3D打印在航空制造中的应用与创新
2019-6-21 来源:转载 作者:-
增材制造俗称3D打印。30多年来,3D打印从初级的原型样品制作方法逐渐转变为一种新兴的高级制造技术。在航空领域,3D打印正在进入产业化应用,通过选区激光熔化成型技术(SLM)制造出高度复杂的零件,或者以电子束熔化技术(EBM)替代锻造,成为航空企业又一轮技术竞争的载体。
一、3D打印的技术分类
1、SLA(StereoLithography,光固化成型技术)
指利用紫外光照射液态光敏树脂发生聚合反应,逐层固化并生成三维实体。SLA制造的工件尺寸精度高,是商业化较早的3D打印技术。
2、CLIP(ContinuousLiquid Interface Production Technology,连续液体界面提取技术)
是Carbon 3D公司在SLA技术的基础上开发的具有革命性的3D打印技术,将3D打印的速度提高了100倍。CLIP从底部投影,使光敏树脂固化,未固化的部分通过控制氧气形成死区,抑制光固化反应而保持稳定的液态区域,保证了固化的连续性。
3、3DP(Three-DimensionalPrinting,三维打印快速成型技术)
与传统二维喷墨打印接近,从喷头喷出粘结剂(彩色粘结剂可以打印出彩色制件),将平台上的粉末粘结成型,通常采用石膏粉作为成型材料。3DP技术目前主要有两项应用:全彩3D打印和砂模铸造。
4、PJ(Poly Jet,聚合物喷射技术)
其成型原理类似3DP技术,但喷射的不是粘合剂而是光固化树脂,喷射完成后通过紫外光照射固化成型。Poly Jet采用阵列式喷头,甚至可以同时喷射不同材料,实现多种材料、多色材料同时打印。
5、FDM(FusedDeposition Modeling,熔融层积技术)
利用高温将材料熔化,通过打印头挤出成细丝,在构件平台上堆积成型。FDM是最简单也是最常见的3D打印技术,通常应用于桌面级3D打印设备。
6、NPJ(NanoParticle Jetting,纳米颗粒喷射打印技术)
这是金属3D打印成型技术,使用纳米液态金属以喷墨的方式沉积成型,打印速度比普通激光打印快5倍,且具有优异的精度和表面粗糙度。
7、SLM(SelectiveLaser Melting,选区激光熔化成型技术)
是目前金属3D打印成型中最普遍应用的技术,采用精细聚焦光斑快速熔化预置金属粉末,直接获得任意形状以及具有完全冶金结合的零件,制件致密度可达99%以上。
8、SLS(SelectiveLaser Sintering,选区激光烧结成型技术)
与SLM技术类似,区别是激光功率不同,通常用于高分子聚合物的3D打印成型。SLS也可用于制造金属或陶瓷零件,制件致密度低,且需要经过后期致密化处理才能使用。
9、LMD(LaserMetal Deposition,激光熔覆成型技术)
该技术名称繁多,常用名称包括:LENS、DMD、DLF、LRF等。与SLM最大不同在于,其粉末通过喷嘴聚集到工作台面,与激光汇于一点,粉末熔化冷却后获得堆积的熔覆实体。
10、EBM(ElectronBeam Melting,电子束熔化技术)
其工艺过程与SLM非常相似,区别在于,EBM所使用的能量源为电子束。EBM的电子束输出能量通常比SLM的激光输出功率大一个数量级,扫描速度也远高于SLM。因此EBM在构建过程中,需要对造型台整体进行预热,防止成型过程中温度过大带来较大的残余应力。
