基于多传感器的高速 CNC机床集成监控系统设计
2018-1-22 来源:旅游职业学院信息工程 郑州旅游职业学院 作者:王珂 陈婉
摘要:复杂工况对于高速 CNC机床加工的精度以及其安全都有很大的影响,因此要设定检测参数阀值,通过检测数据预期对比来判断加工工况是否安全。设计了基于多传感器技术的高速 CNC 机床集成监控系统,对该系统的工艺进行了设计,同时还设计了系统硬件以及开发了 PLC 软件程序,另外对传感器选型进行了说明,并且完成多传感器与840D/828D 数控系统的无缝衔接。最后通过实际试验证明了该监控系统提高了高速 CNC机床在复杂工况下工作的安全性以及生产过程的可控性,同时使得生产产品质量以及其效率得到了保障。
关键词:高速车削;工况预测;集成监控;多传感器
可靠 的 工 况 状 态 是 高 速 CNC 机 床 的 生 产 效率、加工产品质量以及设备安全性的重要保障。因为高速 CNC机床加工的过程具有柔性化及动态化等特点,所以加工过程及其运行状态的监控均包含有明显的复杂性[1-3]。尽管我国当前自主研制的机床的定位及反复定位精度已经很高,但是由于加工的过程很复杂,同时伴随有振动、刀具损耗和热力耦合变形等要素影响,从而致使生产精度及稳定性等特性降低,所以生产过程的稳 定性及可 靠性、产品质量及生产效率等方面和先进国 家还有很大的距离[4-5]。实际生产过程中,由于工艺参数的合理选择、切削振动、刀具磨损、受热变形等诸多影响因素致使加工成品与理论模型之间存在误差,设备性能的发挥和寿命的保障、加工效率和成本等都是需要考虑的因素,这些都离不开加工过程监测技术。对加工装备和加工过程的监控可以有 效保证产品的最终加工精度及全面掌握机床运行 过程中各单元的运行状况,提高机床工作性能,消除废品的产生、降低成本。监控技术 可以提 高加工过程 的可靠性和可控性,要提高加工稳定性 和 可靠性、加工质量和加工效率,不但要加强机床设计和工艺的基础研究,还要善于运用现代化的计算机技术和信息化技术和监控手段,增强加工装备和加工过程的感知和控制功能。
机床和加工过程的监控技术是获取信息、发现问题和解决问题的途径,是实现数字制造、智能 制造的前提和基础,是进行高效、高质、安全、可靠 加工的有利保障,只有对机床、刀具和加工过程进行监测,才能获知设备和过程状态信息,从而据此进行智能优化控制,所以说先进的监控技术是实现智能制造和使机床变聪明的基础和唯一可行的途径。因此本文设计了基于多传感器技术的高速 CNC 机床集成监控系统,对复杂工况进行实时监控,对加工质量进行全程的控制和评测。
1 、集成监控系统工艺设计
高速 CNC机床复杂工况下集成监控系统工艺流程见图1,在加工开始之前,利用虚拟测试过程实现每一项代表性工况的检测工作并将其特性保存至数据库,同时作为工况的辨别以及其参数优化的参考依据。
多传感器的监控将涉及全部生产过程,针对如碰撞、刀具破损、崩刃、超载及颤振等突发性事故完成实时检测甄别,然后动态检测刀具的损耗程度以及切削的振动状态,当检测到刀具损耗时开启机器视觉过程以此来确定其损耗程度,在线检过程完成主要节点以及加工结束的检测,以此来确保生产质量。
该集成监控 系统利用数控系统实现对复杂工况的控制,将测头及 CCD 看成刀具安设在对应的位置,利用数控程序及机床自身的 工作实现其检测,因此该集成监控系统不仅仅含有对硬件的集成而且还有对软件的集成。
2 、监控系统设计
将检测到的主轴电 机功率 信号及切削振动信实时传输到840D/828D 数控系统及上位机,并且通过840D/828D HMI R 变 量 模 式 可 以 对 保 存 在200~203范围内的检测数据进行实时查看,同时利用数控系统实时处理检测数据并 实行对应的控制步骤,然后利用上位机监控界面实现对检测数据的实时显示。
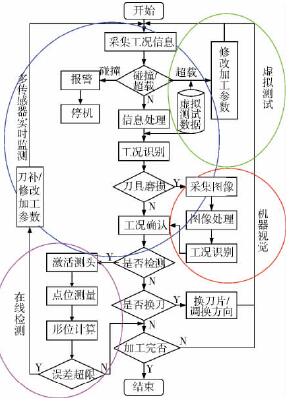
图1 集成监控系统工艺设计
2.1 传感器选型
传感器的选型包 括加速度传 感 器和功率传感器,如表1所示。
2.2 硬件设计
利用嵌入式监控 系统实现各 硬 件接口即加速度、电机电流及温度等信号接口的数据采集以及传送[6],监控系统结构原理见图2。
表1 传感器参数及安装位置

