Tib2-B4C陶瓷刀具切削Inconel 718合金的切削性能与磨损机制
2020-4-8 来源: 广东工业大学机电工程学院 作者:谭大旺,郭伟明,吴利翔,曾令勇,林华泰
摘要:采用热压烧结法制备了组成 (体积分 数,下同)为80%TiB2-20%B4C(TB2)和 20%TiB2-80%B4C(TB8)的陶瓷并制成刀具,分别在切削速度为50 m·min-1和 150 m·min-1下 对Inconel 718合金进行切削加工,研究了陶瓷刀具的切削性能和磨损机制,并与 YG 硬质合金刀具的进行了对比。结果表明:TB2 陶瓷的抗弯强度和维氏硬度均低于 TB8 陶瓷的,但断裂韧度比TB8陶瓷的高约26%;在两种切削速度下,TB2陶瓷刀具的寿命最长,约为 TB8陶瓷刀具和 YG硬质合金刀具的2倍;TB2陶瓷刀具后刀面和刀尖的磨损机制主要为黏结磨损,边界沟槽的形成机制主要为轻微崩刃和冷焊层剥落;TB8陶瓷刀具后刀面和刀尖的磨损机制主要为崩刃,边界沟槽的形成机制主要为崩刃和冷焊层成片剥落。
关键词:TiB2-B4C 陶瓷;刀具;Inconel 718合金;切削性能;磨损机制
0 引言
镍基高温合金具有优异的高温强度、化学稳定性、耐腐蚀性、抗热震性等性能,广泛应用于航空航天、能源和化工等领域。Inconel 718合金是应用最为广泛的一种镍基高温合金[1-3],该合金的强度高、导热系数小且易产生加工硬化,属于难加工材料[4-5]。在加工Inconel 718合金时,为了获得较长的刀具使用寿命和较低的工件表面粗糙度,除了要求切削刀具材料具有较高的硬度外,还要求其具有较高的强度、红硬性、抗氧化性、断裂韧性和高温化学稳定性等[6]。
目前,用于高温合金切削加工的刀具主要为硬质合金刀具。但是硬质合金刀具的耐热性较差,导致其切削速度很慢,无法满足现代工业对加工效率的要求[7]。与硬质合金刀具相比,陶瓷刀具的硬度更高,红硬性和高温强度更好,加工高温合金时的切削速度更高且刀具寿命更长[8-9]。TiB2基陶瓷是一种新型刀具材料,具有高的熔点、高温强度、硬度以及优异的耐磨性能,可用于 切削难加工 材 料[10-14]。SONG等[15]用 TiB2基陶瓷刀具加工 Cr12MoV 模具钢时获得了良好的切削效果,以后刀面磨损高度为0.6mm 为磨损标准,其有效切削长度超过1700m。
B4C材料具有优异的硬度和抗弯强度,将其与TiB2 复合烧结得到的 TiB2-B4C 复相陶瓷具有优异的力学性能[16-18]。目前,TiB2-B4C 复相陶瓷作为刀具材料的研究较少。为此,作者制备了不同配比的TiB2-B4C复相 陶 瓷 并 将 其 加 工 成 刀 具 对 Inconel718合金进行切削,研究了不同切削速度下的切削性能,并与商用硬质合金刀具的进行了对比。1 试样制备与试验方法试验 原 料 有 B4C 粉 体,纯 度 99%,平 均 粒 径3μm;TiB2粉体,纯度99.5%,平均粒径5μm。工件材料为Inconel 718合金,屈服强度为1 100MPa,抗拉强度为1 310MPa,伸长率为23.3%,弹性模量为206GPa,导热系 数为 11.2 W·m-1·K-1,密度 为8 470kg·m-3,退火后的硬度约为2.5GPa[1]。
