超精密车床主轴回转误差测试系统的研究
2016-12-13 来源:哈尔滨工业大学 作者:王世良
摘要
超精密主轴回转误差是影响加工工件表面质量的最主要因素,研究超精密主轴回转误差对于评价主轴回转精度,监测诊断主轴运行故障,预测机床加工工件表面形状误差,加工误差补偿及提高机床加工精度等有重要意义。本文将以超精密车床为研究对象,对主轴的回转误差进行研究。 主轴回转误差包含主轴径向运动误差,倾角运动误差和轴向运动误差。在试验中,主轴回转误差测量数据中混有被测件的形状误差,不可忽略。所以,提取主轴回转误差的核心问题是误差分离。
本文以三点法频域误差分离技术为基础,研究主轴的径向运动误差和倾角运动误差的分离。建立传感器测量值的实际模型,从其解析构成角度证明最小二乘偏心运动对主轴径向误差运动的不可分离性。给出实际测量环境下传感器安装角位置偏差和测量坐标系位置对误差分离精度的定量分析,为超精密车床主轴回转误差纳米级测量采集数据的可靠性提供理论保证。从超精密车床加工工件表面成形角度分析去除一阶谐波分量的依据。在频域中连续对信号进行除噪、滤波、提取同步运动误差和三点法误差分离。建立主轴倾角运动误差分离算法,从双截面测量数据中分离出倾角运动误差。 确定针对超精密车床主轴径向运动误差和倾角运动误差的测量试验方案,搭建超精密车床主轴回转误差测试系统。进行三点法误差分离,获取主轴的径向运动误差。在径向误差分离的基础上,依据本文建立的倾角运动误差分离算法,进行倾角误差测量试验,获取主轴倾角运动误差。研究了超精密车床不同转速下,其径向运动误差和倾角运动误差的变化情况。利用最小二乘圆评价主轴回转精度和从机床加工角度分析主轴回转误差对加工工件表面成形的影响。设计超精密车床主轴回转误差测试系统上位机软件,统筹管理数据采集,数据处理,误差分离及评价。
本文的研究成果主要是建立一套完整的超精密车床主轴回转误差测试系统,包括测试系统的硬件部分和软件部分。定量分析测试系统硬件部分的可靠性,保证测量数据的可信度。建立主轴倾角运动误差的分离算法和实际测量试验方案,可利用倾角误差运动计算各截面的径向运动误差。
关键词:超精密车床;主轴回转误差;径向运动误差;倾角运动误差;误差分离
第 1 章
绪论
1.1 课题来源及研究的背景和意义
课题来源:深圳市重点实验室提升项目“用于光学自由曲面和微结构加工的具有慢刀和快刀伺服功能的超精密车床及其加工工艺开发”。
超精密加工技术是指在机械加工领域中,某一个历史时期所能达到的最高加工精度的各种精密加工方法的总称。
对于超精密车床加工,无论是进行对称回转体工件的加工还是利用快刀加工非对称回转体,回转运动是其基本的运动形式,回转运动误差将反应在加工工件的表面轮廓中。因为超精密车床的加工切削量非常小所以加工工件表面形状误差的最主要来源就是主轴的回转运动误差。超精密车床主轴回转误差将会影响加工工件的圆度误差、圆柱度误差和端面平整度误差等,研究超精密车床主轴回转误差是很多学者关注的问题。
研究机床主轴回转误差的意义在于主轴回转误差可以用来评价主轴的动态性能和工作精度;可以预测加工工件的表面形状误差甚至是粗糙度;机床加工的运动补偿,提高工件的加工精度;判断主轴的运行状态是否良好,及时发现主轴的运动故障等。对于超精密车床,其加工工件表面形状误差的最主要来源就是主轴的回转运动误差,因此研究其主轴的回转运动误差对超精
密车床的加工有着非常重要的作用。
1.2 国内外在该方向的研究现状及分析
1.2.1 国外研究现状
