加工中心主轴箱体制造工艺可靠性保障方法的研究(上)
2017-6-30 来源:吉林大学 作者:谭壮
摘要 :产品的可靠性是由设计、制造、装配、管理等多个因素决定的。目前以加工中心为代表的数控机床可靠性研究主要集中在可靠性设计、可靠性建模、可 靠性试验以及故障分析等方面,尚未涉及到数控机床零部件制造工艺可靠性的研究。主轴箱体是加工中心关键零部件之一,研究加工中心主轴箱体制造工艺可靠性保障方法,不仅有利于减少加工中心主轴箱体制造工艺故障的发生,而且能够保障加工中心整机的可靠性水平,并为研究其它类型数控机床零部件的制造工艺可靠性保障方法提供参考。 本文以加工中心主轴箱体制造工艺可靠性保障方法为研究内容,给出了加工中心主轴箱体制造工艺可靠性定义及其评价指标,应用工艺 FMECA 方法针对可能发生的工艺故障制定改进措施,应用控制图分析方法发现制造过程中的异常因素并将其排除,从而预防工艺故障的发生,建立关键工序质量控制点预防制造过程异常因素的发生。本文主要研究内容如下:
1.分析了加工中心主轴箱体的结构及其在加工中心整机中的作用,说明了不同型号加工中心主轴箱体在制造工艺上的相似性。给出了加工中心主轴箱体制造工艺可靠性的定义以及用于评价加工中心主轴箱体制造工艺可靠性的指标体系,并详细描述了各个评价指标的含义与计算方法。
2. 应用工艺 FMECA 方法对加工中心主轴箱体制造过程进行分析,为了解决数据不足的问题,本文将风险优先数定为评判原则对以故障原因为单位的工艺故障模式应用梯形模糊数评判方法,得出各工艺故障模式的风险程度排序,并将排序较高的工序确定为薄弱工序,对加工中心主轴箱体整个制造工艺系统进行综合评判,确定出系统风险等级,为是否有必要实施改进措施提供依据。
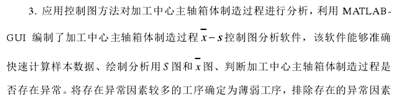
从而预防工艺故障的发生,再将异常样本数据排除从而生成控制用控制图,用于监测加工中心主轴箱体后续制造过程的波动情况。
4. 对加工中心主轴箱体制造过程中的薄弱工序或某些特殊关键工序建立关键工序质量控制点,提出了加工中心主轴箱体制造过程一般关键工序和特殊关键工序的定义以及确定关键工序需要采用的方法,分析了与加工中心主轴箱体制造过程密切相关的 5M1E 因素,并针对各个因素制定了相应的控制文件,描述了建立及管理关键工序质量控制点的方法与流程。
本文从多个角度逐层加深的对加工中心主轴箱体制造工艺可靠性保障方法进行了研究,因而能够适应机床制造企业的生产需求,具有较强的应用价值。
关键词: 加工中心主轴箱体,制造工艺可靠性,工艺 FMECA,模糊评判,控制图分析,MATLAB-GUI,关键工序质量控制点
第 1 章 绪论
1.1 研究背景
机械制造业作为国民经济的重要基础产业,为航空航天、航海、电力运输、高速铁路、汽车生产等多个行业提供了仪器仪表和生产设备等工具[1]。机械制造业是“中国制造 2025”兴国战略中的关键领域,其发展状况直接决定中国能否从制造大国转变为制造强国。机械制造装备的先进程度是机械制造业发展水平的决定性因素,数控机床作为制造装备中的典型代表,在过去的几十年中得到了很大的展,我国也连续多年位居世界机床产量的榜首,为国民经济建设做出了重大的贡献[2-3]。 即便近年来国内经济增速放缓,我国机床产值仍然高于世界上其他国家,同时机床消费值占世界机床总消费值的比例很大,远远超过其它发达国家。如图 1.1、图 1.2 所示,2014 年中国机床产值只是稍稍领先日本与德国,但是消费值以及进口值则与其余四个国家的总和相当,其中机床消费值占世界总消费值的 31%,虽然机床出口值增幅高达 18.1%,但是出口总量相比日本、德国等发达国家差距依然很大[4-6]。我国机床进口值连续多年占机床消费值的 40%左右,并且国内中高端数控机床市场长期由国外进口机床所霸占,这也说明我国机床产业当前依然处于大而不强的境地[7]。
加工中心是一种具有使用范围广、技术先进以及发展速度快等特点的数控机床,其总产值占世界机床产值的 1/6 左右并将逐年高速增长[8]。虽然以加工中心为代表的数控机床在国家科技攻关计划以及国家科技重大专项等政策的支持下得到了发展,尤其是在多轴联动化、高精度化、高速化、柔性化等方面取得了很大的进步,但是与日本、德国等发达国家的数控机床产品相比依然存在差距[9-10]。尤其是在机床可靠性及功能、性能维持能力方面,国产数控机床相比国际知名品牌机床产品落后明显,这也成为了制约国产数控机床技术发展以及占有更多市场的关键因素[11]。因此为了提高包括加工中心在内的国产数控机床可靠性,缩短与国际机床产品的性能差距,应当从设计、制造、装配、使用以及维护保养等方面进行研究,从而提高国产数控机床市场占有率,实现制造强国的目标[12]。