分别按照组成(体积分数,下同)为 80%TiB2-20%B4C(TB2)和20%TiB2-80%B4C(TB8)进行配料,在行星球磨机上以转速为450r·min-1球磨8h,磨球为Si3N4 球,球料质量比为2∶1,球磨介质为丙酮。球磨后的物料在50 ℃下旋转蒸发烘干,过100目筛后,倒入直径为50mm 的石墨模具中,在氩气气氛中以10℃·min-1的升温速率加热至2 000 ℃,保温1h进行热压烧结,压力为30MPa,随炉冷却。应用阿基米德 排水法测定陶瓷试样的体积密度。采用四点弯曲法在INSTRON-1195型万能材料试验 机 上 测 抗 弯 强 度,试 样 尺 寸 为 1.5 mm×2mm×25mm,下跨距为20mm,上跨距为10mm,压头下压速度为0.5mm·min-1。将陶瓷试样镜面抛光后,采 用 HVS-30ZC 型 维 氏 硬 度 计 测 维 氏 硬度,载荷为24.52N,保载时间为10s;应用压痕法测断裂韧 度,载 荷 为 98 N,保 载 时 间 为 10s。 使 用Nova NanoSEM430型超高分辨率场发射扫描电子显微镜(SEM)观察陶瓷试样的表面形貌(抛光后),以及维氏硬度测试后的压痕形貌。
将所制备的复相陶瓷加工成型号为SNGN120712T02020的标准刀具,刀尖圆弧半径为1.2mm。用复相陶瓷刀具和商用硬质合金(YG)刀具对Inconel 718合金进行连续切削,刀片安装前角为-6°,后角为 6°,主偏角 为 45°,切削速度分别为50,150m·min-1,切削深度为 0.5 mm,进给量为0.1mm·r-1。在切削过程中,使用 OLYMPUSSZ61型体视显微镜观察并测量刀具的边界磨损高度、后刀面磨损高度和刀尖磨损高度,当后刀面磨损高度达到0.3mm 时停止切削,对应的切削长度为有效切削长度,以有效切削长度来表征刀具寿命。采用Nova NanoSEM430型超高分辨率场发射扫描电子显微镜观察刀具后刀面的磨损形貌。
2、试验结果与讨论
2.1 陶瓷的微观形貌和力学性能
由图1 可 知:在 TB2 陶 瓷 中,B4C 增强相 (黑色)均 匀 分 布 在 TiB2(灰色)基体中;在 TB8 陶瓷中,TiB2增强相均匀分布在 B4C基体中。
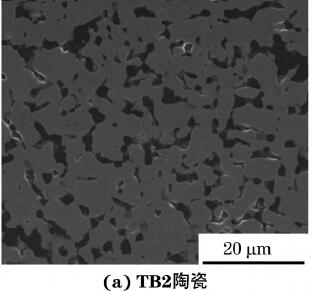
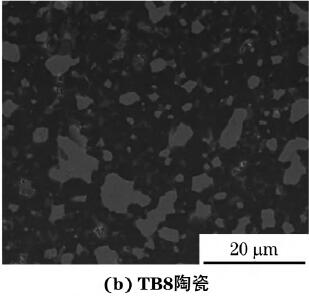
图1 TB2和TB8陶瓷表面抛光后的微观形貌
