汽车覆盖件用淬硬钢模具的铣削加工
2023-7-5 来源:哈尔滨理工大学机械动力工程学院 作者:刘献礼
前言
随着我国汽车工业的快速发展,各大汽车制造厂商为了争夺市场,适应购买者对汽车使用性能及造型个性化等方面的需求,不断进行新旧车型的更新换代,改型车和新型车的最主要的标志就是车身外形必须改换,汽车的覆盖件模具要重新设计制造。
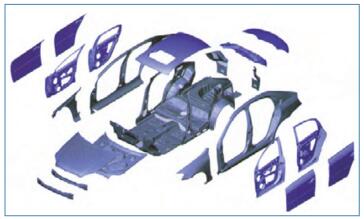
图 1 汽车覆盖件零件分解
图 1 为汽车车身覆盖件拆解,一辆轿车汽车覆盖件数量高达数十件甚至百件以上,每件覆盖件均由其成配套模具冲压成形,这些配套模具的设计和制造时间严重制约汽车换改型的周期。可见,新旧车型的快速升级换代,对汽车覆盖件模
具产生了巨大需求。
为提高汽车大型覆盖件淬硬钢模具的生产效率,铣削加工技术在国内汽车模具制造企业中得到程度不同的应用。对比传统的磨削加工工艺,铣削加工可以获得理想表面质量,同时具有加工柔性好、无污染等特点。国内汽车覆盖件模具加工时,一般在模具切削加工工序之后还要花大量工时进行人工磨抛,其时间一般需要 3 周以上,模具最终尺寸精度和表面质量靠大量的钳工修磨研配来保证,因此,生产效率极低。而且目前中高档轿车的外覆盖件模具,国内汽车模具生产厂家还没有生产能力。因此,开展中高档汽车覆盖件模具的高效、高精度铣削加工技术对提高模具制造水平和促进汽车产业的发展具有重要的支撑作用。
1、汽车覆盖件模具特征和加工难点
汽车大型覆盖件模具是生产汽车车身的大型关键工艺装备,其主要特征如图 2 所示。
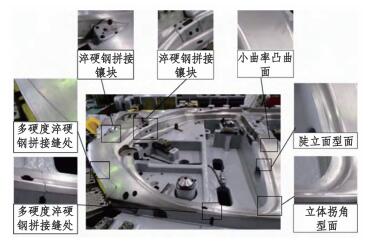
图 2 汽车覆盖件模具的加工特征
(1) 工件材料属于典型高硬度、高强度材料。模具材料多为 7CrSiMnMoV 和 Cr12MoV 等模具钢,淬火后硬度达到 HRC45~65。
(2) 型面特征复杂。存在凹曲面、凸曲面、倾斜面、陡立面、拐角、沟槽等特征型面,且为保证凸凹模的合模精度对模具型面加工精度和表面加工质量要求高。
(3) 轮廓尺寸大。其尺寸范围 (0.5~2.5)m×(1.5~3.5)m,加工型面面积大,切削路径长,数控加工设备各运动轴行程范围大。
(4) 多硬度材料拼接结构。为满足大型冲压模具的加工精确度,提高加工效率,大型模具一般 用多个分块模具拼接而成,或根据模具不同位置所受应力的特征,采用镶块式淬硬钢与模具本体拼接而成。在制作分块模具和淬硬钢镶块时首先单独进行粗加工和半精加工,然后再拼接成整体模具后进行精铣加工。多硬度拼接淬硬钢材料硬度相差高达 ΔHRC5-ΔHRC20。
(5) 加工精度和表面加工质量要求高。为保证覆盖件的光顺性,要求凸凹模具有较高的合模精度,因此凸凹模具各自铣削加工时对加工精度和表面加工质量有很高的要求。若模具上有一处型面轮廓精度达不到要求或存在表面加工缺陷,会导致冲压件出现褶皱、凹陷等缺陷,则整套凸凹模具均不能再使用。
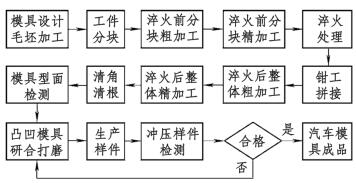
