数控机床驱动装置可靠性技术研究
2019-6-28 来源: 大连机床集团 工艺装备 大连金润液压 作者:饶彦平 尹阔 吕静
摘要:数控机床驱动装置的稳定性决定了机床整机的可靠性。通过分析驱动装置关键零部件的结构特点、加工及装配过程的关键精度要求,提出了相关的精度保证方法以及评定过程,采用技术手段控制关键零件的加工方法,提高了零件的精度及稳定性,并根据结构特点采用合适的装配方法,从而提高了驱动装置的可靠性。该方法可操作性强,有一定的推广价值。
关键词:数控机床;驱动装置;可靠性
目前,数控机床在制造业中所占的比重越来越大,数控机床在使用过程中的可靠性也越来越受到重视。在数控机床的可靠性中,定位精度及重复定位精度更是人们关注的焦点。机床的定位精度与重复定位精度决定了加工零件的精度,如数控车及数控磨加工外圆的精度、加工中心加工零件的孔间位置误差与加工模具时零件表面质量等均与定位精度及重复定位精度有关。定位精度与重复定位精度与驱动装置有关。
1 驱动装置分析
1.1 驱动装置结构
数控机床驱动装置(见图1)包括驱动电动机、电动机座、联轴节、前轴承、丝杠螺母、螺母座、滚柱/滚珠丝杠、轴承座、后轴承和锁紧螺母等。
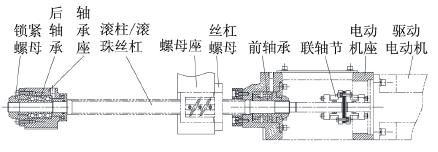
图1 数控机床驱动装置示例
1.2 安装时关键精度
数控机床驱动装置安装时应保证如下精度要求:1)丝杠及螺母副本身的加工及装配精度;2)安装前后轴承外孔(电动机座及轴承座轴承孔)的加工及装配时的同轴度误差;3)螺母座与丝杠螺母接合面的平行度精度;4)电动机座中电动机安装孔与轴承孔的同轴度精度;5)前轴承锁紧螺母的锁紧扭矩控制要求;6)后轴承锁紧螺母预拉变形量控制要求。
1.3 技术要求
驱动装置主要精度为电动机座、螺母座、轴承座(以下简称三座)的制造精度,以及与之相配零件的装配精度有关,其技术要求如下。
1)三座中的基准孔一般是装轴承或电动机止口安装孔,其精度要求为IT6~IT7,表面粗糙度要求为Ra1.6μm。
2)零件上用于连接的装配基面将直接影响三座与其相连接零件安装时的相对位置及加工中的定位精度,因而要有较高的平面度和表面粗糙度。其平面度要求为0.01~0.005 mm,表面粗糙度要求为Ra0.8~Ra1.6μm。
3)与装配基面平行或垂直的基准孔中心线,其平行或 垂 直 在 全 长 范 围 内 要 求 为 0.005~0.01mm。
4)当安装基准面与基体连接有刮研要求时,配合需精密吻合。
2 、加工过程分析
由于三座中,电动机座的制造 精 度 起 作 用,因此,本文对电动机座的加工过程进行分析。
2.1 电动机座加工工艺
电动机座(见图2)为数控机床Z 向驱动装置中与伺服电动机相连的关键零件,其总体尺寸不大,从其功能上看,一方面满足与电动机的连接及与床体的连接;另一方面通过轴承支承丝杠和联轴节等零件,故要求有较高的支承刚度,因此一般将其做成不规则的腔型结构(见图2)。
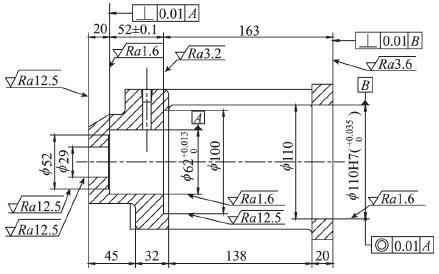
图2 电动机座尺寸图
为了提高电动机座的强度和刚度,一般采用力学性能较好的珠光体灰口铁HT250或 HT300铸造而成。
2.2 电动机座技术要求
电动机座的技术要求见表1。
表1 电动机座的技术要求
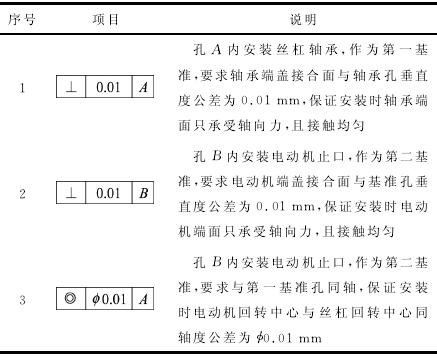
2.3 机械加工工艺过程
电动机座按成批生产时的加工工艺过程如下。
