随着中国汽车制造业高速发展,对曲轴零部件的需求量也逐年增高,这使得近几年来大量的资金投向了曲轴加工行业。曲轴作为主要承力部件,它承受的载荷很大且受力情况复杂。这就要求曲轴有较高的强度、抗疲劳性和较高的加工精度,才能够保证在复杂载荷作用下长时间的工作。目前,国内曲轴市场的总需求量大概每年在3000万只左右(主要指汽车市场),绝大部分都是采用锻造生产工艺。随着发动机技术的不断提高,对曲轴生产工艺的要求也越来越高,为了满足不断提高的技术要求以及复杂的使用环境,越来越多的新技术、新工艺、新装备正应用于曲轴锻造业。
1 曲轴的分类和模锻工艺特点
和其他锻件产品相比,曲轴锻件一般被认为是较为复杂的锻件类型之一,锻造工艺难度较高,为了保证产品的质量要求,需要通过多种工序才能完成。由于其结构具有类似性,典型的工艺路线为:下料—-加热-辊锻制坯-—压扁-预锻-终锻-切边-扭拧-—热精整-悬挂控温冷却-—正火+调质-—校直-去应力-喷丸-—探伤—-防锈—-检验入库。
根据曲轴锻造工艺的不同可以分为以下几种类型。
(1)水平分模直接成形曲轴(图1)。主要包括:单缸、双缸、四缸、六缸曲轴等。大部分应用于乘用车的直列发动机上,其连杆颈呈180°分布,全部采用非调质钢材料,锻造工艺相对简单。主要采用80000kN及以下的设备锻打,对于更小型的轿车曲轴,常采用带有步进梁结构的自动化线进行大批量生产。通常采用:加热-预锻-终锻-切边的模锻工艺,一般不需要制坯工序,在切边的同时完成热精整。
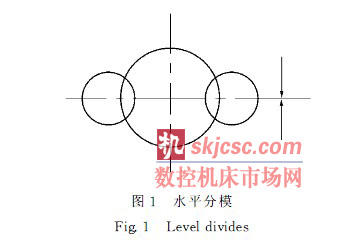
(2)曲面分模直接成形曲轴(图2)。主要包括三缸、六缸等曲轴类型,部分的V8、V10曲轴也采用这种工艺成形,主要应用于200马力以上的重型发动机上,连杆颈一般呈90°,72°和120°分布[1]。这一类型的曲轴需要在250kJ以上的设备上完成。国内目前拥有多条该类型产品的自动线,需要单独的制坯和精整设备。国内部分企业采用非调质钢材料。
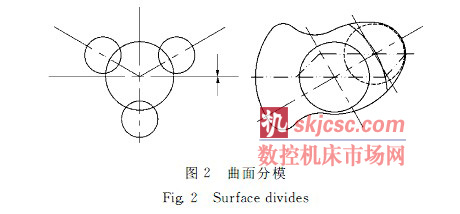
(3)水平分模扭曲成形曲轴。主要是指带有全平衡块结构的六缸12平衡块曲轴、V8、V10曲轴等。这种类型的曲轴如果采用曲面直接成形工艺,会造成锻件局部余量较大、锻造工艺性较差、锻模寿命低等缺陷,一些V8、V10曲轴甚至需要改变平衡块形状,从而导致严重的动平衡问题。因此,采用直接锻造+扭曲成形技术是这一类型产品最理想的生产工艺。该产品的主要工艺难点在于扭曲和精整工艺的合理设计。其中,以六缸曲轴的扭曲成形工艺最为常见(图3),以五缸曲轴的扭曲工艺最为复杂,其扭曲设备的结构也比较复杂,目前国内还没有五缸曲轴扭曲工艺及成形设备,一般要综合采用多台设备来完成。国外一些锻造企业可以在一台设备上完成扭曲和热精整两个工序,在节约设备的同时又提高了生产效率,值得国内同行借鉴[2]。
(4)曲面分模扭曲成形曲轴(图4)。这种类型的曲轴较为少见,一般应用于高速发动机上,到目前还没有看到有国内企业生产。这种产品也称为错拐曲轴,即两个连杆颈之间通过一个平衡块相连,3个曲柄和两个连杆颈组成一个单元,一个曲轴一般有3个单元组成,互呈120°,两个连杆颈之间的夹角为30°,或者是60°。由于特殊的使用环境,其对锻造工艺的精度要求非常高,因此锻造工艺也最为复杂,一般采用普通的分模方式无法锻造成形,通过分析,这种产品可以通过曲面分模和扭曲成形相结合的方式实现。但模具结构非常复杂,尤其是扭曲和热精整模具。通常可在63000kN热模锻压力机上完成锻造和切边,然后在8000kN双工位液压机上来完成扭曲和热精整。
