一款背包塑料扣模具的设计与加工
2021-4-27 来源: 广东东莞理工学校 作者: 陈瑞兵
摘要 : 本文根据该背包塑料扣的结构特点 与生产要求,较为详细地介绍了塑件的成型工艺 方案 ; 包含塑件的工艺分析、型腔排布、分型面 的选择、模仁的加工方法及参数分析。同时探讨 如何有效降低成本和缩短生产周期。
关键词 : 分析、分型、镶块、参数
1.引言
随着模具行业的发展,市场竞争日趋激烈。 缩短模具的生产周期并降低生产成本已经成为每 个加工企业的追求目标。背包塑料扣由六个小塑料 件组成,如果把每件分开制作,就需要六套模具才 能完成,既加大了生产成本和生产周期,也达不到 客户的要求。故采用六件一套模的方式加工。
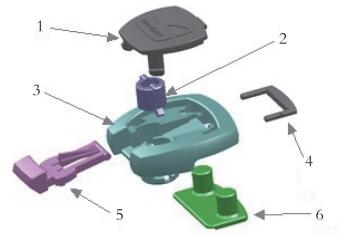
图 1 产品三维装配图
1. 塑件面盖 2. 连接件 3. 基座 4.插销 5. 固定插件 6. 固板
2.塑件工艺分析
塑件结构及装配情况如图 1 所示,材料是 ABS,收缩率为 5‰ 。因六个塑件有装配关系, 故外表面要求光滑平整,不得有扭曲、飞边、毛刺、 气泡、缺胶等注射成型缺陷 ; 这样就增加了以下 设计及加工难度。 1) 塑件形状各异、大小不一,且有许多通 孔,这样就要考虑塑件在模具中如何合理分布。 固定插件和连接件组合后插入基座内,如图 2(a) 所示。
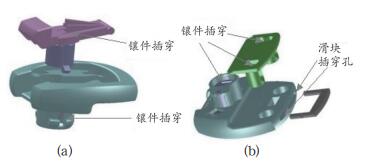
图 2 组合装配示意图
2) 因为固板和插销都要从两个不同方向插 入基座配合,基座两边的孔设计方式如图 2(b) 所示,采用前模碰穿后模加镶件的机构。由于基 座侧面是固定塑件的两个插穿孔,必须设计滑块 机构 ; 设计制作滑块时,要考虑滑块脱离塑件后 塑件对滑块的包紧力是否过大,会否造成塑件变 形、损伤等情况。因插穿孔是扁平型,并且是出 两件产品,出于节省材料并降低加工及装配难度 考虑,把滑块拆分为两个部分,前面插入模芯部分以螺丝固定。这样在加工及装配过程中,只要 保证两部分各自相配合便能达到要求。
3.塑件排布与分型
3.1 型腔排布
根据产品要求对模具的结构综合考虑后,选 择模仁钢材为 718,该钢材硬度为 HRC57-60, 经过热处理后氮化层具有组织致密、光滑等特点, 模具的脱模性及抗腐蚀性能高,使用寿命可达到 100 万次以上。 设计尺寸为 260*170mm,采用 6 模 2 腔 来排布,如图 3 所示。
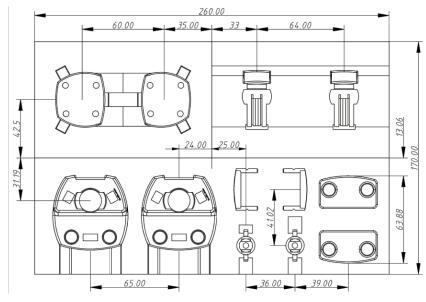
图 3
模具的型腔数目确定后,接着便设计型腔的 布局。主流道设于前模的中心轴上,至于分流道 出于多方面考虑应该满足如下要求 : 尽量保证各 型腔的充模压力相近,充模时间大致相同,并且 能均匀补料,这样才能保证塑件的尺寸及形状精 度,同时也能保证其力学性能。故采用以上排布 方式,既解决了充模问题,又可优化模具结构。