图 3 汽车模具生产企业的一般加工流程
国内汽车模具生产企业的一般加工流程如图3 所示,模具最终表面加工质量和型面精度要靠钳工大量的打磨研合来保证,工件淬火后的加工精度直接影响后期抛光研磨的工作量。目前对于型面特征复杂而表面加工质量和型面位置精度要求不高的汽车内覆盖件模具的加工技术问题已经基本解决了,然而在加工精度要求高的汽车外覆盖件模具制造方面,仍普遍存在着生产效率较低、刀具使用寿命不足、已加工表面质量差等突出问题,导致模具整体合模精度低,覆盖件冲压成品光顺性较差。严重影响汽车模具成形精度、使用寿命和生产效率。
汽车大型覆盖件模具铣削加工中的难点。
(1) 汽车模具铣削条件恶劣,出现型面误差和表面加工缺陷。淬火后高硬度材料铣削时刀具切入困难,与工件之间出现滑擦现象 ; 型面加工特征多变及多硬度拼接特征铣削载荷变化频繁,易引起刀具变形、振动、磨损、破损 ; 材料拼接处由硬度差导致的加工轮廓不一致。这些现象导致型面误差和表面加工缺陷。
(2) 汽车模具铣削过程易产生颤振。汽车模具铣削过程动态铣削力大,且加工工艺系统动态性能了解不清,无法有效的控制颤振,导致加工表面恶化。一些企业为了避免切削颤振发生,通常以牺牲加工效率为代价,选择保守的切削参数,导致数控加工设备性能得不到充分发挥。
(3) 刀具性能不满足铣削要求。为保证模具型面的完整性及覆盖件成形质量,精加工时要求刀具遍历整个汽车模具加工表面,中间过程不能换刀,刀具使用寿命需要达到 4~12 h; 不同硬度工件材料拼接过渡处铣削载荷突变,导致刀具的磨损破损程度加剧,故汽车模具铣削加工对刀具性能提出了更高要求。
(4) 汽车模具复杂型面数控编程及刀具路径规划不合理。对有效加工带宽及加工行距的确定不合理,增加模具抛光、打磨等工序的任务量 ;模具型面变曲率特征、拐角特征等易产生刀具局部干涉 ; 无法有效地根据特定的加工曲面和加工条件进行刀具路径的规划,导致刀具失效过快,且加工效率低下。
综上所述,通过汽车覆盖件模具加工中的难点分析,高效高精度铣削加工汽车覆盖件模具需要在淬硬钢模具铣削过程建模与分析、加工工艺系统动力学特性与铣削稳定性分析、汽车覆盖件淬硬钢模具铣削加工用刀具研制、模具复杂曲面数控编程技术及工艺规划研究等方面进行系统深入的研究,本文针对这几方面的研究现状进行归纳和总结。
2 、淬硬钢模具铣削过程建模与分析
2.1 淬硬钢模具铣削的理论建模
2.1.1 球头刀铣削力建模
汽车覆盖件淬硬钢模具铣削过程中产生较大铣削力,直接影响模具的切削加工性、刀具磨损、刀具变形、机床振动、加工精度及表面完整性等。目前,汽车模具的铣削加工多采用球头铣刀,而球头铣刀铣削力模型应用最普遍的是球头铣刀瞬时刚性力模型。其主要思想是将切削刃离散为切削刃微元,将微元铣削力表达成切削面积和切削刃接触长度的函数。