三点法是一种广泛应用的误差分离技术,最早是由日本学者青木保雄和大圆成夫在 1966 年首次提出[3],该方法成为多点法误差分离技术的一个经典的误差分离方法,国内外许多学者对此进行过研究和补充,使三点法误差分离技术的应用得到了很大的提高和推广。1972 年 Donaldson 和 Estler 首次提出反向法误差分离技术,对主轴回转误差和被测工件的形状误差进行分离[4]。反向法后来也发展成为一种广泛应用的误差分离技术。
九十年代,Shoji N,Tadao T 和 Atsushi S 提出了矢量表示方法,用垂直于轴线的平面上的矢量来表示和计算主轴的径向回转误差运动[5]。实验中用两个相互垂直的传感器进行测量,开发一种新算法来获取主轴轴线位移的瞬时矢量。Wei G,Satoshi K 和 Tadatoshi N 首次提出混合法测量圆度误差,即用两个线位移传感器和一个角位移传感器同时进行测量[6]。相比三点法,混合法能够将圆度误差和主轴的回转误差进行完全分离,也能很好地测出表面形貌里的高频成分。Jay F. Tu,Bernd B 和 Spring C. C. Hung 为传统的三点法误差分离技术提供了精确的几何模型和误差分析[7]。文中指出三点法基本方程中做了哪些近似处理。同时指出为了减少误差,轴的精度应该比轴线的运动精度好至少十倍,传感器探针的安装误差应该小于主轴运动误差和心轴尺寸的五十分之一。Wei G,Satoshi K 和 Takamitu S 基于混合法提出新的误差分离方法——正交混合法,只用一个线位移传感器和一个角位移传感器,相互成 90°布置[8]。正交混合法是对混合法的改进,其传感器布置更为简单,测量效果在文章中也得到了印证。
近十几年来,Robert G,Eric M 和 Ryan V 对 Donaldson 和 Estler 对反向法进行了改进,通过设计转台减少位移传感器的移动和调整;通过鲁棒性移除由热漂移和空气轴承供应压力引起的低频成分;三维角度显示主轴的径向和轴向的同步运动误差[9]。此方法计算结果的重复性误差低于 1 nm。Eric M,Jeremiah C 和 Ryan V 研究了反向法、多步法、多点法三种常用的误差分离技术,通过实验验证了三种方法都能完成纳米级误差分离,其数值误差都优于1 nm[10]。文章还讨论了纳米误差分离应该注意的问题。Wei G、Makoto T 和Takeshi 对车床主轴的误差测量和补偿进行了研究,通过补偿加工获得了很好的工件表面平整度[11]。Eric R. M,David A. A 和 Donald L. M 对反向法和多点法误差分离技术实际测量试验的比较,文中重点研究这两种误差分离算法对纳米级误差分离的可行性,试验验证了它们对主轴回转误差和工件表面形状误差亚纳米级的分离是可靠性和可重复性[12]。Lu X,Jamalian A 和 Graetz R对当前的测量标准中,测量信号的基波分量由安装偏心引起,径向回转误差的基波被视为不存在的问题提出质疑,文章验证了径向回转误差基波分量存在并提出了心的径向回转误差的 2D 测量方法,同时还讨论了现有主轴运动分析的局限性[13]。Jung Chul L,Wei G 和 Yuki S 介绍了一种主轴误差运动测量系统来评估一个大型精密轧辊车床的主轴,利用反转法分离形状误差和主轴运动误差,通过对不同截面数据的测量,计算主轴的径向运动误差和倾角运动误差[14]。美国雄狮精密公司研发了一套五自由度主轴回转误差分析仪,采用 5 个电容位移传感器,对双标准球杆进行测量。每个标准球布置两个互为 90°的传感器,轴端的标准球轴向位置布置一个传感器,完成主轴径向运动误差,倾角运动误差和轴向运动误差的测量[15]。Anandan K P,Tulsian A S和 Donmez A 等用激光多普勒测振仪对超高速微型主轴的径向和倾角运动误差进行测量[16。Huang P,Lee W B 和 Chan C Y 研究了空气静压轴承主轴误差运动对加工精度的影响[17]。另外文献[18]和[19]对传统的误差分离进行改进,也取得很好的效果。
