CO2激光切割LTCC基板工艺技术研究
2016-10-12 来源: 中国电子科技集团公司第三十八研究 作者:王运龙,宋夏,邱颖霞,王志勤
摘要:针对LTCC基板进行CO2激光切割实验研究。分析激光功率、激光频率、切割速度及辅助气体压力等参数对切割宽度、深度及飞溅物的影响。阐述了LTCC中金属导体对切割的阻碍作用以及CO2激光的热效应对LTCC表层导体形貌及附着力的影响。
关键词:CO2激光;LTCC基板;切割
低温共烧陶瓷(Low Temperature Co-firedCeramics,LTCC)采用低温烧结陶瓷生料带为电介质层,Au、Ag或Cu等高电导率的金属为导电材料,通过在生料带上先打孔,然后进行导体填孔和表面电路印刷,经叠片和层压实现多层印刷电路图形的立体累加和互联,最后在低于900 ℃的温度条件下可烧结制成三维空间高密度电路基板[1]。LTCC技术结合了电子电路厚膜技术和金属导体-陶瓷共烧技术,基板烧制温度低,呈现优异的高频高Q 特性,传输损耗低,具有较好的温度特性,可实现无源元件埋置,产品集成密度高,易于实现多层布线与封装的一体化结构[2]。由于LTCC优异的性能,目前已被广泛应用于通信、射频/微波领域、相控阵雷达的T/R模块等模块中。
通常情况下,为了提高生产效率,LTCC是在较大的生瓷带(如20.32 cm生瓷片)上同时制备若干个相同的电路单元,所以经过烧结制成的基板需要对大片电路进行切割使之成为每只独立的电路单元。外形切割基本上是LTCC工艺过程的最后工序,其切割质量和效率直接决定着LTCC的成品率和产量。另外,对于复杂外形结构的LTCC产品,外形切割的作用显得更加重要。LTCC主要成分为陶瓷介质。由于陶瓷是由共价键、离子键或两者混合的化学键结合的物质,在常温下对剪应力的变形阻力很大,且硬度高;并且陶瓷晶体离子间由化学键结合而成,大,又使陶瓷有很大脆性。因此,LTCC基板材料的高硬度及脆性使其可加工性很差,即使有很小的应力集中现象也很容易被破坏。
LTCC基板切割可采取机械砂轮磨削划切和激光划切。机械砂轮划切采用高速转动的砂轮对陶瓷进行磨削加工[3]。由于陶瓷硬度高,刀具磨损量大,磨削效率低;再者由于是接触加工,陶瓷材料在磨削过程中很容易破裂,致使废品率增大。另外,砂轮划切只能进行直线划切,对于异型基板加工无能为力。激光切割具有的单色性好、方向性好、相干性好和高亮度的特征,理论上可以加工任何高硬度高致密的物质[4]。采用非接触式的切割方式,不存在刀具磨损,可以加工任意形状。但激光对材料的加工是一个非常复杂的过程,较小功率的激光切割效率很低,而大功率激光加工的热效应明显,存在着熔融凝固层缺陷和裂纹的问题。本文应用150 W的CO2激光,针对FerroA6M LTCC基板进行激光切割工艺研究,分析工艺参数对LTCC切割宽度、深度及飞溅物的影响规律。对LTCC基板外形加工成型具有一定的借鉴作用。
