基于ANSYS 的激光选区熔化装备进给传动系统结构优化设计
2017-2-15 来源:南京理工大学机械工程学院 作者:崔祎赟, 刘婷婷, 廖文和, 张长东
摘要: 成形缸的进给传动系统作为激光选区熔化装备的主要组成部分, 其静动态性能是影响激光选区熔化铺粉精度的关键因素, 而进给传动系统的结构直接影响静动态特性的好坏, 因此有必要对其进行设计与分析。以有限元软件ANSYS 为工具, 采用有限元的方法对进给传动系统进行静动态特性分析, 仿真分析了单丝杆有无导柱的支承方式以及滚珠丝杆的安装位置对进给传动系统的影响。结果表明: 有导柱支撑并且滚珠丝杆安装在成形缸正下方时, 系统的静动态性能最佳。此外, 在工艺方面研究了铺粉压力对该进给系统的影响。
关键词: 激光选区熔化; ANSYS; 成形缸; 传动系统; 丝杆
0.前言
激光选区熔化(Selective Laser Melting, SLM)技术基于离散-堆积原理, 它利用激光扫描产生的热量快速并完全熔化粉末材料, 可以直接根据3D CAD模型来制造复杂形状物体[1-3] 。其原理如图1 所示。
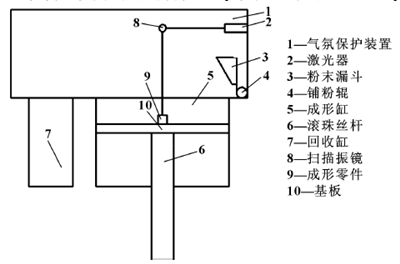
图1 激光选区熔化装备结构示意图
铺粉辊将粉末漏斗中的粉末材料以一定厚度(约30~50 μm) 铺在成形缸上方的粉床上, 一次铺粉完成后激光器通过扫描振镜在气氛保护装置下对粉末进行直接熔化, 该粉层熔化加工完成后, 成形缸中的基板在滚珠丝杆的带动下相应下降一个粉层厚度的高度, 不断重复这一过程, 直至成形零件加工成形[4] 。
成形缸进给传动系统是SLM 激光选区熔化成形设备中的关键部件, 用于控制加工过程中成形缸的移动量。在成形缸中, 成形零件固结在基板上, 每次熔化完一层粉末后, 成形零件跟随基板在成形缸中下降一个粉层厚度的位移。铺粉精度是影响成形零件质量的重要因素之一[4] , 而每次铺粉的厚度取决于成形缸中成形零件和基板的下降位移量, 铺粉的厚度精度又取决于传动系统驱动基板的下降位移精度, 因此, 优化设计成形缸进给传动系统结构, 提高系统工作精度, 是激光选区熔化增材制造装备研制与改进过程中需要考虑的关键问题[5] 。
对于成形缸进给传动系统的设计研究是激光选区熔化增材制造装备研制过程中的重要环节, 国内外相关领域内的学者和机构为了满足增材制造实验需求及商业化装备的研制对成形缸进给传动设计进行了相关研究。其中, 陈光霞等[6-7] 在成形缸活塞运动中设计了导向装置来减少活塞上下运动的摆动误差和转动误差, 同时分析了铺粉装置的误差来源, 提出了若干控制和消除误差的方法; 党新安等[4-5] 研究了分别从振动特性和传动系统动力参数计算等方面来提高铺粉精度要求。除此之外, 史玉升等[8] 于2005 年研制成功SLM 设备样机, 目前, 华中科技大学开发了两套SLM 成形设备: HRPM-Ⅰ和HRPM-Ⅱ、华南理工大学的研究人员激光加工实验室分别于2004 年、2007年研发了DiMetal-240、DiMetal-280, 并于2012 年推出商用化设备DiMetal-100[9] 。德国EOS 公司的研究人员在研发M270、M280、M290 等金属成形设备[10]的过程中, 对于成形缸进给传动系统的设计均进行过相关研究。
