容。因此,实现制造工业领域全系统、全设备、全产业链的信息互通和实现制造业数据的无缝集成是推动智能制造发展的基础。
2.2 数控机床联网方案设计
目前主要有两种机床联网方案,一种是基于DNC的数控机床联网方案,该方案采用RS-232C串行接口经接口协议转换器将串口转为以太网接口,或直接采用以太网接口将本机接入工厂局域网,主要解决车间信息集成问题,对车间的生产技术、技术准备、加工代码及加工操作等基本作业进行集中管理。这种机床联网方式虽然实现了远程DNC加工与管理,但是对机床本身的运行状态、刀具信息、故障状态等无法知晓,不利于智能制造技术的推广与发展。另一种是基于物联网技术的数控机床故障诊断,该方案具有远程、预警式故障机制,但是各种故障判定均基于相应的Zigbee传感器检测模块,忽略了数控系统本身丰富的故障诊断功能和PLC故障诊断方法,在远程DNC加工与管理方面缺乏。
鉴于现有数控机床联网方案的不足,为适应智能制造发展趋势,本文提出一种面向智能制造的数控机床联网方案,将数控加工生产企业中的网络根据职能不同分为3个网络层级,分别为基于互联网的企业资源管理网络(企业层)、基于局域网的制造执行系统网络(车间层)和基于工业现场网络的现场控制系统网络(设备层),如图1所示。
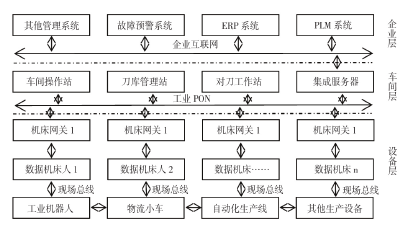
图1 面向智能制造的数控机床网络结构
数控机床、工业机器人、物流小车、自动化生产线、智能仓储等生产设备直接参与生产,各设备通常采用PLC实现逻辑控制。现场总线是一种开放式、全分布控制系统的基层网络,具有协议简单、容错能力强、安全性好、成本低廉、实时性高及网络负载稳定等优点,广泛应用于上述自动化现场生产设备中。现行典型的工业现场总线有FF(基金会总线)、Profibus、Profi Net、World FIP、CC-Link、CAN、Lon Works等。有两种方法实现不同总线协议之间的转换,一种是在设备之间增加嵌入式一对一协议转换网关,如西门子的PN-DP耦合器实现Profibus与Profi Net总线的连接;另一种是基于协议栈的现场总线协议转换通用化设计网关。
各种数控机床、对刀工作站、刀库管理站、操作站等作为客户端与企业集成数据服务器共同组建成制造执行层网络,其中数控机床是制造执行层与现场控制层之间进行数据交换的桥梁。工业以太网具有技术先进性、成熟性和协议经标准化的优点,在工业领域受到广泛的应用,但是因其抗干扰能力弱、业务支撑能力不足、维护困难及仅支持点到点直连组网的缺点,其应用受到一定的限制。本方案采用工业无源光网络技术(PON)将制造执行层内的各种设备进行组网,因为PON通过无源器件组网,采用点到多点的树形拓扑传输架构,具有抗干扰能力强、业务承载范围广、成本低、维护简单、容易扩展、易于升级及安全性高等特点,是车间通信组网技术的一种全新方案。
数据服务器作为企业内部的云平台,主要集成了数控加工程序管理模块、刀具信息管理模块、生产设备数据采集与管理模块、数据访问模块、设备访问模块等,提供基于RPC的灵活通信接口与主控计算机进行数据交换,是车间局域网与企业互联网之间的信息枢纽中心。产品生命周期管理系统(PLM)可以直接访问数控加工程序管理模块、刀具信息管理模块,进一步优化车间生产过程的管理;远程设备故障诊断与预警中心通过访问数据采集与管理模块和设备访问模块,获取现场设备的状态数据、运行数据、报警数据、加工数据等,在进行大数据分析后生成特定的故障排除方法和设备维护建议,通知用户及时进行故障排除或及进行设备维护,减少停机时间,提高设备利用率。