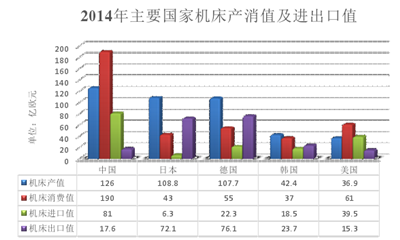
图 1.1 2014 年主要国家机床消值及进出口值
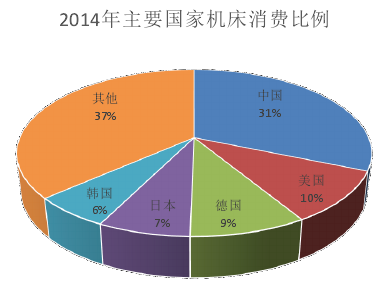
图 1.2 2014 年主要国家机床消费比例
1.2 课题来源
本文所研究的课题来源于“高档数控机床与基础制造装备”国家科技重大专项课题“千台国产加工中心可靠性提升工程”(2013ZX04011-012)和“重型机床可靠性试验与评价方法研究(2014ZX04014-011)。
1.3 论文研究目的和意义
加工中心在国内多个制造领域需求量很大,但由于国产加工中心可靠性低,企业通常只在不重要的中低端制造环节使用国产加工中心,而关键制造环节通常采用进口产品。然而很多发达国家在我国进口高档加工中心时附加了各种限制条件,如限定购买数量、限定使用维修地点和人员等等,这些条件不仅增加了企业的采购成本也影响了企业的生产节拍。目前我国民用、军用行业对国外高档数控机床产品的依赖度很高,严重制约了我国在国际上拥有更多的话语权,因此提升包括加工中心在内的国产数控机床的可靠性迫在眉睫。 加工中心由主轴箱体、主轴、床身、刀库、工作台、立柱等零部件和液压系统、气动系统、数控系统等组成,各零部件的设计、制造、装配水平将直接影响到加工中心整机的可靠性。目前国内外对加工中心可靠性的研究主要集中在产品的设计、试验、维修等阶段,但制造是实现产品设计的过程,也是直接影响到产品质量的重要环节,所以研究零部件制造工艺可靠性保障方法对于保障加工中心整机可靠性具有重要的意义。鉴于主轴箱体是承载主轴的关键件,其制造水平将直接影响到加工中心的可靠性、精度及精度维持能力,在加工中心零部件中具有一定的特殊地位,因此研究加工中心主轴箱体制造工艺可靠性保障方法,不仅有利于减少加工中心主轴箱体制造工艺故障的发生,降低企业在制造过程中的经济损失,保障加工中心整机可靠性水平,而且能够为研究其它类型数控机床零部件的制造工艺可靠性保障技术提供参考。
1.4 国内外发展及研究现状
1.4.1 加工中心国内外发展现状
1.4.1.1 加工中心国外发展现状
上个世纪四十年代初至五十年代末,在成功研制出数控铣床并将其应用到生产实际的基础上,美国研发出了世界上第一台加工中心[13-14]。德国、日本等国家也在这个时间段相继研制出了自己的第一台数控机床,也成为了他们后续垄断高档数控机床领域的基础。上个世纪七十年代,加工中心在国外多个行业得到了广泛应用并受到了越来越多的重视,其技术也得到了广泛的普及。得益于近些年电子、计算机、造型设计等技术的快速发展,加工中心在制造精度、切削速度、人机交互、外观造型等方面取得了很大的进步。目前以德国、日本、美国等发达国家的高档产品为代表,加工中心已经演变成了具有观赏性外观同时又涉及机械、电子、液压等多方面技术的高度自动化机电液产品(如图 1.3 所示德国 DMG 机床集团生产的加工中心)。
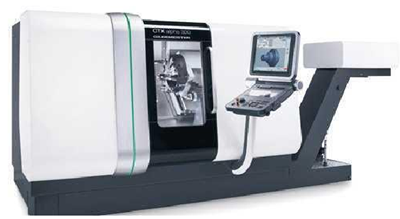
图 1.3 德国 DMG 机床集团生产的加工中心
1.4.1.2 加工中心国内发展现状
我国研究数控机床技术的时间较早,在上个世纪五十年代末开始研发数控铣床,并于六十年代初成功研制出属于自己的第一台加工中心[15]。然而国内研发水平低下、制造能力不足以及国外的技术封锁等原因,造成了包括加工中心在内的国产数控机床在 1979 年之前近乎没有得到任何大的发展。从国家的“六五”规划开始,通过引进和吸收国外发达国家先进机床技术,国产数控机床技术取得了一定的进步并开始受到重视。经过国家改革开放政策后,制造业得到了飞速的发展同时促进了国产数控机床技术取得了更大的进步,并在国内各行各业中应用的更加广泛。虽然目前国产加工中心年产量已经超过 4 万台,并保持着高速增长的势头,但是市场占有率却仅为 30%左右,在高端机床市场几乎得不到市场的认可。因此为了提高数控机床可靠性缩短与国外产品的差距,我国将包括加工中心在内的数控机床可靠性研究定为重点攻关领域,并提出在“十三五”规划结束时包括加工中心在内的数控机床平均故障间隔时间(MTBF)达到 2000 小时的战略目标。
1.4.2 加工中心可靠性国内外研究现状
1.4.2.1加工中心可靠性国外研究现状
