APM系列翻板卧式加工中心的研发与应用
2016-2-17 来源:济南二机床集团公司 作者:任立伟
APM系列翻板卧式加工中心项目是由济南二机床集团承担的,成都飞机、西安飞机、清华大学、北京航空航天大学共同参与研究的国家科技重大专项课题,应用于航空大型铝合金结构件高速高效加工。机床主机采用落地式结构、高速大功率主轴;配K大型翻板工作台,实现零件在水平位置装夹、垂直位置加工的工艺目的。整机加工区全封闭防护,实现绿色安全加工。机床搭载毛坯测量与加工余量分析系统和接触式原位检测系统,实现毛坯的虚拟划线和零件的在线检測。机床主要性能和技术指标达到国际先进水平。
一、研发H的
飞机上95%的金厲结构件需要数控机床加工,由于有强度高、重M•轻、耐腐蚀等特殊要求,多为深槽腔、小转角、薄壁、具有气动理论曲面的盒形结构。通常采用“整体制造法”,即毛坯为板材、锻件和铝合金挤压型材,通过加工形成薄壁、细筋等结构。统计数据表明,一个金厲零件从毛坯加工到成品,材料的利用率仅为原材料的20% ~10%甚至只有5%,其余80% ~90%甚至95%的材料都成了切屑。由于飞机结构件的上述工艺特点,为了缩短零件加工占用的大M时间,必须采用高速高效铣削技术。另外,随着切削速度的提高,切削力会随之下降,在高速切削范围内机床的激振频率远离加工工艺系统的固有频率范围,而切削产生的热量绝大部分也被切屑带走。因此,高速高效铣削技术可以最大程度地减少加工中径向切削力、共振和热变形对加工工艺系统的影响。
采用高速高效铣削技术后,加工工艺系统的落屑和排屑成为问题的焦点。典型的铝合金零件高速加工,每分钟就能产生多达数千立方厘米的切屑。传统的立式加工工艺系统,越来越不能满足用户的需求。这类系统,由于工件水平放置,加工过程中产生的大fi高温切屑堆积在薄壁型腔中无法及时顺利排出,并将热量传递给工件、刀具和主轴,导致整个加工工艺系统产生二次热变形。切屑的堆积,还会产生二次切削效应,加剧刀具的磨损,并影响工件的最终加工质量。
为便于落屑、排屑,避免上述不利的结果,必须转变工艺思路:由工件在水平位置完成整个定位装夹和加工过程,转换为工件在水平位a完成定位装夹,然后在垂直位a完成加工。这样可以集立式、卧式机床的优势为一体(见图1)。加工设备也考虑由水平工作台加立式主轴布局特征的龙门式加工中心,转换为翻板式工作台加卧式主轴布局特征的翻板卧式加工中心。翻板卧式加工中心不仅便于落屑排屑,而且易于实现切削加工工作区全封闭设计,实现了绿色安全加工。卧式的主机结构还便于构建FMC或FMS�
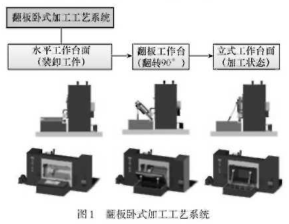
综上所述,APM系列翻板卧式加工中心就是根据飞机制造企业的工艺及设备®求,为其量身定做的专用高档数控机床和解决方案。
二、主要技水参数
工作台规格(宽度x长度):2000mm x4_mm�2000.ii.il x 6000mm (或根据用户要求定制)。主轴功率60kW�最高转速24000r/miri�X/17Z进给速度5 ~ 20000mm/miri�机床定位精度(X/Y/Z ) � O.OlOmni/m,重复定位精度�X/Y/Z� 0.010mm,翻板重复定位精度0. 020mm�
三、关键技术创新
机床整体结构布局采用立柱移动式的主机结构。立柱沿X轴方向横向左右移动,采用双齿轮齿条传动;主轴箱沿y轴垂直上下移动,采用双丝杠驱动;滑枕沿z轴前后水平移动,采用丝杠驱动。配置可90°翻转的大型翻板工作台,通过双丝杠同步驱动实现翻板工作台翻转。翻板工作台翻转到位后采用楔块定位,液压夹紧,钩锁防松确保翻板工作台安全可靠。
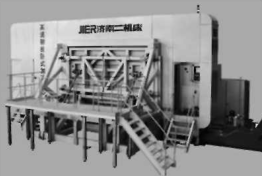
图2翻版卧式加工中心外观图(图中翻板工作台处于加工位置)
1.机床全部大件均采用钢板焊接件,保证