由表1 可知:TB2 陶瓷的相对密度、抗弯强度和维氏硬度 均 略 低 于 TB8 陶 瓷 的,但 断 裂 韧 度 比TB8陶瓷的高约26%;TB8陶瓷的维氏硬度比 TB2陶瓷的高,这 是 因 为 B4C 陶 瓷 的 本 征 硬 度 (35~43GPa)显著高于 TiB2陶瓷的(24~32GPa)。
表1 不同陶瓷的物理和力学性能
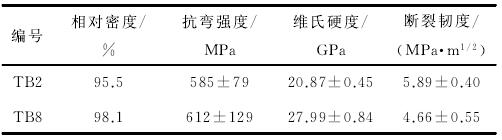
由图2可知:在 TB2陶瓷中,维氏压痕裂纹较曲折,裂纹在 TiB2基体上沿晶界扩展,在扩展过程中遇到 B4C晶粒即发生偏转,如箭头所指;在 TB8陶瓷中,维氏压痕裂纹较平直,裂纹在 B4C 基体中以及遇到 TiB2晶粒时基本都为穿晶扩展。这是因为 TB2陶瓷的断裂韧性高于 TB8陶瓷的。
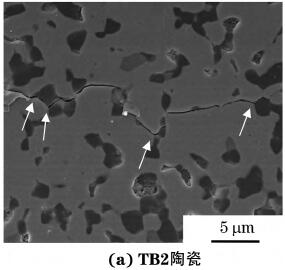
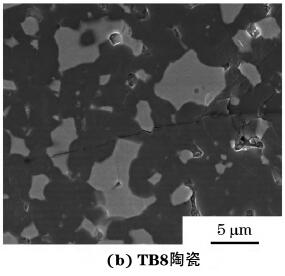
图2 TB2和TB8陶瓷的维氏压痕裂纹形貌
2.2 刀具的切削性能
由图3 可以看出:当切削 速度为 50 m·min-1时,TB2陶瓷刀具的有效切削长度超过800m,约为TB8陶瓷刀具和 YG硬质合金刀具的3倍,当切削速度为150m·min-1时,其有效切削长度超过340m,约为 TB8陶瓷刀具和 YG 硬质合金刀具的2倍,可见TB2陶 瓷 刀 具 的 寿 命 最 长;在 较 低 的 切 削 速 度(50m·min-1)下,三种刀具的后刀面磨损高度均随图3 不同切削速度下不同刀具后刀面磨损高度随切削长度的变化曲线切削长度的增加而平稳增加,没有出现快速磨损阶段,在较高的切削速度(150m·min-1)下,TB2陶瓷刀具和 YG 硬质合金刀具分别在切削长度达 100,200m 时发生快速磨损,TB8陶瓷刀具的磨损很快,在切削长度达到 100 m 时其后刀面磨损高度即达到300μm;切削速度为150m·min-1时三种刀具的寿命均约为切削速度为50m·min-1下的1/2。
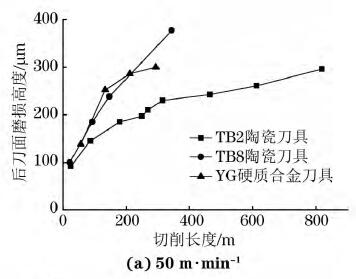
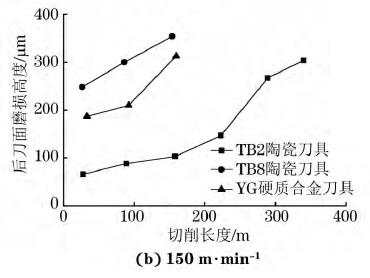
图3 不同切削速度下不同刀具后刀面磨损高度随切削长度的变化曲线
由图4可以看出:随着切削长度的增大,TB2陶瓷刀具和 TB8陶瓷刀具的边界磨损高度均先缓慢增加后迅速增加,而 YG 硬质合金刀具的边界磨损高度保持缓慢增加趋势;三种刀具的刀尖磨损高度均随切削长度的增加而增大,但 YG 硬质合金刀具的刀尖磨损得更慢。结合图3(b)分析可知:当切削长度小于250m 时,TB2陶瓷刀具的后刀面磨损高度大于边界磨损高度,而当切削长度约为300m时,边界磨损高度超过1 200μm,远大于后刀面磨损高度;当切削长度小于100m 时,TB8陶瓷刀具的边界磨损高度与后刀面磨损高度相差不大,但当切削长度约为150m 时,边界磨损高度超过900μm,远大于后刀面磨损高度;YG 硬质合金刀具的边界磨损高度始终小于后刀面磨损高度。