1.2.2 国内研究现状
九十年代,叶京生、顾启泰、章燕申研究了多步法误差分离技术的原理性误差和测量精度。从理论和实验分析得出多步法能够完整地分离主轴回转误差和被测件的圆度误差,有效地提高圆度仪的测量精度[20]。王晓慧、李占魁对了主轴回转误差的实时测量以及工件圆度和圆柱度误差的补偿进行了研究[21]。洪迈生、邓宗煌提出一种新的分离圆度误差和回转误差的方法——时域二点法,对布置在测试件周向的接近 180°的两个传感器的测量数据进行时域上的分离[22]。何钦象,张华容,杨静基于复数频域分析,建立主轴回转运动数学模型。指出轴的回转中心是轴上回转的+1 阶分量为零的点,转轴的误差运动不含+1 阶分量[23]。阚光萍介绍了双向转位法测量主轴的径向回转误差[24]。实质为反向法的应用,此文对安装偏心的大小从测量仪器读数误差的角度对分离精度的影响有一定的讨论。
近十几年来,陈海斌,程雪梅提出正弦回归法分离标准球的安装偏心,利用反向法进行误差分离,指出主轴回转精度评定方法[25]。谭久彬,赵维谦,杨文国分析多步法误差分离技术的原理误差,提出鉴相法误差分离技术,扩展了无谐波抑制范围,并简化测量过程和测量系统[26]。黄长征,李圣怡提出用两点法误差分离技术分离超精密车主轴回转误差和圆度误差的方法,建立相应的数学模型[27]。此文建立的测试系统只是从主轴敏感方向测量,应用受到一定局限,主要用来评价主轴的工作精度和预测车床在理想加工条件下所能达到的最小形状误差。苏恒,洪迈生,魏元雷等采用机床本身加工的工作为被测试件,利用三点法频域误差分离技术对主轴的回转误差和被测试件的形状误差进行分离,实现主轴径向运动误差的在线误差测量。采用自适应阈值的小波包算法除掉加工时存在的噪声。从谐波抑制特性和总体频域特性两个方面分析测量系统的频域特征[28]。黄长征,李圣怡介绍两点法误差分离技术。此测试系统对二、四阶谐波分量没有原理性误差,对三次谐波有原理性误差。试验中其主轴回转误差中的以二阶谐波分量为主,忽略了三次谐波的原理性误差[29]。苏恒,李自军,魏员雷用频域三点法确定被测件形状误差来解决时域三点法误差分离的初值设置问题[30]。陈清、梁兵对主轴径向回转误差测试系统的误差进行了分析,讨论了安装倾斜或偏心对测量结果的影响、测量仪器的线性偏移等误差对测量结果的影响,指出主轴偏心运动与安装偏心的耦合性31]。洪迈生、邓宗煌、陈健强等提出在时域内进行三点法误差分离,相对于频域三点法,此方法避免了正反两次傅里叶变换,分离速度更加快速。此法是在频域三点法的基础上建立的,在实验前同样还要用频域三点法中的权函数来检验三个传感器安装位置对谐波的抑制问题。其时域的分离是一个迭代的过程,迭代初值的确定是时域分析的一个掣肘问题,不精确的迭代初值是其原理性误差的根源[32]。洪迈生,魏元雷,李济顺为多种误差分离技术建立统一的矩阵方程,文章对圆度三点法、圆度转位法、直线乱序式四点法、直线精密三点法、圆度混合三点法、圆柱体五点法、平面混合四点法、摆线齿轮三点法用一个统一的矩阵方程表示[33]。黄长征对两点转位误差分离法的系统误差、安装偏心对分离精度的影响、传感器安装对测量结果的影响、传感器误差对测量结果的影响进行了分析[34]。梁淑卿、孙宝玉、韩连英等提出一种分离主轴回转误差运动中一阶谐波分量和偏心运动分离的方法,能仅消除偏心运动,得到主轴回转误差运动[35]。此方法的正确性有待考证。洪迈生,蔡萍分析了多步法在频域和时域中的解,讨论了多步法的本质,指出多步法分离系统实质上是一个并联系统,并分析其谐波损失问题。介绍了一种并联多步法误差分离方法,具有步数和谐波损失较少的优点[36]。彭万欢,赵午云,陶继忠[37]等对超精密空气静压主轴回转误差的偏心进行了研究,分析其作用原理及影响。设计了偏心调整装置,使安装偏心控制在 1 μm以内。