机床具有良好的刚度质量比床身是机床的基础部件,要求具有良好承载能力和稳定性。设计采用箱式焊接结构,受力中心通过主壁板,使之具有良好的承载能力和刚性。立柱是移动部件,在具有良好刚性的同时,要求尽可能地减轻质姑,以满足高速运动的耑要。设计采用双层壁板焊接结构,合理布筋,开孔减重,满足加速度等动态性能设计指标。
滑枕采用八边形焊接结构设计。与传统方形滑枕对比,在相同切削力作用下,八边形结构滑枕具有更好的刚度,因而变形更小。
溜板主承重壁板采用箱式焊接结构,承载导轨设支撑壁板也形成箱型结构,因而具有良好的刚性。
翻板工作台及其支撑结构均采用钢板焊接结构。采用型钢组焊,相对于钢板焊接,焊接应力小,桁度稳定。
2.基于数字化样机设计进行考虑结合面特性的整机有限元分析,实现机床动静态性能优化设计
在设计阶段,基于数字化样机,对机床整体性能进行预估。采用考虑典型结合面特性的机床整机有限元分析方法,并通过实验对仿真结果进行验证,进而获取机床整机性能参数,为机床性能设计提出优化建议。分析中考虑了三向导轨结合面、丝杠螺母接合面、齿轮齿条结合面、主轴套筒结合面、套筒滑枕结合面等结合面特点,分析影响结合面特性的主要因素,确定结合面参数,进而建立考虑结合面特性的整机有限元仿真模型。通过这种方法,对机床加工过程中不同位置、不同工况下整机的静动热态性能进行仿真研究,识别机动热态性能的薄弱环节并进行优化。计算分析的结果已经在产品研制中得到了部分应用和验证。
3.进给轴采用高刚度设计,满足机床高速高精性能的需要
X轴传动采用双齿轮齿条传动,双电机电气消隙。该传动机构安装在立柱上,由西门子交流伺服电机经精密减速箱降速后带动立柱沿床身导轨移动。该传动采用通用型齿轮齿条,结构简单,可靠性好,制造调试维修方便,可实现正常磨损的自动补偿,保证机床长期高精度稳定运行。F轴传动采用双丝杠重心驱动,滚珠丝杠采用消除间隙的预双螺母的结构形式。由西门子交流伺服电机驱动,经减速筘降速后,通过滚珠丝杠旋转带动主轴箱上下运动。y轴承担溜板及滑枕的上下移动,需克服较大质量的影响,采用双丝杠驱动,可以提高传动刚性,满足快速响应。
z轴采用丝杠驱动,滚珠丝杠采用消除间隙的预载双螺母的结构形式。由西门子交流伺服电机驱动,经一级同步带降速后,通过滚珠丝杠旋转带动滑枕前后运动。
各轴传动链短、刚度大,使机床具有良好的增益特性、加速度性能,以满足高速高精加工的需要。
4.采用大功率电主轴配置,满足铝合金零件的高效加工需求
主轴采用60kW大功率高速电主轴,最高速度可达ZAOOOr/min�主轴支承采用大接触角高速角接触球轴承,滚动体为耐髙温陶瓷球,以适应轴承高速运行。刀柄采用HSK-A63标准,主轴采用碟簧拉刀-液压刀,动作准确可靠,有专用传感器用于检测刀具的松、拉、空刀位。电主轴具有自动刀柄吹气功能,以便在换刀时用压缩空气对主轴锥孔和刀具锥柄进行清洁。主轴在运转时发热S很大,为防止其过热烧坏线圈或轴承,在电主轴的定子和主轴轴承套的外壁有液冷螺旋循环套,经过水冷机降温的液体通过其中,带走热量;同时,在电主轴内部设有温度传感器,实现电主轴的温控电气联锁。主轴具有主轴中心出水及外冷功能。主轴套筒采用树脂砂造型、高强度无应力铸铁件。套筒采用锥形结构,保证套筒具有较高的抗弯及抗扭刚度。
5.双丝杠驱动型翻板工作台,具有良好旳重复定位精度和精度保持性
翻板工作台S于主轴的对面,可完成水平和竖直状态的自动转换并定位夹紧,方便工件的装夹。翻板工作台翻转运动采用消除间隙的预载双螺母双滚珠丝杠传动。西门子交流伺服电机经梢密减速箱降速后,带动滚珠丝杠螺母旋转,推动翻板工作台实现其翻转运动。翻板工作台定位夹紧:翻板工作台由水平位a翻转到竖直位a后通过V型块进行定位,然后接着旋转液压缸旋转90°后夹紧翻板工作台,气缸推动防松钩锁动作勾住翻板台,确保工作台不会意外翻落。当翻板工作台由竖直位置向水平位置翻转时,首先气缸拉动放松钩锁松开,接着旋转夹紧液压缸旋转90。松开翻板工作台,然后滚珠丝杠副驱动翻板工作台翻转至水平位置。双丝杠驱动同步性好,工作台扭转变形小,精度保持性好;楔块定位机构保证工作台具有良好的重复定位精度。
