经济型数控车床自动上下料系统设计
2017-1-18 来源: 辽宁工业大学机械工程与自动化学院 作者:刘占娟 张艳冬
摘要:针对批量加工减震器活塞杆的经济型数控车床人工上下料问题,提出了采用自动上下料装置进行自动化上下料的方案。应用SolidWorks 软件对自动上下料装置进行了机械结构设计。通过对上下料装置工作过程及数控加工程序的分析,设计了与机床运行相匹配的自动上下料电气控制系统。自动上下料系统取代了传统的手工操作,提高了生产过程的自动化程度。该自动上下料系统的机械结构比常见的送料机械手简单,降低了生产成本。
关键词:上下料系统;数控车床;机械结构;电气控制
0.引言
减震器活塞杆是汽车减震器中重要部件,且是汽车使用过程中的易损配件,因而市场需求量大,需要大批量生产。为满足生产需求,某企业引进了一批经济型数控车床用于减震器活塞杆的生产。该企业每天要求加工3000 ~4000 件活塞杆,目前采用人工方式装卸工件,工人劳动强度极大,存在较大的安全隐患,且生产效率低,产品的质量难以保证。因此,为了提高竞争力,企业迫切要求实现活塞杆上下料的自动化,将劳动者从机械重复的简单劳动中解放出来,实现自动化生产,提高生产效率。随着国民经济和科学技术的不断发展,实现数控车床的自动化加工也是我国现阶发展和国情的需要[1] 。目前,国内已有数控车床自动送料装置的研究,但相对较少,如文献[2]设计了一种数控车床自动送料装置,实现了数控车床的自动上料,但只能为一种直径的棒料送料,且占地面积较大;文献[3]研究了一款数控车削自动送料装置,实现了数控车床的自动化加工,但只能输送一种长度的细长轴。针对数控车床单一的自动送料装置研究现状及其存在的问题,本文以SolidWorks 软件[4] 为开发平台,设计了一种新型数控车床自动上下料装置,能够实现不同直径和长度的棒料的自动供料,并设计了与机床运行相匹配的自动上下料电气控制系统。
1.工件的结构特点
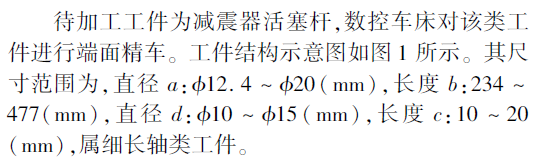
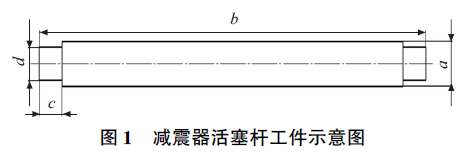
2.上下料装置总体结构及工作过程
2. 1 自动上料装置总体结构
自动上料装置总体结构[5-7] 如图2 所示,自动上料装置是利用气压缸活塞杆的伸缩运动带动工件在整个上料装置中移动,从而把工件送入车床主轴内。
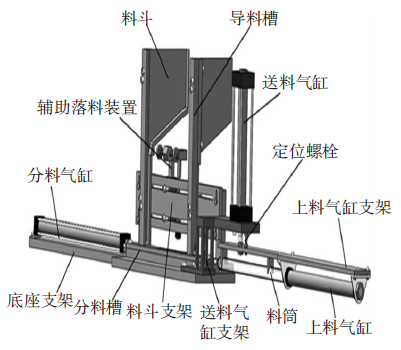
图2 自动上料装置总体结构图
该装置底座支架上安装分料气缸、分料槽、料斗支架和送料气缸支架,料斗支架上安装料斗、导料槽和辅助落料装置,送料气缸通过送料气缸支架固定在底座支架上,送料气缸通过螺纹与上料气缸支架连接,上料气缸支架上安装上料气缸、料筒和定位螺栓。其中分料槽和导料槽槽宽设计可调,以实现不同轴径工件的上料;料斗间距可调,可实现不同长度工件的上料;定位螺栓伸出量可调,从而保证料筒与分料槽内工件同轴。
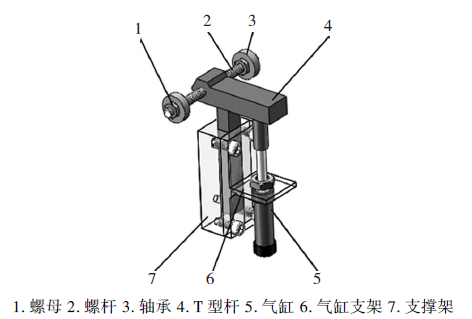
图3 辅助落料装置简图