汽车模具复杂曲面铣削加工中,刀具的铣削状态一般是不断变化的,变铣削状态主要包括刀具进给方向的变化和刀具 - 工件切触区域的变化。而刀具铣削状态变化在铣削力模型中主要通过未变形切屑厚度体现出来,进给方向变化通过对未变形切屑厚度计算模型的影响体现出来,刀具与工件切触区域的变化用以界定未变形切屑厚度计算模型的有效范围。球头刀铣削曲面的铣削力建模需要解决的关键问题有 : 球头刀刃线几何模型、刀具 - 工件接触区域确定、瞬时未变形切屑厚度计算、铣削力系数识别、铣削力在各坐标系间的转换、被加工表面类型。
2.1.2 球头刀铣削表面形貌建模
从理论研究的角度,球头刀铣削表面形貌建模方法主要分为两类。一类是几何实体建模法,建立刀具和工件的 CAD 几何实体并离散,通过布尔操作运算获得工件表面形貌模型。另一类是Z-Map 法,将工件模型在 XOY 坐标内离散成大量分布均匀的 xy 网格节点,并求得每个网格节点对应 z 坐标的法向残余高度值,这些网格节点就组成工件的数字化模型,用以表述已加工表面。
2.2 淬硬钢模具铣削过程的有限元模拟
淬硬钢模具铣削机理的有限元模拟研究中主要关注分析预测铣削力、铣削温度场、切屑形成与流出、刀具磨损、加工变形、表面残余应力和加工过程中微观结构变化等方面,图 4 为汽车模具有限元数值模拟实施方案。
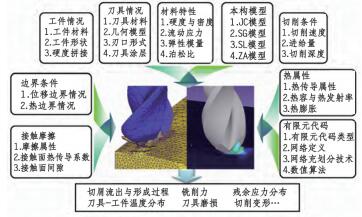
图 4 汽车模具铣削仿真过程
绝大多数的淬硬钢铣削过程有限元数值模拟仿真都是平面或斜面铣削加工,对于凸凹曲面及拐角等特征型面的研究较少,其主要难度体现在凸凹曲面及拐角等型面特征的铣削过程刀具运动轨迹非直线,刀刃与工件的接触区域不断变化,运动轨迹加载难度较大 ; 凸凹曲面及拐角等型面特征的铣削过程的模拟仿真过程计算量大,不易收敛。图 5、图 6 分别为凸曲面铣削过程有限元数值模拟和为拐角铣削过程有限元数值模拟。
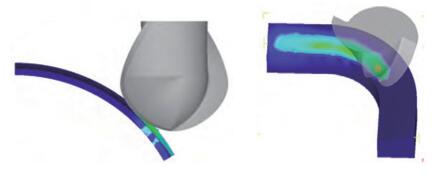
图 5 凸曲面铣削有限元仿真 图 6 拐角铣削有限元仿真
3、 汽车覆盖件模具铣削刀具研制
汽车覆盖件模具铣削加工过程中刀具磨损破损严重,因此刀具应具备高硬度、良好的耐磨耐热性、抗冲击和化学稳定性等性能。汽车模具铣削用刀具主要采用硬质合金、PCBN、陶瓷等材料,一般企业首选铣刀材料应是硬质合金,其特点是硬度高、导热性好且成本较低。为了提高刀具的耐磨性、耐高温性和化学稳定性,涂层硬质合金的使用越来越普遍。涂层的材料,从 TiN、Al2O3、TiC 发展为 TiCN、TiAlN、TiSiN、CrSiN 等。陶瓷刀具耐磨耐热性好、化学稳定性优良,其抗黏结性比硬质合金好,主要失效形式是冲击破损和切削刃磨平。PCBN 的主要特点是硬度高、耐磨性和耐热性好,切削难加工材料时耐磨性约是陶瓷刀具的 25 倍,硬质合金的 50 倍。在汽车覆盖件淬硬钢模具铣削加工中,PCBN 的性能相对较好。
选定刀具材料后,设计和优选出合理的刀具结构是实现高效高精度铣削的重要途径。将有限元铣削过程仿真分析方法结合刀具铣削加工模拟试验,对比分析刀具物理场分布,来设计和优选刀具结构、刀具刃口刃形及刀具几何参数,提高刀具切削的性能。