采用两点法误差分离技术,对比圆度仪测量结果,验证了测量原理。指出消除偏心只能采用消一次谐波分量的方法,不能用最小二乘法。徐秀玲,姜军,王红亮从消除安装偏心为出发点,通过光学测量系统对主轴的误差运动进行测量,通过此文建立的模型分离出测试件的安装偏心,并通过实验对测量结果加以验证[38]。李九川分析主轴径向运动误差、轴向运动误差、倾角运动误差在不同的应用场合,如车床、镗床等对加工精度的影响以及提高加工精度的措施[39]。刘启伟分析回转误差产生的原因、主轴回转误差对加工精度的影响、机床主轴回转精度测量方法及回转误差的评定[40]。孙郅佶、安晨辉、杨旭等[41]采用双精密球杆和五通道电容测微仪,组成主轴回转误差测量系统。实验中忽略双精密球杆的形状误差,对主轴五个自由度的误差运动进行在线测量并分离。顾妍[42],文章从主轴的刚度、热变形、轴承间隙和轴承轴承误差、主轴配合件、主轴转速等方面分析它们对主轴回转误差运动的影响。指出在实际生产中针对具体的应用,找出影响主轴回转运动误差的主要因素,采取相应措施,以减少主轴的运动误差。
1.2.3 国内外文献综述的简析
主轴回转误差测量的关键在于测量方案和主轴回转误差与被测试件圆度误差的分离,也即误差分离技术。目前主要的误差分离技术有反向法、多步法和多点法,这三类方法在合适的条件下都能够达到纳米级精度。反向法和多步法在主轴回转误差有很好的重复性时,能够有效地分离主轴回转误差和圆度误差。多点法更适合在机测量,因为它不要求主轴回转误差的重复性。基于多点法可以在机测量的特点,我们可以在机床运转甚至是工况时测量主轴回转误差。在多点法中应用最为广泛的是三点法,如图 1-1。三点法应用三个线位移传感器对主轴进行测量,可以对主轴的 2-D 回转误差(径向回转误差)与圆度误差进行分离。但是三点法存在原理上的缺陷:三点法存在谐波抑制问题使得圆度误差的高频成分不能被很好地测得,进而不能彻底地将主轴的回转误差与圆度误差分离开来。尽管三点法在原理上存在缺陷,但是可以通过采取相应的措施来减少谐波抑制带来的影响,达到测量精度的要求。有学者指出通过四点测量 2-D 回转误差可以解决谐波抑制问题,但有学者指出多点法都存在谐波抑制问题(论文观点矛盾)。要测量主轴五个自由度上的回转误差需要布置更多的传感器,如图 1-2,对更多的点进行测量。前人对主轴径向误差测量研究很多,对倾角误差和轴向误差的研究相对较少。
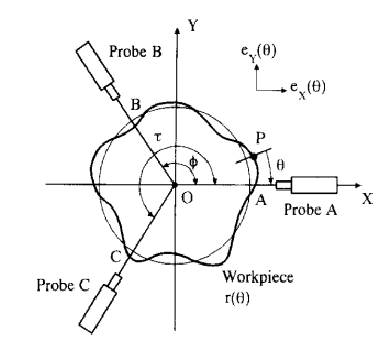
图 1-1 传统三点法测量主轴径向回转误差
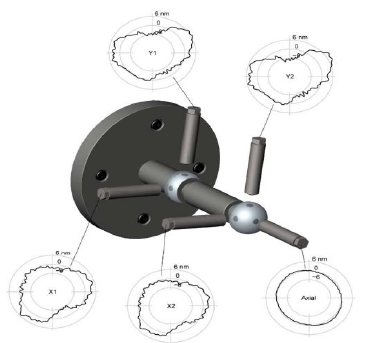
图 1-2 双球试件五自由度测量主轴回转误差
1.3 主要研究内容
主要从解决实验室现有的超精密车床主轴回转误差测试方法存在的问题出发,进行突破和创新。组建由超精密车床主轴、测试标准棒、高精度电容测微仪和计算机构成的主轴回转误差测量系统。测试标准棒是通过机床本身加工的,在无拆卸状态下随主轴旋转。通过电容测微仪的测头对测试件的表面形貌进行测量,采集数据。借助 Matlab 对采样数据进行除噪和误差分离处理,最终得到主轴的回转误差。主轴的回转误差包括:径向运动误差、倾角运动误差和轴向运动误差。课题的最终目的在于能精确的得到主轴的回转误差,以便将来对主轴回转精度进行评价和对工件加工进行补偿控制。
