高速、高精度数控铣床电主轴结构优化及其性能研究
2016-8-25 来源: 机械工程学院 作者:陈丽婷
摘要:主轴系统等窩端装备所需的关键零部件是我国剌造装备技术发展过程中急需解决的瓶颈问题。论文W海天精工VMC系列立式統床主轴为研究对象,进行具体的结构参数设计,并对主轴系统静动态特性及其热态特性开展研究工作,为主轴系统产业化打下基础。论文取得了W下研巧成果:
(1)完成了电主轴结构的初步设计,如设计主轴的整体布局、选择主轴结构参数、选择主轴电机和轴承等。并利用H维实体建模软件SolidWorks完成髙速电主轴建模工作。
(2)利用大型有限元分析软件ANSYSWorkbeiKh对电主轴系统进行结构静力学学分析,得到其静刚度,验证了本论文所设计电主轴满足静刚度要求。
(3)为提高主轴静刚度、减小主轴质量,论文采巧AnsysWorkbench的优化模块AnsysDesignXplorer为优化工具,对电主轴系统前端悬伸量(a)和前后支撑跨距 (L)进行优化设计,得到主轴系统a和L的最优解。
(4)利用有限元分析软件AnsysWorkbench对优化后的电主轴的动态性能进行分析,得到电主轴的低阶固有频率和振型,验证电主轴系统的一阶临界转速是否符合要求;然后对电主轴进行谐响应分析,得到电主轴系统在正弦周期激励下的固有频率,经过分析计算得到电主轴设计转速可有效避开共振区间的结论。
(5)对电主轴内部热源及热生成率进行分析研究,模拟研究优化后的电主轴结构的热态性能,创造性的分析了电主轴恒功率变速范围内不同转速时的热态性能,分别得到了热态分析图。通过分析电主轴的温升情况,有针对性的提出改进措施。
关键词:结构设计,静态特性,动态特性,热态特性,ANSYSworlcbench
高速电主轴结构的设计及H维模型的建立
本研究中的立式统床用电主轴W宁波海天精工集团高速、高精密VMC系列立式锦床电主轴为研巧对象,VMC系列现有VMC850L和VMC1000L两种型号,其最高转速为12000r/min,额定功率为llkw,额定转矩为15N,m。本设计旨在对电主轴最高转速、额定功率和额定转矩都有所突破。设计目标为电主轴最高转速20000r/min;输出功率不低于25KW;扭矩不低于25Nim;静刚度不低于235NAim;锐削方式为端面洗削。
2.1、髙速电主轴的基本结构
高速电主轴的基本结构可分为W下几个部分:主轴壳体、主轴芯轴、内装式电机、高速轴承、冷却润滑系统、拉刀系统等[49]。高速电主轴的结构见图2.1。
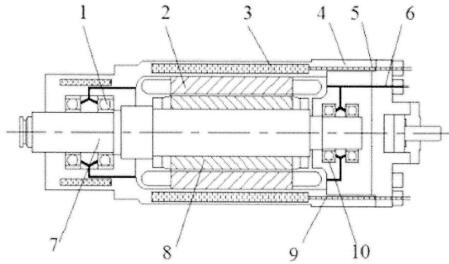
1.前轴承沮2.定子3.冷却液套4.主轴壳体5.出水管6.进气管
7.主轴芯轴8.转子9.进水管1化后轴承组
图2.1高速电主轴的结构图
2.2、高速电主轴的结构设计
2.2.1电主轴总体结构设计
传统机床主轴的驱动形式一般为链传动、带传动或者是齿轮传动,主轴与驱动电机是分开安装的,主轴受力较大,其动静态性能很难得到保证。随着主轴技术的不断发展,实现主轴的高速旋转、高精度、高稳定性的内置电机得到了越来越广泛的应用。根据高速电主轴电机的装配位置可W分为中置式和后置式,具体表述如下:
