1 引言
叶轮是一种由复杂曲面构成的机械零件,是对小型燃气轮发动机等动力机械性能影响最大的核心部件。通常小型燃气轮发动机叶轮为整体叶轮,其叶片的形状是机械加工中最难成型的曲面,因此其加工一直是困扰工程技术人员的难题。随着人们对叶轮在流体中受力的研究,叶轮的叶片也从开始的径向直叶片发展为带有后弯和前倾的扭曲叶片。再加上新型叶轮的叶片长而薄,从加工工艺角度来看,为机械加工提出了更具挑战性的难点。为了能够精确地加工出形状复杂的叶轮,现在广泛采用高性能四五轴联动的数控机床来完成叶轮的加工。然而高性能四五轴联动的数控机床一般都是从国外引进,价格昂贵,其加工费用较高。另外整体叶轮的加工一般周期长、效率低,往往造成其加工成本很高。如何提高整体叶轮加工效率,降低制造成本,是叶轮加工行业工程技术人员的研究重点。
钛合金以其优良的机械性能被广泛地作为叶轮的材料,但钛合金在机械加工中属难加工材料。采用钛合金的新型整体叶轮加工,难度都较大,另外,其加工质量的优劣对发动机的性能又有决定性的影响。如何能高效率地研制出质量优良的钛合金整体叶轮是值得研究的问题。
2 加工难点分析
本文所研究的整体叶轮加工精度要求较高,尺寸精度为IT6 级,表面粗糙度为Ra1.6。叶片曲面为自由曲面,其曲率变化大。叶轮流道狭窄,极易发生加工刀具与临近叶片碰撞干涉的问题。叶片较长,超过50mm,叶片厚度较薄,最厚的部位也只有2.8mm,在加工过程中极易引起振动,影响表面加工质量。如图1。
叶轮材料为钛合金TC4,其切削性能较差。同时钛合金的弹性模量小(大约是45#钢的1/2),在加工过程中很小的切削力就会产生较大的变形,容易出现粘刀、让刀、啃刀的现象,使工件的表面质量、几何精度难以保证。钛合金材料的加工往往选用较低的切削参数,其加工效率一般很低。采用钛合金材料的整体叶轮的加工效率较其他材料更低。
叶轮的加工大体分为叶片粗开槽、叶片粗加工和叶片精加工三个步骤完成。叶片粗开槽主要是去除叶片间的大部分材料,叶片精加工则是保证叶片形状和表面质量。由于此叶轮的叶片处于悬臂状态,精加工时叶片刚性不足,很容易发生弹性变形,使叶片精铣时处于十分不稳定的切削状态。
a. 此叶轮叶片为自由曲面,在精加工时必须采用点铣加工。点铣加工刀具切削角度随时变化,造成切削力变化频繁,且方向也不确定。很容易使叶片在刀具的随机激励力下产生剧烈的强迫振动,在叶片上留下严重振纹,影响表面加工质量;
b. 精加工时的叶片刚性不足,使点铣过程中很小的切削力就会造成叶片让刀,影响叶片型面的精度。
合理确定叶片精加工余量,保证叶片刚性,以及选择合适的精加工刀具参数,减小切削力,是解决不稳定切削状态的主要途径。
本文所研究的整体叶轮的加工难点在于铣加工工序,一般铣加工工序占整个加工总工时的80%以上,同时铣加工质量直接影响着叶轮的性能。如何提高铣加工效率和叶片成型质量是本文讨论的重点。
3 多轴数控铣加工工艺要点
整体叶轮铣加工工艺一般为:叶轮粗开槽,去大余量;叶片半精铣,轮毂面粗扫底;叶片精铣,轮毂精扫底。
为了提高叶轮的加工效率和加工质量,结合本文提到叶轮的特点以及我们在叶轮加工方面积累的经验,实际安排铣加工工艺为:叶轮粗开槽;叶片精铣,叶轮轮毂面精扫底。