主要研究内容包括以下几个方面:
(1)参考国内外的相关文献,分析现有的测量方案及误差分离算法的优点与局限,并结合实际加工需要,设计测量方案并进行论证;
(2)研究实际测量环境下各种测量误差对误差分离精度的影响,为超精密车床主轴纳米级运动误差测量系统的搭建提供理论保证;
(3)建立传感器测量值的实际模型,从此模型中分析最小二乘偏心运动对主轴径向运动误差和倾角运动误差的不可分离性,从加工工件成形角度分析去掉一阶谐波分量的依据;
(4)建立主轴倾角运动误差分离算法;
(5)搭建超精密车床主轴回转误差测试系统软硬件平台,确定针对主轴的径向运动误差和倾角运动误差的测量试验方案,并进行实际测量试验及主轴回转误差运动评定。
第 2 章
主轴回转误差分析及测试系统设计
本章主要介绍主轴回转误差组成及测量方法,确定以三点法误差分离技术为基础进行超精密车床主轴回转误差的分离。分析测量系统的测量误差来源及其对误差分离结果的影响,设计超精密车床主轴回转误差测试系统。
2.1 主轴回转误差测量原理
2.1.1 主轴回转误差及测量方法
主轴回转误差是由主轴的误差运动引起的,理想的主轴只有自身转动一个自由度的运动,实际上主轴除自身转动外,还有其他五个自由度上的误差运动。如图 2-1 所示,主轴除绕 z 轴的转动外,其回转轴线沿 x,y 方向上的运动为径向误差运动,绕 x,y 轴的转动为倾角误差运动,沿 z 轴的运动为轴向误差运动,这些误差运动总称为主轴的回转误差运动。
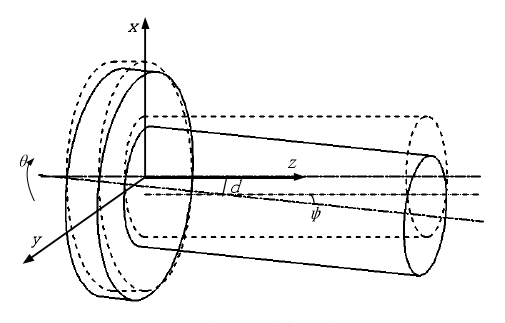
图 2-1 主轴的回转误差运动
以上描述是从主轴运动角度描述,通常所说的主轴的回转误差即是这些误差运动相对于理想的纯自身转动产生的误差,包含径向运动误差、倾角运动误差和轴向运动误差[43]。
对主轴径向运动误差的测量,其难点是主轴的被测截面不是理想圆,而是具有形状误差,测量时被测截面的形状误差回混入测量信号中,如图 2-2所示。同样其他形式的回转误差的测量同样有这些问题。对于高精度的回转轴,特别是超精密机床主轴,被测件的形状误差相对于主轴的回转误差是不可以忽略的。所以,对主轴回转误差的测量的核心问题是误差回转误差和形状误差的分离,即误差分离。
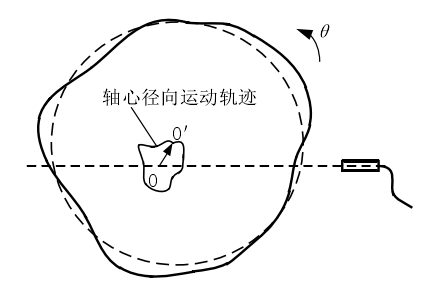
图 2-2 形状误差混入测量信号示意图
近几十年内国内外提出了很多误差分离技术,有反向法、多步法、多点法、数理统计和图像法等,其中应用最为广泛的是利用传感器进行测量[44]。对于本课题对超精密车床主轴误差的测量,要求高精度,在线实时测量等,综合分析以上各种误差分离技术,确定以多点法为基础进行测量系统的设计。三点法是多点法误差分离中最常用的方法,满足上述要求。
2.1.2 三点法误差分离原理
三点法误差分离技术[28]的测量方法是利用三个线位移传感器,以一定的角度间隔布置于回转轴某一截面周向位置,对轴的回转运动进行测量,如图2-3 所示。理想情况下,测量数据会包含主轴的回转运动误差和被测截面的形状误差,三点法误差分离技术即是对上述两种误差进行有效地分离。
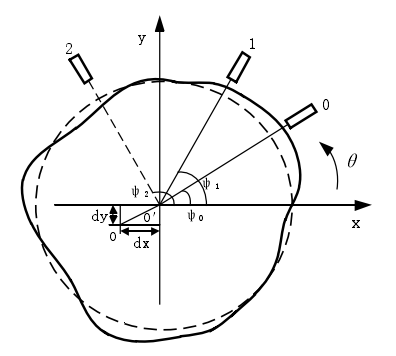
图 2-3 线位移三点法测量原理
三点法的基本方程,即三个传感器的输出分别为

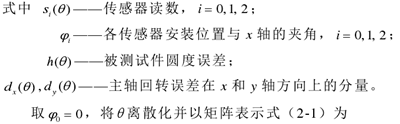
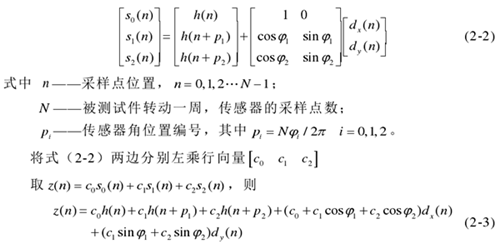
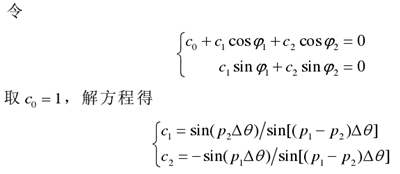
