立式数控机床主轴热态精度检测
2014-1-15 来源:数控机床市场网 作者:马晓波 仇健
摘要: 利用电容式位移传感器和电阻式温度传感器对立式数控机床主轴进行高精度测量,试验获取主轴端径向和轴向热位移,以及主轴系统热敏感位置的温升。对于机械式主轴,主轴前后轴承和减速器因高速滚动摩擦发热,使得主轴的发热量很大,造成的热变形会严重影响机床的加工精度。对于结构稳定、技术成熟的数控机床,提高数控机床的热态精度最有效的措施是改进机床的主轴润滑方式或者对主轴轴承进行强制冷却。
关键词: 主轴温度场;主轴热误差;热稳定时间;热态精度
1 引言
数控机床的精度通常分为几何精度、位置精度和工作精度。几何精度和位置精度可概括为机床的静态精度,静态精度只能在一定的程度上反映机床的加工精度。除此之外,机床的精度还主要有动态精度,是指机床在外载荷、温升及振动等工作状态作用下的精度。而其中对动态精度影响最为严重的是机床生热造成的热态精度。
温升是评定机床主轴的一项重要性能指标,综合反映了主轴的设计、制造水平和材料质量。主轴系统的温升,通常是指在无外加载荷和无外部热源影响的条件下的典型区域温度与环境温度的差值。通常用主轴前轴承的外圈作为测量系统温升的典型区域。系统的温升越高,零配件的热变形越大,引起精度丧失的可能性越大,系统的热态特性就越差。
2 试验条件
使用 API 主轴误差测试分析仪,测量范围 0. 1-0. 8mm,测量频率10s/s,分辨率0. 1μm,可测量的最大主轴转速为 60000r/min。在 5 个自由度(X轴、Y 轴和 Z 轴漂移、X 轴和 Y 轴倾斜)上测量和分析主轴误差的短期和长期变化,并配备 20 个带磁性底座的热传感器以及计算机辅助软件,可以描述主轴的温度及变形状况。温度测量除使用主轴动态误差分析仪自带的温度传感器外,还辅以红外热像仪进行温度场测试。利用红外热成像原理可测量 -40— +120℃范围内的温度变化,近焦距 <0. 3m,精度 ±2Co或读数的 ±2%,采样频率 1Hz。
机床主轴在运转过程中主轴轴承、电机等由于摩擦而生热,尤其是高速主轴,其温升更快、更高。主轴装配体部件在温度升高过程中会出现热变形现象,不对称热变形将导致主轴系统精度降低,具体表现为主轴沿轴向的伸长和主轴沿径向的弯曲变形。研究表明,影响高速机床加工精度的主要因素之一是热误差,在用现代机床加工零件的制造误差中,机床热变形所引起的制造误差可占总误差的 50%,在精密加工中热误差约占机床总误差的 40%—70%。而主轴系统的热变形误差又是引起机床热变形误差的重要因素。因此,主轴系统的热特性分析与设计对机床精度的保证至关重要,是高速高精度机床必须要考虑的关键技术之一。
3 主轴热态精度测试