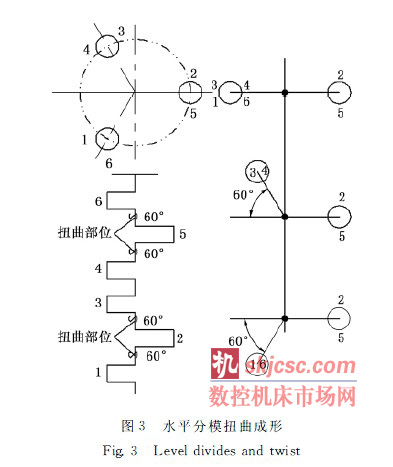
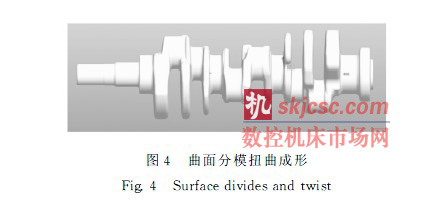
2 新设备在曲轴锻造线中的应用特点
根据曲轴锻件结构以及成形工艺的不同,曲轴生产所需要的设备也不尽相同,大致可分为热模锻压力机生产线、模锻锤生产线以及螺旋压力机生产线等3种类型。其中,电动螺旋压力机曲轴锻造技术是近几年来的一个新的发展方向。
2.1 模锻锤生产线
模锻锤生产线又可分为蒸空气锻锤、程控电液锤以及电液对击锤3种类型。其中,蒸空气锻锤生产线由于效率低下,劳动强度大,污染严重,能源消耗大,生产成本高,锻件公差、余量、出模斜度大,锻件精度低等缺点,已经难以满足现代发动机对曲轴加工方面的需求,因此,采用蒸空气锻锤生产的曲轴将越来越少。随着电液技术以及自动化技术在锻造设备上的广泛应用,也有部分企业采用电液锤设备来生产大型的曲轴。尤其是锻重在250kg以上的大型曲轴,仍然需要在400kJ的程控电液锤或者是40t·m 及以上吨位的电液对击锤设备上生产,据了解国外有不少企业仍然在采用对击锤设备生产大型的曲轴锻件。我国目前在这一类型的锻造设备上仍有投资的空间[3]。
2.2 锻压机生产线
近几年,随着曲轴市场需求的不断扩大,对曲轴锻件质量的要求也日益提高。由于热模锻压力机上模锻曲轴件具有加工余量小、锻件精度高、质量稳定、可以自动化生产、工人劳动强度低、对周围环境污染小等特点,受到越来越多的曲轴锻造企业的青睐。2005~2010年,我国分别从俄罗斯、德国、日本等国家引进十多条大型的曲轴自动化生产线,其中部分采用了韩国、日本的步进梁技术。但是,由于这一类型的设备一次性投资较大,设备结构复杂、维修不便、维修费用高、电气电子元件需要检修调整、要求工人素质高,同时具有设备行程固定、有焖车可能等特点,目前这一类型的设备主要还是集中在大型国有企业中。典型的锻压机生产线的设备组成如图5所示[4-6]。
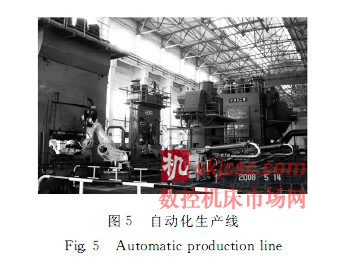
2.3 电动螺旋压力机生产线
近两年,电动螺旋压力机在我国的曲轴锻造行业得到了快速发展,目前国内大都采用德国米勒万家顿公司生产的PZS系列的电动螺旋压力机来生产各种类型的曲轴。与其他设备相比,造价较高,但是由于其行程不固定、不会产生焖车现象、可以实现多次打击、输出能量可控、设备整体结构简单、维修方便、锻件精度较高等优点,非常适合于大型曲轴的锻造。特别是在锻打一些小批量、大变形、大截面、平衡块高深比相对较大的曲轴锻件时优势较为明显。
3 新技术在曲轴锻造生产中的应用
3.1 半闭式模锻工艺技术的应用