二、3D打印在航空制造中的应用
1、打印涡轮叶片铸造型芯
在铸造金属涡轮叶片时,为了形成高度复杂的内部冷却通道结构,常使用陶瓷铸造型芯。铸造叶片冷却后,将叶片从模具中取出,同时内部的陶瓷型芯需要溶解掉。
目前,陶瓷铸造型芯的结构越来越复杂,通过传统的注射成型方式已经无法实现。奥地利Lithoz公司采用LCM技术制造陶瓷叶片型芯,可以满足航空航天和电力工业的需求。
LithaCore 450是由Lithoz公司自主研发用于3D打印陶瓷叶片型芯的硅基材料,制备精度高,烧结后的叶片型芯产品具有非常低的热膨胀率、较高的孔隙率、优异的表面质量和优良的洗滤性等优点。典型的应用有:单晶镍基合金涡轮叶片铸造型芯、定向凝固铸造型芯、等轴铸造型芯。
2、打印发动机支架
2018年11月1日,GE增材制造宣布,美国联邦航空管理局已批准3D打印支架用于波音747-8 机型的GEnx-2B发动机(双转子轴流式大涵道涡轮风扇发动机),该支架将取代传统制造的电动门打开系统支架,其作用是打开和关闭发动机的风扇罩门,制造设备为GEAdditive Concept Laser M2多激光器选区激光熔融系统。
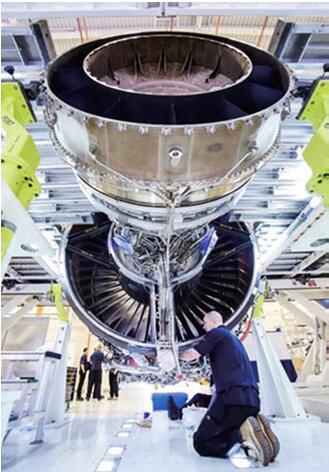
这款3D打印支架将在GE航空集团阿拉巴马州奥本市的工厂开始批量生产。GE公司表示,与传统方式制造的支架相比,3D打印技术将减少高达90%的材料浪费。在传统支架的制造中,因金属加工而产生的材料浪费约占50%。此外,3D打印支架采用了优化设计方案,重量比传统支架轻10%。
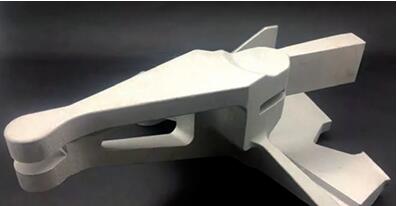
据了解,这款3D打印支架为GE航空创造了两个“第一”。首先,这是GE 第一个获得认证的由ConceptLaser公司的选区激光熔融设备生产的3D打印零件。其次,这是GE航空第一次完成一种3D打印零件从设计到生产于10个月内开发完成。
在进行支架生产时,一次打印可以生产4个支架,在构建室中4个支架以互锁设计的形式实现,打印材料为钴铬合金。
3D打印支架的制造成本低于原有成本,GEnx发动机的订单量为2200台,整体来看节约的成本非常可观,并且3D打印支架比传统支架更轻,将为航空公司节省燃料。
3、打印燃料喷嘴
2010年,空客将GE生产的LEAP-1A发动机作为A320neo飞机的选配,LEAP发动机中就带有3D打印的燃油喷嘴。2015年5月19日,A320neo飞机首飞成功,装有LEAP发动机的A320neo 同时获得欧洲航空安全局和美国联邦航空管理局的认证。
2018年10月8日,GE航空工厂庆祝第30000个3D打印燃料喷嘴的成功出货。该喷嘴自2018年以来一直在该工厂生产,标志着规模化增材制造的重要里程碑,预计2019年这种产品将达到40000支。
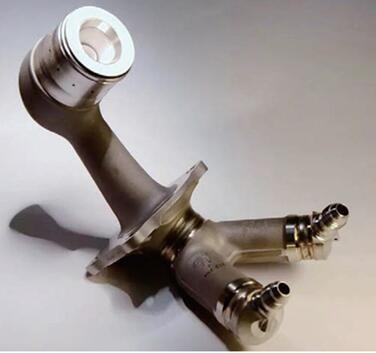
4、3D打印的其他应用
2018年,以下信息显示了3D打印在航空航天领域应用进展情况。
(1)总部位于佛罗里达州的金属3D打印机制造商Sintavia LLC在1月宣布,他们是第一家获得批准生产3D打印飞行零件的公司,零件采用粉末床熔合技术生产。