辅助落料装置能为堆积在料斗里的工件顺利进入导料槽提供辅助作用,如图3 所示。气缸支架通过螺栓与支撑架连接,气缸支架对气缸起支撑固定作用。T型杆安装在气缸支架与支撑架构成的方孔内,小气缸活塞杆的一端顶住T 型杆,T 型杆随着活塞杆的上下移动而移动。T 型杆与螺杆通过螺纹连接,螺杆上装有轴承,轴承通过螺母固定在螺杆两端。气缸推动T型推杆上升,料斗中堆积的工件被抬高,轴承转动将工件送入导料槽。
2. 2 自动上下料装置工作过程
如图4 所示,自动上下料装置安装在数控车床主轴箱箱体上,安装时保证上料气缸下移至车床主轴中心时料筒轴线与车床主轴轴线重合。当加工某一批次工件时,根据工件长度,调节料斗间距和定位棒在主轴内的位置。根据工件直径,调节导料槽和分料槽的宽度,一般分料槽宽要比工件直径大0. 5mm 左右,才能保证工件在分料槽内顺利移动,同时调节定位螺栓的伸出量,保证送料气缸活塞杆缩回后,料筒与分料槽内工件同轴。当工件直径发生变化时,料筒内加入相应衬套,确保工件轴线在料筒内的位置不发生变化。
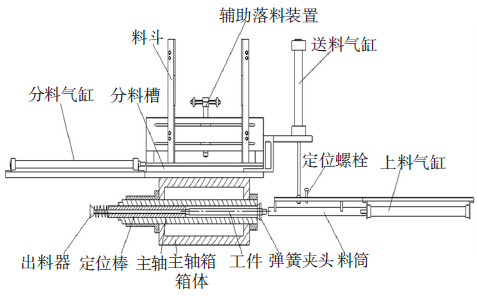
图4 自动上下料装置工作过程示意图上下料协调工作过程:上下料装置在工作前,工人将料斗内装满工件。工作时,工件在辅助落料装置的作用下落入分料槽。分料气缸将工件送入料筒后,送料气缸动作,将工件移至车床主轴,最后上料气缸动作,将工件送入车床主轴内,并经定位棒定位,同时将出料器中的弹簧拉伸。弹簧夹头夹紧工件,数控车床根据编好的程序对工件进行加工。加工结束后,弹簧夹头松开,工件被出料器弹出,一次加工结束。
3.自动上下料装置控制系统设计
3. 1 气动控制回路的设计
该装置中的气缸全部为内置磁环气缸,内置磁环的作用是配合外面的磁性开关工作,及时感应活塞的位置。气动设计原理[8] 如图5 所示。其中磁感应开关安装位置的选择与控制系统的设计有关。送料气缸推出后需要保持推出状态不能立即复位,所以选用双电控三位五通电磁阀控制,其他的都是由单电控二位五通电磁阀控制。
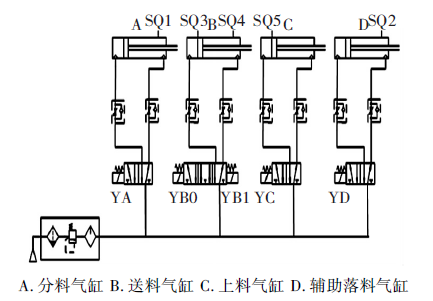
图5 自动上料装置气动原理图
3. 2 自动上下料装置电气控制回路设计
自动上下料装置电气控制的设计即多气缸顺序动作电气控制回路的设计,该设计需要考虑自动上下料装置中气缸动作与工件加工的数控程序相协调,因此完整的控制包含两部分:电气控制[9] 和数控程序辅助M 控制[10] 。其中部分气缸动作由外接电气控制回路实现,该电气控制回路的设计需要实现两个功能,一是上料功能,当工件加工完成后,控制电路接收信号,自动送料气缸将会按照工作流程动作。二是报警功能,当工件没有顺利进入车床主轴内或自动送料装置内没有工件时,该控制回路会提示报警,如图6 所示。
按下启动按钮SB1, 辅助继电器KA0 得电,并自锁,电路接通, 中间继电器KA1 得电,KA1 常开闭合, 电磁阀YA 得电,分料气缸前进分离工件,当分料气缸运动到磁感应开关SQ1 时,SQ1 常闭断开,KA1 失电,分料气缸退回,同时SQ1常开闭合, KA2 得电, 自锁, 电磁阀YB0 得电, 送料气缸下移送料, 当送料气缸运动到磁感应开关SQ4 时,SQ4常闭断开, KA2、YB0 失电,SQ4 常开闭合,KA3 得电,KA3 常开闭合,电磁阀YC 得电,上料气缸动作,将工件送入车床主轴内,并通过定位棒定位,同时出料器被工件顶出,弹簧被拉伸。