3.1 刀具结构设计
汽车模具制造厂家的常用刀具如表 1 所示,主要有球头铣刀和环形铣刀。球头铣刀由于具有数控编程和避免局部干涉简单的特点,在复杂曲面铣削中应用最多。但球头铣刀切削刃上不同位置切削速度不等,刀尖点切削速度为零,切削状态恶劣,加剧刀具的磨损,影响表面加工质量,且行间距较小,加工效率较低。近年来学者们逐渐发现非球头铣刀在加工质量和加工效率上的优势,开始注重对非球头铣刀的设计研究,主要是环形铣刀的设计和研制。
表 1 适用于不同加工型面的汽车模具铣刀
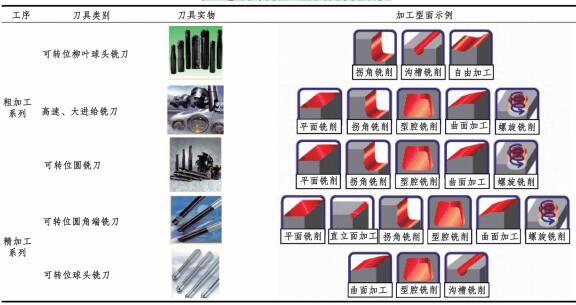
环形铣刀在铣削小曲率大曲面平坦型面时能发挥其优势,在铣削大曲率小曲面和陡立面等型面时易出现欠切和过切,因此环形铣刀铣削复杂曲面适用情况有限。非圆弧刃球型刀 ( 双曲线回转刃形、椭圆回转刃形、抛物线回转刃形等 ) 适用于仿形加工,如图 7 所示,可用于不同曲率的复杂曲面加工。
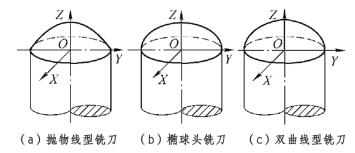
图 7 非圆弧刃球型刀
非圆弧刃球型刀与相同直径的球头铣刀相比,参与切削的切削刃长度更长,切削过程中变形振动减小,可以实现平稳切削,提高了刀具寿命,加工成本降低。与环形铣刀相比,非圆弧刃球型刀的切削刃曲率光滑渐变,可以实现平稳切削。对于非圆弧刃球型刀的研制需要在刃形结构设计,优化刃形参数,建立几何结构模型,准确磨制切削刃,评价切削性能,制定工艺规范,数控加工刀具路径规划技术等方面进一步进行研究。
3.2 铣削刀具磨制
目前还未有汽车覆盖件淬硬钢模具铣削加工用的专用刀具,一般制造企业在汽车模具精加工多采用可转位球头铣刀,这种刀具除了是点接触窄行加工效率低,还易出现崩刃破损,导致刀具使用寿命小、加工效率低。因此,面向多硬度拼接汽车大型覆盖件淬硬钢模具开发高效高精度加工新型专用刀具,是提高汽车模具加工效率和表面质量的一种新途径。合理选择刀具材料并结合优质涂层材料和涂层技术,选用整体式磨制刀具结构和镶片式刀具结构,优选刀具刃线形式,精准设计刀具刃口刃形和前刀面槽型等几何参数,开发用于精加工的环形刀具和非圆弧刃球型刀具,并开发相关磨制工序及工艺优化技术。
4、 模具曲面数控编程技术及工艺规划
汽车覆盖件模具型面和型腔精加工在保证加工质量的前提下,提高加工效率。为保证复杂曲面和型腔的铣削过程稳定、高效,通常通过提高刀具路径的光顺性和保证铣削载荷恒定来实现。
4.1 模具复杂曲面自由曲面刀具路径规划
汽车车身曲线曲面造型是由自由曲线和自由曲面来描述,因此,汽车覆盖件及其内饰件用模具多数为轮廓尺寸大、型面特征复杂的空间自由曲面。自由曲面的数控加工过程中刀具轨迹规划是关键任务,直接影响零件表面加工精度和加工效率。目前针对汽车覆盖件模具的加工设备大多为 3 轴数控加工中心或者 3+2 轴数控加工中心,粗加工和半精加工使用的刀具多为环形铣刀和球头铣刀,精加工使用的刀具多为球头铣刀。