首先,主轴电机可^式安装在电主轴前后轴承组之间。此种安装方式使得主轴轴架构较为紧凑,主轴整体尺寸相对变短,W至于主轴刚性也会相对较好、承受功率也会相应増大。但是此种结构主轴系统散热相对比较困难〇]。另外一种安装方式就是将电机安装在主轴后轴承姐么后,此种结构电机远离主轴前端,使得主轴前端的径向尺寸能够有效减小,同时电机的散热也更方便。但是,如此安装的缺点就是电主轴的轴向尺寸会比较大,主轴系统冈帳很难得到保证,因此此中安装方式通常用于对刚度要求较低的小型高速数控机床上。本论文所涉及数拉钥床电主轴输出功率、输出转矩要求都比较高,因此需要高刚度大功率才能满足要求,因此其总体结构布局适合选用内置电机安装于轴承组之间的安装方式,内置电机转子与主轴采用过盈配合,通过过盈配合的摩擦输出转矩。由于相对于VMC系列现有型号机床,设计参数有明显变化,现有机床主轴所选用的电机W及轴承显然己不能满足要求,下面首先对主轴电机和轴承组进行重新选择。
2.2.2主轴电机的选择
高速电主轴技术水平直接决定着数控机床的性能,而电机的技术指标则直接决定了电主轴系统的技术水平,因此,如何选择合适的电主轴显得尤为重要。于电主轴系统结构相对紧凑的结构特性,在对电主轴进行选择时要求电机的散热性能好,还要求电机在低速下能够输出大功率,高速条件下又能够恒功率运行。目前,最常使用的交流同步电机和异步电机相比,交流同步电机极限转速更高,冷却功率更大,电机的体积相对更小,维修也更方便。因此本论文中决定选择交流同步电机作为驱动电机。
本论文所设计电主轴前述设计要求,选择最高转速、最大输出功率和最高输出功率都能够达到设计要求的电机。另外,由于国产电主轴功能部件如滚珠丝杠、刀架、电机等发展都相对滞后。因此,本论文选择西口子系列进口电机,具体型号为lFEl(T/2-4WNllBA,电机外形如图2.2所示,电机结构示意图如图2.3,电机的主要技术、尺寸参数分别见表2.1、表2.2。
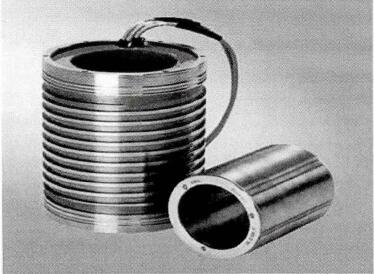
图2.2西口子同步内装式电机1FE1组件
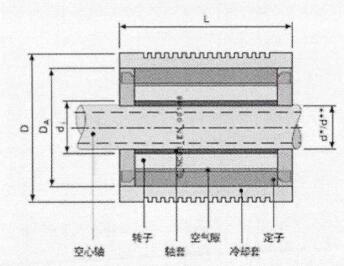
图2.31FE1072-4WN11BA内装电机的结构示意图
表2.11FE1072-4WN11BA内装电机的技术参數

表2.21FE1072-4WN11BA内装电机的尺寸参数

2.2.3主轴轴承的选择
a)轴承类型的选择
轴承是电主轴实现高速、高精度的前提条件,是高速电主轴的关键部件。本文选择高速电主轴轴承时,不仅要考虑到速度的问题,同时还要考虑轴承的刚度和抵抗温度变形的能力口2]。因此,本文要充分考虑到主轴轴承与普通轴承的差异性,选择出最合适的轴承组。在综合分析各种轴承的性能之后,选择洛阳轴承研究所研制的角接触球轴承,具体参数如下表2.3:
表2.3角接触球轴承参数
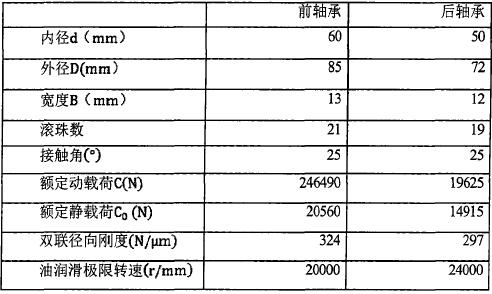