与前面相比,这种安排去掉了叶片半精铣和轮毂面粗扫底,从理论上节省了1/3 的铣加工工时。本文要加工的叶轮材料利用率只有8.5%,其中叶轮粗开槽是去除材料的主要工序,大约能去除1/3 的材料。由于粗开槽工序去除材料量较大,使材料内部应力释放,造成应力变形,影响叶轮的几何尺寸。实际加工测量表明,叶轮开槽后孔的尺寸大约变化为0.02mm。如何保证严格的尺寸精度,减小应力变形的影响,则必须考虑铣加工工序的合理安排。为了获得严格的尺寸精度,在叶轮的粗精铣之间安排了精车序,以避免叶轮应力释放变形而产生的尺寸变化。实际加工表明,此种安排能够消除叶轮粗开槽造成的应力变形,获得严格的尺寸精度。
叶轮粗开槽考虑的重点是加工效率和成本,一般尽量选用低档的四轴联动数控机床来实现粗开槽。另外在粗开槽时选择合适的精铣切削余量,设法加强叶片刚性,确定合适的切削用量,对精加工的难度和质量有着重要的意义。本文通过改进粗开槽路径及工艺参数,较大地提高了叶轮粗开槽的效率,使粗开槽后叶轮的状态更适合于精加工。在精加工时,选择合适的加工刀具和切削参数,在高转速高进给的情况下,提高了整体钛合金叶轮的加工效率和加工质量。
4 毛坯粗加工刀位规划
粗加工是以快速切除毛坯余量为目的,其考虑的重点是加工效率。尽量使刀具以大进给量,尽可能大的切削深度工作,以便在较短的时间内切除尽可能多的材料。粗加工对表面质量要求不高。开槽时应尽量选择大尺寸刀具,以改善切削性能,提高切削效率。另外由于该叶轮在工艺安排上取消了半精加工,同时考虑到叶轮精加工时不稳定的切削状态,这就对粗开槽后叶轮的状态提出了适合于精加工的严格的要求。
首先,粗加工后叶片的余量不宜太小。由于钛合金弹性模量小,硬度又相对较高,加之叶片刚性较差,因此粗开槽后的留量不能太小。一方面会影响叶片的成型精度和表面质量,甚至尺寸精度;另一方面会缩短刀具寿命。同时也不宜太大,否则较难获得高质量表面粗糙度。根据经验,余量一般在2~4mm 之间。其次,粗开槽后的余量一定要均匀,避免叶片上的余量有突然变化,否则精加工时在余量突变处由于叶片变形不一致,产生过渡痕迹,影响表面质量。再次,叶片表面的余量要尽可能做成塔形,即余量从叶片顶部到叶片根部逐渐增加,来增强叶片的刚性。塔形余量的叶片具有较强的刚性,可以减轻精加工时引起的振动。
根据以上对整体叶轮开槽提出的要求,现对以下几种开槽路径规划进行介绍:
a. 将叶轮卧压在机床上,适合于从轴向看叶片没有重叠且没有扭曲的叶轮,否则会使开槽去除毛坯余量不彻底,不能达到去除流道间余量的目的;
b. 对根据余量偏移后的叶片进行仿型铣削。这种方式留量均匀,但开槽过程中,铣削偏移后的叶片时总有半圈是整个刀具(球头和侧刃)参加切削,使切削进给率不能提高,且影响刀具寿命;
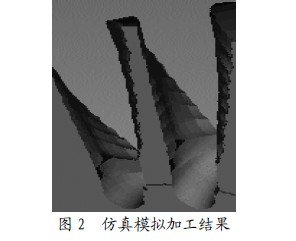
c. 针对以上两种开槽方式的缺点,本文提出根据叶轮流道方向逐层由上而下建立刀路,通过控制每层在流道间的加工面积来实现在叶片上的留量,同时可根据加工面积的不同来实现在叶片上的余量成塔形,从而保证叶片刚性。图2 为仿真模拟加工完成后的情况。
三种粗加工方式比较如表1。

本文采用沿流道逐层开槽的方式。实际加工表明该方式具有效率高,开槽后叶片余量均匀,同时保证叶片具有足够的刚性。另外该方式对刀具刃长要求较短,可避免过长的刀刃参加切削,切削力小。刀具干涉少,排屑情况好,冷却充分。
由于钛合金加工过程中爬坡铣时存在啃刀现象,因此切削进给率不能很高。爬坡铣时的切削条件极不稳定,刀具接近中心处由于线切削速度几乎为零,因此极易发生崩刃。实际加工表明,存在爬坡铣的情况下,向上铣的刀具寿命优于向下铣。向上铣刀具中心不参加切削,刀具不易发生啃刀和崩刃,因此应该采用向上铣。图3 为啃刀情况示意图。