随着切削长度的增加,陶瓷刀具的切削刃与刀尖变钝,变钝的刀尖对加工表面的挤压作用增强,导致材料的加工硬化更严重;在下一次刀具进给时,硬化的工件材料与刀具的边界接触,从而加快了边界磨损。同时,变钝的切削刃对工件过渡表面的挤压作用也增强,切削刀无法顺利切下待加工表面硬化层,使待加工表面与过渡表面交界处形成硬化毛边;硬化毛边对刀具的高频冲击造成刀具在边界处发生轻微崩刃,因而边界磨损迅速增加。与陶瓷刀具相比,YG 硬质合金的韧性更高,边界处不易发生崩刃;此外,切削温度对硬质合金的影响较大,而切削温度最高的位置位于切深中部。因此,YG 硬质合金刀具的后刀面磨损高度大于边界磨损高度。
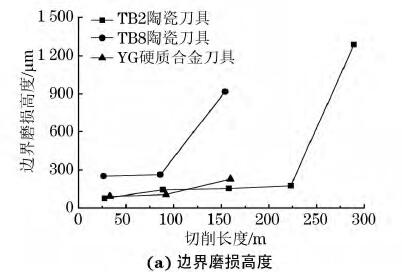
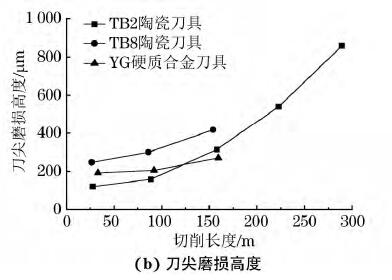
图4 当切削速度为150m·min-1时不同刀具的边界磨损高度和刀尖磨损高度随切削长度的变化曲线
2.3 刀具的磨损形貌
由图5(a)可以看出,在150 m·min-1下切削340.1m 长时,TB2陶瓷刀具的后刀面边界(N 区)发生了严重的沟槽磨损,刀尖处(C 区)的磨损高度小于边界处的,而后刀面(B区)的磨损高度最小。
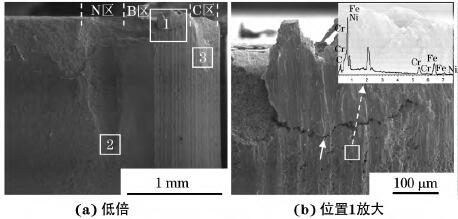
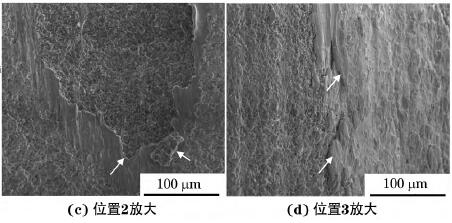
图5 在150m·min-1下切削340.1m长时TB2陶瓷刀具的磨损形貌
由图5(b)可以看出:在切削刃(位置1)处存在比较严重的积屑瘤,以及会导致积屑瘤剥落的裂纹;后刀面出现了黏结层,该黏结层主要含有镍、铁和铬元素,说明黏结层由工件材料形成,由于后刀面与工件之间存在持续的挤压和摩擦,黏结层会不断发生剥落和重新形成,因此会不断带走刀具表层的材料,导致后刀面磨损高度不断增大;在该区域还存在轻微的崩刃现象。综上可知,刀具后刀面的磨损机制主要为黏结磨损和轻微崩刃。
由图5(c)可以看出,后刀面边界(位置2)的磨损沟槽边缘存在工件冷焊层,冷焊层发生剥落使刀具基体裸露在外,在冷焊层上还黏结着刀具基体晶粒的剥落鳞片(如箭头所示)。随着切削的进行,陶瓷刀具边界处发生轻微崩刃,崩刃处挤压工件使工件过渡表面的材料在刀具后刀面形 成硬化的冷焊层;冷焊层在切削过程中不断地受到硬化毛边的冲击而发生剥落,剥落的冷焊层带走大量黏结在其上的刀具基体材料,导致沟槽不断向尾部扩大,从而形成边界区细长的沟槽磨损形貌。沟槽一旦形成,刀具边界对工件的挤压作用和工件表面的加工硬化程度均增大,从而加速沟槽的磨损。因此,刀具边界的磨损机制主要为轻微崩刃和冷焊层剥落。
