自适应控制系统在数控机床闭环控制中的应用研究
2019-4-29 来源:广东松山职业技术学院 作者:杨秀文
摘 要:利用自适应控制系统,实现在线检测数控加工过程中引起加工误差的随机因素参数及工件的精度指标,实时调整切削加工参数,提高加工零件的精度。研究适应当前数控机床的“PC+自适应控制器”结构,实现数控机床自适应闭环控制,提高数控加工过程的自适应控制能力、加工精度及加工效率。
关键词:数控机床;自适应控制系统;闭环控制
1、数控机床伺服控制系统
数控机床伺服系统控制方式可分为开环控制系统、全闭环控制系统、半闭环控制系统。数控机床半闭环控制系统的检测装置为编码器等,检测元件安装在进给伺服电机轴端或滚珠丝杠轴端,通过测量电机轴或丝杠轴的转角及角速度并与CNC装置的指令值进行比较,用差值进行控制,间接控制工作台的实际位移;数控机床全闭环控制系统的检测装置可采用光栅尺或者磁尺等,安装在机床工作台上,直接测量工作台的线位移和线速度,并与CNC装置的指令值进行比较,用差值进行控制。
2、自适应控制系统
自适应控制系统是指在随机变化环境中,对工作过程中监控参数实时在线监测,参照给定评价指标或最佳条件不断地对当时的工作状态做出判断,并以闭环控制方式对工作状态的判断结果按照一定的处理逻辑(算法)进行调节,使系统达到最佳综合效果的控制系统。
3、数控机床全闭环自适应控制系统工作分析
数控机床全闭环自适应控制系统是在数控系统本身的速度和位置伺服控制之外,利用自适应控制系统在线实时监测切削速度、切削进给量、主轴转速、机床变形量、刀具磨损量、切削力等各种随机加工过程参数,将在线检测到的数据通过信号采集装置和数据处理模块,经过自适应控制系统运算评价,分析实时加工的尺寸误差是否超过了零件精度指标所规定的阈值,并实时校正加工参数,传送到数控系统,数控系统进而自动调整加工过程参数,消除机床加工过程中机床各种状态变化和外界扰动因素引起的影响,从而减小加工误差,优化加工过程。数控机床全闭环自适应控制系统加工流程如图1所示。
数控机床常用的全闭环自适应控制系统分为约束自适应控制(ACC)和优化自适应控制(ACO)两类。
约束自适应控制(ACC)是在切削过程中以功率、切削力、切削速度等一个或几个参数为约束,预先设置参数的约束值,并在切削过程中在线检测并比较规定变量的实际值与约束值之间的差值,进而实时调整切削进给量,使规定的过程参数变量控制在规定的约束值范围内。约束自适应控制系统需要在线检测的参数较少,是数控机床粗加工过程中适宜采用的自适应控制系统。
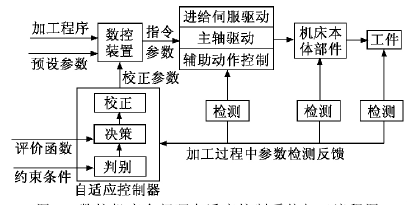
图1 数控机床全闭环自适应控制系统加工流程图
优化自适应控制系统(ACO)是指在加工过程中一个或几个参数受过程和系统的约束条件控制,在加工过程中,规定过程变量的约束条件,建立约束评价函数fn=f(x,y,z,…),根据检测到的可控变量和过程变量的实时数据,得到约束条件下对应最优f值的可控参数变量的最佳组合,使加工过程在保证精度的条件下获得最大生产率和最低生产成本。优化自适应控制系统可保证每个函数都达到最优而不超过约束,以使切削过程达到最优化为目标,是一种较高级的自适应控制,但控制过程中需要在线辨识的参数较多,计算量大,结构复杂,适宜用在数控机床自动加工模式,如DNC、FMS、CIMS中。
4、数控机床全闭环自适应控制系统的实现
数控系统全闭环自适应控制具有延长刀具寿命、提高加工精度、提高工作效率、稳定系统、适应非线性和时变性等显著优点。但是自适应控制系统控制器参数调整算法复杂,计算量大,检测系统中传感器及检测装置一般需要安装在机床工作台的下方,影响正常的加工作业,且可靠性不高。目前自适应控制系统在数控加工中的应用不是很普及。随着计算机技术的迅速发展,控制理论、数学建模的推广深化完善和在线检测技术的发展,数控系统自适应控制技术必将进入迅猛发展的实用阶段。目前自适应控制在数控机床控制系统中的实现主要有以下方式:
4.1 人工自适应控制过程
人工自适应控制工作过程是在数控加工过程中由操作人员对加工过程中需要控制的过程参数进行监测和数据采集,依据事先建立的切削过程数学模型或数据库及操作人员的知识和经验得出调整参数,由操作人员将调整参数输入给机床控制系统,对需要控制的切削参数进行校正。该系统的控制效果主要取决于操作人员的判断和经验知识,加工过程中状态变化的获取和调节适应的工作主要由人工完成,其主观性较强,不具有实时性,但绕过了自适应控制过程中在线测量、计算量大的难点。已有文献说明,人工自适应控制技术可使生产效率明显提高,是目前适合我国国情的一种技术方案,随着控制效果及智能控制技术的应用,这种控制系统将逐步退出市场。
4.2 基于单片机控制的数控机床自适应控制系统
基于单片机控制的数控机床自适应控制系统的抗干扰性强、可靠性高、指令系统效率高,适用开放型数控系统。该系统通过光栅、磁栅等检测单元检出刀具的绝对坐标,即工件瞬时直径,由自适应控制系统得到最佳切削速度和最佳转速,驱动变频器实现数控机床主轴电机实时转速调整控制,从而实现恒切削速度自适应控制。
4.3 基于PC的数控机床自适应控制全闭环控制系统
基于PC的数控机床自适应控制全闭环控制系统可以在Windows平台下自行开发。借助插入控制板的编写软件程序,实现数控机床自适应控制的全闭环控制,该系统具有工业机的柔性和CNC系统的稳定性和可靠性。基于PC的数控机床自适应控制全闭环控制系统结构框图如图2所示。
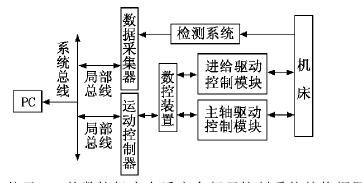
图2 基于PC的数控机床自适应全闭环控制系统结构框图
4.3.1 数据采集器
“PC+自适应控制模块”控制系统的数据采集器模块可以直接接收由检测系统处理好的数字量,也可以通过传感器等检测装置对工作过程信号进行数字采样、组合,并快速传输给PC进行分析和后期处理。数据采集器工作过程包括信号采集、信号调理、A/D转换、信号触发控制和数据采集器与局部总线接口的通信处理等。
4.3.2 运动控制器
运动控制器是控制电动机运行方式的专用控制器。运动控制器是决定数控机床自动控制系统性能的主要器件,在数控机床自适应全闭环控制系统中,对于简单控制系统,采用单片机设计的运动控制器即可满足要求,且性价比较高。为提高加工精度及加工效率,数控机床对加工过程中的实时随机参数在线检测要求很高,在数控机床自适应控制系统中可以采用基于PC总线的以DSP和FPGA作为核心处理器的开放式运动控制器,PC与运动控制器采用上、下位机模式,将运动控制器嵌入PC机,由运动控制器实现运动参数计算,PC机完成信息处理,提供数控系统多轴协调运动控制和复杂的运动轨迹规划、实时插补运算、误差补偿、伺服滤波算法。为实现数据快速通讯和控制,PC和运动控制器之间可以通过ISA工业标准总线形式进行通讯。
5、结束语
数控机床已经广泛应用于加工生产,数控机床的精度和效率已经成为决定生产效率的主要因素,采用全闭环自适应伺服控制系统,能够通过在线检测引起加工误差的随机因素参数,实时调整切削加工参数,实现数控加工过程的在线监测、实时控制,提高加工零件的精度。研究适应当前数控机床的“PC++自适应控制器”自适应闭环控制系统,对提高数控系统的自动化程度和自适应控制能力具有非常重要的意义
投稿箱:
如果您有机床行业、企业相关新闻稿件发表,或进行资讯合作,欢迎联系本网编辑部, 邮箱:skjcsc@vip.sina.com
如果您有机床行业、企业相关新闻稿件发表,或进行资讯合作,欢迎联系本网编辑部, 邮箱:skjcsc@vip.sina.com