1. 实验材料与设备
实验用LTCC材料选择FerroA6M,基板厚度约0.96 mm,密度约2.45 g/cm3,热膨胀系数7×10-6/℃,热导率2 W/(m·K),杨氏模量92 GPa。激光器选用150 W CO2激光器,激光波长10.6 μm,采用TEM模式。以脉冲输出为工作方式,同轴辅助压缩空气为工作气氛,最高气体压力0.2 MPa,采用同轴吹气,喷嘴直径1.5 mm,聚焦镜焦距100 mm。激光划片时焦点位置位于试样表面,使其达到熔融状态,进而汽化形成圆坑。激光束在计算机的控制下产生移动,从而使圆坑部分重叠,在LTCC表面形成连续的刻槽。通过改变激光加工参数、加工速率和吹气压力,进行划片实验。用白光干涉仪测出试样的一维表面形貌曲线,分析切割质量。
2 .实验结果与分析
2.1 激光参数的影响
如图1所示,实验中设定激光重复频率0.3 kHz,切割速度1 mm/s,气体压力水平50%,激光功率水平从3%改变至36%,测得相应的切缝深度和切割宽度。激光平均功率对切割深度和切缝宽度有明显影响在其他参数固定不变时,切缝宽度和切割深度随着激光功率的增加而增大。当激光输出功率增大时,使单位时间内材料获得的能量增加,切割深度随之增加,当输出功率水平达到20%左右时,试样被完全切穿。此外,随着功率水平的增大,热影响区也变大,处于材料破坏阈值之上的能量所对应的宽度增大,表现为切缝宽度的增加。值得注意的是,在试样未被切穿的情况下,切缝宽度基本呈现线性增大的趋势,而当试样被完全切穿时,切缝宽度虽然随着能量的增大而增大,但是增大的趋势降低,激光能量水平的影响作用降低。在试样未切穿和切穿之间,切缝宽度变化较大。对于表面的飞溅物,激光能量水平的影响主要是通过试样是否被完全切穿体现的。在较低的能量水平条件下,试样未被完全切穿,这样熔融和汽化的陶瓷只能在气流的带动下通过试样的上表面排出,容易在切缝的边缘沉积形成飞溅物。而当试样被完全切穿时,气流带动熔融和汽化的陶瓷通过试样的下表面直接排出,表面飞溅物较少。另外,较高的激光能量增大材料汽化比例,同样会使得表面飞溅物含量降低。在以下的试验及分析中,针对试样未切穿和切穿分别讨论,激光能量水平分别选择12%和30%。在分别设定激光功率水平为12%和30%,其他参数不变的情况下,如图2和图3所示,激光重复频率从0.1 kHz改变至0.7