1)10序:以安装面定位加工工艺粗基准面。
2)20序:粗半精加工安装面及工艺孔。
3)30序:以20序安装面及工艺孔定位粗半精加工各面、孔。
4)40序:精加工安装面。
5)50序:以精加工后安装面及工艺孔定位精加工各面、孔。
2.4 工艺分析
2.4.1 精度要求
要求孔系与安装接合面平行度为0.01mm(比较严格),距离公差为±0.05mm,电动机安装面与孔系垂直度为0.01mm,电动机安装孔与轴承安装孔同轴度为0.01mm。从各项几何公差来看,此工件为高精度工件。
2.4.2 材料特性、加工方案及工艺措施
工件材料为灰口铸铁 HT250或 HT300,材质比较软,装夹力量过大则容易变形,为保证工件各项精度,对于单件生产需要对安装接合面进行刮研,保证平面度0.01 mm,在 坐 标 镗 床 上 对 孔 系 进 行 精镗,保证孔系与安装接合面的平行度及电动机安装孔与轴承安装孔的同轴度。但是对于目前机床的批量生产,电动机座需要大批量加工制造,每天的产量在60件以上,仍然使用传统工艺对工件进行加工制造,需要增加坐标镗床的数量,生产成本过大。
为了完成每天60件的生产任务,在保证工件加工精度的前提下,笔者对工件的加工工艺进行了调整,使用立式加工中心(VDL1000)对安装接合面进行粗铣留量,同时加工两沉孔(按 H7加工成品)以一面两销的定位形式对孔系及工件其他部分进行粗加工,使用立式加工中心(MDV55 带 光 栅 尺)对安装接合面进行精加工,同时加工两定位销孔(按 H7加工)孔距±0.01mm,再以一面两销的定位形式对孔系进行精加工。如此方法,只需在原有设备基础上新增2、台立式加工中心(MDV55)设计制作4套液压夹具,实行一人多机,即可降低每年数十万元的生产成本。
2.5 质量评定
试制的样件经过三坐标检测,安装接合面平面度为0.01mm,电动机安装面与孔系垂直度在 200mm 长度上为0.01mm,距离公差为±0.02mm,电动机安装孔与轴承安装孔同轴度为0.008mm。实践证明,新的工艺方法能够满足图样设计要求。
3 、装配过程分析
3.1 主要装配零件
该驱动装置是由滚珠丝杠副、前端电动机座组件、后端轴承座组件、联轴器及伺服电动机组成的,这种结构有着很高的传动精度、定位精度和重复定位精度。由于经过精密的加工、装配,加上丝杠的传动效率高,所以它有较好的高速特性。滚珠丝杠副由丝杠与螺母两大部分组成,工作时借助钢球在丝杠与螺母之间做点接触的滚动,从而实现丝杠或螺母的位移。
近年来,滚珠丝杠副作为数控机床直线驱动执行单元,在机床行业得到了广泛的应用。滚珠丝杠副具有极高的传动效率,可达90%以上,为传统滑动丝杠的 3 倍,并可实现可逆性传动,使运动部件的发热量大幅降低。滚珠丝杠副经过精密磨削、精密装配和严格检验,因此,有很高的传动精度。由于丝杠、螺母和钢球之间均为点接触,且本身经过硬化处理及多次定性处理,所以其磨损、变形极小,因而大大提高了其使用寿命。
电动机座组件是丝杠的主要支承单元,丝杠的前端支承在一对角接触轴承上,两轴承背靠背安装,能承受径向负荷和2个方向的轴向负荷,在有力矩作用时刚度很高,但同时这种结构对轴承孔的几何公差要求较高;预紧力是决定角接触轴承性能的重要因素,预紧力越大,径 向刚 度和轴向刚度都会提高,但同时温升也会加大,因此在安装过程中应采用合适的力矩控制轴承的预紧力,防止预紧力过大或过小。
