在西门子840Dsl数控系统中实现进给轴全环多级变速
2020-8-12 来源:中国一重集团有限公司 作者: 樊 凯
【摘要】介绍在数控机床改造中,采用西门子840Dsl数控系统如何实现进给轴全闭环多级变速应用。
在国外老的进口机床中进给轴采用多级变速的比较常见,如科堡20-10FP225龙门铣床X轴(工作台移动)进给分2级变速,SKODA产D-SIU400型重型卧车及SKODA产SUT200型重型卧车X轴、Z轴进给分2级变速。在这些数控机床应用西门子840DSL数控系统升级改造中,全闭环进给轴多级变速就成为我们研究的课题了。
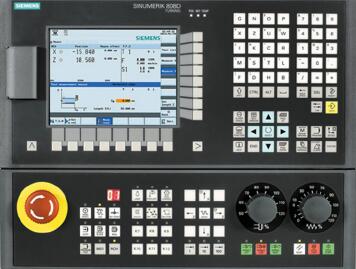
一、课题的重要性
主轴变速功能在所有使用ISO代码的数控系统中都规定了一些特定代码和功能,比如西门子840D系列中,辅助应答代码M41-M45分别代表了主轴的I、II、III、IV、V档,这些档位的传动比参数可以提前预设写入,为31050和31060的(0-6)中,当主轴变速完成后,对应接口信号(DB31--DB3n).DBX16.3为1,同时(DB31--DB3n).DBX16.0、(DB31--DB3n).DB16.1、(DB31--DB3n).DBX16.2组合起来反馈当前档位信号,读取对应档位的传动比和对应档位的最大速度值,则所有参数都能匹配起来,档位变换产生的轮廓偏差、定位误差等都可分别调整,可以实现加工编程中的多级转速变换。
进给轴多级变换功能则没那么容易实现,因为840D系统中没有在参数设计中充分考虑进给轴多级变速功能,对于进给轴变速后的最大进给速度、加速度、定位误差、轮廓偏差、伺服增益系数、传动比等都没有设置对应档位的参数组,最最关键的问题是,西门子没有相应的接口信号通知NC系统该进给轴当前档位,无法将实际档位与机床参数有机结合起来,那么就会出现这种情况,就是进给轴变速后,由于NC无法得知,但速度变化引发的轮廓偏差、定位误差等会让进给轴频繁报警,无法工作。当然了,变速完成后,手动去输入所有相关参数是可以的,但是,这种频次高的改动即不安全可靠又费时费力,因此,不是长久之计。
那么,进给轴多级变速是否有必要保留呢?在现代新机床设计中,进给轴多级速度很少看到,因为在新机床设计中,通过电机功率、转速、传动比、安装空间匹配,可以满足一台机床的所有加工需求,不需要进给轴有机械变速。但是,在一些进口旧机床改造中,设计理念不够先进的情况下还是应用了进给轴变速。比如以我们改造的一台SKODA产SUT200型重型卧车为例,原来通过I级变速增
大输出转矩、降低进给速度,用于粗加工;通过II级变速提高进给速度、降低输出转矩,用于精加工。做改造方案时,如果只保留一个档位,由于电机安装空间极其狭窄,可选择的伺服电机不能满足原有加工需求,要么进给速度太低,要么输出转矩不够,机床的改造就不能取得满意的效果,所以,必须实现进给轴的多级变速。
在我们最近的数控机床改造过程中,接连发现了三例这种问题,于是,如何平滑稳定实现进给轴多级变速,而且使位置环不报警,这就成了一个重要的问题。经过多次摸索,我们终于攻克了这个难题。
二、解决方案
以SUT200型数控卧车为例,刀台X、Z分别都具有两级变速,其中,X轴电机自带编码器,外置光栅尺,I级传动比为1:18,II级传动比为1:3;Z轴电机自带编码器,外置一个编码器作位置环,位置环编码器自带一个减速箱,I级传动比为1:6,II级传动比为1:2,位置环编码器传动箱传动比为2:5。这两种情况代表了两种非常典型的全环方式,分别以这两种情况描述进给轴多级变速的实现。
情况一:光栅尺作位置环,以X轴为例
实现步骤:
