预防高速走丝电火花线切割断丝的措施
2017-4-28 来源:青岛理工大学机械工程学院 作者:王贤勇
摘要:研究预防高速走丝断丝的措施,将有助于减少断丝,提高生产效率,增加高速走丝机床的市场竞争力。本文主要从电极丝的因素、送丝机构的因素、工件的因素、电参数的因素、工作液的因素和操作使用的因素等6个方面提出了预防断丝的措施,通过这些措施大大减少了断丝的几率,减少了成本,提高了生产效率。对于实际生产有很强的指导意义,将有助于提高高速走丝的市场占有额。
关键词:电火花;线切割;电极丝;工作液
1.引言
随着经济和社会的发展,人们对机床的精度和效率的要求也越来越高,而高速走丝机床低的加工精度严重影响了其发展。通过研究发现,电极丝在加工过程中的断丝现象是影响高速走丝机床效率和精度提高的重要因素。通过总结前人的研究成果,发现影响电极丝断丝的因素主要有 6 种:电极丝的因素、送丝机构的因素、工件的因素、电参数的因素、工作液的因素和操作使用的因素。通过进行一系列的试验和研究,针对这6个方面存在的问题提出了相应的解决措施,将大大减少断丝现象,提高高速走丝的加工精度和效率,增加高速走丝的市场竞争力。
2.电极丝
在高速走丝中,电极丝的材料、长度和直径、速度和存储条件等选择不当都会引起断丝,影响实际生产。
(1)电极丝材料一般选用钼丝,因为其具有很好的韧性,可以减少电极丝在换向时造成的冲击,同时还有较好的导电性,价格便宜等优势。
(2)频繁的换向是造成断丝的一个很重要的原因,为此要加长工作的电极丝的长度,一般不应小于贮丝筒工作区域长度的一半,大约300~400m。在满足实际加工条件的情况下,选取粗的电极丝,因为粗的电极丝不易断丝,且加工效率高,但直径不是越粗越好,若直径大,则电蚀颗粒会增多,使工作液纯度降低,及易造成断丝[1]。选取的电极丝直径一般为0.10~0.18mm[2],当加工的零件圆角半径较小或精度要求较高时,可选取直径<ϕ0.06mm的电极丝。另外当直径损耗了 0.03~0.05mm 时,应及时更换新丝,防止断丝。因此选用合适的电极丝直径是至关重要的,工件材料的厚度与直径的选取关系如表1所示。
表1 工件材料厚度与电极丝直径关系 mm
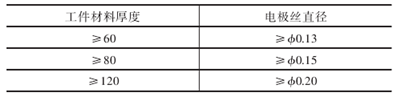
(3)电极丝的运行速度一般为 8~10m/s,有助于工作液进入到加工间隙带走电蚀产物。若移动速度太慢,会造成集中放电,烧伤电极丝,引起断丝,反之则会使振动幅度加大,精度降低。
(4)因为电极丝选用钼丝,而钼丝在空气湿度大的环境下极易被氧化,被太阳晒时会变脆,且受折容易断裂,为此需要把新买进的钼丝放入密封的容器中,用时再取。
3.送丝机构的因素
送丝机构中的导轮、导电块、挡丝块和贮丝筒等零部件的安装不当及磨损,以及机构中导轮的材质选用不当和电极丝的松紧不适都会引起电极丝断丝。
(1)在向高速走丝机床上安装导轮、轴承和衬套等零件前一定要先将这些零件清洗干净,保证没有杂质,且在使用 6~8 个月后需及时更换,防止断丝[3]。在进行加工前,需将贮丝筒后端的限位挡块调整好,防止贮丝筒冲出限位行程开关而断丝,同时贮丝筒上缠绕的电极丝不允许出现叠绕和夹丝现象。新买进的导电块由于棱角比较锋利,在运行中可能会划断电极丝,因此需在使用前将棱角进行倒圆。
(2)陶瓷和硬质合金导轮主要用来加工材质较硬和难熔合金工件,而钢制导轮主要加工材质较软的工件(如钢、铝和铜等),根据工件材质的不同选择合适的导轮,可减少导轮的磨损,减少断丝。