6.机床搭载形貌测量系统和原位检测系统,实现毛坯的虚拟划线和零件的在线检测
某些大型航空结构件的毛坯采用桁铸件和模锻件,限于目前国内祷造和模锻的整体工艺水平,精铸件和模锻件的桁确尺寸控制还是一个难题。毛坯加工中还需人工划线,加工余量分配缺乏量化测量和分析手段。加工余量不均易导致加工出现欠切而报废,严重影响产品的质量和制造周期,造成浪费。形貌测a系统实三维视觉传感器、国产数控系统、计算机与数控机床的集成,构成航空结构件毛坯测量与加工余a分析系统。原位检测系统可以实现零件模型和测黾点的三维实时仿真,根据检测规划文件生成数控机床可执行的NC测量文件,实现检测软件与数控系统的机床通讯。对数控系统上传的测量数据进行误差补偿、质m评价,生成测i报告。根据误差快速辨识方法,建立误差补偿模型,研发原位检测系统标定技术,对测量数据进行误差补偿,消除整体测:a误差。针对大型飞机结构件数控加工过程的特点,实现加工测量一体化应用。
7.全封闭防护设计,实现安全绿色切削
翻板卧式加工中心属于高速、高效加工机床。由于主轴商速旋转,切削液雾化严重,需要进行封闭防护,以防危害操作者、污染环境。机床主轴转速可以高达24000r/min,加工时铝屑会带着高温快速飞出,对机床操作者构成危险。高速加工时,刀具可能存在的断裂、解体等更高的危险,需要对机床进行全封闭防护。机床高速切削时会产生噪声,是另一个污染源,也需要对机床进行隔音处理。
翻板式加工中心对主机和翻板工作台之间的空间进行全封闭防护构建,使之形成一个封闭的加工区域,与操作区域和外部区域完全隔离。在封闭的加工区域顶部开设三个吸风口,配置吸雾器将水雾吸走。吸雾器底部设有排液口,将液化后的水雾排至切削液水箱,实现重复利用。
x轴和y轴采用壁式防护系统。x轴采用铝帘式防护结构,f轴采用铠甲式防护结构。考虑到r轴移动范围较大,对于x轴的壁式防护左右两侧设有铝帘卷筒,对卷帘进行支撑、回收或释放。机床配S旋转视窗,便于操作者对加工区域进行观察。旋转视窗由一个固定部分加一个高速旋转的玻璃结构元件组成。高速旋转的玻璃体将飞溅到上面的冷却液及切肩通过离心力的作用向外甩掉,以保证玻璃体的透明度。
加工区域配K随动式高清摄像头,可自动跟随主轴的移动,实时显示在外ft显示器上,对加工过程进行监控。
四、成果应用及推广
2014年4月,APM系列翻板卧式加工中心的第一台样机研制完成,并成功参加了第八届中国数控机床展览会,引起众多关注。为推进该型产品在航空航天工业的应用,2014年10月,济南二机床集团举办了 APM系列翻板卧式加工中心技术研讨会,来自成都飞机、沈阳飞机、西安飞机、哈尔滨飞机、洪都航空、上海飞机、天津航天长征火箭公司、上海航天设备制造总厂、长征机械厂等18家航空航天企业50余人参加了会议,就技术研发和应用进行了研讨。
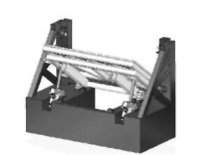
图3翻板卧式加工中心切削的模拟试件
未来,根据用户的耑求,在翻板卧式加工中心产品系列中,济南二机床将继续研发并推出配a自主知识产权数控双摆角万能铣头(五轴头)的五轴联动翻板卧式加工中心、适应于钛合金加工的重型翻板卧式加工中心、自动化程度更高的 带有交换工作台的翻板卧式加工单元、配置有自动物流输送系统的翻板卧式加工柔性生产线等飞机大型结构件加工专用高档数控机床,满足航空工业对翻板卧式加工工艺系统的大量需求,降低 企业采购成本,提高经济效益,保障国家安全。
投稿箱:
如果您有机床行业、企业相关新闻稿件发表,或进行资讯合作,欢迎联系本网编辑部, 邮箱:skjcsc@vip.sina.com
如果您有机床行业、企业相关新闻稿件发表,或进行资讯合作,欢迎联系本网编辑部, 邮箱:skjcsc@vip.sina.com
更多相关信息