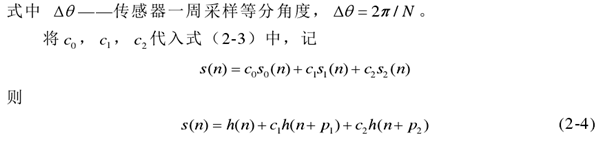
至此,可通过式(2-6),(2-7)从传感器的离散读数中分离出圆度误差和径向运动误差。
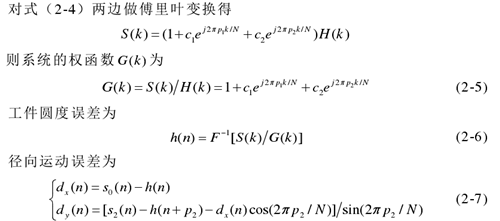
2.2 测量误差来源及影响
2.2.1 传感器读数误差影响
本节讨论布置于被测试件截面周向的传感器,其读数的是否具有独立性,分析其测量值误差。在回转轴 x,y 轴方向上布置传感器 1 和传感器 2,回转轴半径为 R,如图 2-4 所示。主轴沿 x 轴方向运动误差记为xd ,主轴沿 y 轴方向运动误差记为yd ,传感器 1 和 2 的测量值分别记为y1 和y2。
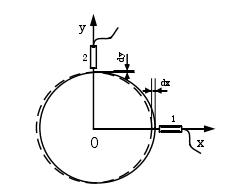
图 2-4 传感器读数误差示意图
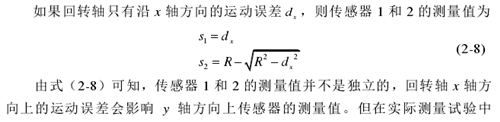
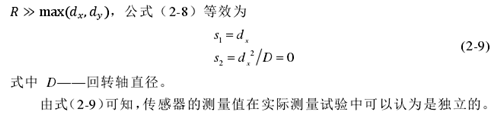
2.2.2 安装偏心对误差分离的影响
为探讨安装偏心对传感器测量值的影响,假设回转是理想轴,即回转轴无运动误差,做定轴转动。图 2-5 中圆代表安装工件某一理想圆截面,由于安装偏心使得测试工件圆心 O 与回转轴心 O?有偏差 。回转轴在做回转运动时,圆心 O 做偏心运动。
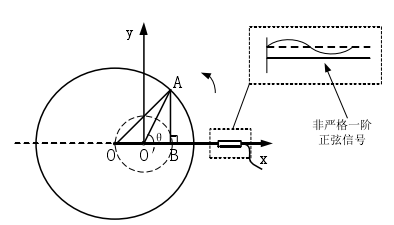
图 2-5 偏心运动时传感器测量

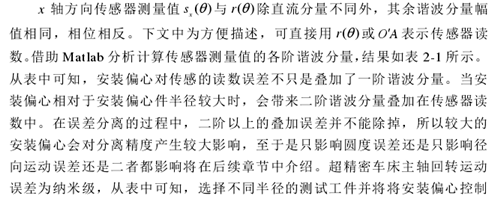
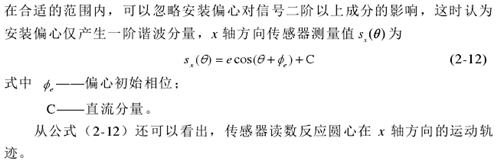
表 2-1 偏心运动产生各阶谐波分量情况表
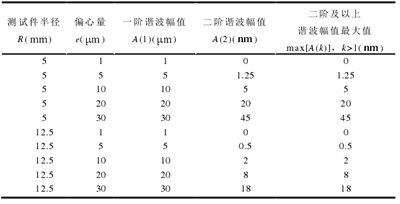
2.2.3 传感器安装角偏差对误差分离的影响
在实际测量过程中,传感器测量值不但包含圆度误差,回转误差,最小二乘偏心运动量,还包含由传感器安装角偏差引起的误差量,初始安装间隙,噪声等。传感器实际测量环境中测量值见下式。
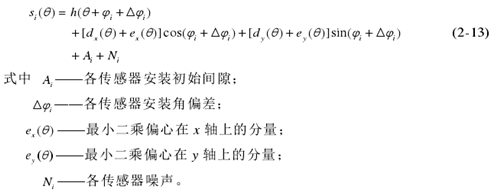
实际测量试验时,传感器夹具有一定加工误差,导致传感器的安装出现角位置偏差。对于纳米级精密测量,传感器角位置偏差对传感器测量值和误差分离效果影响有多大,重点关注角位置偏差对回转误差的影响,本节给出定量分析。
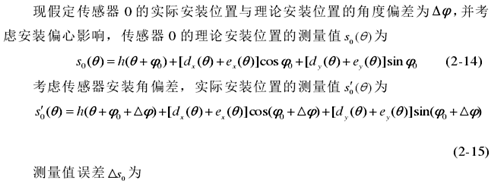
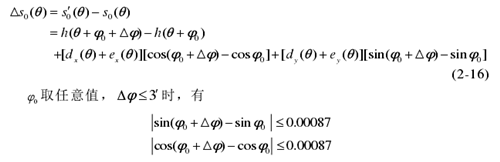
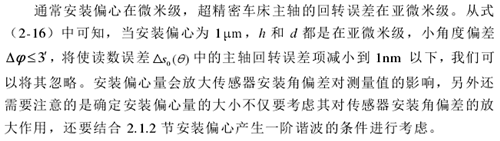
2.2.4 传感器安装线偏差对误差分离的影响
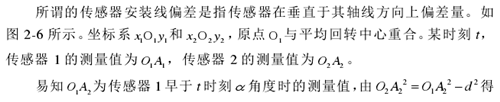

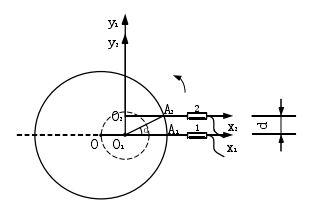
图 2-6 测量坐标系偏差影响

2.3 回转误差运动对工件表面成形的影响
基于本课题所用的超精密车床,其主轴的轴向运动误差相对于径向运动误差可以忽略,由超精密车床固定刀具加工的对称回转体的截面形状误差主要由径向运动误差引起。本节从运动学方面讨论主轴径向运动误差对固定刀具方向加工工件截面成形的影响。此截面的形状误差将作为超精密车床主轴回转精度的一个评价标准。
所谓的单向固定敏感指的是对于有回转误差运动的回转轴,固定刀具在某一方向上对加工工件的影响[13]。车床在加工对称回转体时,刀具固定不动,主轴做回转误差运动。刀具固定在某一方向,其对回转轴不同径向方向的运动误差的敏感程度是不一样的。或者说刀具固定在不同的径向方向时,主轴的回转运动误差对加工表面形貌的影响是不同的。