目前,国内曲轴市场已经出现产能过剩的迹象,曲轴锻件的市场竞争日益加剧。现阶段,降成本成为许多企业最紧迫的事情。随之而来的越来越多的新技术、新工艺开始应用于曲轴的生产过程中。半闭式模锻工艺是近年来应用较多的一种新的技术。其主要是借鉴了挤压工艺的原理,将曲轴的开式模锻工艺通过适当的改进模具结构转化为闭式锻造的一种新型技术。它介于开式模锻与闭式模锻之间,其关键是通过改变锻模的桥部结构(图6),实现金属在半封闭的模具型腔中挤压成形,从而将锻件开式模锻转化为闭式挤压模锻,实现小飞边锻造,最大程度上提高材料利用率、降低生产成本。
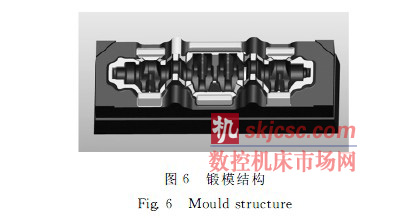
采用半闭式模锻工艺,由于增加了型腔压力,有利于成形复杂锻件,特别是高深比大的锻件成形,对提高锻件充满程度较为明显,也降低了曲轴的焊补率。由于半闭式模锻工艺中存在阻力墙结构,也可以提高锻件水平方向的精度,减小错移误差。国外的锻造企业很早就开始采用这种工艺生产曲轴,虽然我们国家这几年引进了不少先进的锻压设备,但是在工艺研发方面和国外还有很大的差距。许多企业还是停留在重设备、轻技术的层面上。有了好的设备,并不意味着能够生产出好的产品,只有做好技术上的提高,才能成为市场竞争中的优胜者。
3.2 曲轴锻造的自动化生产
3.2.1 自动化生产线
锻造自动化生产线技术通常是指以工业机器人为核心单元,以信息技术和网络技术为媒介,以profibus现场总线控制技术为通信手段,将所有设备连接到一起而形成的大型自动化生产线。能够实现设备单元的自动化、生产工序过程自动化、管理自动化、基于WEB技术的工厂安全过程监控系统自动化以及故障诊断系统自动化等。其核心是设备单元自动化和过程自动化。它是锻造企业先进制造技术应用的典型代表,是发展先进制造技术实现锻造生产线的数字化、网络化和智能化的重要手段[4-5],目前已成为国内外锻造企业极力发展的高新技术应用领域。
自动化生产线的设计要求是生产稳定、设备电控能正常工作、工艺合理、多机配合协调、综合经济效益高,达到优质、高产、低耗的目的。在整个生产线设计过程中,前期工艺分析尤为关键,生产线工艺方案的制定,关系到设备选型、经济效益、生产能力、厂房建设、能源供应、设备平面布置、操作方式等一系列的方案的实施,是项目成功与否的关键所在[4]。因此,锻造生产线的自动化控制技术的应用,既包含机械电子以及自动控制技术,还涉及对制造工艺的熟练程度。目前,我国从事这方面的专业技术人员非常少,也没有专业性的企业从事这方面的研究,这也是和国外差距最明显的地方。
3.2.2 新型设备和工艺的适应性
从自动化设备的发展趋势来看,以热模锻压力机为主的自动线,在生产大批量的曲轴类产品的生产中,优势较为明显。但是,该类型的产品的设备维护较为复杂,因此,国内一些企业转向采用米勒万家顿公司的PZS系列的电动螺旋压力机来锻造曲轴。它可以很好的适应半闭式模锻工艺的技术特点以及工艺要求。在其他如扭曲、切边、校正等一些曲轴锻件的典型生产工序上,随着新型锻压设备的不断发展,原来那种每个工序分别由不同设备来实现的生产方式,现在可以在一台设备上完成多个工序的生产,在节约设备的同时,也相应的缩短了工序之间的传递时间,因此,更能体现出自动化生产的优越性。如国外的有些设备已经可以实现扭曲+校正工序的自动化生产。而切边+校正工序也可以通过复合工艺在单一设备上完成。
随着国内液压机技术的日益完善,同时其又具有良好的经济性、工艺适应性强等优点,正越来越多的被应用于大型的曲轴锻造自动线上,但是曲柄压力机仍然作为主导产品服务于锻造业。现在,也出现了同时带有保压功能的曲柄压力机,在实现切边功能的同时对锻件进行精整校直,这种和工艺结合紧密的新型锻压设备将会得到广泛的应用。