主轴温升和热变形实验包括空载温升试验和热变形测试试验。空载温升试验用来检验空运转情况下轴承的温度与温升,评定机床主轴系统的温度场分布。主要目的是检验装配质量,实现轴承的充分磨合和润滑。温升试验使主轴在额定电压额定转速和额定功率下连续空载运行,直至主轴和部分温度达到实际热稳定状态。主轴热态误差测试使用API 主轴误差分析仪,型号 SPN-500,主轴转速3000rpm,每 10s 采集一次,总采样点 1797 个。利用FLIR 热成像仪,可以采集到机床主轴系统的温度变化及分布数据,了解及掌握机床在运转过程中主轴系统的实际工况,如热平衡时间、主轴系统不同时刻在各方向的变形量等信息,对主轴系统的优化设计和动态补偿提供了基础数据支撑。
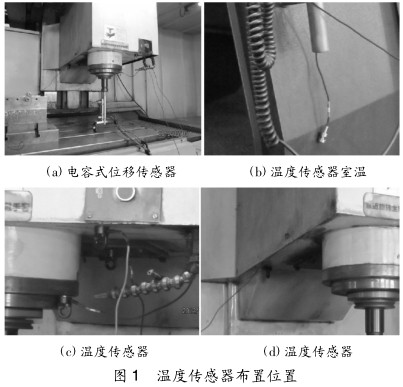
测试在生产车间进行,室温 28 -32℃。机床在冷态下开始试验,为了得到良好的测试数据,试验前机床超过 12h 之内处于空闲状态,可保证机床测试初始条件良好,试验时不准中途停车。该试验机床主轴最高转速范围为 5000 -6000r/min,在安装检棒以后,为了保证机床在高速运行时的绝对安全,在进行主轴箱温升及主轴系统热变形试验时,采用3000r/min 的转速进行温升及热变形试验。主轴热变形测试时间从上午8:30 到中午12:30,共4 个小时。
4 机床主轴热态精度分析
(1)主轴瞬态温度场
使用 FLIR 红外热像仪对测试部位进行测量时,需确定被测物体的发射率、反射温度、测量距离和环境的相对湿度。由于红外热像仪对被测物体表面的反射率等较敏感,因此需在关键点处贴上胶布,降低表面反射率,同时可以使表面反射率具有一致性,提高测试精度。
除利用温度传感器对敏感位置进行温升测试外,辅以红外热像仪对空运转试验进行温度场采集,可有效了解温度分布状况以及主要热源的热平衡状况。瞬态温度场关注系统的温度随时间变化情况,图 3 和图4 分别为测试开始和结束时的主轴温度分布情况,图中十字点为关键点布置位置。表 1 为主轴上关键点位置分布汇总,其中温度测点共计3 个。
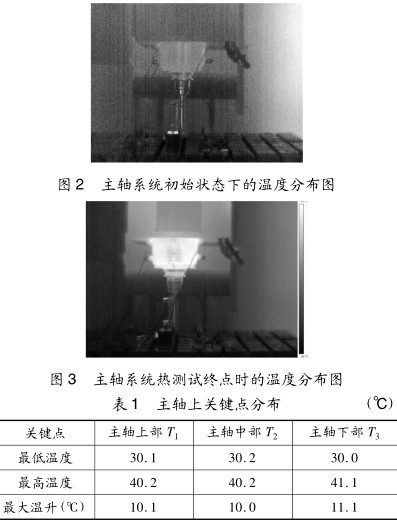
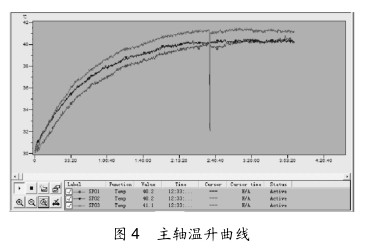
整个试验过程中主轴上主要关键点的温度随时间变化情况见图 5。从图中曲线的走势看,主轴系统在开始的一个小时的时间里温度上升较快,接下来的一个小时里温升较缓和,然后趋于稳定状态。
由温升曲线可知,在主轴以 3000r/min 连续运转 4 个小时期间,主轴轴端的温升较为一致,主轴温升较快,最大温升大概 10℃左右。
图 7 是温度传感器的温度—时间曲线,图中最下部的曲线表示环境温度,由图中温度测点 1—5 温度—时间变化曲线可见,温升趋势明显,并且不同测点具有相同的变化趋势。主轴温升和热变形在经过2 h 10 min 后基本达到热稳定,与中小机床一般 4 h的平均热平衡时间相比,被测机床更快达到热稳定,机床的热态性能优异。另外,与热像仪测试获得的温升曲线比较发现,两种温度测量方式得到的结果一致。