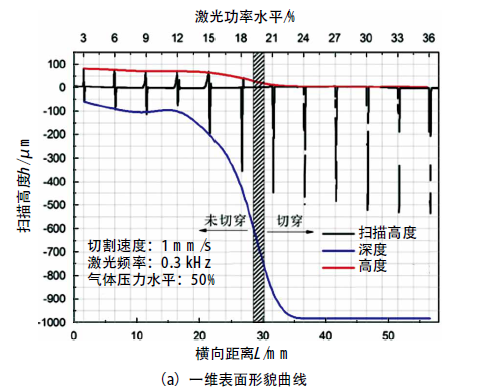
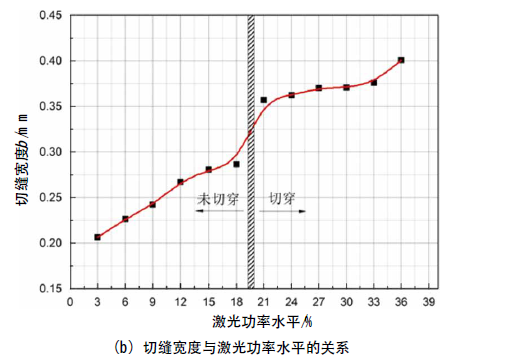
图1 不同激光功率水平加工条件下试样的
一维表面形貌曲线及切缝宽度
kHz,测得相应的切缝深度和切割宽度。激光功率水平为30%的条件下,改变激光重复频率,试样均被完全切穿。切缝宽度基本在0.35±0.03 mm,虽然随着重复频率的变化,切缝宽度有所变化,但变化较小。可见在试样被切穿的情况下,重复频率对切缝宽度和深度影响较小。激光功率水平为12%的条件下,改变激光重复频率,试样均未被完全切穿。切缝深度随着频率的增大呈现的变化趋势较为复杂,而切缝宽度则在一直减小。通常而言,在固定其他参数的条件下,重复频率越高,峰值功率越小,单脉冲与材料作用的能量越小,影响区越小,切缝宽度也就越小。所以,随着频率的增大,切缝宽度降低。但是,重复频率越高,激光平均输出功率增大。当重复频率较低时,虽然平均功率很低,但脉冲的峰值功率很高,激光束能够使被加工材料快速汽化,材料汽化比例高,表面飞溅物较少,会获得较大的切割深度。而随着重复频率的上升,脉冲峰值功率降低,材料汽化比例降低,飞溅物增大,切割深度降低。当重复频率继续上升时,虽然脉冲峰值功率处于较低水平,但输出的平均功率增加较为明显,因此切割深度增大。进一步增大重复频率,激光脉冲峰值功率进一步降低,材料汽化难度最大,而输出的平均功率增加有限,飞溅物比例更高,切割深度则呈现降低趋势。
2.2 切割速度的影响
切割速度的变化意味着激光与材料相互作用的时间变化,使材料在单位面积上得到的激光能量发生改变。如图4和图5所示,设定激光功率水平为12%和30%,其他参数不变的情况下,切割速度从0.5 mm/s改变至3.5 mm/s,测得相应的切缝深度和切割宽度。在30%功率水平条件下,切割速度越快,激光照射材料的时间越短,材料在单位面积上得到的能量越少。试样从切穿状态向未切穿状态转变,切缝
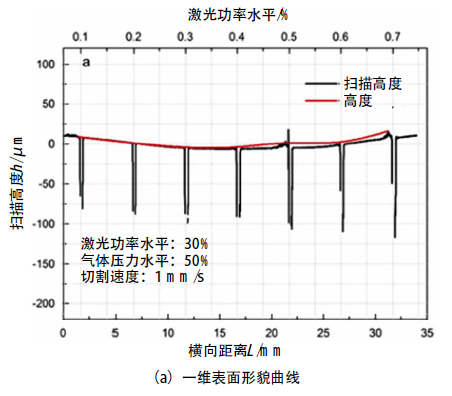
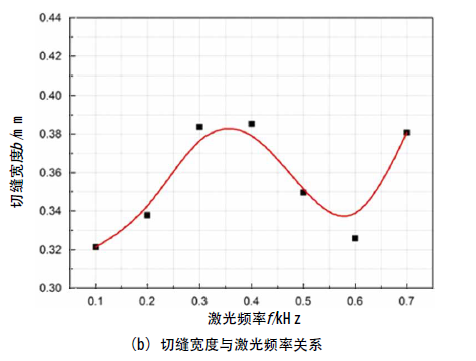
图2 30%激光功率水平条件下,不同激光频率对试样的一维表面
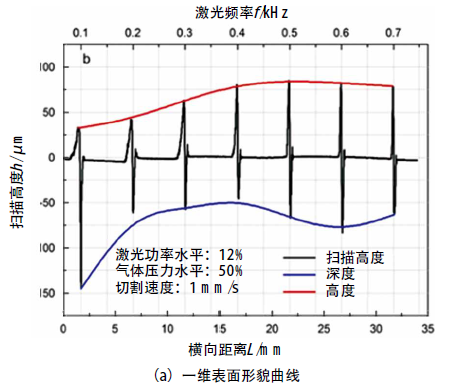
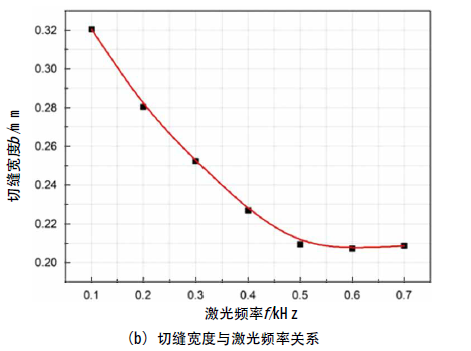
图3 12%激光功率水平条件下,不同激光频率对试样的一维表面
形貌曲线及切缝宽度的影响