(3)合适的电极丝张力将有助于减少断丝,提高生产效率,电极丝张力一般为 5~10N,但在加工断面和孔时,因为在放电初始位置容易发生断丝,需要适当的减少张力,在工作一段时间后将张力调到稳定状态[4]。
4.工件的因素
待加工工件的表面质量、内部的应力、厚薄和本身的材质都能引起断丝。
(1)当在进行线切割加工的前一个工作流程为平磨加工时,需要进行退磁处理,避免电蚀颗粒被吸附到切缝中,引起断丝。在进行加工前,需观察工件表面,若存在铁锈、污物和毛刺等,需及时清除,以免引起集中放电,造成断丝。若工件内部存在不导电杂质,可以编制一段每进0.05~0.1mm便后退0.5~1mm的程序,在加工中反复使用,同时加大工作液的流量,将杂质冲刷掉[5]。
(2)若工件在线切割加工前有热处理工序,可在热处理前从工件内部加工穿丝孔,减少加工时因内应力释放造成的断丝。另外线切割工艺路线要选择合理,如在粗加工时要尽量去除掉多的材料,让工件释放出更多的应力,减少因线切割加工时工件变形造成的夹丝现象。
(3)一般称厚度在 3mm 以内的工件为薄工件,加工时必须采用封闭式切割,从毛坯内部打工艺孔穿丝加工,避免工件因产生应力变形而夹断电极丝。且加工时要提高电源脉冲幅值,加大脉冲宽度,采用较粗的电极丝,使放电间隙加大,同时要将工件夹紧防止冷却液对它产生过大的振动,从而减少断丝[6]。厚工件一般是指厚度在100mm以上的工件,加工此类工件引起断丝的主要原因是排屑不畅。为此应尽可能地增大放电间隙(一般应大于 0.02mm),使工作液在加工过程中充足稳定的包裹住电极丝并进入到加工区内,增强排屑效果,提高切割的稳定性,减少断丝。
(4)切割铝材会加快导电块磨损并会切出窄缝,加工时窄缝会使钼丝产生抖动并使工件上出现搓板纹,且会使工作液内含有大量的铝质蚀除产物,容易导致断丝现象,为此切割铝材要经常更换导电块和工作液[7]。
5.电参数的因素
在高速走丝电火花线切割加工中,选择合理的电参数,可以有效地减少断丝,提高加工效率和精度。
(1)为减少断丝几率,加工时选择脉冲间隔与脉冲宽度的比值在3~4倍之间,工件与电极丝之间的放电间隙在0.01mm左右。同时在加工过程中适时的调整脉冲间隙开关(工件越厚,脉冲间隙要调宽一些,工件越薄,脉冲间隙则要调窄一些),直到电流表上指示电流稳定在某一数值且指钟摆动平稳为止[8]。
(2)在加工前要使预置的进给速度与工件的蚀除速度相当,这样加工出来的表面精度高,且不易断丝。同时正式加工的进给速度一般调整到试切时的80%~90%,有助于减少断丝。
(3)电极丝因直径和材料的不同,所以其所能承受的短路电流峰值是有限度的。工作时的峰值电流一般为电极丝所能承受的最大短路电流峰值的75%~90%,应在 40A 以内,平均放电电流小于 5A,同时减小放电电流的上升率以降低电极丝的损耗,可提高加工精度,并延长电极丝重复使用寿命,防止断丝。选择合理的电参数将有效地减少断丝,表2 是对于一定厚度的工件,电参数的选择情况:
表2 一定厚工件的电参数选择
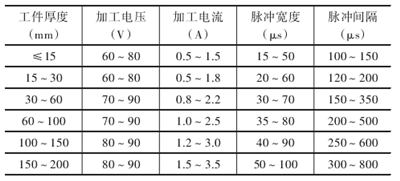
6.工作液的因素
选择合适的工作液成分、性能、浓度和水压等将有助于减少断丝,同时切割软材料时,要对工作液进行适当调整,且要定期更换工作液。