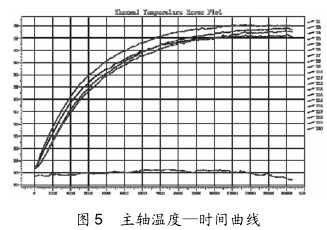
(2)主轴热变形
测试时,机床主轴安装一热敏感较低的检棒,热变形测试时每隔 10s 采集一次数据。主轴热变形试验数据受检棒本身精度及检棒和机床主轴连接后的装配精度影响很大,检棒与主轴连接后,其随主轴旋转的跳动(包括径向跳动和端跳)越小,测试结果的精度越高;反之则会降低测试精度。
主轴热变形测试使用 API 主轴误差测试和分析系统,系统自带温度传感器。在整个测试过程中,主轴在 X 方向的热变形分别为:近主轴端 0. 0036mm,远主轴端 0. 0056mm;在 Y 方向的热变形为:近主轴端 0. 0250mm,远主轴端 0. 0280mm;主轴最大伸长为 0. 0564mm。
图 6 为主轴热变形—时间关系曲线,图 7 为主轴热倾角—时间曲线,表 2 为主轴热变形测试结果汇总。从图 6 不难看出,机床主轴的热变形量很小,并且机床整体热变形在 X 向较小,在 Y 向和 Z 向相对较大,说明此种结构机床在 X 轴向具有相对热对称结构,可以较好地平衡掉加工误差;而 Y 方向和 Z方向是误差的敏感方向,在机床设计中应注意改善结构,优先考虑对称布局,并且可通过加大热敏感方向的通风、冷却来达到抑制目的。此外,也可在热敏感方向布置热源,通过热平衡方法达到变形的抵消。
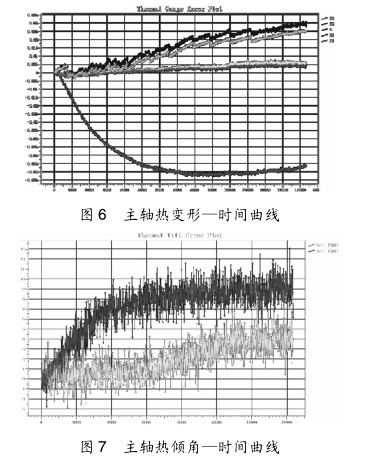
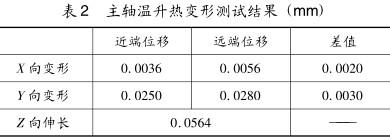
根据试验结果,本机床在主轴以 3000r/min 运转时,近 4 个小时的热变形测试过程中,主轴在 X和 Y 两个方向的热变形并不很明显。在 Z 轴方向热变形较大,且变化率较快,应给予足够的重视。在2 小时左右主轴系统达到热平衡。
综上,由于被测机床的结构稳定,热态结构合理,可保留机床的设计结构,在不增加外部补偿等措施的条件下,通过改善机床主轴的润滑方式或增加主轴轴承等主要发热体的冷却强度,可有效地改善机床的热态性能,从而提高机床的工作精度。
5 结语
(1)通过试验方法获得加工车间立式数控机床的温度场、温升和热变形状况,被测机床超过 2 小时即可达到热平衡,与中小机床一般 4 小时的热平衡时间相比,被测机床更快达到热稳定,并且热变形量极小,机床的热态性能优异。
(2)机床的轴向热伸长较径向热变形更大,提高轴向热态精度是提高该机床工作精度的主要目标。
(3)通过改善机床主轴的润滑方式或增加主轴轴承等主要发热体的冷却强度,可有效改善机床的热态性能,从而提高机床的工作精度。
投稿箱:
如果您有机床行业、企业相关新闻稿件发表,或进行资讯合作,欢迎联系本网编辑部, 邮箱:skjcsc@vip.sina.com
如果您有机床行业、企业相关新闻稿件发表,或进行资讯合作,欢迎联系本网编辑部, 邮箱:skjcsc@vip.sina.com