本文作者以激光选区熔化装备成形缸进给传动系统的优化设计、提高系统工作精度为目标, 利用ANSYS有限元分析软件构建进给传动系统的仿真模型,对进给传动系统进行静动态分析, 并且模拟不同压力下铺粉辊的铺粉过程对成形缸进给传动系统的影响。基于仿真分析结果, 优化、改进成形缸进给传动系统结构, 为自主激光选区熔化增材制造装备研制提供相应部件的设计方案。
1.成形缸进给传动系统建模
成形缸进给传动系统主要由成形缸体、基板、活塞、固定板、导柱、滚珠丝杆副、支撑板和底板等组件构成成。文中采用Pro/E 软件绘制进给传动系统的三维CAD 模型如图2 所示。在保证分析结果的精度和可靠性的前提下, 为了提高有限元分析的计算速度, 避免不必要的计算量, 对模型进行简化[11] , 主要包括:以等直径光杆代替滚珠丝杆副; 去除模型的倒圆倒角以及基板、固定板、支撑板和底板等结构上的小螺栓孔等小特征区域[12] 。
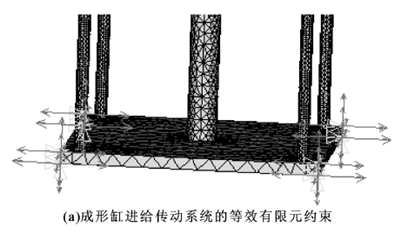
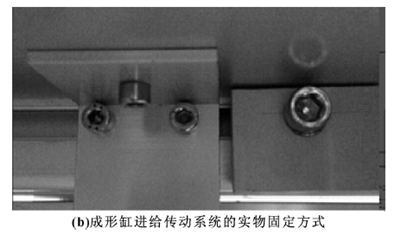
图4 成形缸进给传动系统的固定方式
三维模型建立之后, 导入有限元软件ANSYS 中进行分析处理, 整个结构实体单元类型选择Solid185单元, 采用自由划分和人工干预相结合进行网格划分[13] 。由于组成成形缸进给传动系统的各个零部件在稳态下保持相对静止, 在不考虑结合面动态参数特性的情况下, 各零部件之间采用刚性联接[11] 。有限元模型如图3 所示。
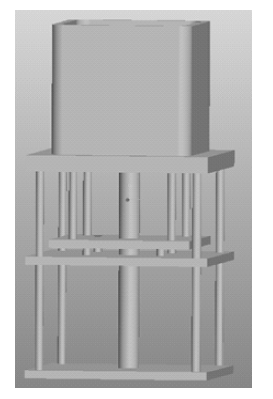
图2 进给传动系统Pro/E 建模图
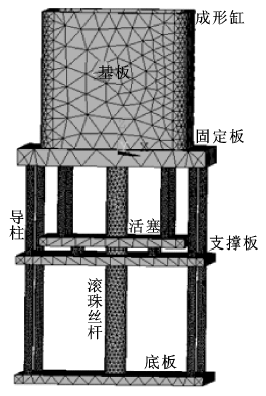
图3 进给传动系统有限元建模图
设定成形缸进给传动系统滚珠丝杆副的螺母运动方向为设备的Z 轴(向上为正方向), 铺粉辊的直线运动方向为X 轴(向右为正方向), 再根据笛卡尔坐标系即可确定设备的Y 轴方向。
文中成形缸进给传动中的滚珠丝杆和导柱的顶部和底部通过螺母座分别固定在固定板和底板上, 通过ANSYS 有限元软件布尔运算的“add” 操作将成形缸进给传动系统“加” 为一个整体; 成形缸的底板利用螺栓固定连接在设备铝合金总框架上, 因此ANSYS有限元软件分析的等效约束是: 在底板顶点处建立节点, 约束是这些节点X、Y、Z 3 个方向上的自由度, 固定约束如图4 所示。成形缸设计尺寸为150mm×150 mm×100 mm, 最大的承载钴铬合金粉末质量约为20 kg, 等效于在ANSYS 分析中, 在基板表面沿Z 轴负方向施加104 Pa 的压强。