建立固连在机床上的坐标系 xOy ,称为固定坐标系,固连在加工工件上

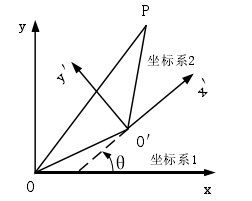
图 2-7 固定敏感坐标系关联

公式(2-18)可反应固定刀具在主轴有径向回转误差运动时对被加工工件的表面成形。下面将通过一个例子进行说明:

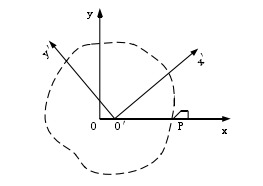
图 2-8 主轴在 x 轴方向做简谐运动工件的表面成形
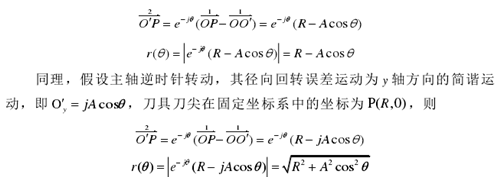
为能直观地看出固定刀具安装方向对加工工件表面形貌的影响,我们夸大主轴径向运动误差,令 R ?100,A ?50,计算机仿真工件表面形貌如图 2-9。
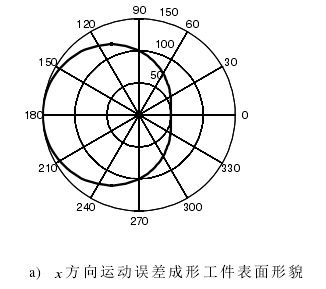
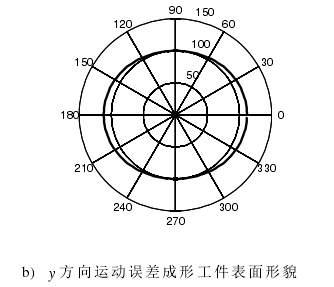
图 2-9 主轴径向误差运动工件表面成形
可见,从成形后的工件表面形貌来看,固定刀具方向对主轴不同径向的运动误差的敏感程度是不一样的。上图 b)也可以看作是刀具安装在固定坐标系(0,R)处,主轴有 x 轴方向的简谐运动时成工件的表面形貌。从这个角度来讲,那就是对于同一个有误差运动的主轴,刀具安装方向的不同对工件表面成形的影响是不一样的。所以,对于主轴回转误差的评价要根据主轴在加工中的具体应用来评价。
图 2-10 为主轴有径向回转误差运动时,快刀加工工件端面示意图。对于此类型加工,虽然运动形式更加复杂,但是还是归到固定敏感类。
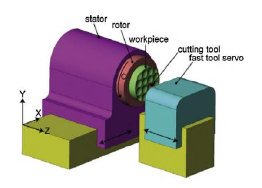
图 2-10 主轴径向误差运动时快刀加工工件端面表面成形
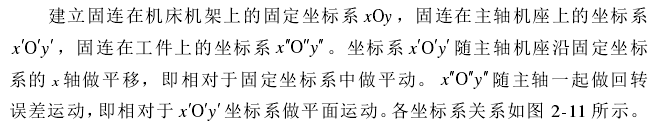
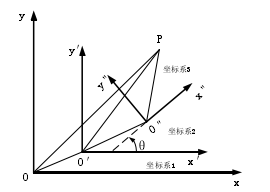
图 2-11 快刀加工工件端面各坐标关联
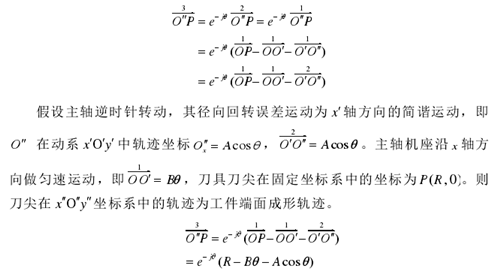

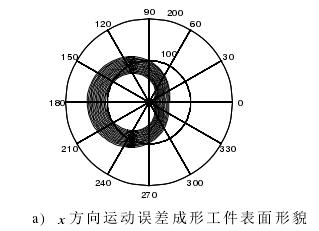
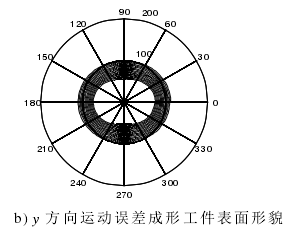
图 2-12 主轴回转误差对轴向端面成形的影响
由上图可以看出用快刀伺服在端面加工微表面结构时,主轴径向回转误差对工件端面成形轨迹的影响,越接近工件中心影响越大。
2.4 测试系统设计
2.4.1 硬件系统设计
超精密车床主轴回转误差测试系统主要由测试工件、位移传感器、数据采集卡、计算机以及误差分离上位机组成,系统组成示意图如 2-13 所示。
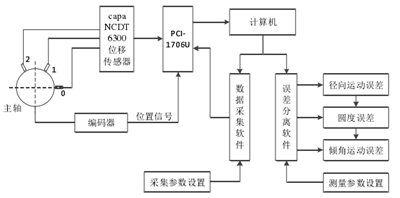
图 2-13 超精密车床主轴回转误差测试系统图
对于超精密车床主轴回转误差的测量,位移传感器的选用有以下条件:
(1)超精密车床主轴回转误差量级是在纳米级,所以要求高精度、高分辨率的位移传感器;
(2)测试系统要保证主轴的正常旋转状态下进行测量,所以要求位移传感器必须是无接触式。
因此本试验测量系统采用德国米铱公司 capa NCDT6300 单通道高精度电容式位移传感器,如图 2-15。此位移传感器为无接触式测量,测量分辨率可以 达 到 0.5 nm , 能 够 满 足 超 精 密 车 床 主 轴 回 转 误 差 运 动 的 测 量 。capa NCDT6300 传感器的主要性能指标如表 2-3 所示。