深度逐渐降低。在较高能量状态下,切缝宽度主要受激光平均能量影响。当切割速度较低时,激光与材料的作用时间过长,影响范围过大,使得切缝周围的材料也被熔化或气化,导致切缝较宽,随着速度的增加,材料接受激光减少,影响范围降低,切缝宽度降低。在12%功率水平条件下,随着切割速度的增大,切缝深度同样呈现降低趋势。由于在较低能量状态下,切缝宽度主要受激光峰值功率影响。改变激光扫描速度不能使脉冲能量和光斑的大小改变,所以切割速度对切缝宽度影响不大。
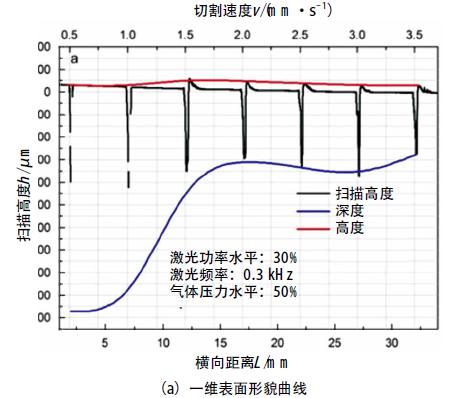
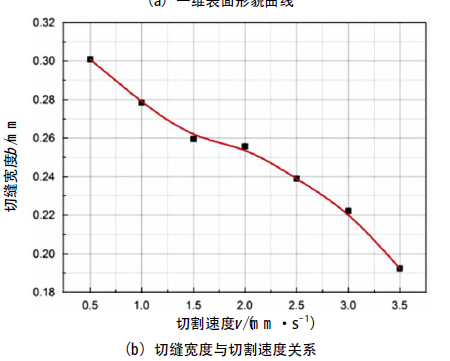
图4 30%激光功率水平条件下,切割速度对试样的一维表面形貌
曲线及切缝宽度的影响
2.3 辅助气体压力的影响
激光切割中最常用的辅助介质是气体,一般采用与激光束同轴的形式喷出,直接作用在切割处。图6和图7给出了激光功率水平分别为12%和30%,其他参数不变的情况下,辅助气体压力对切缝深度、切割宽度及表面飞溅物的影响。激光功率水平为30%的条件下,增大辅助气体的压力水平,试样均被完全切穿。切缝宽度先增大后降低。辅助气体一方面可以将熔融或气化的材料喷出,同时也将切割热量带走。
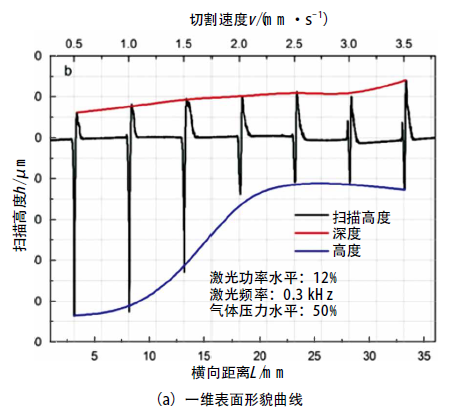
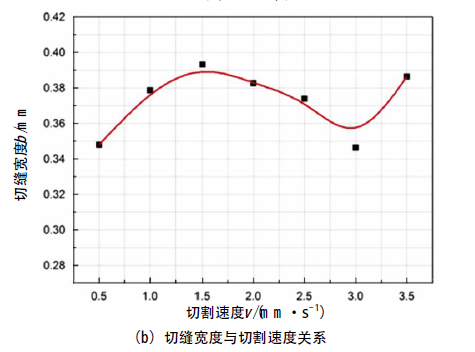
图5 12%激光功率水平条件下,切割速度对试样的一维表面形貌
曲线及切缝宽度的影响
在较低的气体压力条件下,气体辅助熔融或气化的材料喷出的能力较低,气场分布作用区域较小,从而切缝较小。熔渣不能及时带走,切割表面飞溅物较多。随着气体压力的增大,气体作用区域增大,切缝有所增大。但是,随着气体压力的进一步增大,气体的冷却作用明显,熔渣易在切割表明堆积,切缝宽度降低。表面的飞溅物水平在适中的气体压力下达到最小。激光功率水平为12%的条件下,改变气体的作用压力,试样切割深度先增大后降低。这是由于气体压力较小,带走熔融或气化的材料的能力有限,而在较高的气体压力下,气体的冷却作用明显。因此在适中的气体压力下具有较大的切割深度。对于切缝宽度,主要受峰值功率和切割深度的影响。由于气体的压力对激光光斑和峰值能量影响不大,因此切缝宽度则与切割深度的变化趋势相反,呈现先降低后增大的趋势。
2.4 导电金属的影响
LTCC主要介质层为陶瓷材料,其主要成分为氧化铝陶瓷。单一的这种陶瓷材料,热导率较低,对波长为10.6 μm的CO2激光有很高的吸收率,在一些CO2激光切割非金属材料理论模型中通常假设所