加速度传感器的信号输出运用4线制连接到前置专用信号采集模块 CS2ACSF/CS2ACPW 将其转变成以太网信号输出再连接到嵌入式监控系统的以太网接口[7],从而完成检测数据采集,其采集的频率是10Hz;同理功率传感器的信号输出运用5线制连接到前置专用信号采集模块 CS2ACPW 转变成以太网信号输出再连接到嵌入式监控系统以太网接口,从而完成检测数据采集,其采集的频率是10Hz。
2.3 监控系统软件设计
依据非正常工况 的急迫程度 来 设定其优先等级,该集成监控系统按照工况的优先等级从高到低的次序往复扫描,同时自 动采 用相应的应对方法。设定最高优先等级的工况是超载、超限等可能致使严峻事故或者损伤设备的状况,如果检测到振动或者功率超越设定的最高阀值,同时连续时间超越设定最高时间,那么系统将鸣 起警笛并照亮警灯,与此同时系统对该报警进行 记录存档。
依据每一道加工工序条件以及系统的规定范围设定各自的最高阀值及其连续时间。设定 像发生刀具毁损或碰撞等紧急事件时的连续时间通常小于等于15ms,从而保证在没有导致设备损伤之前启动报警系统同时实施相应措施;设定像刀具磨损等非紧急事件时的连续时间适宜延长60~90ms。
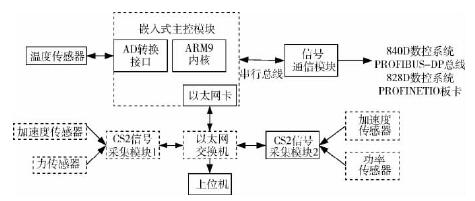
图2 监控系统结构原理图
2.4 PLC开发程序设计
通过 PLC自动控制集成监控系统的运行,其部分 PLC开发程序见图3。
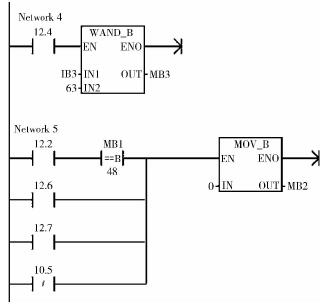
图3 PLC开发程序
2.5 与 CNC的无缝衔接设计
通过运用840D/828D 扩展接口编辑集成监控HMI窗口实现与 CNC 的无缝集成。首先,设计自动及程序两种方式启动集成监控系统界面,其相应的配置文件是 MA_AUTO.COM 及 PROG.COM,其存储 在 PCU50 的 硬 盘 中 且 保 存 路 径 是:\DH\CUS.DIR\;其次创建界面显示文本:设定界面文本保存文件名是 ALUC_XX,存储路径是:\OEM\,文本代码区间85000~89899;第三,设计编程各界面中的水平及垂直方向各8个软键,实现界面的跳转;第四,设计开发的集成监控系统集成在 HMI界面的 HEBUT 软 键 中,点 击 HEBUT 软 键 进 入 高 速CNC机床集成监控系统界,采用 PROFIBUS 总线实现其间的通讯工作。通过软硬件上的集成,完成了监控系统与 CNC的无缝衔接。
3 、试验结果
HTC2550hs高速数控车削中心,数控系统西门子828D 系列,选取加工直径是600mm 的45钢棒料,主轴的 转速、电机 功率及最高 扭 矩分别是 0~6000转、20.5/15kW 及162N·m,X 轴及 Z轴的移动 速 度 和 进 给 电 机 功 率 分 别 是 60m/min 和4.71kW,Z轴(主轴)、X 轴的最高进给抗力分别是1290N、1720N,人为 设 定 六 种 不 同 的 工 况 条 件,其试验结果见表2。对于预设的过载、碰撞、颤振、刀具严重磨损的异常工况识别和处 理,不同级 别 的警报响起,警灯点亮,并记录下此时的最大值和持续时间。
多传感器监测到刀具磨损时,会调用基于机器视觉的刀具状态诊断功能。由于环境噪声、毛胚或材料的瑕疵可能造成的传感器误报,会导致错误的控制决策,所以采用多传感器实时监控与 CCD 分时监控手 段,确 保 刀 具 工 况 及 时 准 确 的 识 别 与 控制。确认为磨损状态后,以 PLC 变量的方式反馈换刀信息和刀补值。
根据试验结果说 明该集成监 控 系统能够及时精确的鉴别高速 CNC 机床 的 各种复杂工 况,并且根据工况界别结果做出对应的控制措施。
表2 六种工况及相应的识别结果与应对措施
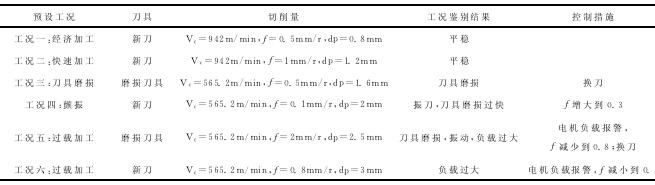
4 、结 论
基于多 传 感 器 的 高 速 CNC 集 成 监 控 系 统 不仅提升了 加 工 过 程 的 可 靠 性 及 可 控 性,而 且 还 提升了其稳定性以及加工质 量与效率。同时用户可以很简单、方便、直观的运用该系统,在很大程度上提高了 其 对 复 杂 工 况 的 预 测 感 知 能 力 以 及 监 控能力。
投稿箱:
如果您有机床行业、企业相关新闻稿件发表,或进行资讯合作,欢迎联系本网编辑部, 邮箱:skjcsc@vip.sina.com
如果您有机床行业、企业相关新闻稿件发表,或进行资讯合作,欢迎联系本网编辑部, 邮箱:skjcsc@vip.sina.com
更多相关信息