模型中除了丝杆材料是轴承钢GCr15 和基板材料是不锈钢304 之外, 其余材料为铝合金3003。材料参数见表1。
表1 材料参数
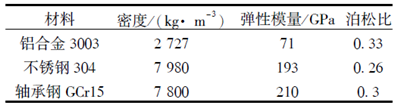
2.导柱对成形缸进给传动系统的影响
成形缸中采用滚珠丝杆在竖直方向上的上下直线运动带动基板的直线运动, 导柱在装置中主要作用是: (1) 支撑作用。导柱安装在固定板上, 对成形缸体有一定的支撑作用; (2) 导向作用, 使支撑板在滚珠丝杆的作用下沿导柱上下运动以实现基板的上下运动[6] 。下面探讨有无导柱对进给传动系统运行精度的影响。文中设计滚珠丝杆的顶部固连在固定板中心位置, 基于ANSYS 有限元平台分别对固定板4 个角有导柱和无导柱两种设计进行静动态分析。
2.1有无导柱的两种进给传动系统静力学分析
静力分析显示: 有导柱支撑时, 成形缸进给传动系统的总变形量最大值为3畅45 μm; 最大值位于基板中心位置, 最小值位于施加约束的底板的顶点上; 成形缸进给传动3 个方向中变形最大为Z 方向, 如图5 (a)所示。无导柱时, 总变形量最大值为15畅1 μm,如图5 (b) 所示, 该变形量是有导柱支撑结构的近5 倍; 一般而言, 激光选区熔化过程成形缸进给量为一个粉层厚度, 约30~50 μm, 而无导柱支撑结构的最大总变形量接近粉层厚度的一半, 误差较大; 相比而言, 有导柱支撑结构增加了传动进给沿轴向的静刚度,能减少最大总变形量, 从而提高加工中的进给精度。
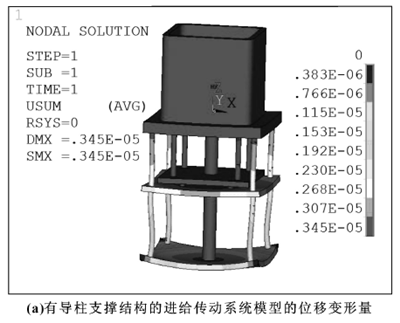
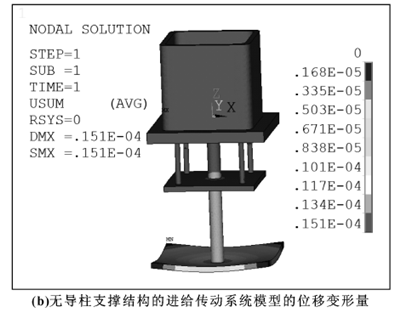
图5 有无导柱支撑结构的两种进给传动系统模型的位移变形量
2.2 有无导柱两种进给传动系统的模态分析
在ANSYS 中采用BlockLanczos 模态提取法对有无导柱支撑这两种进给传动系统进行模态分析, 提取前10 阶固有频率, 一般而言, 低阶固有频率起主导作用, 高阶固有频率在通常情况下是无法激发的。图6 为该两种传动进给系统前10 阶模态频率对比图。
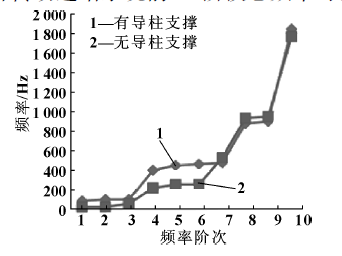
图6 有无导柱两种进给传动系统模型的模态频率对比图
可知: 当有导柱支撑时, 其模态频率比没有导柱支撑时高, 因而在质量相近情况下, 有导柱的进给传动系统刚度更大。除此之外, 固有频率的提高能在一该传动进给系统的动态性能。
3.丝杆的安装位置对成形缸进给传动系统的影响
