重型金属3D打印技术产业化应用取得突破
2015-7-2 来源: 作者:
从风扇产业到核电风机领域,南方风机股份已经成为国内核电通风设备的龙头企业,如今又向“工业级3D打印”领域尝试二次创业。日前,民生证券调研南风股份后发布报告称,南方增材(南风股份子公司)与上海核工程研究设计院的合同产品—核电主蒸汽管道贯穿件样品已经完成。
如果样品检验合格,该技术将大大提高核电站安全性能,并缩短建设周期。若加上核电站核岛核心部件,市场价值可达数百亿元。这一技术也是佛山重工业发展史上的一次重大突破,对佛山实现万亿装备制造业的产业目标具有积极意义。
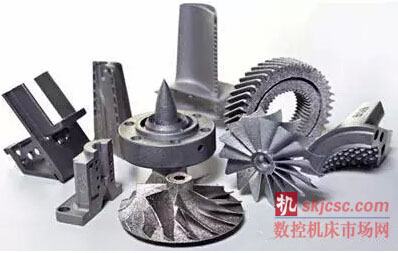
一.联手领军人才二次创业
南风股份相关负责人介绍,在国内核电风机设备领域,南风股份的设备市场占有率已超过70%,但主营风机业务受到国家核电发展的环境影响,企业处于一种被动式跟随状态。
由于国内核电风机设备领域的市场空间存在“天花板”,再加上风机的制造方面已经很难有大的突破,企业决定寻求新的突破。
处于核电装备领域的南风股份发现,在国内核电站建设过程中,目前核心部件的制造技术仍掌握在国外企业手中,核电站设备部分部件高度依赖进口。以核电站的大型铸锻件为例,其核心技术主要集中在日韩和欧洲,中国企业与其有差距,部分大型、复杂铸锻件尚未攻关成功,只能依靠进口,关键时候还受到其对中国出口的限制,一定程度上影响了项目的建设进程。
“打造一个大型锻件要几百吨钢材和三年的时间,做完后只要检验不合格,几千万元就打水漂了。”南方增材总经理朱志宇说,传统的锻造工艺要求高,流程复杂,生产周期长,需要多套设备配套完成,导致核电成本居高不下。
高端技术人才资源是企业创新的第一资源。2009年底,南风股份的技术团队在北京遇到了北京航空航天大学教授王华明。王华明是航空材料与结构研究部首席科学家、国内激光制造的学术带头人。此前,飞机大型结构件的生产采用传统的锻造和机械加工等方法,光大型模具的加工就要用一年以上的时间。模具加工出来后,再用它锻造出一个大型结构件的毛坯,然后继续加工各部位的细节,等到最后成形,几乎90%的材料都被切削、浪费。
王华明创新了一条截然不同的道路,通过计算机控制,用激光将合金粉末熔化,一层层堆积起来,高效率地“生长”出一个合金部件。
南风股份与王华明在开发金属3D打印技术上进行合作。两者合资成立南方增材公司,成立了“重型金属构件电熔精密成型技术项目”,面向民用领域,王华明团队持有31%股份。“王华明教授带领公司技术团队,自主研发了重金属3D打印技术,是高端重大工业装备中大型、特大型关键构件制造方式的一项变革性技术。”朱志宇说。
二.填补重型金属3D打印空白
王华明核心技术团队经过上百次实验后,在关键技术上取得了突破性进展,并在实验室成功做出了物理、化学性能皆优于锻件的核电重型装备的金属构件缩比件。
重型金属3D打印技术产业化应用的突破,在国内属于空白。在3D打印的应用领域,核电又是一块处女地。南方增材相关负责人表示,重型金属3D打印技术是一种国际首创的重型金属构件短流程、绿色、精密、数字化的增材制造新技术,可广泛应用于百万千瓦核电装备、百万千瓦超临界和超超临界火电机组,以及水电、石化、冶金、船舶等现代重大工业装备合金钢等重型金属构件的制造。
“我们在材料、设备、工艺研发设计上,整套流程都拥有自主知识产权。我们通过国家专利局检索了这个领域的所有相关信息,国内外没有发现与我们技术相似的。”朱志宇表示。
相比起传统铸造工艺,增材制造技术的优势在于“轻装备”,只要一台3D打印机,一道高温电熔的“打印”工序即可见成品。而在传统锻造工艺中,如果要制作一件50吨的核电部件,至少需要180吨的钢锭材料,放入200吨以上的电弧炉进行冶炼浇注,还要经过万吨以上机器的锻造和热处理,多达十几道工序需要耗时6个月以上。
目前,核电站的建设周期是60个月。引入增材制造技术制造重型金属构件,整个周期可以压缩到50个月。
朱志宇认为,以前发展核电站的瓶颈是造价高,因而电价也高,现在压缩周期后电价会比火力发电低;另外,南方增材瞄准的是核电装备,涉及传统重工业行业这个新技术的应用,提升了产品的性能,也提高了安全等级。
三.推动3D打印在制造中应用
经过30多年的快速发展,珠江西岸已发展成为广东省重要的装备制造业生产基地,初步形成了产业特色鲜明、具有一定规模和技术水平的装备制造业体系,为发展先进装备制造业奠定了坚实的基础。《佛山市打造万亿规模先进装备制造业产业基地工作方案》要求加快工业机器人、3D打印等先进制造技术在生产过程中的应用。
今年年初,南方风机股份控股子公司南方增材与上海核工程研究设计院签订了《核电主蒸汽管道贯穿件模拟件增材制造技术支持与服务合同》。在合作的基础上,2015年,企业将完成模拟件的验证,通过实验数据验证模拟件可取代传统冶炼、锻造工艺制造的产品,在力学、性能等指标上达到核工业领域的标准。
“核电代表工业最高领域,如果顺利达到了各项标准,这样一项全新工艺就可以在其他装备领域的生产制造中运用。”朱志宇称。
增材制造技术在核电部件制造上得到突破后,压力容器、蒸汽发生器、稳压器等大量核反应堆中的核心部件都能通过增材制造进行生产。以核心部件蒸汽发生器的管板为例,朱志宇称,这一项的市场价值就超过20亿美金,再加上核电站核岛核心部件,市场价值可达数百亿元。
“通过3D打印,我们可以根据客户需要,完成不同构件的个性化定制,特别是装备业中一些关键的金属异形件,也可尝试进行突破。”南方增材总经理助理李春华说道。
近年来,增材制造、新材料、大数据等技术突破和广泛应用,正推动制造业生产方式的深刻变革。李春华表示,不远的将来,金属增材制造将是佛山重工业发展的一次重大突破,对佛山打造万亿装备制造业的产业目标具有积极意义。
投稿箱:
如果您有机床行业、企业相关新闻稿件发表,或进行资讯合作,欢迎联系本网编辑部, 邮箱:skjcsc@vip.sina.com
如果您有机床行业、企业相关新闻稿件发表,或进行资讯合作,欢迎联系本网编辑部, 邮箱:skjcsc@vip.sina.com
更多相关信息