表 2-3 capa NCDT6300 单通道高精度电容式位移传感器性能指标

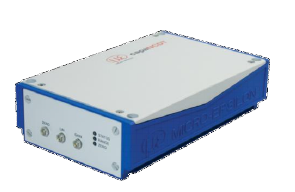
图 2-15 capa NCDT6300 电容式位移传感器

capa NCDT6300 电容式位移传感器含有一个直径 6 mm,长为 25 mm 的圆柱体测头,试验时要针对现有的超精密车床本身结构的空间状态设计传感器测头夹持平台,如图 2-16。图中的夹持平台主要包含两个部分:一是双截面多点位测头夹持件,用于夹持传感器测头进行测量任务;二是调节台,负责水平和垂直两个方向上的调节,使测头夹持件尽可能与被测试件保持较好的同心。
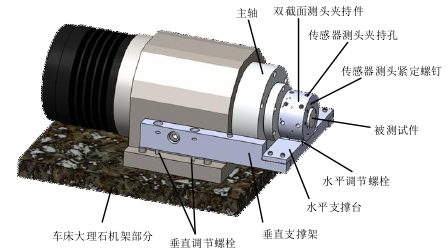
图 2-16 传感器夹持平台
设计双截面测头夹持工件时测头夹持孔要严格安装位移传感器手册中的标准设计孔的大小,并保证加工精度。孔过大时将会使传感器测头安装产生角偏差,降低误差分离精度。两截面对应点位的孔要保持较高的平行度,垂直孔轴线要与夹持件低端平面有较高的垂直度。
安装调整的目的是保证测头夹持件与被测试件的高度同心。具体的做法分为粗调和精调两步:粗调借用水平仪保证安装的初始精度,精调是在同一截面上安装上水平和垂直方向上的传感器,通过调整水平和垂直调整螺栓寻找垂直和水平方向传感器读数的最小值。
2.4.2 软件系统设计
为方便进行主轴径向运动误差和倾角运动误差的计算,设计一套针对超精密车床主轴回转精度的测试系统软件。该软件统筹管理数据采集,数据预处理(除噪,提取同步运动误差等),误差分离(径向运动误差分离和倾角运动误差分离),主轴运动误差评价及结果显示。用户通过简单的初始变量设置,就可以方便的进行主轴误差运动的分析。图 2-17 为超精密车床主轴运动误差分离评价的程序设计流程图。
设计超精密车床主轴回转精度的测试系统软件,其分析界面如图 2-18。软件主要包含初始变量设置区,控制区,运算结果显示区。初始变量设置区主要是传感器分布点位设置,传感器编号与数据采集卡通道号连接设置,主轴转速,采集卡采样频率,分析主轴数据转数,滤波阶次,径向运动误差分解方向等。控制区主要控制图形以时域还是频域形式显示,是在软件内画出还是以 Matlab 原始图形输出。运算结果显示区主要显示分离中间结果和最终分离结果的图形区域和主轴误差运动评价结果显示区域。
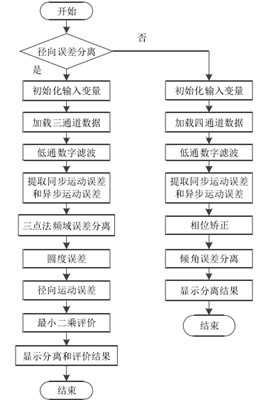
图 2-17 径向运动误差和倾角运动误差软件设计流程图
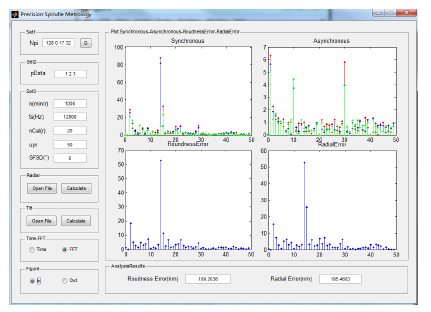
图 2-18 超精密车床主轴回转精度的测试系统软件界面
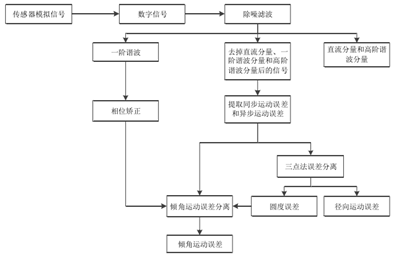
图 2-19 超精密车床主轴回转误差分离数据处理流程
2.5 本章小结
本章分析了主轴回转误差分离的基本测量方法,确定以三点法误差分离技术为基础进行超精密车床主轴回转误差的分离。分析测量系统的测量误差来源及其对误差分离结果的影响。通过测量误差分析指导超精密车床主轴回转误差测试硬件系统的搭建,为超精密车床主轴纳米级回转误差实际测量数据的可靠性提供理论依据,设计了主轴回转误差测试系统硬件和软件系统。
投稿箱:
如果您有机床行业、企业相关新闻稿件发表,或进行资讯合作,欢迎联系本网编辑部, 邮箱:skjcsc@vip.sina.com
如果您有机床行业、企业相关新闻稿件发表,或进行资讯合作,欢迎联系本网编辑部, 邮箱:skjcsc@vip.sina.com
更多本专题新闻