可靠性理论发展于上个世纪三十年代末,指的是产品在规定条件下及规定时间内完成规定功能的能力,通常用可靠度衡量产品的可靠性水平[16-17]。加工中心可靠性理论是伴随着数控机床可靠性理论的发展而发展[13]。 国外不仅研制数控机床的时间较早,而且将可靠性理论应用于数控机床包括加工中心的时间也早于我国。1963 年,Milton C. Shaw[18]研究了能够使机床寿命周期内的经济性达到最高的优化算法。1967 年,W.A. Knight[19]在文献中对机床因切削工件而产生的振动性能开展了研究,提出了评估和预算机床稳定性的方法。以上学者虽然没有直接提出机床可靠性的研究术语,但是他们所研究的内容都与可靠性密切相关。1975 年,T.S Sankar[20]评估了主轴系统在随机切削载荷下的可靠性水平,是早期直接与数控机床可靠性理论相关的研究成果之一。1982 年,A.Z. Kelle[21]等研究学者采用威布尔分布以及对数正态分布理论对数控机床的可靠性和维修性进行了数学建模。虽然早期学者对数控机床包括加工中心的可靠性进行了相关研究,但没有形成理论体系。苏联在 20 世纪 70 年代对数控机床可靠性理论开展了专门的研究,并出版了相关学术专著,是后期建立包括加工中心在内的数控机床可靠性理论体系的重要基础[22]。由于国外机床企业对产品质量的高度重视,数控机床包括加工中心的可靠性问题通常由企业内部进行解决并作为商业机密,因此专门的科研机构对于数控机床可靠性的研究较少,这也是难以查阅国外相关先进研究成果的重要原因。 目前,国外关于数控机床包括加工中心的可靠性研究多数集中在可靠性建模以及维修性等方面。数控机床寿命分布模型的建立方法主要是采用威布尔分布模型、指数分布模型以及正态分布模型等。S. Tanaka[23]在考虑到尺度参数与形状参数存在关联性的情况下,研究出威布尔分布尺度参数的快速估计方法。此外,D.M. Brkich Stephen Shifley 等[24-25]也对威布尔分布模型进行了研究扩展,使其在可靠性研究领域中应用更加广泛。除了威布尔分布模型之外,离散事件树方法、蒙特卡洛方法、Petri 网建模方法等也广泛应用在可靠性建模理论中。然而目前国外关于数控机床零部件制造工艺可靠性的研究成果几乎没有。
1.4.2.2 加工中心可靠性国内研究现状
国内可靠性理论研究时间相比国外较晚。直到 20 世纪 80 年代,我国才开始研究加工中心可靠性理论。从“八五”规划开始,数控机床包括加工中心的可靠性研究得到了国家的重视,并在“九五”规划结束时将其平均故障间隔时间(MTBF)提高了 2 倍达到 500-600 小时。吉林大学是国内较早开展数控机床包括加工中心可靠性研究的单位,随着国家科技重大专项对数控机床可靠性支持力度的加大,越来越多的企业和科研院所开始对数控机床可靠性进行研究。 目前,国内对包括加工中心在内的数控机床可靠性理论的研究已经取得了很多成果。许彬彬[26]考虑不同维修程度对数控机床的影响建立了数控机床整机及子系统的可靠性模型。申桂香等[27]运用了熵权法对加工中心可靠性评价指标包括平均故障间隔时间(MTBF)、平均首次故障时间(MTTFF)、当量故障率 D 分配权重,从而得到加工中心可靠性的客观评价结果。邵娜等[28]利用物元可拓模型对数控机床的子系统包括液压、电气等进行可靠性评价。张根保等[29]研究了对数线性比例强度理论模型,并运用该理论对数控机床在不完全维修情况下的可靠性进行了评估。李小兵[13]提出了针对故障发生时间的加工中心可靠性建模方法,并且对加工中心在受到切削负荷影响时的可靠性水平进行了评估。魏领会等[30]利用Petri 网模型和蒙特卡洛仿真分析理论对数控机床可用度进行建模与仿真分析。以上学者的研究成果主要集中在加工中心可靠性建模及评价方面,具有一定的研究深度。 除了可靠性建模及评价之外,国内学者在可靠性试验、故障分析等方面同样取得了很多研究成果。肖俊等[31]将模糊理论应用到了数控机床可靠性分配模型中,并综合考虑了可靠性分配准则,为数控机床可靠性设计研究提供了参考。蒋敬仁[32]对加工中心盘式刀库的可靠性试验方法进行了研究,对企业以及科研院所制定加工中心盘式刀库可靠性试验规范具有一定参考价值。方杰[33]对加工中心的载荷谱进行了研究,依据加工中心切削载荷编制出了相应的速度谱、切削力谱以及切削扭矩谱,对加工中心可靠性试验具有指导意义。上述研究成果主要集中在机床可靠性试验方面,也是目前机床可靠性研究中最为常见的试验方法。段炜[34]对加工中心盘式刀库换刀系统的故障模式进行了研究,并提出了相应故障预警方法。李加明[35]研究了加工中心链式刀库和机械手的模块化可靠性分配方法,并对链式刀库和机械手的传动系统运用了动作可靠性设计。程晓民等[36]分析了加工中心发生的早期故障,并建立了加工中心早期故障间隔时间的数学模型,为加工中心可靠性改进提供了重要的依据。这些研究成果主要集中在加工中心可靠性设计、故障分析以及可靠性评估方面。 通过总结上述研究成果,可以发现目前国内学者在数控机床可靠性设计、可靠性建模、可靠性试验以及故障分析等方面已经取得了很多研究成果,但同样是尚未涉及数控机床零部件制造工艺可靠性的研究。