激光选区熔化成形技术通常采用粒径30 μm 左右的超细粉末为原材料[14] , 在成形缸进给传动过程中, 滚珠丝杆在竖直方向上带动基板做上下直线运动, 从而推动成形缸中的成形零件和成形缸内微细粉末上下运动, 因此, 在运行过程中不免有粉末从基板与成形缸内壁的间隙中泄漏, 从而透过缝隙下落。然而, 若滚珠丝杆副安装在成形缸正下方, 则微细粉末可能会进入滚珠丝杆, 使得滚珠丝杆磨损, 导致滚珠丝杆的运行精度降低, 从而影响成形缸进给精度。因此, 文中设计滚珠丝杆副两种不同的安装位置(滚珠丝杆副安装在成形缸正下方与右侧), 基于ANSYS有限元软件进行静动态分析, 如第1 节所述在基板表面沿Z 轴负方向施加104 Pa 的压强, 在底板顶点处建立节点, 约束这些节点X、Y、Z 3 个方向上的自由度。
3.1 滚珠丝杆不同安装位置下两种进给传动系统模型的静力学分析
静力分析显示: 丝杆安装在成形缸右侧位置时,成形缸进给传动系统的总变形量最大值为7畅06 μm;最大值位于成形缸左侧顶部位置, 约为丝杆安装在正下方位置时变形量最大值的两倍, 如图7 (b) 所示;同时, 依据表2 以及图7 (c) — (h) 所示。
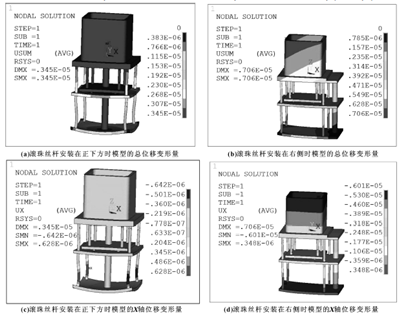
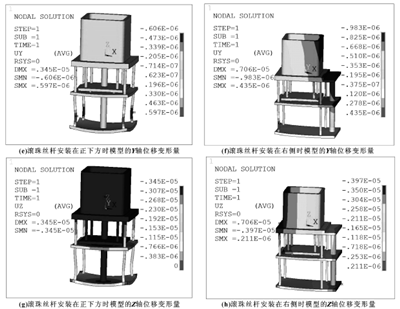
图7 滚珠丝杆不同安装位置时两种模型的位移变形量对比图
丝杆安装在成形缸正下方时, X、Y 轴方向的位移变形量几乎相同, 节点位移的最大值和最小值数值相等, 符号相反, 变形量集中在导柱下半部分, 导柱产生小量弯曲变形, 基板以及成形零件的在X、Y 轴方向上的位移变形量最小; 然而若使用丝杆在成形缸右侧的安装方式时候, X、Y、Z 3 个方向上节点位移最大值和最小值数值相差较大, 存在倾斜, 这使得整个成形缸进给传动系统倾斜, 从而可能导致成形零件变形或者翘曲。
表2 滚珠丝杆不同安装位置下两种进给传动系统模型总位移以及X、Y、Z 3 个方向位移
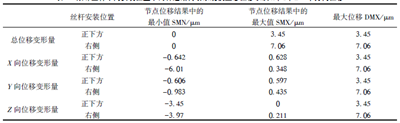
3.2 滚珠丝杆不同安装位置下两种进给传动系统模型的模态分析
为了提取两系统的固有频率和各阶振型, 在ANSYS中采用BlockLanczos 模态提取法对它们进行模态分析, 考虑到系统低阶模态主要表现为X、Y、Z 3 个方向的振动以及扭转变形[13] , 高阶固有频率很少出现,故提取前10 阶固有频率, 见表3。相同振型下, 滚珠丝杆不同安装位置下两种进给传动系统固有频率最大相差767 Hz, 滚珠丝杆安装在成形缸正下方比安装在右侧固有频率提高了71畅2%, 该频率下, 系统沿Z 轴上下振动; 其次, 在第一阶次时, 安装在正下方的位置比右侧提高了53畅9%, 该频率下, 成形缸以及活塞等系统的上半部分绕Z 轴扭转变形; 在第4 阶次时,安装在正下方的位置比右侧提高了41畅8%, 该频率下,活塞绕Z 轴扭转变形; 而Z 轴方向为成形缸的进给方向, 提高Z 方向的精度可直接减少成形缸进给误差。
表3 滚珠丝杆不同安装位置下两种进给传动系统模型在同一振型下的固有频率值
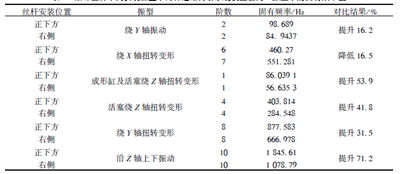