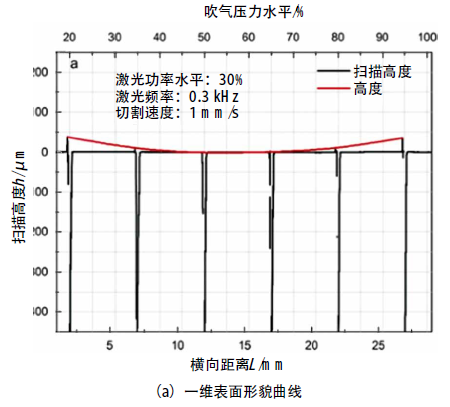
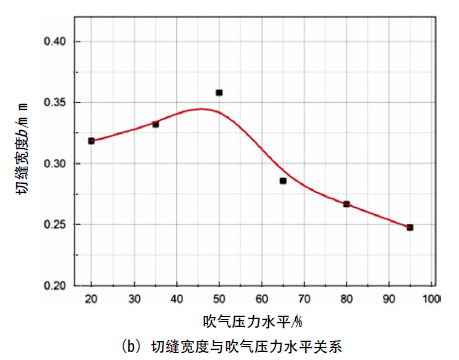
图6 30%激光功率水平条件下,吹气压力水平对试样的一维表面
形貌曲线及切缝宽度的影响
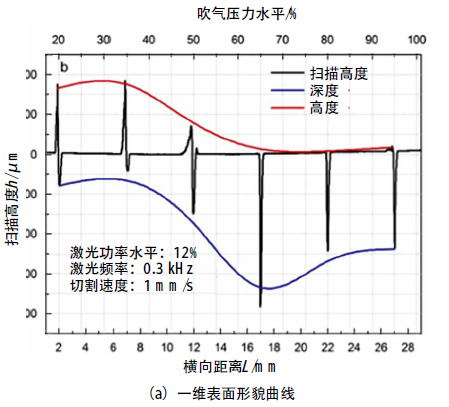
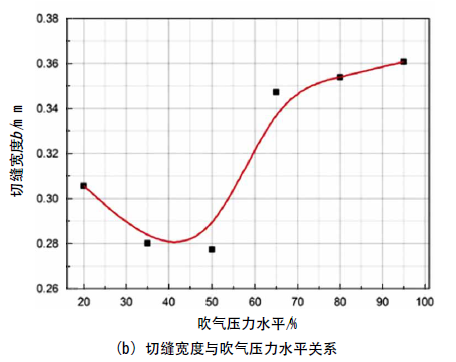
图7 12%激光功率水平条件下,吹气压力水平对试样的一维表面
形貌曲线及切缝宽度的影响
有的激光能量都被材料吸收,并转化为热量用于分解或气化材料[5]。在LTCC中,导通电路的基本上是Au、Ag或Cu等金属材料。这类金属材料对CO2激光的吸收率较低,以Au为例,其对CO2激光的吸收率仅为0.017。再者,金属材料导热率较高,不利于能量聚集,增大切割难度。图8给出了LTCC切割处有无金属导体的切缝断面形貌比较。从图中可以看出,当切缝处无金属导体时,切面光滑而且均一。但是,对于切缝处存在垂直互联孔及内层电路时,切面发黑,不再光滑均一。对于垂直互联金属孔,由于其深度较大,对激光的发射较大,激光能量容易在孔上方聚集而使得孔上方产生孔洞。当金属材料通过热传导获得能量,自身状态发生改变时,其对激光的吸收率增大,进而可以进行激光切割。而金属材料的熔融容易导致粗糙的切割断面和较差的切割质量。而对于内层电路,虽然对激光有阻挡作用,但是由于其厚度很低(一般为8 μm),阻挡作用有限。因此,在LTCC设计的切割过程中,应尽量避开金属导体,特别是金属互联孔。
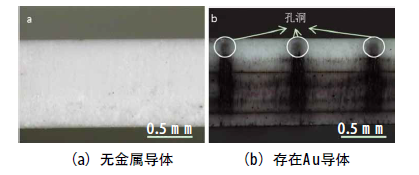
图8 切割处有无金属导体切缝断面形貌比较
2.5 激光切割热效应的影响
在CO2激光切割LTCC基板的过程中,基板吸收激光能量导致材料的汽化和熔化,在切缝的周围不可避免地受激光加工热效应的影响。随着LTCC设计的密度越来越高以及组装互联的要求,次产品电缆连接器,其双组份密封胶灌封合格率达到96.3%。进一步对灌封缺陷进行了统计,“有气孔”占缺陷总数的11.1%,已是影响连接器双组份密封胶灌封质量的次要因素,充分说明改进活动是有效的。本文通过试验寻找到搅拌胶液的最优参数组合,适用于今后其他多组份胶的配制过程,具有积极的推广意义。
投稿箱:
如果您有机床行业、企业相关新闻稿件发表,或进行资讯合作,欢迎联系本网编辑部, 邮箱:skjcsc@vip.sina.com
如果您有机床行业、企业相关新闻稿件发表,或进行资讯合作,欢迎联系本网编辑部, 邮箱:skjcsc@vip.sina.com