3.2 塑件分型
根据塑件几何形状等特点,开模时尽量使塑 件留在后模,有利于侧面分型和抽芯。该模具采 用 UG 模具设计软件进行分型,首先做好分型面 然后用抽取几何体这个功能,选择区域的方式把 整个前模和后模的面提取出来 ; 接着再跟分型面 结合成一个整块的片体,用该片体去切割镶块实 体便得到前、后模仁 ; 具体如图 4 所示。 根据型腔排布确定模具的前、后模非常重要, 因为其决定了型腔的朝向、进料方式、进料位置、摆放位置等塑料模具的设计要点。选择前后模可 采取如下原则,产品外观要求很高的一般作为前 模,反之则作为后模。经分析对六件塑件采用以 上最合理的分型方式最便于后期加工。
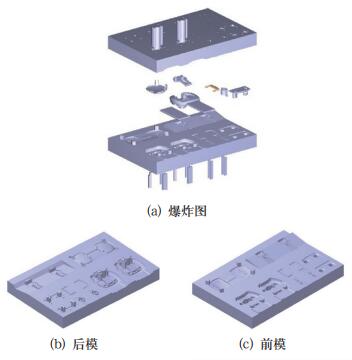
图 4
4.型腔与型芯制作
分型完成后型腔与型芯是一个整体,由于固 定插件的分型面有斜面和角度,如果采用 CNC 直接加工则要设计多个铜公进行清角,这样在材 料的的选用上就加大了成本,同时也加大了工期, 故采用拆分型芯方式。分拆后用线切割进行加工, 为了节省材料、缩短加工时间及维护方便,把前 后模各分拆成三块,这样就要解决以下难点。 1) 前后模的分型面采用分拆方式加工,加工 时要采取合适的加工工艺。 2) 多处的分型面设计采用了前后模碰穿结 构,在前后模型芯上形成了多个凸凹台,加工较 为困难。3) 加工时前后模型芯前部缺口处很难进行 清角,可采用小直径刀具,尽可能清除加工余量。 加工完毕后,可进行人工打磨或设计小铜公进行 清角。4) 模具型腔中间的台阶孔碰穿位在前后模 型腔中形成了多个孤岛,孤岛和前模型腔直角相 交,很难清角加工,这里采用了线切割镶件加工。
表 1 前模加工参数
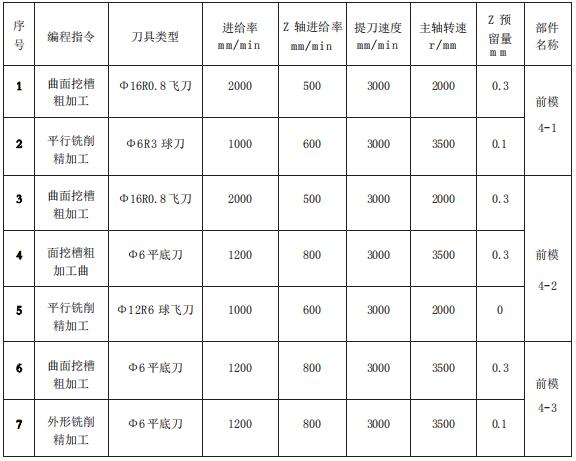
表 2 线切割加工参数
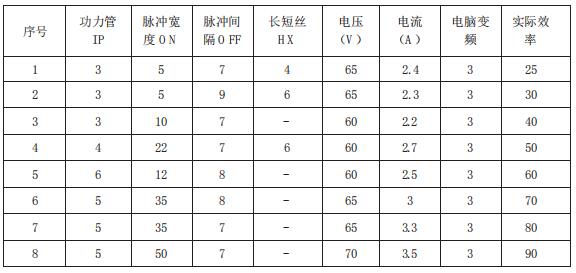
5) 前模要设计多个铜公进行清角,为节约 成本,各款铜公只设计加工了一个铜公(精公), 这样前模型腔的精加工余量尽可能小,以减少铜 公的损耗,如图 5 所示。
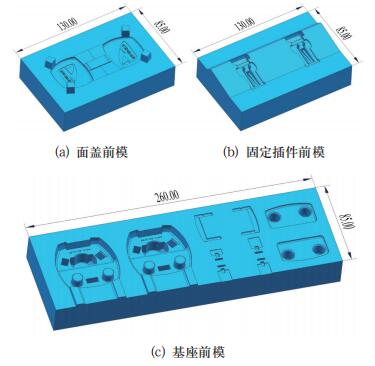
图 5
4.1 前模型腔加工
首先使用普通铣床和磨床加工两块 130*85*40mm 钢料,分别用于图 5(a)和图 5(b), 再 加 工 一 块 260*85mm 为 图 5(c) 使 用。 图 5(a)为专用塑胶扣的中心面盖,上面 有两个倒扣,一般需要做斜顶才能完成。这里采 用更合理的插入式脱模斜度方式加工。如图 5(a) 所示 4 个方形柱子,用来插入后模,三面都要封 胶,所以这里的加工精度要求较高,加工时要留 0.1mm 的余量做配模时用。倒扣留在后模型芯 用电极来加工完成。