基于第3畅1 节静力学分析和第3畅2 节模态分析的结果可知: 滚珠丝杆安装在成形缸正下方位置可以避免系统倾斜变形, 并且可以减少总位移变形量; 同时可以较好的提升进给传动系统沿丝杆轴向的动刚度,这有利于提高进给传动系统的精度和负载能力。与滚珠丝杆安装在正下方的方式相比, 滚珠丝杆安装在右侧的方式虽然可以避免粉末污染磨损丝杆, 但是此安装方式的静动态性能不好, 特别影响进给传动系统在Z 轴的运行精度, 综上所述采用滚珠丝杆安装在成形缸正下方的方式, 该方式可以提高Z 轴精度, 从而提高成形缸的进给精度, 同时为了避免粉末侵入滚珠丝杆, 采用防尘密封圈及防尘装置。
4.铺粉辊不同铺粉压力对成形缸进给传动系统的影响
激光选区熔化技术所需的铺粉过程采用铺粉辊将粉末均匀地铺覆在成形缸上方的粉床上。粉末不像致密体那样具有固定的形状, 其表现为与液体相似的流动性; 由于颗粒之间相对移动时存在摩擦, 粉末的流动性又很有限, 粉末在松散堆集时颗粒之间存在大量的孔隙, 松散粉末的密度只有致密体的20% ~50%[15] , 而粉层的粉末密度大小直接影响成形零件的密度, 从而影响零件的强度、收缩和翘曲变形。为了铺出具有较高致密度的粉末层, 铺粉辊在水平运动的同时, 对粉末层施加向下的压力使之压实, 这也对成形缸进给传动系统产生了一定影响。铺粉辊的受力分析如下: 如图8 所示, 铺粉辊对粉末产生正压力F的作用, 其分力F1 推动粉末向前运动, 分力F2 对粉末起到压实的作用[16] 。而正压力F 与铺粉辊的质量有关, 因此铺粉辊的质量大小决定分力F2的大小。文中以有导柱支撑并且滚珠丝杆安装在成形缸正下方的铺粉进给传动系统模型为例, 设计铺粉辊的直径为40 mm, 长约为170 mm, 材料为不锈钢304 (铺粉辊的重力约为15 N)。在铺粉辊对粉末施加压力下, 研究铺粉辊从右向左铺粉过程中成形缸进给传动系统的变形, 并且研究不同压力大小(分别施加1、2、4、6、8、10 N 的压力) 对成形缸进给传动系统的变形影响。
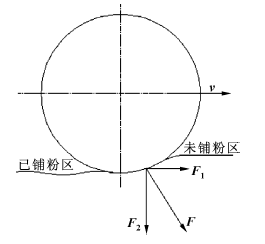
图8 铺粉辊铺粉时粉末受力示意图
在ANSYS 有限元中, 铺粉辊对粉末施加压力等效于对成形缸上表面施加一项移动载荷, 铺粉过程中圆柱形铺粉辊与成形缸成线接触, 等效成对成形缸进给系统施加一个移动的线载荷, 因此每次只需将载荷施加在规定线单元上的各个节点处, 而采用GUI 方式会占用大量时间, 利用APDL 语言可以加快分析过程中的加载和求解[17] 。设置每次载荷步结束时间为1, 载荷步数为5, 从成形缸最右端每隔1 s 依次向左移动到作用规定的节点上, 直到载荷移动到最左端的规定节点位置, 一次铺粉运动完成。移动载荷命令流如下:
TIME,1
NSUBST,5,2
F,725,726,727,728,729,730,731,732,FY,-1
LSWRITE,1
TIME,2
FDELE,All,ALL
F,745,746,747,748,749,750,751,752,FY,-1.......