产品生命周期管理(PLM)、企业资源计划(ERP)、供应链管理(SCM)、客户关系管理(CRM)、电子商务(EC)等技术是制造企业管理不可缺少的组成部分,运行在企业互联网层,负责车间与企业其他部门、外部相关企业的联系,以便传递任务、发布信息和查询数据等。智能制造要求网络体系更加开放,因此必须通过综合性的安全防护措施保证网络和数据的安全。智能设备与数据服务器之间、企业外部与企业内部云平台之间应设置防火墙进行有效安全的隔离与控制,同时DDo S防御功能、网络入侵防护系统也应纳入网络安全保护。对所有接入企业内部云平台、信息系统、服务器及控制系统的设备必须进行接入认证和访问授权。对企业外部网络传输的数据,采用VPN隧道传输机制或VPN专网技术,防止数据泄露或被篡改。
3、数控机床网关设计
以上面向智能制造的数控机床网络结构中,机床网关是数控机床联网的核心部件。本文设计的机床网关兼容FANUC、三菱、西门子等主要品牌的系列化数控系统,充分利用数控系统自身的串行通信功能和自诊断功能实现远程DNC加工和远程、预警式故障诊断。
3.1 硬件结构设计
图2是适合多种数控系统的机床网关硬件结构。在远程DNC加工方面,具备以太网功能的数控机床经RJ45接口直接接入工业级路由器,而仅支持RS-232通信的数控机床经串口转以太网模块接入工业级无线路由器,如图2a所示。在远程、预警式故障诊断方面,数控系统本身具有丰富的信息,通过系统PLC单元的窗口功能和特定寄存器功能对系统信息、状态信息、刀具信息、坐标信息、诊断数据、当前运行程序段及各电机的负载数据等进行数据采集,并将采集数据通过编码式通信[7]发送到本网关,采集数据经处理器解析、存储与转换后由WIFI模块发送到互联网,如图2b所示。微处理器IAP15W4K61S4具有4 K的SRAM和4个串口,是本网关的核心模块,负责实现协议的转换、管理、安全等各方面的数据处理和存储。ESP8266模块内置TCP/IP协议栈,支持多路TCP Client连接和无线802.11b/g/n标准,具有高集成度、低功耗和
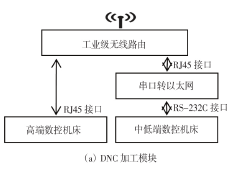
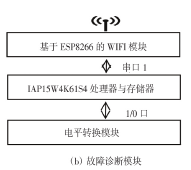
图2 数控机床网关硬件结构
易用性的特点,负责实现处理器串口数据与网络协议数据的转换。电平转换电路负责I/O模块的24V电平与TTL电平的转换。
3.2 软件结构设计
软件结构采用模块化设计思想并用C语言编写各模块程序。图3是数控机床网关软件程序流程图,系统上电后对硬件驱动进行初始化,采用Smart Config一键配置功能对ESP8266进行网络配置,建立网关与数据服务器的连接并进入数据透传模式。网关与PLC之间的通信采用编码方式,与服务器及其他传感器模块之间的数据通信采用TLV(Type、Length、Value)数据格式模型。数据帧由帧头、帧类型、帧长度、数据包及帧尾组成。帧头采用0x55,0x AA,0x7E 3个固定字节,帧类型和帧长分别由一个字节组成,数据校验采用异或校验、CRC16校验双重校验以保证通信的可靠传输,帧尾采用0XD0结束一帧数据的传输。
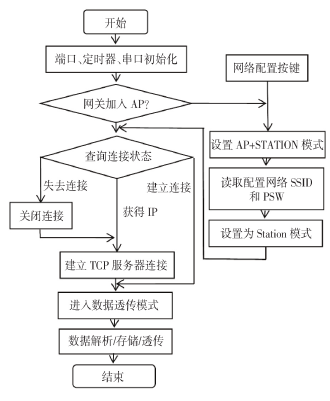
图3 网关程序流程图
4、结论
本研究针对目前数控加工企业的实际现状及面向智能制造的需求,在分析了数控系统的通信接口基础上,提出了面向智能制造的数控机床联网方案。设计的基于物联网的数控机床网关能适应多种数控系统共存,如FANUC、三菱、西门子的系列化数控系统,利用数控系统的窗口功能和特定寄存器功能对数控机床进行信息数据采集,为智能制造环境下数控机床联网提供了一种低成本组网方案
投稿箱:
如果您有机床行业、企业相关新闻稿件发表,或进行资讯合作,欢迎联系本网编辑部, 邮箱:skjcsc@vip.sina.com
如果您有机床行业、企业相关新闻稿件发表,或进行资讯合作,欢迎联系本网编辑部, 邮箱:skjcsc@vip.sina.com
更多相关信息