1.4.3 制造工艺可靠性国内外研究现状
1.4.3.1制造工艺可靠性国外研究现状
目前国外对于制造工艺可靠性已经进行了研究,并取得了一定的成果但尚未涉及数控机床类的产品。Bruno Bosacchi[37]将模糊逻辑理论应用到了微电子质量控制系统中,并提出三种保障产品可靠性的方法,分别是优化产品部件质量、提高生产过程成品率以及尽早考虑产品可能发生的可靠性问题。William Q. Meeker等[38]将多种统计方法,如六西格玛设计等应用于产品研发制造阶段的可靠性分析中。上述研究都是从宏观角度提出一些解决问题的措施,而并没有具体落实到某个产品的生产过程中。Kanchan Kumar Das[39]认为整个制造系统受到制造设备可靠性的影响很大,并以生产费用为约束对制造系统可靠性数学模型进行了优化,但并未从保障所生产的产品符合设计要求的角度进行研究。
此外,许多学者都是从提高产品可靠性的角度保障制造过程可靠性,而单独针对制造过程可靠性研究的理论较少。Michael Pecht 等[40]认为物理失效模型的研究理论与成果可以用于产品的制造过程中,从而达到提高产品可靠性的目的。Taeho Kim 和 Way Kuo[41-42]建立了半导体生产线成品率与产品可靠性的关系模型,并认为与设计过程、制造过程以及操作过程相关的参数是影响产品成品率与可靠性的主要因素。这些学者的研究主要是对产品的物理失效机理进行分析,研究领域也是主要集中在半导体等电子器件领域。Angus Jeang 等[43]研究了产品使用时间与制造方法以及制造误差之间的关系,并建立了产品寿命周期经济性的优化模型。Biren Prasad[44]从提高产品寿命周期经济性的角度对制造企业的管理进行了优化。Om Prakash Yadav[45]将 Bayes 方法与模糊理论相结合,利用产品设计与制造过程中的定性信息,从而实现对产品可靠性的预计。Carlos Adrino Rigo Teixeira[46]将客户评价结果、故障树分析结果以及一些定性方法应用于产品可靠性提升中,并在汽车离合器的生产中运用了相关理论。这些学者虽然分析了制造过程与产品寿命周期或者产品可靠性的关系,说明了制造过程的重要性,但并未针对具体产品的制造过程进行研究。Seiichi Nakajima[47]在日本工业界推行全员生产维护的概念,在实际生产应用中取得了很好的效果并得到了业界内的认可。B. M. Hsu[48]在无法得到产品精确的加工尺寸时,运用模糊方法对产品制造工序能力指数进行了评估。上述研究成果虽然是以产品制造过程为研究对象,但是研究角度较为单一。
1.4.3.2制造工艺可靠性国内研究现状
目前国内对于制造工艺可靠性的研究同样取得了一定的成果但也均未针对数控机床类产品进行专门的研究。赵天旭等[49]研究了集成电路可靠性与制造成品率之间的关系,并认为集成电路的失效由多种原因引起,这些原因包括温度、化学过程、电路以及机械制造等,并说明了机械制造过程对集成电路可靠性的影响。孙继文等[50]认为制造系统可靠性受产品质量的影响,并利用产品特征测量值、系统故障要素与性能衰退的相互影响建立了相关模型,从而实现对制造系统可靠性定量分析的目的。范文贵[51]分析了小批量生产中存在的数据信息不足的问题,并运用贝叶斯理论对小批量生产建立质量控制模型,从而减少建模对数据量的依赖。余忠华等[52]运用贝叶斯理论对产品工序质量建立了动态控制模型,并将其应用到汽轮机的叶片制造工序中,证明了该方法的应用价值。上述研究成果主要针对的是质量控制模型的建立,但是未提出保障产品制造过程符合设计要求的具体措施。王丽颖等[53]提出了对影响生产工序的因素进行柔性编码的方法,从而能够适应生产中灵活性与标准性的需要,并运用了相似制造论对相似工序分组,从而解决小批量生产中数据不足的问题。
许多学者将统计过程控制与诊断技术应用到了产品制造过程的质量控制中。刘春雷等[54]将多品种小批量生产中结构相似的产品建立分组,运用正态分布等数据转换方法解决了样本数据不足的问题,并利用动态控制图监测加工过程是否存在异常情况。乐清洪[55]研究了人工智能技术在产品工序质量控制中的应用,分析了智能统计过程控制和质量预测控制存在的主要问题及解决方案。陈志强等[56]对产品生产过程中定性质量指标运用模糊理论,从而能够对其建立控制图进行生产过程质量监测,并扩展了控制图的应用领域。刘艳永等[57]将两种质量诊断理论与多元累积和控制图相结合,并运用实例对其研究成果进行了说明。上述研究成果主要是对控制图分析进行了研究,并提出了解决小批量生产过程数据不足的方法。