为了避免啃刀和粗开槽全过程频繁抬刀,在建立刀路过程中,使流道的上几层刀路与XY 平面平行,采用等高铣刀具路径。下几层刀路由下而上走刀,采用向上铣刀具路径。通过对刀具路径进行后置处理,最终在低档四轴联动机床上实现了叶轮的粗开槽。图4 为叶轮开槽过程和产品实物。
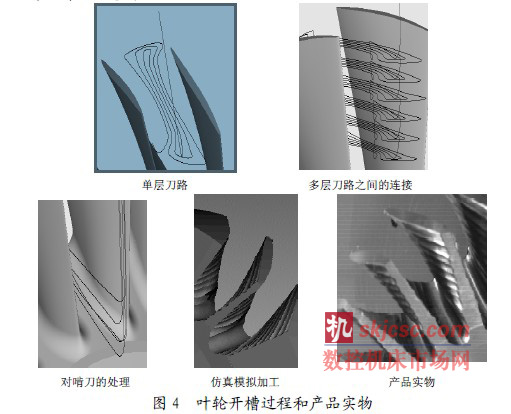
5 叶片精加工和轮毂面精扫底
叶片精加工和轮毂面精扫底是叶轮加工的重点部分,其加工精度和表面质量对叶轮的性能影响很大。采用UG 的可变轴轮廓铣对叶片精加工进行编程,切削方式采用顺铣,每层加工步长0.3mm,表面粗糙度为0.01mm。图5 为叶片精铣刀路轨迹。
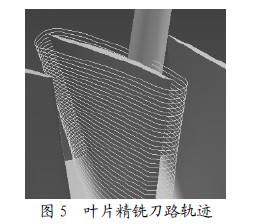
轮毂面精扫底采用ZIG-ZAG双向往复切削方式,使刀路沿流道方向双向往复加工。该切削方式的特点是切削过程中顺铣逆铣交替进行,其加工效率高。图6 为轮毂面精扫底刀路轨迹。
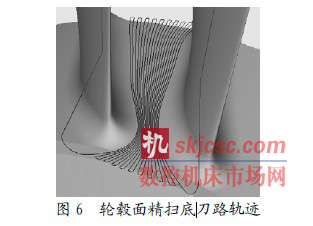
6 叶轮精加工刀具和切削参数的选择
在实际加工中,由于精铣加工存在不稳定的切削状态,因此刀具参数的合理选择和加工参数的匹配,对钛合金叶轮的加工效率、表面质量有重要影响。在精加工时解决不稳定切削状态的一个重要途径是选择合适的精加工刀具。根据钛合金的加工特点和我们在钛合金加工方面的经验,其精加工刀具材料一般选用细晶粒硬质合金YL10.2。钛合金加工刀具后角的选择是最关键的。适当增大后角可以提高刀具的耐用度,但同时会发生崩刃的现象,一般选择8°~10°。前刀面与材料的接触面小,则前刀面的磨损小,应选择较小前角,前角取值应在10°以内。螺旋角对刀具前角有较大的影响,增大螺旋角可以提高刀具实际切削前角,这样可以避免因前角过大而降低刀具强度,又可以减小切削力,提高刀具寿命。根据经验,加工钛合金刀具螺旋角应在30°~40°之间。实际加工表明叶轮精加工刀具的轮廓度对叶片的成型质量有重要影响,若刀具实际廓形与理论廓形相差较大,在精加工时会将刀具廓形误差反映在叶片上,影响叶片型面的成型质量,因此必须对叶轮精加工刀具的廓形进行严格的控制。
对加工质量和效率有重要影响的另一因素是切削参数的匹配和机床的选择。本文采用哈默C40U 五轴数控机床进行叶轮的加工,转速选择10000rin/min,进给率900mm/min。最终高效率地加工出表面质量较好的钛合金整体叶轮。图8 为在哈默C40U 上加工完后的产品实物。
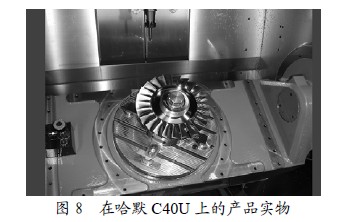
7 结束语
叶轮的加工主要是在昂贵的多轴高性能数控机床上进行的,如何降低成本,提高效率和质量是工程技术人员研究的重点。本文结合某钛合金整体叶轮的加工过程,调整工艺流程,提出一种新的粗加工刀路规划,在五轴高速铣床上高转速、高进给地实现了叶轮的加工。实际加工表明,该方案能高效率、高质量地完成钛合金整体叶轮的加工。
a. 本文重点介绍了粗开槽阶段的刀位规划。分析和比较了三种粗开槽方式的优缺点,提出了沿流道方向逐层由上而下进行开槽的方法。该方法具有开槽效率高,留量均匀,开槽后叶片的刚性好,更适合精加工的优点;
b. 在叶轮精加工时选择合理的刀具参数和切削参数,最终采用哈默C40U 五轴高速加工中心,用高转速、高进给实现了高效率、高质量的加工。
如果您有机床行业、企业相关新闻稿件发表,或进行资讯合作,欢迎联系本网编辑部, 邮箱:skjcsc@vip.sina.com