(1)检查传动比。若机械能够确切推算传动比,则可省略此步。进行此步的前提是,与传动比相关的31050(负载齿轮箱分母)、31060(负载齿轮箱分子)、31064(附加齿轮箱分母)、31066(附加齿轮箱分子)这几个参数必须设置为默认值1, 31030(滚珠丝杠螺距)也按默认值10设置,反向间隙补偿32450清掉,且X轴应激活的是不带光栅尺的第一测量系统(DB31.DBX1.5=1)。前置条件满足后,X轴切换到I级,在X轴终端压上一块百分表,向一个方向开1mm,此时可消除反向间隙,然后百分表清零,再向前开1mm,观察实际百分表的计数,比如实际百分表动0.2mm,则传动比为1:0.2=5:1,将此传动比写入31064、31066,然后再压百分表,看是否准确,如果有微量误差,将传动比细分为500:101、5000:999等进行尝试,直到误差进一步减小到可忽略不计。如果追求更加精确的数显精度,可以通过激光干涉仪进行螺距误差补偿(LEC)。记录下I级的传动比,然后切换到II级,将31064、31066清掉,重新进行上述步骤,得到II级的传动比。这里需要特别说明的是,为什么传动比写入31064、31066,而不写入31050、31060?因为31064、31066的生效方式是CF(NEW CONFIG),不需停电重启,而31050、31060的生效方式是PO(POWER ON),需要停电重启。
(2)建立定义文件。得到I、II级的传动比后,开始写定义文件。在840Dsl的“调试”菜单里找到“系统数据”菜单,再找到“定义”文件夹。在该文件夹内新建一个定义文件,默认客户自定义文件名为MMAC.DEF,可任意定义文件名,打开该文件,在该文件内写入如下内容:DEF M51 AS MLX1;书写M51调用MLX1.SPF子程序。
DEF M52 AS MLX2 ;书写M52调用MLX2.SPF子程序。
然后保存退出,则系统开始自动编译该定义文件,如果文件内容书写无错误,则编译可顺利通过,若编译不通过,请检查书写。这里,MLX1.SPF为X轴I级变速子程序,MLX2.SPF为X轴II级变速子程序。
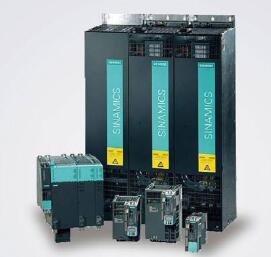
(3)建立变速子程序。定义文件建立后,可以在“制造商循环”文件夹内建立MLX1、MLX2变速启动子程序。该子程序的作用有两个,一个是驱动PLC程序进行变速执行元件的动作,比如离合器、电磁阀等;一个是写变速相关参数,包括传动比、伺服增益系数、最大进给速度等。子程序以MLX1.SPF为例,书写子程序如下:

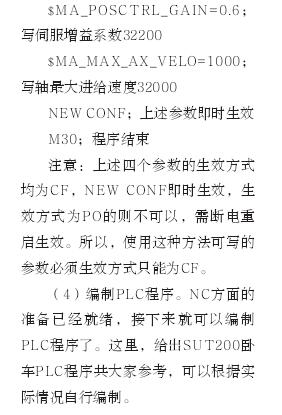
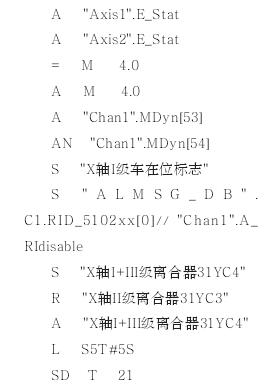
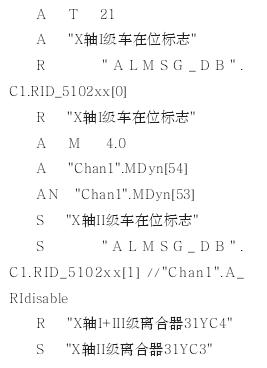
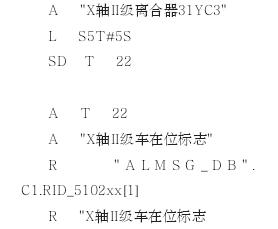
(5)全环试车。上述步骤完成后,则可以进行半环试车,可以看到,当在MDA方式下执行M51时,则31064、31066、32200、32000等自动按照MLX1.SPF(I档)内设置而更改;执行M52时,上述参数按照MLX2.SPF(II档)内设置而更改。在I档、II档速度下,明显可以看到同样的电机速度,驱动X轴的速度已经按传动比切换过来。此时,可以激活带光栅尺的第二测量系统(DB31.DBX1.6=1)。按照常规设置,将31000(是否光栅尺)、31040(位置环检测是否直接安装到机床上而没有中间变速)均设置为1,全环设置完成。注意,若31040为0,则NCU会检测31050、31060的数值,当挂光栅尺时,会出现轮廓监控报警、不受控制等现象。由于光栅尺直连,31070(编码器齿轮箱分母)、31080(编码器齿轮箱分子)默认为1即可。
情况二:编码器外带减速箱做位置环,以Z轴为例。
实现步骤与上面完全一样,但设置参数有略微差别。31000、31040必须设置为0,同时,31044(编码器是否有中间变速)必须设置为1。由于编码器中间有传动比,那么31070、31080必须设置。
三、 结语
经过以上设计,完全实现了在840DSL下用M代码或面板自定义键实现进给轴的多级变速切换,保障了机床原设计功能,增强了机床的可操做性,满足了机床各种加工生产需求,这种应用值得其他同行借鉴及推广。
投稿箱:
如果您有机床行业、企业相关新闻稿件发表,或进行资讯合作,欢迎联系本网编辑部, 邮箱:skjcsc@vip.sina.com
如果您有机床行业、企业相关新闻稿件发表,或进行资讯合作,欢迎联系本网编辑部, 邮箱:skjcsc@vip.sina.com
更多相关信息