b)轴承的配置方式
主轴系统前后轴承姐是主轴系统的重要支撑部件,因此,主轴系统对轴承的支撑能力和刚度要求都较高。但是角接触球轴承的为点接触式受力方式又使得轴承的刚度较低。因此,为了能够满足系统对支撑能力和支承刚度的要求,我们必须合理选择轴承组配置型式。所谓轴承姐配是指将两个或多个轴承配合W姐为单位使用。由两个W上轴承组成的配置为多联组配,此配置型式能够大幅度提高电主轴的整体刚度,但是考虑到组成多练配姐轴承的的个体差异,每个轴承的误差各不相同,累积误差会随着轴承组配数的增多而变大,反而不利于实现主轴的高速运转。因此,不能为了提高系统刚度而一味增加轴承个数,应该同时考虑高速电主轴系统对高速性能的要求31。本论文最终研巧决定采用两个轴承沮配的双联配置方式。其中轴承双联配置方式又分为背靠背(DB)、面对面(DF)和串联(DT)H种形式,各种双联结构形式图分别如图2.4所示,
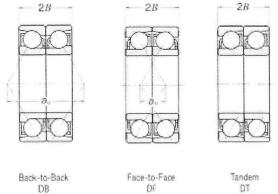
图2.4轴承双联配置形式
分析W上H种配置形式,由于背对背组合的支撑刚度值相对较大。因此,本文最终采用背靠背的组配方式,并在两轴承之间加隔离套,电主轴轴承组在主轴系统内的安装方式为:前端的轴后端的轴承在主轴轴向方向可游动。送样配置不仅可满足电主轴的高速性与整体刚度的要求,而且可^:^部分补偿主轴的热变形。
C)轴承的润滑
由于轴承在高速旋转的电主轴上滚珠与内外圈及保持架之间会产生摩擦力的作用,而轴承摩擦力引起的轴承损坏、发热W及变形是轴承失效的主要因素,因此轴承润滑对保证系统的高速、高精度性能W及提高轴承的寿命有至关重要的作用。轴承滴滑是指:套圈、滚动体和保持架之间的润滑剂能够形成的涧滑油膜,该润滑油膜可W将套圈、滚动体和保持架进行隔离作用,降低轴承各部件之间的磨损与摩擦,确保轴承能够运行良好。
常见的润滑方式主要有脂润滑和油润滑,涧滑方式可由速度参数Dm(其中Dm为轴承中径,n为最高转速值)来确定。通常,当小于1.0X106时,轴承采用脂润滑;当Dm,n大于1.0X106时,轴承采用油润滑4]。此次设计中轴承的Dm,n值为:Dm?II=^?n=?20000=1.4SX1〇6,所W本电主轴的轴承采用油润滑的润滑方式。油润滑分为:油雾润滑、油气润滑和喷油润滑。综合考虑本设计主轴轴承的相关参数レッ及工作运斤状态,再综合分析兰种油润滑方式的利弊条件下决定选择油气润滑方式。
d)轴承的预紧
为了提高主轴系统的旋转精度和增强主轴系统的整体刚度。需要对轴承组进行适当的预紧,这样可W部分消除轴承的径向间隙,还可W对补偿轴向间隙,进而提高电主轴系统的加工精度,延长主轴系统特别是轴承组的寿命。由于工作量的关系,本论文中无法完成对电主轴系统轴承预紧力的计算,根据本设汁轴承需要进行轻度预紧,轻度预紧时选用轴承的预紧力大小为前轴承0N,后轴承90N。
2.2.4主轴单元主要结构参数的确定