(2)波音公司与瑞士欧瑞康集团签署了一项为期五年的合作协议,涉及开发金属3D打印标准工艺和材料。除了通过各种不同材料和机器生产金属部件外,他们将共同收集数据来支持标准3D打印钛金属的生产工艺。他们的研究将首先关注工业化钛粉床融合3D打印,并确保该工艺制造的任何部件都能满足美国联邦航空局和国防部的必要飞行要求。
(3)FIT和NIK成立了一家名为FITNIK的新合资公司,该公司结合了两家公司的最佳产品,并在飞机研发中心Zhukovsky开展业务。
(4)威奇塔州立大学国家航空研究所是美国最大的大学航空研发机构,宣布将帮助航空航天工业中的3D打印聚合物创建新的技术标准文件,支持行业对3D打印聚合物的零件认证。
(5)金属3D打印专家、空客子公司APWORKS宣布,已被航空结构供应商PremiumAEROTEC收购为子公司。两家公司合并后,客户可以使用11个生产单元和各种材料。
(6)Gefertec与BIAS合作,对其送丝3D打印方法进行鉴定,用于生产大型结构航空航天部件。德国联邦经济事务和能源部资助了该项目,研究了保护气体含量、热输入对钛和铝组件机械性能的影响。
(7)据预测,到2021年,75%的新型商用和军用飞机将包含3D打印部件。纽约大学Tandon工程学院的研究人员提出了一种保护零件完整性的方法,即将QR码和条形码转换为隐藏在3D打印物体内。
(8)洛克希德马丁公司与海军研究办公室签订了一份价值580万美元的合同,协助其进一步开发航空航天业3D打印技术应用。
(9)以定向能源沉积(DED)技术而闻名的BeAM宣布与德国PFW Aerospace公司建立新的合作关系,后者为所有民用空客型号和波音787梦想飞机提供系统和组件。除了DED工艺之外,两者共同致力于为大型民用客机提供3D打印的Ti6Al4V合金部件。
三、3D打印创新技术
近期,《科学》杂志上发表的论文介绍,加州大学伯克利分校Hayden K. Taylor团队及其合作者发展了一种全新的3D打印技术,无需逐层打印,直接在高粘度树脂容器内通过光聚合一次形成整个3D物体。该技术具有以下特点:
(1)计算轴向光刻技术CAL。目前常规的立体光刻3D打印机主要使用扫描点光源或投影仪来顺序地逐层构建3D对象,这往往会导致边缘的“阶梯”效应,也难以生产柔性物体,因为可弯曲的材料在打印过程中会变形,并且打印某些特定形状的物体时需要支撑物。
Hayden K. Taylor团队则创造性地采用了一种计算轴向光刻技术CAL(Computed AxialLithography),在围绕垂直轴旋转时,将预先计算的光图案序列数字投影到树脂容器中,旋转时可以在树脂中照射出上千个不同的投影。随着时间的推移,累积的光照穿过聚合阈值的区域变为实心,而未穿过该阈值的区域保持未固化,从而一次性打印出所设计的三维物体。
(2)打印树脂材料的配置。未固化的液体,会有光线穿过它,因此整个过程需要有一个从液体到固体过渡的光照阈值,打印树脂材料的配置是这项技术的一个关键难点。研究人员所采用的3D打印树脂由混有光敏分子和溶解氧的液体聚合物组成。光照激活光敏化合物来消耗氧,只有在所有氧气用完的那些3D区域,聚合物才形成“交联”,将树脂从液体转变为固体,而未使用的树脂可以通过氧气加热来回收利用。这种氧气抑制机制,可以确保容器中心的物体在积聚足够强度的光而变成固体之前,最靠近光源的树脂不发生反应。