使用 MasterCAM 来编程, 用数控铣或加工中心进行加工,用 Φ16R0.8 镶 方合金刀粒圆鼻刀,进给率 1200mm/min,下 刀速率 500mm/min,抬刀速率 3000mm/min, 主轴转速 S=2000 转 / 分。用 3D 曲面挖槽刀路 对前模型腔曲面进行粗加工。采用相对尺寸,最 小加工深度和最大加工深度都设置成 0.2mm, 加工余量为 0.3mm; 采用螺旋下刀,下刀处为前 模型腔的中心,切削方式选择环绕方式 ; 加工完 成后需要做电极加工。
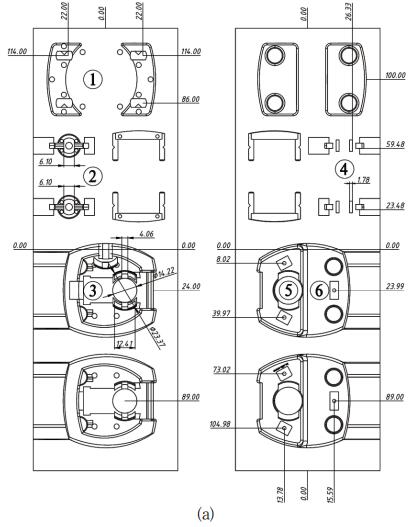
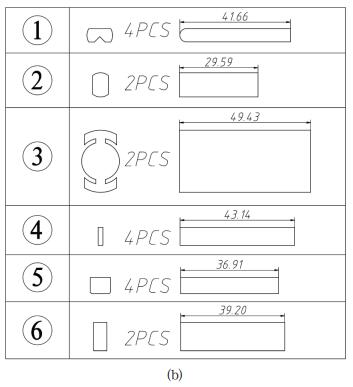
图 6
图 5(b)固定插件前模同样采用如上方法, 用 Φ16R0.8 镶方合金刀粒圆鼻刀粗加工,再用 Φ12R6 镶球头合金刀粒圆鼻刀(球飞刀)进行 精加工完成。(也可使用线切割加工分型面)后 用 Φ4 铣刀对型腔开粗,单边留 0.3 余量。具体 加工参数如表 1 所示。 图 5(c)基座前模,先钻线切割孔,再用 Φ6 铣刀对型腔进行粗加工,单边留 0.3mm 余量。 型腔要做多个电极和线切割镶件切割加工,如图 6 所示。图 6(a)为线切割加工的关键尺寸标注, 所有需要线切割加工的位置先用钻床或铣床钻 孔,以作线切割穿丝孔用。切割孔位数量与镶件 数相同,采用线切割四边分中加工,按所示尺 寸加工型腔与型芯,要求加工完成后的镶件与 型腔、型芯孔的配合为过盈配合,公差范围为 0.01~0.02mm。 图 6(b)为线切割所需镶块数量,①号处 是后模插穿位置镶件,共 4 件 ; ②号是后模插穿 位置镶件,共 2 件 ; ③号处是后模基座插穿位置 镶件,共 2 件 ; ④号处是前模插穿位置镶件,共 4件;⑤号处是前模基座插穿位置镶件,共4件;⑥ 号处是前模基座插穿位置镶件,共 2 件。具体线 切割加工参数如表 2 所示。 线切割加工难点是镶件的表面光洁度要求 高,这样加工时参数的选择就要求合理。在功力 管、脉冲宽度和间隔之间要根据机床当时的情况 而定,适时调整。 图 6(a)型芯上总共分布四件产品,较为 复杂的是塑料扣基座,其包含有滑块和插穿,其 三件则比较简单。
4.2 后模型芯加工
先用普通铣床和磨床加工两块 130*85*35mm 钢料,分别用于图 7(a)和图 7(b),再加工一块 260*85mm 图 7(c)使用。 当然前、后模仁钢料一般是一起加工好的,只是 钢料的厚度不一而已。 图 7(a)后模仁先采用数控铣加工,采用 Φ12 R0.8 镶方合金刀粒圆鼻刀粗加工,再用Φ12R6 镶球头合金刀粒圆鼻刀进行精加工。由 于倒扣出在后模,插穿孔要和前模方柱碰穿,精 度要求较高,加工有一定的难度。