联轴器能在一定程度上补偿连接件的轴向、角向和径向偏差,同时不会造成磨损和提前失效,最大程度地避免了伺服电动机振动、发热等因素对丝杠的影响。在安装过程中,连接轴的对中性越好,它的使用寿命和传递效果就越好,因此,应最大程度地保证联轴器的安装精度。为确保数控机床进给系统的传动精度、灵敏度和工作稳定性,在装配过程中应使用合理的工具、工装和检具,才能保证装配精度,获得合格的产品。
3.2 装配要求
驱动装置装配要求如下。
1)丝杠组件自身的精度。滚珠丝杠副作为关键的滚动原件,对机构的性能举足轻重,其精度的高低直接影响了整个机构的工作效果,因而应根据实际的工作要求(定位精度、传动速度和扭矩等情况)选择合适的丝杠组件。
2)丝杠中心线与导轨平行度。由于丝杠是精密部件,电动机座、轴承座的同心度以及轴线对床身导轨的平行度直接决定了丝杠安装后的综合精度,在整机试车过程中的定位精度、重复定位精度和反向偏差等都与丝杠安装质量的好坏有着直接的关系;因此,在安装丝杠前,应先检测电动机座、轴承座的单项精度、两座轴线对导轨的等距度及接合面的接触精度,并将各支座打上锥销孔定位;之后再进行滚珠丝杠副和其余件的安装。
3)丝杠装配后的轴向窜动与径向跳动。这两项精度对所传动部件的运动精度有很大影响,国家标准对于丝杠的轴向窜动和径向跳动有着严 格的规定,主要通过轴承的预紧进行控制。
4)联轴器的安装精度。要求安装时丝杠轴线与伺服电动机轴线同轴度为0.01mm。3.3 精度要求安装过程中应重点保证如下精度。
3.3 精度要求
安装过程中应重点保证如下精度。
1)轴承座、电动机座与床体接触面的接触精度,螺母座端面与接合面的接触精度:8个/25mm×25mm。
2)轴承座与电动机座轴承孔轴线与床身导轨的平行度0.01mm/200mm。
3)轴承座与电动机座轴承孔轴线与床身导轨的等距度0.02mm。
4)伺服电动机轴线与丝杠轴线的同轴度0.01mm。
3.4 保证精度的措施
保证精度的措施如下。
1)首先,将电动机座、轴承座各接触面、棱边、内孔各处清理干净,保证各安装面无飞边后,将其固定到床体面上;然后,将轴承座、电动机座孔内分别装上检验棒,采用专用找表胎,以床身导轨为基准,用千分表分别检测两检验棒的上母线、侧母线,按具体情况调整各件;最后根据实测误差配磨轴承座下的调整垫,以达到精度要求。精度合格后,将电动机座、轴承座分别打上锥销孔,复查各检棒精度合格后将检棒拆下。
2)滚珠丝杠副安装到轴承座过程中,应保证轴承端盖压靠到轴承外环上,前后锁紧螺母应采用力矩扳手安装并锁紧。定丝杠螺母座时,应检测螺母座端面与接合面的接触,保证螺母座与螺母接合面的平行度。为补偿由于加工过程中丝杠温度引起的伸缩变形,在装配时还应通过锁紧螺母对丝杠进行预拉伸。
3)该联轴器的安装精度主要通过加工保证,即电动机座上的110H7孔与A 孔的同轴度保证了安装后径向偏差的大小,伺服电动机和电动机座接合面与110H7孔的垂直度要求保证了安装后角向偏差的大小,在加工过程中应重点保证其精度。
4 结语
经过近几年对大连机床集团数控机床驱动装置生产过程中加工及装配工艺的研究,产品质量和出厂精度稳定性有了明显的提高,机床使用的可靠性也有了明显的提高。
投稿箱:
如果您有机床行业、企业相关新闻稿件发表,或进行资讯合作,欢迎联系本网编辑部, 邮箱:skjcsc@vip.sina.com
如果您有机床行业、企业相关新闻稿件发表,或进行资讯合作,欢迎联系本网编辑部, 邮箱:skjcsc@vip.sina.com