根据W上两节选定的轴承和电机尺寸,可初步确定主轴中H段轴段的长度和直径。即电机轴段直径58mm,轴段长暂定200mm;前轴承轴段直径60mm,轴段长30mm;后轴承轴段直径50mm,轴段长28mm。如此便初步确定了电主轴系统巧轴三段主要轴段长度。下面来确定主轴内孔径d、主轴前端恳伸量a和主轴支撑跨跑L。
(1)主轴内孔径d的确定
电主轴内孔主要用于通过拉刀机构等,为减轻主轴重量,在选择主轴内孔直径d时,在满足结构要求及不削弱主轴刚度的前提下,尽量取较大值。结合VMC系列现有主轴拉刀系统直径,最后取d=25mm。
(2)主轴前端悬伸量a的确定
在进行就削加工时,刀尖处受力通过刀柄最先传到主轴系统前端悬伸处,因此前悬伸对主轴的综合刚度有较大影响,因此在进行设计时,必须使主轴的前端悬伸量尽量小。此外,在确定a的具体值时还要考虑主轴系统其他部件的安装尺寸和结构,综合各方面取主轴的悬伸量a=50mm。
(3)主轴支撑跨距L的确定
支撑跨距(L)就是指主轴系统前后两支承轴承姐径向支承力的中也作用点间的距离。支撑跨距是影响主轴系统整体刚度的关键因素,因此在设计主轴系统时,支撑跨距的确定至关重要。理论研究可知,当主轴系统前端拐度最小值时,支撑跨距存在最优值L0即最佳跨距。此时,主轴的静刚度达到最大值。但是在实际设计中,最佳跨距是很难获得的,因此相关专家根据经验制定了最优跨距范围公式iyL0=0.75?1.50。当主轴系统支撑跨距在这个范围内时,主轴的静刚度也即处于一个良好的状态。根据文献[55],最佳跨距与前悬伸量关系式如下:

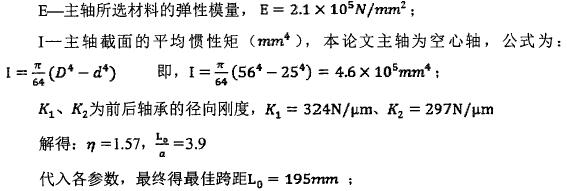
最后,综合主轴的整体结构布局,选取L=282mm?L/Lg=1.4支撑跨跑取值在合理跨距范围之内。
2.3、高速电主轴H维实体模型的建立
2.3.1高速电主轴主要零部件H维模型的建立
主轴苍轴、内置电机、前/后轴承姐、冷却套、主轴壳体、轴承端盖、系统密封件等都是高速电主轴系统的主要零部件。本论文采用大型兰维实体造型软件8〇114\¥〇&8来完成高速电主轴主要结构的^维建模。下面1^芯轴、轴承模型的建模为例,给出在SoMWorks中高速电主轴主要零部件H维模型的具体建立方式。
(1)芯轴模型的建立
根据电主轴巧轴的结构特征,总轴是轴对称的中空阶梯轴。我们可W利用SolMWorks旋转功能模块进行建模。首先,依据设计尺寸进行转轴绘制草图,只绘制芯轴上半部分草图即可,然后WZ轴为旋转中也轴对草图进行%0°旋转建立芯轴H维实体模型,如图2.5所示。当然建模过程也可W采用逐段拉伸,最后拉伸切除内孔的方式来建立。
(2)刖、后轴承模型的建立
本论文中所选用的轴承为角接触球轴承,前后轴承建模方式相同,这里仅W前轴承的H维建模为例进行具体描述。由于轴承是装配体,所首先要建立轴承的各部件即内圈、外圈、保持架和滚动体的模型,然后再利用SolMWorks装配功能模块将它们组装起来。建立轴承各元件的方法为:过旋转、边倒角的方法建立轴承内、外圏模型,并且建立参考平面W便后续装配工作;滚珠模型的获得,的首先通过旋转特征建立单个滚动体,然后再对滚动体进行圆周阵列;保持架的建模过程相对复杂,需要通过拉伸、拉伸切除、圆周阵列等特征才可W实现。