以此循环, 完成铺粉压力为1 N 下的一次铺粉过程, 而后改变压力为2、4、6、8、10 N, 利用有限元ANSYS 分析每次铺粉过程成形缸进给传动系统的变形量。
4.1 成形缸进给传动系统一次铺粉过程的变形
施加的铺粉压力使成形缸产生Z 轴负方向的位移变形, 对于X、Y 轴可忽略不计。由于成形缸传动进给系统结构对称, 在铺粉辊从右向左运动过程中, 该系统的变形成对称分布。如图9 所示, 以铺粉压力1 N 为例, 分析一次铺粉过程内成形缸进给传动系统的变形。
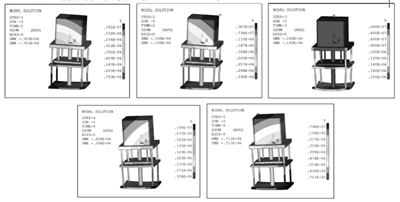
图9 铺粉压力1 N 时各载荷步下成形缸进给传动系统变形图
在中间位置时即载荷步3, 整个系统的最大变形量最小, 系统变形呈整体下降趋势。各载荷步下最大变形量的最大值处在成形缸最右端和最左端即载荷步1、5, 下降变形最大, 约是载荷步3 处变形的4 倍。铺粉过程, 成形缸传动系统的变形处在弹性阶段, 呈椭圆体状; 铺粉结束时, 恢复原状, 因此铺覆在左右两端的粉末最多, 并且向中间位置处逐渐减少, 粉层呈不均匀分布, 从而可能使得成形零件产生翘曲等变形。
4.2 不同铺粉压力对成形缸进给传动系统的变形影响
结果表明: 在铺粉压力10 N 以下时, 整个铺粉过程, 成形缸进给传动系统的变形趋势一致, 变形处于弹性阶段; 随着压力的增加, 各个载荷步的最大变形量成线性增加如表4。如图10, 铺粉压力越小, 成形缸进给传动系统的变形越小, 铺覆在成形缸粉床上的粉层越均匀。当铺粉压力为4 N, 铺粉过程中变形量的差值为2.13 μm, 即左右两端高于中心位置2.13μm, 该数值近似于每次铺粉厚度(约50 μm) 的4.26%; 若增大铺粉压力至10 N, 则变形差值增大为5.31 μm, 接近每次铺粉厚度( 约50 μm) 的10.62%, 误差较大; 若继续增大压力时, 变形差值也相应增大, 则翘曲变形更为严重, 因此为了保证误差控制在10%以内, 则在本装置设计的成型实验中,铺粉压力应小于10 N。
表4 不同压力各载荷步下进给传动系统的最大变形量 μm
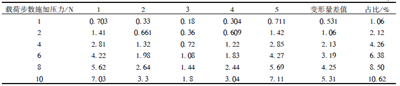
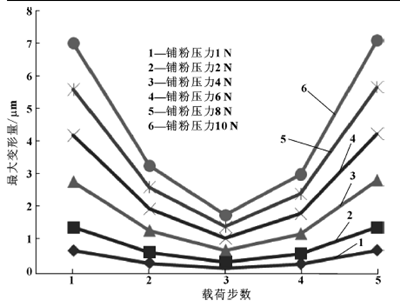
图10 不同压力各载荷步下成形缸进给传动系统的最大变形量折线图
5.结论
(1) 由静态分析结果和模态分析对比结果可知,有导柱支撑的进给传动系统轴向静态刚度相比无导柱时提升了77%, 同时也提高了系统固有频率, 在一定程度上避免共振的产生。这有利于提高系统的负载能力和使用寿命。
(2) 滚珠丝杆在成形缸正下方的安装方式使得该进给传动系统的静态刚度相比一侧安装提升了51%, 也避免了系统倾斜, 同时提高进给传动系统沿丝杆轴向的动刚度, 这有利于提高进给传动系统的精度和负载能力。
(3) 铺粉压力在10 N 以下时, 成形缸进给传动系统处于弹性变形阶段, 不同压力下铺粉过程的变形趋势一致; 当铺粉压力超过10 N, 铺覆的粉层的中心位置与两端的高度差值大于每次铺粉厚度的10.62%, 若继续增加压力, 粉层中心与两端高度差越大, 则翘曲变形加重。
投稿箱:
如果您有机床行业、企业相关新闻稿件发表,或进行资讯合作,欢迎联系本网编辑部, 邮箱:skjcsc@vip.sina.com
如果您有机床行业、企业相关新闻稿件发表,或进行资讯合作,欢迎联系本网编辑部, 邮箱:skjcsc@vip.sina.com
更多相关信息