由图5(d)可以看出:后刀面刀尖(位置3)存在与刀具基体结合比较紧密且比较厚的黏结层(如箭头所指),因此刀尖的磨损机制主要为黏结磨损。由于 TB2陶瓷的韧性较好,且以沿晶断裂为主,因此刀具材料更容易以拔出、脱落的形式被工件冷焊层和黏结层带走,从而造成后刀面的磨损。
由图6可知:在150m·min-1下切削154m 长时,TB8陶瓷刀具的后刀面边界(N 区)同样发生了图6 在150m·min-1下切削154m长时TB8陶瓷刀具的磨损形貌Fig.6 Wear morphology of TB8ceramic cutting tool after cuttingin 154mlength at 150m爛min-1:(a)at low magnification and(b)enlarged view of the rectangle严重的沟槽磨损,同时后刀面(B 区)和刀尖处 (C区)发生严重的崩刃和轻微的黏结磨损;TB8 陶瓷刀具的沟槽磨损形貌与 TB2陶瓷刀具的类似,但由于TB8陶瓷的断裂韧度较低,更容易出现大块崩刃,因此磨损沟槽的宽度更大;由边界区(图中方框)的放大形貌可见,崩刃处形成了新的切削刃,新切削刃较锋利,因此刀具对工件的挤压作用较轻,工件与刀具之间的冷焊作用较弱,沟槽磨损的原因主要为工件硬化毛边的冲击导致沟槽位置的冷焊层带着刀具基体成块裂开并剥落,而不是刀具晶粒被冷焊层黏结而带走,因此 TB8陶瓷刀具的边界磨损机制为崩刃和冷焊层成片剥落;由于新切削刃处的排屑阻力增加,因此崩刃处形成一些积屑瘤,如图6(b)中箭头所指。TB8 陶瓷刀具的后刀面虽然存在黏结磨损,但是由于 TB8陶瓷的断裂韧性低,因此后刀面磨损以切削刃崩刃破损为主;刀尖的磨损形貌与后刀面 的几乎一致,磨损机制主要为崩刃。 虽然TB8陶瓷刀具的硬度更高,但是 由 于断 裂 韧 度较小,同时崩刃和剥落现象严重,因此其寿命比 TB2陶瓷刀具的更短。
由图7(a)可以看出,在150 m·min-1下切削159.5m 长时,YG 硬 质 合金 刀 具 后 刀面(B 区)的磨损高度略大,但不同区域均以黏结磨损为主,同时后刀面边界发 生 轻 微 崩 刃 (如 图 中 箭 头 所 指)。由图7(b)可以看出,YG 硬质合金刀具后刀面存在明显的黏结层,且切削刃处存 在 积屑瘤,高度约为60μm,积屑瘤与刀具基体结合紧密。由于 YG 硬质合金的断裂韧性较高,其刀具的切削刃在切削过程中不易发生崩刃,可以保持比较锋利的切削刃结构,因此对工件的挤压作用较轻,工件的加工硬化不严重;后刀面边界没有出现因工件硬化导致的沟槽磨损形貌。但是,由于 YG 硬质合金抗黏结磨损性能差,其刀具材料更容易因为黏结层不断的剥落与形成而脱落,因此刀具寿命较短。
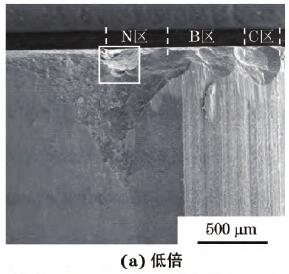
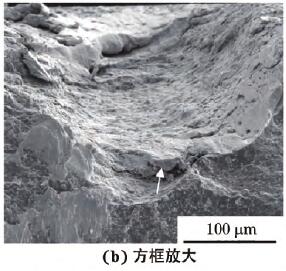
图6 在150m·min-1下切削154m长时TB8陶瓷刀具的磨损形貌