安装在出料器前方的光电开关SQ6 感应,SQ6 常开闭合,KA6 得电,该信号通过导线传递给数控车床的控制系统,弹簧夹头在该信号的作用下夹紧,将控制弹簧夹头的继电器KA9 的一个常闭触点延出,当程序运行到M10 指令时,KA9 常闭断开,KA3 失电,电磁阀YC 断电,上料气缸退回。当气缸运动到磁感应开关SQ5 时,KA4 得电,电磁阀YB1 得电,送料气缸上移,当送料气缸运动到磁感应开关SQ3 时,SQ3 常闭断开,KA4 失电,电磁阀YB1 断电。数控车床开始对工件加工,加工完毕后,弹簧夹头松开,工件在出料器的作用下弹出,出料器在弹簧的作用下恢复原位,光电开关SQ6 失去感应,断开的SQ6 再次闭合,由于各气缸均处在初始状态,所以常闭SQ1 闭合,常开SQ3 和SQ5 闭合,KA1 再次得电,自动上下料装置开始进行下一轮的送料工作。
辅助落料气缸的动作是通过中间继电器KA5 和时间继电器KT0 实现。当KA1 得电后,中间继电器KA5 得电并自锁,KA5 常开闭合,电磁阀YD 得电,辅助落料气缸上移,当气缸运动到磁感应开关SQ2,时间继电器KT0 得电,开始计时,计时时间要大于分料气缸的循环时间,以保证落料的顺利进行。当KT0 时间到,KT0 常闭延时断开,KA5 线圈失电,电磁阀YD 失电,气缸退回。
送料气缸动作后,报警系统也开始工作。KA1 得电后,中间继电器KA7 得电并自锁,同时时间继电器KT1 得电,开始计时,计时时间为完成一次送料的时间。当KT1 时间到,KT1 常开延时断合,车床主轴内若无工件送入,SQ6 常闭保持闭合,KA8 线圈失电并自锁,KA8 常开闭合,报警器开始报警。
与自动送料电气控制相适应的数控加工程序如表1 所示
表1 数控加工程序
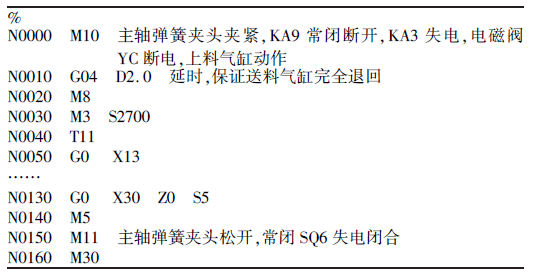
数控程序辅助M 控制是实现机床运行与自动上下料电气控制协调工作的关键。通过增加数控程序中的M10 指令,实现继电器KA9 对自动送料电气回路的控制。弹簧夹头夹紧工件后,数控加工并没有立刻进行,而是延时,待送料气缸退回后才开始加工工件。加工完毕,程序运行到M11 指令,常闭SQ6 失电闭合,中间继电器KA1 重新得电,送料工作再次开始,由此将自动上下料驱动指令与数控车床整体运行加工相融合。
4.结束语
为大批量生产减震器活塞杆的经济型数控车床设计了一个气动自动上下料装置,并通过对数控加工过程进行分析研究,设计了与机床加工程序相适应的电气控制回路和数控辅助控制。该装置提高了生产过程中的自动化程度,提高了产品的一致性,且一人可同时照看2 台车床,大幅度提高了生产效率,降低了工人劳动强度,减少企业人工成本支出。而且由于上下料装置的动力源为压缩空气,因此维护保养容易,无污染。通过对自动上下料装置调节,可以实现不同规格工件的加工,使用范围广泛。本设计已在某汽车零部件有限公司投入使用
投稿箱:
如果您有机床行业、企业相关新闻稿件发表,或进行资讯合作,欢迎联系本网编辑部, 邮箱:skjcsc@vip.sina.com
如果您有机床行业、企业相关新闻稿件发表,或进行资讯合作,欢迎联系本网编辑部, 邮箱:skjcsc@vip.sina.com