3.3 曲轴的低能耗制造
在原材料应用方面,目前更多的碳钢、合金钢锻件被微合金钢、铝合金及镁合金所代替。国外很多年以前就实现了曲轴材料的100%非调质钢化[7]。我国由于标准等方面的不同,至今仍有相当数量的曲轴采用调质材料生产,既浪费了能源,又增加了生产成本。从上游企业来看,在微合金钢原材料方面的技术研发上,我们仍然需要提高。
国内许多企业在采用非调质材料生产曲轴的同时,也采用控温冷却技术来实现曲轴的余热处理。
这样既可以节省能源,也可以减小设备投资、减少生产工序、降低生产成本、缩短生产周期。在车间厂房建设方面,越来越多的企业建立了隔音的生产厂房,避免了对周围环境的噪声污染;在车间内部,通过增加设备减震装置、添加隔音沟槽等多种措施进行降噪处理;在粉尘治理上采用了新型的回收净化装置用于车间的除尘等,最大限度的降低了对车间人员的身体危害[8]。
3.4 联合创新技术的发展
在产品工艺研发上,国外的企业和科研院所之间的结合非常紧密,许多大型的锻造企业,都有自己的联合技术研究室,专门用于新工艺新技术的研究,真正的形成了产学研结合的模式。虽然我国有众多的研究所和大专院校,但能够和企业成立联合技术研究所的不多,国外的零部件企业已经实现了和整车厂商的产品上的同步开发,很值得国内的企业借鉴。现在的锻造企业要想适应多变的市场需求,和整车厂产品的同步开发是今后企业必须要面对的问题。
3.5 计算机辅助技术的应用
随着制造业全球化的日益加快,在带来更多机遇的同时,也加剧了市场竞争,而客户对产品的质量及生产周期的要求越来越高。因此,传统的生产工艺已经不能满足市场的要求,这就要求企业向着产品设计的数字化、锻造生产的数字化、管理的数字化方向发展。对于曲轴类产品而言,新的制造技术在不断发展变化的同时,计算机辅助技术也开始应用于曲轴产品的工艺开发当中。
首先,由于PRO/E、UG、CATIA 等大型CAD、CAM 软件的广泛应用,锻件图及工装图的设计开发变成了3D的直接建模,传统的车削加工全部被数控技术代替。其次,随着有限元技术的广泛应用, 一些专用软件如DEFORM、Qform、FORGE、VeraCAD等CAE锻造模拟技术开始更多的被锻造企业采用(图7),从而可以使设计人员在计算机中完成产品设计的优化及修订工作。既减少了试模的时间,也缩短了产品的开发周期。同时,一些特殊的制造技术也开始应用于锻造业,如快速成形技术,逆向工程及CAT技术。
4 结语
从传统的观点来看,锻造行业实际上是一个没有自我产品研发的外包产业,其在产业链中所处的位置不断的被上下游企业所侵蚀。因此,要想实现整个行业的长久发展,首先要重点做好技术的研发和创新,在引进国外先进技术的基础上要不断的消化吸收再创新;其次是优化生产工艺,降低成本消耗、缩短产品开发周期、适应快速变化的市场,走专业化的生存之路。只有这样,才能使我们国家的曲轴制造水平在国际市场中有更大的竞争力。
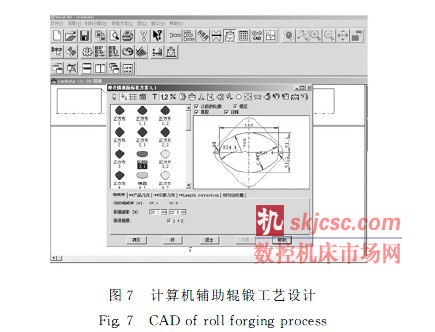
如果您有机床行业、企业相关新闻稿件发表,或进行资讯合作,欢迎联系本网编辑部, 邮箱:skjcsc@vip.sina.com