(1)为了提高切割的稳定性,并减少断丝几率,一般选用水基或含油成分少的工作液,同时在调配工作液时,最好不要使用自来水,因为自来水中存在钙和镁等有害于电蚀加工的离子[3]。
(2)工作液的性能好,将有助于减少断丝几率。为此工作液需要有一定的绝缘性能,较好的洗涤性能和冷却性能,以及减少脉冲能量损耗和改善电极丝损耗的性能。为有助于产生高频脉冲火花放电通道,并实现能量转化与传递,同时放电结束之后又能及时恢复绝缘状态,工作液要有一定的介电性能。此外理想的工作液应能产生合适的镀覆现象,保护电极丝[9]。
(3)工作液的浓度对电极丝是否发生断丝有至关重要的影响。工作液浓度太高,易在放电时产生气泡,致使放电在空气中进行而产生电弧,会烧断电极丝[10],工作液浓度太低,将使工作液绝缘性能降低,电阻率减小,降低了对工件的润滑作用,也容易断丝,因此一般工作液浓度控制在5%~10%左右。在进行大厚度工件切割时,因为切缝较窄,导致工作液很难渗透到切缝内,排屑困难,易产生短路而引起电弧放电,从而烧断电极丝。此时需调整工作液浓度到 3%~5%左右,容易使工作液进入切缝内,带走切屑,使加工比较稳定,且不易断丝。
(4)线切割加工中工作液的冲刷作用相当重要,加工电流越大,切割就越迅速,则产生的切屑就越多。此时需要的水压要求就越高,以便将切屑快速带走,减少断丝几率,水压最高可达1.5MPa/cm
[11]。
(5)切割铝、铜等软性材料时,为了提高加工效率和表面光洁度,减少断丝现象,可采用一些专用冷却液,也有利于环境保护。
(6)若线切割机床每天工作8h,则需在工作8~10天后更换工作液,对于连续工作的线切割机床,工作180~200h 后应更换切割液,以免工作液中杂质太多,造成断丝。
7.操作使用的因素
正确操作机床,注意有可能造成断丝的细节,将有助于减少断丝,提高加工效率。在加工过程中切勿切换功能键,以免开关接触不良造成短路从而引起电极丝烧伤,造成断丝。在加工结束时,切割掉的部位会在重力的作用下坠落,此时电极丝极易被夹断,可采用磁铁吸附和夹板夹持等方法及时固定。为减少电极丝在换向时造成的冲击,以及张紧力不均匀造成的断丝,在贮丝筒两端应该预留5~10mm宽度的钼丝间隔[11]。在切割过程中,如果贮丝筒换向时没有切断高频电源,会导致处于切割部位的钼丝在短时间内因温度过高而产生烧丝,因此在加工时需检查贮丝筒后端的行程开关是否失灵[12]。中途停机时必须先切断高频电源,否则会导致电极丝在短时间内因温度过高而产生烧丝[13]。同时停机床时,最好停在两个行程开关位置(贮丝筒刚好换向时按下急停),因为如果此时钼丝张力过紧,则电极丝冷却后可能会挣断钼丝,而这样即使断丝了,损失的电极丝会很少,剩余部分仍可继续使用,减少了损耗,此外如果不加工零件时还应该松开丝头一端。在拆丝和上丝时,会剪下很多长度很小的电极丝,可能会混到电器部位中或夹在走丝装置中,引起短路,造成断丝,需将这些短头集中放置。
8.结论
影响高速走丝机床断丝的原因有很多,本文通过一系列的实验和前人的研究,总结出了针对这6个方面可能出现的问题的预防措施,大大减少了断丝几率,对于提高生产精度和加工效率有一定的借鉴意义。
投稿箱:
如果您有机床行业、企业相关新闻稿件发表,或进行资讯合作,欢迎联系本网编辑部, 邮箱:skjcsc@vip.sina.com
如果您有机床行业、企业相关新闻稿件发表,或进行资讯合作,欢迎联系本网编辑部, 邮箱:skjcsc@vip.sina.com
更多相关信息