此外一些学者研究了关键工序的确定方法以及降低制造工艺故障发生率等相关理论。杨承先等[58]采用层次分析法(AHP)确定出关键工序质量控制点,并将其理论应用到液压挖掘机的生产过程中。周东君等[59]对传统多层次分析法进行了改进,并将其应用到军械器材关键工序质量控制点的监控上。张曼[60]对小批量产品试制过程建立了有向图模型,确定出关键工序节点,并利用分析软件 NWA绘制了移动极差控制图,进一步检测了关键工序的稳定性。上述研究成果针对制造过程关键工序的确定方法进行了研究,从而能够针对性的实施相关的保障性措施,但并未针对具体的保障措施开展研究。孙静[61]分析了接近零不合格过程概念的发展历程,并提出了实现这一概念的理论体系,但是研究方法较为宏观且过于理论,还需要进一步细化研究。蒋平[62]提出了制造工艺可靠性的定义以及评价指标,并将产品的孔位特征作为制造工艺可靠性的主要考察对象,对工艺可靠性的主要影响因素进行了分析判别,提出了工艺可靠性的建模与评定方法。但是以产品孔位特征作为产品可靠性指标的决定性因素值得商榷,其研究方法不能适用于所有机械制造产品,而且其理论较为复杂,对于企业而言具有较大的实施难度。
虽然目前国内外制造工艺可靠性的研究成果并未针对数控机床零部件且存在某些方面的局限性,但可以为加工中心主轴箱体制造工艺可靠性保障方法的研究提供一定的参考。加工中心主轴箱体的生产分为单件小批量生产和大批量生产两种,单一的制造工艺可靠性保障理论并不一定能够适用,此外理论结构过于复杂则不利于机床企业开展具体的实施工作,因此在研究加工中心主轴箱体制造工艺可靠性保障方法时应当考虑到上述情况。
1.5 论文主要研究内容
本文结合“千台国产加工中心可靠性提升工程” (2013ZX04011-012)和“重型机床可靠性试验与评价方法研究”(2014ZX04014-011)国家科技重大专项课题的研究内容及长期在机床制造企业的实践经历,以便于企业实施为重要原则,从多个角度并逐层加深的对加工中心主轴箱体制造工艺可靠性保障方法进行研究,本文研究内容的逻辑结构如图 1.4 所示,本文主要研究内容如下:
第 1 章 绪论。了解目前国内外加工中心发展现状和加工中心可靠性的研究现状,得出目前加工中心零部件制造工艺可靠性的研究尚处于起步阶段。总结国内外其他产品的制造工艺可靠性研究现状及其不足,提出加工中心主轴箱体制造工艺可靠性保障方法的研究思路和主要内容,并说明其研究意义。
第 2 章 加工中心主轴箱体制造工艺可靠性定义及评价指标。分析加工中心主轴箱体的结构及其在加工中心整机中的作用,说明不同型号加工中心主轴箱体在制造工艺上的相似性。提出加工中心主轴箱体制造工艺可靠性的定义,同时提出用于评价加工中心主轴箱体制造工艺可靠性的指标体系,并详细描述各个评价指标的含义与计算方法。
第 3 章 基于模糊评判的加工中心主轴箱体制造工艺 FMECA。介绍加工中心主轴箱体制造工艺 FMECA 实施流程,为了解决数据不足的问题,本文将风险优先数定为评判原则,对以故障原因为单位的工艺故障模式应用梯形模糊数评判方法,从而得出各工艺故障模式的风险程度排序,再对加工中心主轴箱体整个工艺系统进行综合评判,确定出系统风险等级,为是否实施改进措施提供依据。
第 4 章 加工中心主轴箱体制造过程控制图分析及软件编制。介绍控制图分析方法的原理以及加工中心主轴箱体制造过程控制图分析流程,利用 MATLAB-GUI(图形用户界面)编制加工中心主轴箱体制造过程 x ?s 控制图分析软件,该软件能够准确快速计算样本数据、绘制分析用 S 图和 x 图、判断出加工中心主轴箱体制造过程是否存在异常,通过对异常因素和异常样本数据的排除可以生成相应的控制用控制图,用于监测加工中心主轴箱体制造过程的波动情况。
第 5 章 加工中心主轴箱体制造过程关键工序质量控制点。提出了加工中心主轴箱体制造过程一般关键工序和特殊关键工序的定义,以及确定关键工序需要采用的方法。说明了加工中心主轴箱体制造过程关键工序质量控制点的内容,分析了与加工中心主轴箱体制造过程密切相关的 5M1E 因素,并针对各个因素制定相应的控制文件,描述了建立以及管理关键工序质量控制点的方法。
第 6 章 总结与展望。对本文的主要工作进行总结并对课题的未来研究方向进行展望。
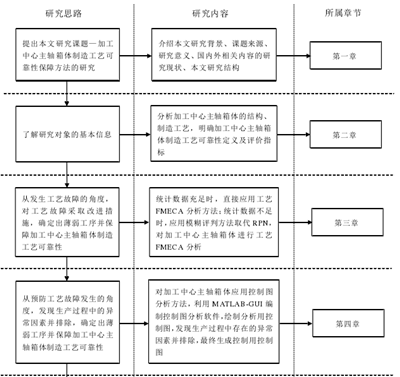
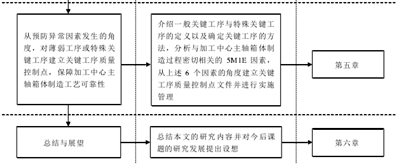
图1.4 论文的逻辑结构
第 2 章 加工中心主轴箱体制造工艺可靠性定义及评价指标