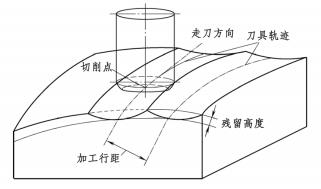
图 8 环形铣刀加工自由曲面示意图
汽车大型覆盖件模具型面中存在着大量的大面积平坦面,如发动机盖模具、天窗模具等,球头铣刀加工这些型面时切削效率低且切削速度不恒定,而将环形铣刀宽行加工技术应用于汽车模具加工中,可提高切削效率和表面加工质量。图8 为环形铣刀宽行加工自由曲面示意图。汽车模具制造企业中已意识到环形铣刀宽行加工的诸多优势,但实际铣削过程应用存在着切削余量掌握不好,已出现过切和欠切,这些问题需要由宽行数控加工切触理论和刀具轨迹规划的研究来解决。
4.2 基于切削载荷的加工工艺规划
这方面的研究主要集中在对自由曲面的球头铣刀三维铣削刀具路径的优化,基本方法是通过控制主轴转速和进给速率来保持切削速度和切削载荷维持在稳定的范畴之内。基于这一原则进行数控加工编程可以减少铣削加工时间,同时延长刀具的使用寿命。在粗加工和半精加工过程中该方法可以避免过大的刀具偏移量导致的加工曲面轮廓偏离理论设计曲面。
恒定切削载荷为目标的加工工艺规划研究主要从两个方面展开。
(1) 基于体积模型的优化研究,假设铣削力与材料的平均 / 瞬时材料去除率成比例关系。多数研究者通过改进材料去除率的算法实现进给量的优化研究。目前多数的商用 CAM 软件的加工参数优化模块多采用这种方法。
(2) 基于铣削力预测模型的进给优化研究,该方法具有更高的精度和可靠性,通过将加工过程中的铣削力限定在某一固定值 / 某一范围内,将固定的进给量值重新优化为一系列进给量,以满足高效加工的要求。
5. 结论
由于汽车覆盖件模具工件材料和结构的特殊性,还需要对以下几个方面进一步研究。
(1) 通过理论建模分析、数值模拟和试验研究,进一步研究自由曲面硬态铣削过程切削层参数变化机制、铣削力、铣削温度、切入切出情况、轮廓精度、表面完整性及刀具使用寿命等基础问题,揭示自由曲面硬态铣削过程的特殊规律和现象 ; 深入研究多硬度拼接过缝处的加工特性,即铣削力阶跃值、铣削温度、刀具磨损破损等随工件材料硬度差、刀具材料和几何参数、切削参数及加工策略的变化规律。
(2) 面向多硬度拼接汽车大型覆盖件淬硬钢模具开发高效高精度加工新型专用刀具,是提高汽车模具加工效率和表面质量的一种新途径。合理选择刀具材料并结合涂层技术,优选刃线形式,精准设计刀具刃口刃形和前刀面槽型等参数,并开发相关磨制工序及工艺优化技术。
(3) 对汽车模具特殊型面和多硬度拼接等特征的铣削精加工刀具路径生成算法深入研究,开发的环形刀、非圆弧刃球型刀具等新型刀具的路径规划算法 ; 在综合考虑机床铣削特征、刀具切削性能及物理因素的基础上制定综合加工工艺。
投稿箱:
如果您有机床行业、企业相关新闻稿件发表,或进行资讯合作,欢迎联系本网编辑部, 邮箱:skjcsc@vip.sina.com
如果您有机床行业、企业相关新闻稿件发表,或进行资讯合作,欢迎联系本网编辑部, 邮箱:skjcsc@vip.sina.com
更多相关信息