(3)CAL新型3D打印的灵感来源。基于CAL的新型3D打印技术的灵感来自医学领域的计算机断层扫描技术(CT),CT扫描从各个角度将X射线或其他类型的电磁辐射投射到体内,通过分析传输能量的模式来揭示物体的几何形状。
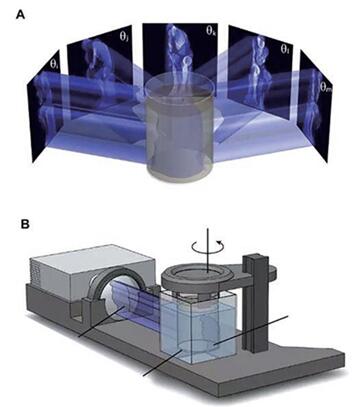
研究人员将层析成像算法与光聚合物的理想阈值相结合,并使用迭代优化法来提高目标几何的精度。通过这种全新的3D打印技术,他们打印了几种几厘米大小的物体来进行验证,包括雕塑模型、微型飞机模型、小格子和悬梁等。
(4)CAL新型3D打印的前景。由于现有的立体光刻技术已经很成熟,CAL很可能在现有方法不足的新兴领域才能找到最大用途。如:打印不能承受分层打印时施加力的软材料;制作具有光滑曲面的透镜;封装其他物体等。
作为原理验证,研究人员在螺丝刀的金属轴上封装打印出三维手柄,这是不可能通过现有3D打印技术实现的,需要昂贵的注塑工具。
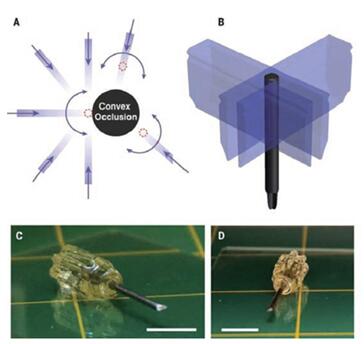
除此之外,由于未固化的树脂材料可以回收,100%可重复使用,这种3D打印技术几乎不产生任何材料浪费。而且,在某些情况下,CAL可能比目前的立体光刻法更快。
不过,速率、分辨率、对象大小和最终材料属性之间的权衡都值得进一步考虑,聚合反应的动力学以及树脂中的扩散和光散射,也将最终限制CAL打印的物体保真度。
总之,这项工作使3D打印从逐层打印方式过渡到一次性全三维打印,为3D打印开辟了全新的篇章,堪称里程碑之作。
四、结语
3D打印技术的应用颇具挑战,但它开创了更多可能性、更高的效率和更快的速度,帮助航空制造业克服发展瓶颈。其主要优势在于:
(1)提升生产速度。目前一台发动机的生产周期要2-3周,而巨大的市场需求和订单量要求达到一周7台的产能。利用增材制造技术一次成型复杂的发动机部件,避免了传统工艺中连接、热处理、加工和组装等繁琐步骤,能显著提升生产效率,缩短交货时间。
(2)创造更多可能性。设计工程师不再受到传统制造工艺的束缚,能够利用增材制造技术生产出最接近“大自然产物”的发动机部件。可以实现常规制造过程无法完成的复杂形状,帮助我们针对任何需求制造出最合适的部件。
(3)减少浪费和降低成本。增材制造技术使我们能在设计制造过程中的几乎任意一点做出修改,节省了制造时间和加工成本。将材料仅用于需要的地方,而无需对每个部件进行成本高昂的专业加工,在提升产品性能的同时节约了材料。
(4)数字产业的一部分。利用增材制造技术,工程师只需将所需部件的几何文件上传到3D打印机,便可立即打印出来。这显著减少了部件库存和不必要的运输时间,从而缩短交付周期。
(来源:《世界制造技术与装备市场(WMEM)》杂志2019年第2期 作者:中良 机械工业信息研究院)
投稿箱:
如果您有机床行业、企业相关新闻稿件发表,或进行资讯合作,欢迎联系本网编辑部, 邮箱:skjcsc@vip.sina.com
如果您有机床行业、企业相关新闻稿件发表,或进行资讯合作,欢迎联系本网编辑部, 邮箱:skjcsc@vip.sina.com
更多相关信息