为了便于研究加工中心主轴箱体制造工艺可靠性的保障方法,本文对加工中心主轴箱体制造工艺可靠性进行了定义并提出相应的评价指标。在 2.1 节中介绍了加工中心主轴箱体的结构及其在加工中心整机中的作用,结合企业的加工实例介绍了加工中心主轴箱体制造工艺流程,在 2.2 节中提出了加工中心主轴箱体制造工艺可靠性的定义,在 2.3 节中提出了加工中心主轴箱体的主要评价指标,并描述了各个评价指标的含义与计算方法。建立的指标体系能够全面评价加工中心主轴箱体制造工艺可靠性,为是否需要实施制造工艺可靠性保障方法提供决策依据,也为验证制造工艺可靠性保障方法的有效性提供考核依据。 2.1 加工中心主轴箱体结构及其制造工艺
2.1.1 加工中心主轴箱体结构
加工中心是一种具有两种或者两种以上加工方式并能自动换刀的数控机床[63]。根据主轴空间布置形式的不同可以分为卧式加工中心和立式加工中心(如图2.1、图 2.2 所示),卧式加工中心的主轴平行于工作台,而立式加工中心的主轴垂直于工作台。在对加工中心进行可靠性研究时,通常将其划分为基础部件、机床附件、主轴系统、液压系统等子系统,其中主轴系统包括了主轴箱体、主轴、主轴轴承、电机等。
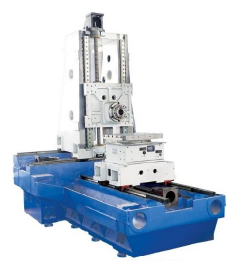
图 2.1 卧式加工中心
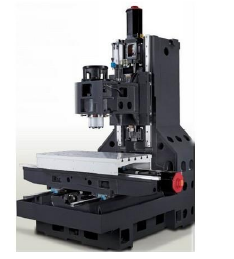
图2.2 立式加工中心
加工中心主轴箱体是承载主轴的关键零件,同时与立柱的滚珠丝杠装配连接。主轴箱体的制造质量将会直接影响到其与主轴、电机、轴承等的装配质量,从而影响到整机的可靠性水平。加工中心主轴箱体的结构与多种因素相关,包括主轴的传动形式、丝杠传动数量、主轴尺寸等。如果主轴传动形式为齿轮传动,则主轴箱体上需要有相应的电机孔、传动轴孔以及主轴孔;如果主轴传动形式为带传动,则主轴箱体上不需要传动轴孔;如果主轴为电主轴,则主轴箱体上不需要具有电机孔及传动轴孔。根据丝杠传动数量的不同,主轴箱体上相应的布有不同数量的丝杠连接孔。此外,主轴箱体上还会布有润滑管路连接孔、导轨面等。图 2.3所示为某型号卧式加工中心主轴箱体,图 2.4 所示为某型号立式加工中心主轴箱体。
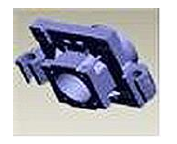
图 2.3 某型号卧式加工中心主轴箱体
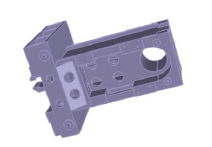
图 2.4 某型号立式加工中心主轴箱体
2.1.2 加工中心主轴箱体制造工艺
虽然不同形式的加工中心主轴箱体在主轴孔、传动轴孔、电机孔、丝杠连接孔的相对位置关系上存在一定不同,但是从制造工艺的角度分析,卧式加工中心主轴箱体与立式加工中心主轴箱体均可看作是需要进行面孔加工的箱体类零件,工艺过程具有较大的相似性。
工艺过程指的是直接改变生产对象相关性能的过程,这些性能包括了物理性能、化学性能、尺寸、形状以及相对位置关系等,某些工作如装夹、测量等虽然不是直接改变生产对象的物理性能、化学性能、尺寸、形状以及位置关系,但是这些工作与加工过程密切相关而且无法割离,因此这些工作也归属到工艺过程的范畴中;工艺过程的种类较多,包括机械加工、冲压、热处理等工艺过程;工序是组成产品制造工艺过程的基本部分,也是企业制定生产计划及核算生产成本的基本单元[64]。因此本文将工序定为研究加工中心主轴箱体制造工艺可靠性保障方法的基本单元。
在制定加工工序的顺序时,通常有如下原则:先进行定位基面的加工,后进行其他表面加工;先进行粗加工,后进行精加工;先进行主要表面加工,后进行次要表面加工;先进行平面加工,后进行孔的加工。但是工序顺序的制定在考虑到上述原则时也需要综合考虑企业生产设备的安放位置、生产成本、生产调度等其他因素,从而才能制定出符合企业自身情况的合理工序顺序。 加工中心主轴箱体的毛坯为铸件,制造精度尤其是主轴孔的制造精度要求较高,有些型号加工中心主轴箱体体积较大,装夹费时费力(如图 2.5 所示),运输困难,存在一定的加工难度。本文以某机床企业的主轴箱体为例(见图 2.6)介绍其制造工艺流程(见表 2.1,只保留加工内容),为了便于理解各工序的作用,本文将该型号加工中心主轴箱体的工序按加工位置不同或者功能不同进行了分类(见表 2.2)。因涉及企业机密,图 2.6 中未注明尺寸参数,表 2.1 中工序内容除技术要求外,其余尺寸均为零件图尺寸,但经过处理并非企业完整的真实数据。
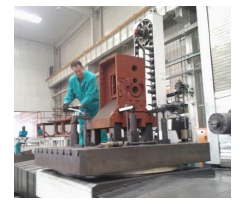
图 2.5 某型号主轴箱体生产现场
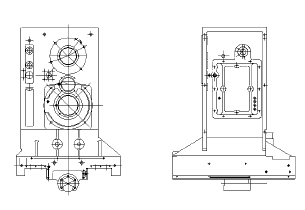
图 2.6 某型号主轴箱体示意图
表 2.1 某型号加工中心主轴箱体制造工艺流程