主轴系统前轴承各元件的H维建模完成之后,进入SolidWorks的装配模块,首先导入轴承外圈,并约束其中屯、位置与原点重合,然后导入滚动体模型和保持架模型,将滚动体和保持架通过中必线和参考平面重合等约束方式进行装配,然后将装配在一起的滚珠保持架装入轴承外圈,最后导入装配内圈,并确定拾当的约束类型。至此,前轴承的建模完成,图2.6、2.7为前、后轴承的模型。
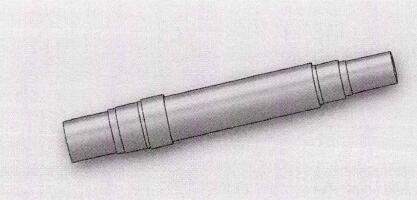
图2.5电主轴转轴模型
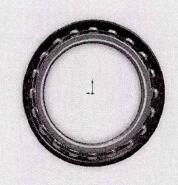
图2.6前轴承
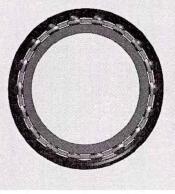
图2.7后轴承
对于电主轴系统的冷却套,电机、轴承端盖等部件的模型的建立,都可W参照芯轴和轴承的建模方法来进行,这里不再详细论述其建模方法。
2.3.2高速电主轴装配体的建立
前面章节已完成高速电主轴全部零部件的建模,然后利用So抽Works装配功能对电主轴进行装配。SoIidWoi-ks软件主要由下到上和由上向下两种装配方式:由下到上的装配方法要求设计者首先完成系统所有零部件的建模,然后通过各部件之间的约束关系进行约束装配。这种方法装配过程比较简单,但前提是必须在建模之前完成所有零部件尺寸的确定。由上向下的装配方式需要知道系统的整体结构关系,然后在此基础上设计附加零部件。
本论文中起初只能确定零部件一一电机W及轴承的尺寸,与轴承组配合的轴承端盖、外壳等一些零部件尚无法确定具体尺寸大小,需要在装配过程中进斤最终的确定工作。综上知,本文比较适合采用首先由下到上装配芯轴、电机和前后轴承组,然后再利用由上向下装配电主轴外壳、前后轴承组轴承座、前后轴承组预紧装置、前后端盖。最终确定电主轴结构的布局和尺寸。高速电主轴H维实体装配最终模型如图2.8所示。
为了清楚地显示主轴系统内部复杂的结构,建模完成W后使用SolidWorks软件中的X截面命令对模型进行1/2剖面命令,得到电主轴系统剖视图如图2.9所示。
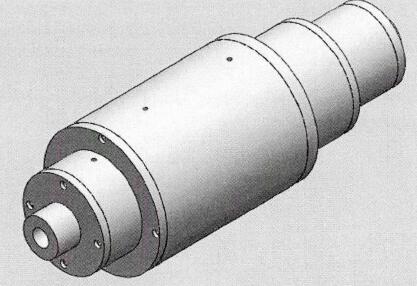
图2.8电主轴的S维模型
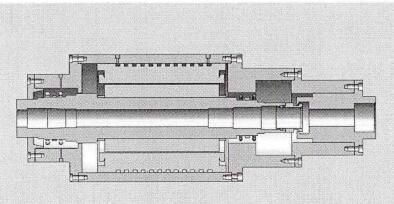
图2.9电主轴的剖视图
2.4、本章小结
本章海天精工集团VMC系列主轴为依托,对电主轴提出新的设计目标,进而对电主轴电机、轴承进行重新选择,然后进行电主轴整体结构布局设计、确定电主轴巧轴主要结构参数,通过计算确定电主轴支撑跨距和前端悬伸量等结构设计参数,完成电主轴的整体结构设计。接下来论文依据H维软件SolidWorks描述了高速电主轴主要零部件和装配体的建模方法和步骤。
投稿箱:
如果您有机床行业、企业相关新闻稿件发表,或进行资讯合作,欢迎联系本网编辑部, 邮箱:skjcsc@vip.sina.com
如果您有机床行业、企业相关新闻稿件发表,或进行资讯合作,欢迎联系本网编辑部, 邮箱:skjcsc@vip.sina.com
更多本专题新闻