其工序为先 用 Φ4 合金刀开粗,单边留 0.3mm 余量,再做 电极用火花机加工后进行人工打磨即可达到加工 要求。由于倒扣胶位出在碰穿位下方,直径小的 刀具无法加工,故要做两个电极加工 : 一个粗铜公单边留 0.2mm 余量,一个精铜公留 0.08mm 余量,分别进行电火花加工。 具体后模加工参数如表 3 所示。 图 7(b)后模型芯中间有两处要插入前模中, 同前模型腔加工基本相同。先用 Φ16R0.8 镶方 合金刀粒圆鼻刀,进给率 1200mm/min,下刀 速 率 500mm/min, 抬 刀 速 率 3000mm/min, 主轴转速 S=2000 转 / 分。用 3D 曲面挖槽刀路 对前模型腔曲面粗加工。采用相对尺寸,最小加 工深度和最大加工深度都设置成 0.2mm。加工 余量 0.3mm。采用螺旋下刀,在前模型腔的中 间下刀,切削方式选择环绕方式。粗加工后再用 Φ12R6 镶球头合金刀粒圆鼻刀进行平行铣削精 加工 ; 最后用 Φ6 平底刀进行塑件胶位的粗加工, 加工余量 0.3mm,完成后需要做电极加工。 图 7(c)后模型芯上有四个塑件产品,最 难加工的部件是塑件基座,首先采用线切割加工 凸出区域,如果整体式加工,CNC 加工的工作 量就很大,模仁材料也要加厚购买,清角比较麻 烦,且尖角过多也不便于加工,如果用多个电极 清角则增加了加工成本和时间,所以考虑采用线 切割方式加工该蓝色区域。用 Φ10 合金刀 3D 曲 面挖槽刀路对前模型腔曲面粗加工,接着用 Φ4 平底刀等高外形清角粗加工,后续用 Φ6R3 合金 球刀进行平行铣削精加工,留余量 0.3 mm 做电极加工。因镶件上有台阶要加工,故电火花加工 完成后,装上镶件再进行台阶加工,且台阶处也 要做电极清角。
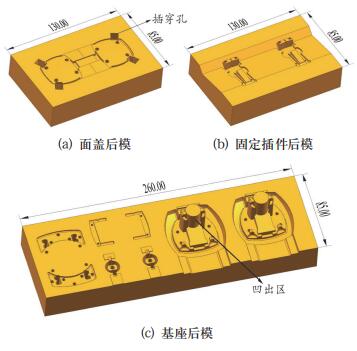
图 7
表 3 后模加工参数
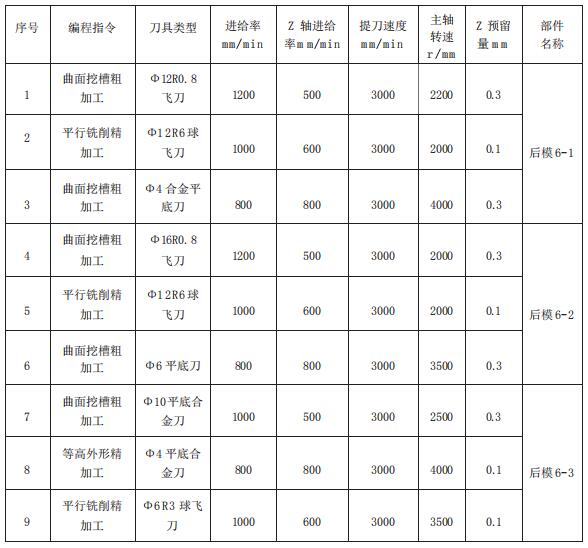
后模型芯加工完成后,经过后期制作便完成 了整套模具的加工。加工完成后的模具成品图如图 8 及图 9 所示。
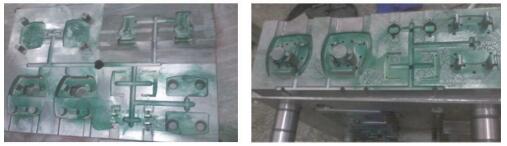
图 8 前模 图 9 后模
5.结束语
这套模具经生产验证,塑件质量达到设计要 求。纵观该模具的设计及制作过程,可见一套模 具的开发首先要对塑件结构进行分析,然后提出 几种可行的成形方案,在确保质量、减少投资的 前提下,根据生产要求选择最优方案 ; 同时也要 对模具零件的加工工艺进行推敲,并对模具后期 维修的便利性提前考虑。
投稿箱:
如果您有机床行业、企业相关新闻稿件发表,或进行资讯合作,欢迎联系本网编辑部, 邮箱:skjcsc@vip.sina.com
如果您有机床行业、企业相关新闻稿件发表,或进行资讯合作,欢迎联系本网编辑部, 邮箱:skjcsc@vip.sina.com
更多相关信息