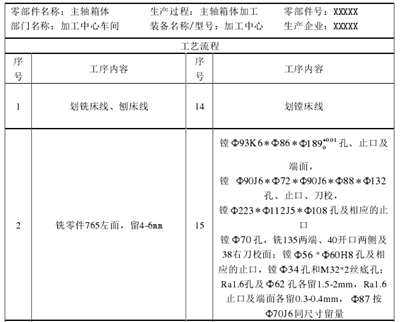
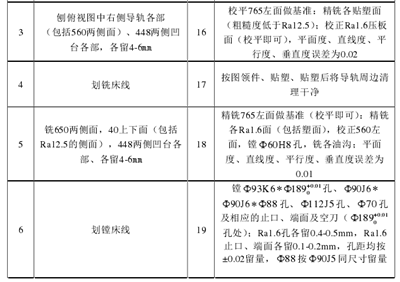
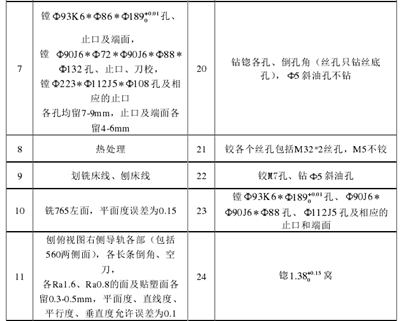
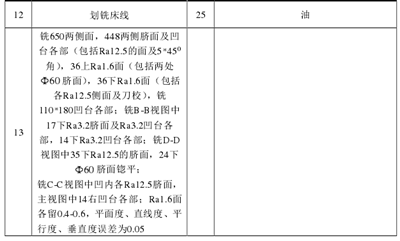
表 2.2 工序分类
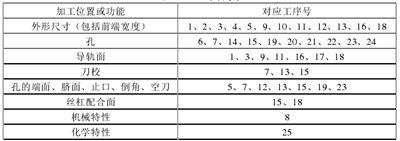
2.2 加工中心主轴箱体制造工艺可靠性定义
为了研究加工中心主轴箱体制造工艺可靠性保障方法,在对加工中心主轴箱体结构及其制造工艺进行了解后,需要明确加工中心主轴箱体制造工艺可靠性的定义。国家标准 GJB451A-2005 对可靠性的定义为:产品在规定的时间内以及规定的条件下,完成规定功能的能力[65]。虽然可靠性的定义是统一的,但是由于产品的差异,对各种产品的可靠性进行定义时也应存在区别。目前国内外相关学者虽然从多种角度提出了制造工艺可靠性的定义,但并没有一个得到了广泛的认同[62]。对于加工中心主轴箱体制造工艺可靠性而言,可靠性定义中的产品指的是加工中心主轴箱体制造工艺,可靠性定义中的功能指的是制造完成的加工中心主轴箱体应符合设计要求。
综合考虑可靠性的定义以及目前国内外学者提出的制造工艺可靠性定义,结合加工中心主轴箱体制造过程的特点,本文从制造过程符合规定要求能力的角度,对加工中心主轴箱体制造工艺可靠性定义如下:在规定的制造时间内和规定的制造条件下,加工中心主轴箱体制造工艺过程符合规定生产要求的能力。定义中规定的制造时间指的是生产前所指定的任务完成时间,其可以是加工前规定的某个工序完成时间也可以是整个工艺流程完成时间,或者是其他某个任务所需要的完成时间;规定的制造条件指的是加工中心主轴箱体加工过程中所涉及到的因素包括生产环境、工件材料、生产设备、生产人员、工艺方法、测量等;规定生产要求指的是加工所依据的技术要求,包括设计图纸、制定的工艺要求等。本文提出的加工中心主轴箱体制造工艺可靠性定义强调了整个工艺过程要符合规定要求,即制造完成的加工中心主轴箱体不仅符合设计图纸的要求,而且制造过程中每道工序也应符合工艺要求,即制造过程中每个操作均应符合工艺要求中的所有内容。
2.3 加工中心主轴箱体制造工艺可靠性评价指标
2.3.1 加工中心主轴箱体制造工艺可靠性评价指标的确定
为了便于评价加工中心主轴箱体制造工艺可靠性,需要制定相应的制造工艺可靠性评价指标。薄弱工序指的是评价指标不符合规定要求或者具有不符合规定要求的风险较大的制造工序,因此根据制造工艺可靠性评价指标的评价结果可以确定出加工中心主轴箱体制造过程中的薄弱工序,从而可以有针对性的采取制造工艺可靠性保障方法。目前国内外不仅没有被一致认可的制造工艺可靠性定义,而且也没有被一致认可的制造工艺可靠性评价指标。数控机床可靠性评价指标有平均故障间隔时间 MTBF、平均首次故障间隔时间 MTTFF、平均修复时间 MTTR等[66];蒋平[62]提出制造工艺可靠性指标体系包括工艺稳定性、工艺自修正性、工艺遗传性、工艺故障平均维修时间等。为了制定出合理的加工中心主轴箱体制造工艺可靠性评价指标,本文参考了数控机床可靠性评价指标以及目前相关学者的研究成果,同时综合考虑了加工中心主轴箱体制造工艺可靠性的定义。
加工中心主轴箱体制造工艺可靠性与多种因素相关,包括生产环境、工件材料、生产设备、生产人员、工艺方法、测量等,而这些影响因素对制造工艺可靠性的影响可以通过工序或者工件完成的时间、工艺故障发生的概率、工艺稳定程度等体现出来,此外制定的加工中心主轴箱体制造工艺可靠性评价指标应具有可计算性、适用性、完备性等要求[67]。根据上述情况的讨论,本文提出的加工中心主轴箱体制造工艺可靠性评价指标如图 2.7 所示,具体的指标有工艺可靠度、工艺故障风险优先数、工艺稳定性、平均工艺故障间隔时间、平均工艺故障修复时间、合格工序平均完成时间、单个合格工件平均完成时间及其他指标。
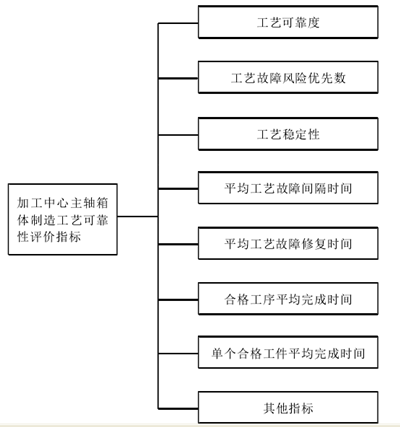
图 2.7 加工中心主轴箱体制造工艺可靠性评价指标
2.2.3 加工中心主轴箱体制造工艺可靠性评价指标的计算方法
2.2.3.1 工艺可靠度
工艺可靠度是衡量加工中心主轴箱体制造工艺可靠性的总体指标,是对加工中心主轴箱体制造工艺可靠性的概率度量,也是研究加工中心主轴箱体制造工艺可靠性模型的重要指标。工艺可靠度 R(t) 可以用式 2.1 表示。
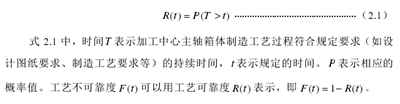
2.2.3.2工艺故障风险优先数