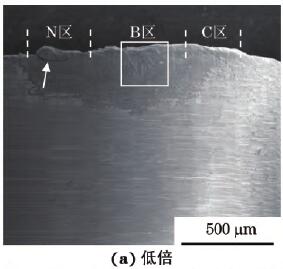
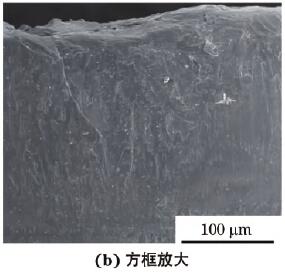
图7 在150m·min-1下切削159.5m长时YG硬质合金刀具的磨损形貌
与传统的 YG 硬质合金刀具相比,TiB2-B4C 陶瓷刀具由于断裂韧性较低,在切削高温合金时容易发生崩刃,导致切削刃过早钝化;钝化的切削刃使高温合金在切削过程中的加工硬化比较严重,导致刀具发生沟槽磨损。与硬质合金相比,TB2陶瓷具有更好的抗黏结磨损性能,因此 TB2陶瓷刀具的寿命更长。TB2陶瓷和 TB8陶瓷的硬度均超过20GPa,远高于高温合金的(约为2.5GPa),因此硬度不是影响 TiB2-B4C 陶瓷刀具加工高温合金时切削性能的主要因素。TB2陶瓷的抗弯强度虽略低于 TB8陶瓷的,但仍保持在一个较高的水平,陶瓷刀具并没有因为强度不足而发生整体断裂,因此抗弯强度也不是影响 TiB2-B4C 陶瓷刀具加工高温合金时切削性能的主要因素。TB8 陶瓷的断裂韧度低于 TB2陶瓷的,较低的断裂韧度易 导致切削刃崩刃,因 此TB8陶瓷刀具的崩刃现象比 TB2陶瓷刀具的更严重,这说明断裂韧性是影响 TiB2-B4C 陶瓷刀具加工高温合金时切削性能的主要因素。提高陶瓷刀具的断裂韧性,有利于保持切削刃的整体结构,减小切削阻力。综上可知,TiB2基陶瓷刀具在切削高温合金时的切削性能比 B4C基陶瓷刀具的更好,可以获得更长的刀具寿命。
3、结论
(1)采用热压烧结法制备了以 TiB2为 基 体、B4C为增强相的80%TiB2-20%B4C(TB2)陶瓷和以B4C 为基体、TiB2为 增 强 相 的 20%TiB2-80%B4C(TB8)陶瓷,两种陶瓷中的增强相都均匀分布在基体中;TB2陶瓷的相对密度、抗弯强度和维氏硬度都略低于 TB8 陶瓷的,但断裂韧度比 TB8 陶瓷的高约26%。
(2)对Inconel 718高温合金进行切削时,在切削速度为50,150 m·min-1下,TB2 陶瓷刀具的寿命约为 TB8陶瓷刀具和 YG 硬质合金刀具的2倍;当切削速度为150m·min-1时,三种刀具的寿命均约为切削速度为50m·min-1时的1/2。
(3)TB2陶瓷刀具后刀面和刀尖的磨损机制主要为黏结磨损,边界沟槽的形成是由于刀具发生轻微崩刃和冷焊层的剥落;而 TB8陶瓷刀具后刀面和刀尖的磨损机制主要为崩刃,边界沟槽的形成是由于刀具发生崩刃和冷焊层发生了成片剥落;TB2陶瓷的断裂韧性更好,更有利于保持切削刃结构的完整性和锋利程度,且具有更好的抗黏结能力,因此其刀具寿命更长。
投稿箱:
如果您有机床行业、企业相关新闻稿件发表,或进行资讯合作,欢迎联系本网编辑部, 邮箱:skjcsc@vip.sina.com
如果您有机床行业、企业相关新闻稿件发表,或进行资讯合作,欢迎联系本网编辑部, 邮箱:skjcsc@vip.sina.com
更多相关信息