工艺故障风险优先数用 RPN 表示,从工艺故障严酷度 S 、工艺故障发生概率O 、工艺故障被检测难度 D 三个角度对制造工序发生的工艺故障模式进行评价,S 、O 、D 的评分标准可参考相应的国家军用标准,具体内容参见本文的第三章,RPN 的计算方法为

2.2.3.3 工艺稳定性
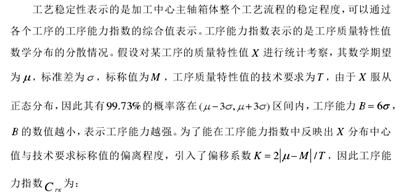
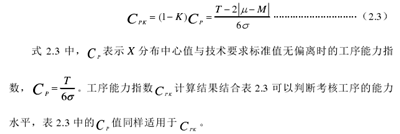
表 2.3工序能力指数
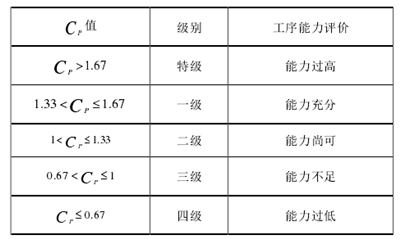
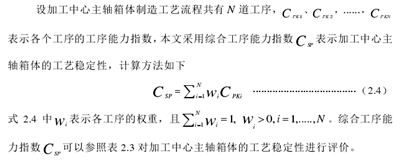
2.2.3.4 平均工艺故障间隔时间
平均工艺故障间隔时间( PFMTBF 或CBFT)应用于工艺故障可修复的加工中心主轴箱体制造工艺过程中,工艺故障是指产品制造过程中因未按规定要求而引起的故障。在规定时间和条件下,加工中心主轴箱体制造过程中发生 N 次工艺故障,每次经过修复便可继续生产作业,假设连续按照规定要求进行生产作业的时间为1t , 2t ,......, Nt ,则平均工艺故障间隔时间为

式 2.5 中T 表示加工中心主轴箱体按照规定要求进行生产作业的总时间。
2.2.3.5 平均工艺故障修复时间
平均工艺故障修复时间( PFMTTR 或CCTT)指的是将加工中心主轴箱体制造过程中发生的工艺故障修复到正常状态下所需要的平均时间。假设在规定时间和
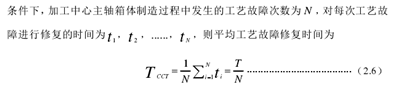
式 2.6 中T 表示加工中心主轴箱体发生工艺故障总的修复时间。
2.2.3.6 合格工序平均完成时间
合格工序平均完成时间( MQPCT 或PCTT)指的是某个加工中心主轴箱体制造工序最终完成合格的加工作业所需要的平均时间,是衡量该工序加工作业效率的重要标准,也是综合评价加工中心主轴箱体制造工艺可靠性的重要指标之一。MQPCT 不仅包括了工艺故障修复时间,还包括加工过程涉及到的其它时间如加工设备的维修保养时间、操作人员的误工时间、正常加工作业所需要的时间等。假设在规定时间和条件下,某工序最终完成合格加工作业的加工中心主轴箱体数量为 N ,每个加工中心主轴箱体最终合格完成该工序所用的加工作业时间为1t ,2t ,......, Nt ,则合格工序平均完成时间为

2.2.3.7 单个合格工件平均完成时间
单个合格工件平均完成时间( MQWCT 或WCTT)指的是整个制造工艺流程完成单个合格加工中心主轴箱体所需要的平均时间,是衡量整个工艺流程生产效率的重要标准,也是综合评价加工中心主轴箱体制造工艺可靠性的重要指标之一。MQWCT 指标可以与成品率综合使用,为考核整个制造工艺流程是否达到企业要求提供参考。假设在规定时间和条件下,完成合格的加工中心主轴箱体数量为 N ,合格完成每个加工中心主轴箱体零件所用的时间为1t , 2t ,......, Nt ,则单个合格工件平均完成时间为

需要说明的是:只有在样本数量比较大的情况下(通常要求样本数量大于30),上述计算方法(2.5)、(2.6)、(2.7)、(2.8)的计算结果才能较为准确的反映实际情况。对于多品种小批量的加工中心主轴箱体,可以采用相似工序或零件成组的方法进行样本数量的扩充,并将采集到的质量特性值进行相应的数学转换[54],从而保证相关指标计算结果能较为准确的反映实际情况。
2.3 本章小结
本章分析了加工中心主轴箱体的结构及其在加工中心整机中的作用,说明了不同型号加工中心主轴箱体在制造工艺上的相似性,并结合实例介绍了加工中心主轴箱体的制造工艺流程。根据可靠性的定义以及国内外相关学者的研究成果,结合加工中心主轴箱体制造过程的特点,本文从制造过程符合规定要求能力的角度,提出了加工中心主轴箱体制造工艺可靠性的定义。本章提出了可定量计算的加工中心主轴箱体制造工艺可靠性评价指标,包括工艺可靠度、工艺故障风险优先数、工艺稳定性、平均工艺故障间隔时间、平均工艺故障修复时间、合格工序平均完成时间、单个合格工件平均完成时间等,并描述了各个评价指标的含义与计算方法,从而能够全面评价加工中心主轴箱体制造工艺可靠性,为是否需要实施制造工艺可靠性保障技术提供依据,也为验证制造工艺可靠性保障技术的有效性提供了考核依据。本章内容是后续章节能够针对性研究加工中心主轴箱体制造工艺可靠性保障方法的重要基础。
投稿箱:
如果您有机床行业、企业相关新闻稿件发表,或进行资讯合作,欢迎联系本网编辑部, 邮箱:skjcsc@vip.sina.com
如果您有机床行业、企业相关新闻稿件发表,或进行资讯合作,欢迎联系本网编辑部, 邮箱:skjcsc@vip.sina.com
更多本专题新闻